En el sector industrial, la gestión efectiva de la corrosión es fundamental para preservar la integridad de los activos. En este contexto, el mapeo de corrosión se presenta como una herramienta clave, especialmente en activos propensos a la corrosión por picaduras internas y grietas. Este método permite identificar y evaluar de manera precisa los puntos vulnerables, proporcionando información para implementar estrategias preventivas y de mantenimiento.
La corrosión representa una amenaza significativa para la integridad de los activos industriales, provocando deterioro estructural, mayores costos de mantenimiento y posibles riesgos de seguridad. Entre los diferentes tipos de severidad, la corrosión por picaduras internas y grietas se localizan en zonas específicas difíciles de prever, lo que dificulta su detección, especialmente si esta se desarrolla debajo de los recubrimientos en la superficie a inspeccionar.
En este artículo, se abordan temas como: los retos planteados frente a la corrosión por picaduras internas y grietas, los métodos tradicionales de detección y los avances en tecnologías electromagnéticas automatizadas integradas en el mapeo de corrosión.
Mapeo de corrosión en estructuras metálicas
El mapeo de corrosión consiste en es una representación bidimensional a través de una presentación C-Scan, es un método usado para caracterizar áreas afectadas por corrosión interna. Proporciona una imagen de fácil interpretación y resultados cuantitativos, además de permitir la detección y dimensionamiento de picaduras y grietas sobre superficies metálicas mediante técnicas empleadas.
En términos generales, es una herramienta aplicada en monitoreo identificación y ubicación de áreas afectadas por corrosión en componentes, partes o estructuras metálicas sujetas a inspección. Este método no solo se limita a señalar la presencia de corrosión, sino que abarca aspectos importantes, tales como:
- Clasificación de la corrosión según su morfología o tipo.
- Evaluación del grado de afectación de la zona.
- Cuantificación del nivel de corrosión en funciónde las propiedades mecánicas del material.
- Estimación de la posibilidad de reparar la corrosión detectada.
- Localización de fallas, defectos o discontinuidades que podrían convertirse en zonas potenciales de corrosión a corto plazo.
- Evaluación macroscópica del estado del componente, parte o estructura.
- Valoración de la eficacia de los productos aplicados que hayan mostrado fallos.
Este proceso integral de mapeo proporciona información sobre la presencia de corrosión en componentes metálicos y también ofrece un análisis detallado para la toma de decisiones informadas en cuanto a la gestión y mantenimiento de los activos. Desafíos frente a la corrosión por picaduras internas y grietas.
La corrosión por picaduras internas ocurre cuando áreas localizadas en las superficies internas de activos, como tuberías, tanques de almacenamiento y recipientes, presentan corrosión por espacios confinados . A diferencia de la corrosión general, que se propaga de manera uniforme sobre una superficie, la corrosión por picaduras y grietas puede comprometer la integridad estructural del material.
El desafío radica en detectar este tipo de corrosión antes de que conduzcan a fallas catastróficas. Las picaduras debajo de recubrimientos pueden ser un reto para un mapeo de corrosión a través de la técnica de Ultrasonido por Arreglo de Fases (PAUT), y la presencia de grietas son imposibles de mostrar en una presentación C-Scan para esta misma técnica.
Métodos tradicionales de detección
- Inspección Visual (IV): La inspección visual es un método fundamental para la detección de corrosión, pero tiene limitaciones cuando se trata de la corrosión por picaduras internas. La corrosión puede estar oculta debajo de recubrimientos o en áreas de difícil acceso, lo que dificulta su identificación a simple vista.
- Pruebas Ultrasónicas (UT): Las pruebas ultrasónicas implican enviar ondas sonoras de alta frecuencia a través de un material para identificar zonas de corrosión. Si bien es efectivo en muchos escenarios a través de técnicas avanzadas como Ultrasonido por Arreglo de Fases (PAUT), en algunos casos las pruebas ultrasónicas pueden no ofrecer un rendimiento suficiente o ser lo suficientemente sensibles para detectar fosas muy pequeñas en diámetro e imposible en la captación de grietas en una presentación C-Scan.
- Pruebas radiográficas: Las pruebas radiográficas utilizan rayos X o rayos gamma para capturar imágenes de estructuras internas. Sin embargo, este método presenta ciertos inconvenientes para su aplicación como: seguridad, accesibilidad limitada y limitaciones para detectar la corrosión por picaduras en etapas tempranas.
Avances en tecnología electromagnética
En los últimos años, la tecnología electromagnética ha surgido como una herramienta poderosa para mapear la corrosión en la detección de picaduras internas, así como en la captación de grietas. Estos avances aprovechan los principios de la inducción electromagnética para detectar y cuantificar la corrosión sin necesidad de contacto directo con el material.
Ensayo de Corrientes Eddy (ECA)
Las pruebas de corrientes Eddy implican inducir corrientes eléctricas en un material conductor y medir los campos magnéticos resultantes. Se detectan y analizan cambios en la conductividad, como los causados por la corrosión por picaduras. Este método no destructivo se puede aplicar a una variedad de materiales y en diversas formas tales como tubos y planchas.
Tecnologías modernas tales como Corrientes Inducidas por Arreglo de Sensores (ECA), permiten mapear en componentes tales como tubos, recipientes, tanques de almacenamiento, partes de turbinas, entre otros, siendo muy sensibles a detección de picaduras y grietas. Esta tecnología genera resultados más consistentes que los escaneos manuales rasterizados, disminuyendo así la dependencia del operador.
Las sondas ECA de Eddyfi Technologies utilizan multiplexación, lo cual consiste en activar y desactivar bobinas en secuencias específicas para aprovechar el ancho de la sonda. La multiplexación también minimiza la interferencia entre bobinas muy próximas (inductancia mutua) y maximiza la resolución de la sonda.
En el siguiente video se muestra la aplicación de las sondas ECA de Eddyfi Technologies, sobre tuberias.
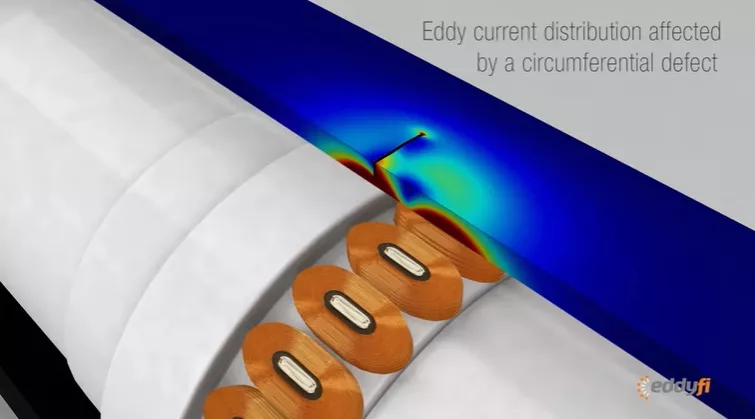
Mapeo de corrosión por Corrientes de Foucault (ECA). Fuente: Eddyfi Technologies.
Fuga de Flujo Magnético (Magnetic Flux Leakage – MFL)
MFL es una técnica de detección de corrosión rápida, confiable, que detecta el volumen de material magnético faltante en un componente bajo inspección. MFL implica magnetizar un material ferromagnético y medir la fuga de flujo causada por defectos como la corrosión y/o presencia de grietas.
Este método es particularmente útil para tubos de intercambiadores y calderas, así como para la evaluación específica de pisos de tanques de almacenamiento, ofreciendo un mapeo integral de la corrosión, también puede ser aplicado sobre recubrimientos.
Eddyfy technologies ofrece el nuevo FloormapX con características innovadoras únicas, como dirección activa de precisión para escaneos curvos rápidos y de alta calidad en la zona crítica, una guía láser interactiva para correlacionar fácilmente las ubicaciones físicas de los defectos del piso del tanque con imágenes de escaneo C, iluminación potente a bordo y SmartMAGNET™ para un rendimiento de inspección optimizado dependiendo del espesor de la placa.
Las inspecciones MFL son un recurso rápido y rentable para las evaluaciones del piso de los tanques. Este método magnetiza temporalmente el fondo del tanque, generando un campo magnético. Las perturbaciones en el campo magnético indican fallas en la estructura.
Medición de Campo de Corriente Alterna (Alternating Current Field Measurement – ACFM)
Se trata de una técnica electromagnética completamente cuantitativa que permite detectar y caracterizar grietas superficiales (metales ferromagnéticos) y subsuperficiales (metales ferromagnéticos y no ferromagnéticos) bajo recubrimientos no conductores de manera rápida y confiable.
La técnica está dirigida principalmente a la detección de grietas y con el uso sondas con sensores dispuestos en arreglo, se puede inspeccionar una mayor área y mostrarla en una presentación C-Scan, siendo ventajoso en aquellos casos donde el agrietamiento sea el principal mecanismo de degradación esperado, tal es el caso de la detección de grietas por fatiga en estructuras subacuáticas que soportan las plataformas marinas.
En inspecciones de pisos de tanques de almacenamiento, ACFM es utilizado como complemento del MFL en la evaluación de las zonas de las juntas soldadas y con ventajas sobre otros ensayos tradicionales como la prueba de caja de vacío, la cual es difícil de aplicar en soldaduras solapadas o cerca de obstrucciones, y partículas magnéticas cuando es requerido remover el recubrimiento (epoxi) para la aplicación efectiva del ensayo, pues la limpieza y re-aplicación de la capa protectora lo hacen mucho más costoso que hacer la inspección con ACFM.
Beneficios del mapeo de corrosión electromagnética
No destructivo: Las técnicas electromagnéticas no son destructivas, lo que significa que pueden evaluar la extensión de la corrosión sin causar daño al activo, lo cual es determinante para minimizar el tiempo de inactividad y preservar la integridad estructural del material.
Alta sensibilidad: Los métodos electromagnéticos muestran una alta sensibilidad a pequeños cambios en las propiedades del material, siendo adecuados para detectar la corrosión por picaduras en etapas tempranas y gestación de grietas. Esto permite un mantenimiento proactivo y evita reparaciones costosas.
Versatilidad: La tecnología electromagnética se puede aplicar a una amplia gama de materiales y tipos de activos. Ya sea inspeccionando tuberías, tanques de almacenamiento, recipientes a presión o infraestructuras críticas, estos métodos ofrecen versatilidad en el mapeo de la corrosión.
Conclusiones
El mapeo automatizado de la corrosión se ha convertido en una parte integral de la inspección de NDT y ha sido ampliamente adoptado en los programas de gestión de la corrosión. Las nuevas tecnologías integradas a las pruebas de: Corrientes Inducidas con Arreglo de Sensores (ECA), Fuga de Flujo Magnético (MFL) y Medición de Campo de Corriente Alterna (ACFM), ofrecen un detallado y oportuno mapeo de la corrosión. Esta precisión facilita un enfoque proactivo en el mantenimiento, asegurando la integridad y eficiencia operativa de los activos industriales.
Referencias
- J. C. DRURY I. Magnetic flux leakage technology; Consultado en fecha 23 de Enero de 2024. https://www.eddyfi.com/doc/Downloadables/magnetic_flux_leakage_technology-01.pdf
- SHANNON P. FARRELL, MARTIN LUGG, AND KYLE AVERY. Application of Alternating Current Field Measurement for Determination of Surface Cracks and Welds in Steel Structures at Lift-of; Consultado en fecha 24 de Enero de 2024. https://cradpdf.drdc-rddc.gc.ca/PDFS/unc199/p802467_A1b.pdf
- CHARLES TREMBLAY. Safeguarding Storage Tanks by Scanning Welds with ACFM; Consultado en fecha 24 de Enero de 2024. https://blog.eddyfi.com/en/safeguarding-storage-tanks-by-scanning-welds-with-acfm
- MATHIEU BOUCHARD. Surface Eddy Current Array: The Unsung Hero of Corrosion Mapping; Consultado en fecha 25 de Enero de 2024. https://blog.eddyfi.com/en/author/mathieu-bouchard
- J. C. DRURY I, A. MARINO. A Comparison of the Magnetic Flux Leakage and Ultrasonic Methods in the detection and measurement of corrosion pitting in ferrous plate and pipe; Consultado en fecha 25 de Enero de 2024. https://www.ndt.net/article/wcndt00/papers/idn701/idn701.htm