Tabla de Contenidos
- Introducción
- ¿Qué es el Mantenimiento Centrado en Confiabilidad (RCM)?
- Ventajas del Mantenimiento Centrado en Confiabilidad
- Aumento de la eficiencia/Optimización de costos operativos
- Reducción de costos
- Mejora de la productividad
- Sustitución de activos
- Mejora en la seguridad
- Mayor alineación con estándares regulatorios
- Desventajas del Mantenimiento Centrado en Confiabilidad
- Mantenimiento continuo
- Costos de formación y puesta en marcha
- Complejidad
- Estrategias para implementar el Mantenimiento Centrado en Confiabilidad
- Simplificación del análisis
- Diagnóstico basado en el conocimiento
- Optimización del mantenimiento predictivo
- Evolución del mantenimiento industrial: De TPM a RCM
- Conclusiones
- Referencias
Introducción
El Mantenimiento Centrado en Confiabilidad (RCM, por sus siglas en inglés) es una metodología avanzada que garantiza el óptimo funcionamiento de los equipos industriales, aumenta la fiabilidad de los activos y mejora la eficiencia en la producción. Este enfoque combina diversas estrategias de mantenimiento para optimizar la inversión en programas de mantenimiento preventivo, predictivo y proactivo, lo que asegura un control más efectivo de los costos y una mayor capacidad de las instalaciones.
A medida que las industrias se vuelven más competitivas, la gestión del mantenimiento y la mejora de la confiabilidad operacional se han convertido en áreas clave de atención. Entre las diferentes metodologías de mantenimiento, el RCM se destaca por su enfoque integral, que abarca tanto el diagnóstico basado en conocimiento como la resolución de problemas mediante la identificación de fallas funcionales y su eliminación.
¿Qué es el Mantenimiento Centrado en Confiabilidad (RCM)?
Es una estrategia de mantenimiento que combina técnicas reactivas, preventivas, predictivas y proactivas para maximizar la confiabilidad de los equipos a lo largo de su ciclo de vida. A través de un análisis profundo de las posibles fallas funcionales y la integración de diferentes enfoques, esta estrategia de mantenimiento proporciona una solución completa para la gestión de activos industriales.
Un claro ejemplo de esto, es el mantenimiento llevado a cabo en una plataforma petrolera, donde las bombas de extracción de crudo son equipos críticos. Anteriormente, la estrategia de mantenimiento era reactiva.
Sin embargo, con el Mantenimiento Centrado en Confiabilidad (RCM), las plataformas actuales emplean sensores que monitorean la vibración y temperatura de las bombas, con la finalidad de predecir fallas antes de que ocurran (mantenimiento predictivo).
Esta estrategia de mantenimiento permite a las organizaciones identificar las causas raíz de fallas en los sistemas y seleccionar las mejores estrategias para eliminarlos. Esto reduce los tiempos de inactividad, optimiza la vida útil de los activos y asegura un funcionamiento seguro y eficiente.
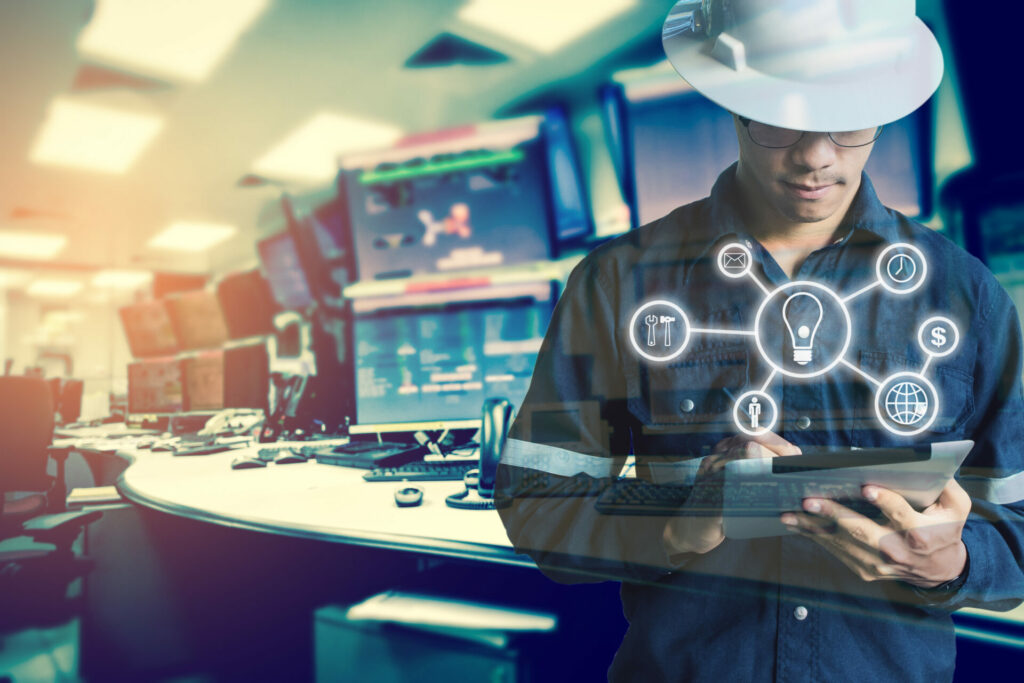
Ventajas del Mantenimiento Centrado en Confiabilidad
El éxito de esta metodología radica en sus múltiples beneficios, entre los que destacan:
Aumento de la eficiencia/Optimización de costos operativos
Optimiza la gestión de activos mediante la eliminación de fallas no deseados, mejorando la confiabilidad y aumentando la productividad. Al abordar los problemas antes de que ocurran, se reduce la frecuencia de reparaciones y paros inesperados.
Un estudio reciente del World Economic Forum sugiere que la implementación de estrategias de mantenimiento predictivo y RCM puede reducir los costos de mantenimiento en un 20-30%, y un estudio realizado por la firma consultora Accenture mostró que las empresas que implementan la metodología junto con tecnologías predictivas, como IoT y análisis de datos, pueden reducir los tiempos de inactividad en un 15-25%.
Reducción de costos
Al prevenir fallas mayores y optimizar las operaciones, se disminuyen significativamente los gastos relacionados con reparaciones y repuestos y al identificar las causas raíz de las fallas y gestionar el mantenimiento adecuadamente, se logra prolongar la vida útil de los activos. Según datos de McKinsey, una adecuada implementación del método puede extender la vida útil de los equipos hasta un 30%.
Mejora de la productividad
La implementación de estrategias de mantenimiento predictivo y preventivo evita las averías imprevistas, lo que se traduce en una mayor disponibilidad de los equipos y una mejora en la satisfacción del cliente.
El sistema se centra en prevenir fallas críticas de los equipos, lo que resulta en una mayor disponibilidad operativa. Empresas que han adoptado la estrategia han reportado mejoras en la confiabilidad de los activos en un 10-15%.
Sustitución de activos
Si un equipo presenta fallas recurrentes o está llegando al final de su vida útil, el RCM permite identificar el momento óptimo para su sustitución, evitando interrupciones innecesarias en el proceso productivo.
Mejora en la seguridad
Ayuda a prevenir fallas catastróficas que podrían poner en riesgo a los trabajadores o las operaciones. En el sector energético, se ha observado una reducción de incidentes relacionados con equipos críticos en un 20% tras la adopción de la estrategia.
Mayor alineación con estándares regulatorios
Está alineado con regulaciones internacionales y normativas de seguridad, lo que permite a las empresas cumplir más fácilmente con los requisitos de auditoría.
Desventajas del Mantenimiento Centrado en Confiabilidad
Aunque esta estrategia de mantenimiento ofrece múltiples ventajas, también presenta algunos desafíos:
Mantenimiento continuo
Se requiere un monitoreo constante de los equipos y un mantenimiento regular, lo que puede suponer una carga adicional en términos de tiempo y recursos. Es decir, se debe disponer de un presupuesto de gastos en la gestión de activos, que para unos operadores son gastos adicionales, no mirando la cantidad de beneficios que puede generar.
Costos de formación y puesta en marcha
Implementar el programa implica una inversión inicial considerable en formación del personal y en los recursos necesarios para llevar a cabo los análisis de confiabilidad.
Complejidad
Es un sistema complejo que requiere un profundo conocimiento de los activos y procesos de la planta. La planificación y ejecución adecuada del programa puede resultar un reto para las organizaciones que no cuenten con el personal capacitado.
Estrategias para implementar el Mantenimiento Centrado en Confiabilidad
La implementación de esta metodología implica un enfoque estructurado y planificado. A continuación, se presentan algunas estrategias clave:
Simplificación del análisis
El análisis preventivo debe enfocarse en las tareas clave para reducir el número de intervenciones innecesarias. Herramientas como el Preventive Maintenance Optimization (PREMO) se han desarrollado para optimizar el número de tareas y reducir costos.
Diagnóstico basado en el conocimiento
El análisis de fallas es fundamental en el mantenimiento centrado en confiabilidad. Utilizando herramientas como el FMECA (Failure Mode, Effects and Criticality Analysis), se pueden identificar los modos de falla y priorizar las intervenciones de mantenimiento.
Optimización del mantenimiento predictivo
El uso de tecnologías de mantenimiento predictivo permite monitorizar los activos en tiempo real, anticipando fallas y programando el mantenimiento de manera eficiente.
Evolución del mantenimiento industrial: De TPM a RCM
El mantenimiento industrial ha evolucionado considerablemente desde los enfoques simplistas del pasado. En la década de los 80 y 90, se desarrollaron conceptos como el Mantenimiento Basado en Condición y el Mantenimiento Productivo Total (TPM), que revolucionaron la industria.
Hoy en día, el enfoque del RCM ofrece una visión más holística, permitiendo a las organizaciones adoptar un enfoque proactivo para la gestión del mantenimiento. Este avance ha llevado a la creación de sistemas de Mantenimiento de Clase Mundial (WCM), que integran la confiabilidad con la eficiencia operativa.
Según un informe de McKinsey, las empresas que han integrado esta estrategia y tecnologías digitales en sus estrategias de mantenimiento han reducido los costos de mantenimiento en un 20-30%, con mejoras del 25% en la confiabilidad de los activos.
Un estudio de la Society for Maintenance & Reliability Professionals (SMRP) revela que las empresas que adoptan enfoques proactivos, como RCM y WCM, experimentan una reducción del 45% en fallas no planificadas de equipos.
El mantenimiento industrial ha evolucionado desde el TPM, que involucraba a todos los niveles de la organización en la prevención de fallas, hasta el RCM, que adopta una visión más analítica y basada en confiabilidad. Hoy en día, los sistemas WCM, potenciados por la digitalización y el monitoreo en tiempo real, representan el último avance en el mantenimiento industrial, integrando eficiencia operativa y confiabilidad de activos de manera óptima.
Conclusiones
El Mantenimiento Centrado en Confiabilidad es una estrategia fundamental para mejorar la eficiencia operativa, reducir costos y aumentar la confiabilidad de los activos industriales. Las empresas que lo implementan, optimizan sus recursos al centrarse en las áreas más críticas, lo que les permite reducir el tiempo de inactividad y maximizar el retorno de la inversión.
Aunque esta implementación puede ser costosa y compleja al principio, los beneficios a largo plazo justifican ampliamente el esfuerzo. Los programas de la metodología son particularmente beneficiosos para organizaciones que operan con activos complejos y que buscan mejorar su confiabilidad operacional, seguridad y eficiencia.
En resumen, la estrategia de mantenimiento ha ganado terreno no solo como una metodología para optimizar los procesos de mantenimiento, sino también como un enfoque integral de gestión de activos que busca maximizar el valor de los equipos, minimizar fallas y mejorar la seguridad operativa. Su aplicación sigue expandiéndose en sectores críticos gracias a su capacidad de adaptación a nuevas tecnologías como la inteligencia artificial y el mantenimiento predictivo.
Referencias
DEEPAK PRABHAKAR[1], DHARMARAJ A [2]
[1] Research Scholar, Department of Management, Karpagam Academy of Higher Education, Coimbatore, Tamil Nadu, India
[2]Associate Professor, Department of Management, Karpagam Academy of Higher Education, Coimbatore, Tamil Nadu, India
[3] Turner, S. (2002). PMO Optimisation: A Tool for Improving Operations and Maintenance in the 21st Century. International Conference of Maintenance Professionals. Melbourne.