Tabla de Contenidos
- ¿Qué es la IBR y cómo mejorar su eficacia?
- Cómo mejorar la eficacia de los programas de IBR
- Metodología RBI en tanques de almacenamiento
- Integración de la matriz de riesgo
- Planificación estratégica del programa RBI
- RBI Evergreen: Manteniendo el modelo de riesgo vivo
- Cómo aplicar RBI a tanques de almacenamiento
- La robótica en la inspección de tanques de almacenamiento basada en riesgos
- Conclusión
- Referencias
Los planes tradicionales de inspección de tanques de almacenamiento suelen basarse en intervalos fijos dictados por normas como API Standard 653, que no reflejan las condiciones operativas reales ni la evolución de los perfiles de riesgo de estos activos. Este enfoque basado en el tiempo puede dar lugar a inspecciones innecesarias o a la pérdida de oportunidades para prevenir fallas. Por el contrario, la Inspección Basada en Riesgo (IBR) ofrece un enfoque más inteligente y estratégico al priorizar las inspecciones según la probabilidad y la consecuencia de falla específicas del activo y su contexto operacional.
La metodología RBI, basada en el estándar internacionalmente reconocido API RP 580 (Risk-Based Inspection) y complementada por el API RP 581 (Risk-Based Inspection Technology), se considera una práctica recomendada para la gestión de la integridad de activos. Este artículo examina su aplicación en tanques de almacenamiento, explora métodos para evaluar y optimizar su eficacia, describe la planificación estratégica necesaria y presenta una guía paso a paso para su implementación. Además, aborda el concepto de RBI Evergreen y el impacto de la tecnología robótica en el proceso.
¿Qué es la IBR y cómo mejorar su eficacia?
Se define como una metodología estructurada del estándar API 580 que proporciona las directrices requeridas para diseñar, implementar y mantener un programa confiable de inspección y mantenimiento en función del riesgo. Tiene como función optimizar la asignación de recursos, mejorar la seguridad y maximizar la integridad operativa de los activos mediante un análisis conjunto de la Probabilidad de Falla (PoF) y la Consecuencia de Falla (CoF).
Complementado por el API 581, que detalla los aspectos cuantitativos de la evaluación, el RBI permite calcular la PoF considerando factores como mecanismos de degradación, historial de inspecciones y condiciones operativas, mientras que la CoF se enfoca en los impactos potenciales sobre la seguridad, el medio ambiente y la economía.
El objetivo principal es concentrar los recursos finitos de inspección y mantenimiento en los activos críticos; con el fin de lograr beneficios tangibles como:
- Mayor seguridad y fiabilidad operativa: Al identificar y mitigar proactivamente los riesgos más significativos.
- Optimización de costos: Reduciendo inspecciones innecesarias en equipos de bajo riesgo y evitando paradas no planificadas.
- Intervalos de inspección optimizados: Posibilidad de extender los intervalos de forma segura, basados en datos y análisis de riesgo, sin comprometer la integridad.
- Alineación con estándares: Cumplimiento con las directrices de API 580 / API 581.
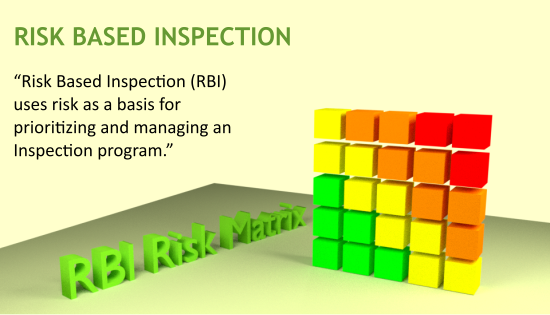
Cómo mejorar la eficacia de los programas de IBR
Una vez entendidos los principios fundamentales de la efectividad, resulta clave analizar cómo esta metodología se adapta específicamente a RBI en tanques de almacenamiento, cuyos desafíos operativos requieren un tratamiento diferenciado.
La efectividad de un programa RBI no se mide solo por realizar inspecciones, sino por la capacidad del programa para identificar correctamente los riesgos y guiar acciones de mitigación que reduzcan dichos riesgos de manera eficiente. Una inspección es efectiva si utiliza la técnica adecuada, en el lugar correcto y en el momento oportuno para detectar los mecanismos de daño activos antes de que conduzcan a una falla.
Para lograr una mayor efectividad del proceso, es necesario considerar los siguientes aspectos:
- Comprensión del PoF y CoF: Identificar correctamente los factores que impulsan la probabilidad (corrosión, fatiga, condiciones operativas) y las consecuencias (tipo de producto, volumen, ubicación, impacto ambiental/seguridad).
- Selección adecuada de técnicas de inspección (intrusivas vs no intrusivas): Elegir métodos de Ensayo No Destructivo (NDT) que sean capaces de detectar y cuantificar los mecanismos de daño esperados. Por ejemplo, Ultrasonido Convencional (UT), Phased Array (PAUT), Fuga de Flujo Magnético (MFL), Corrientes Pulsadas (PEC), etc. La elección entre inspecciones intrusivas (requieren sacar el tanque de servicio) y no intrusivas (realizarse en operación, a menudo con robótica) es precisa para la optimización del RBI.
- Vinculación de mecanismos de daño con métodos de inspección: Asegurar que la técnica seleccionada tenga una alta probabilidad de detección (PoD) para el daño específico que se busca (ej., MFL para corrosión del fondo, PAUT para soldaduras).
- Calidad y validación de datos: La precisión de los datos de entrada (espesores, tasas de corrosión, historial) es fundamental. Validar los resultados de la inspección y usarlos para recalibrar los modelos RBI.
- Actualización continua: Implementar un modelo que se actualice regularmente con nuevos datos para mantener la precisión del perfil de riesgo operacional.
Una métrica utilizada para evaluar si el RBI es efectivo es la Eficacia Global de la Inspección (OIE), la cual pondera la calidad de la planificación, la ejecución y el análisis de los resultados de la inspección en relación directa con la mitigación del riesgo cuantificado. Una alta OIE se logra cuando los recursos se enfocan en áreas de alto riesgo y se aplican las estrategias de mitigación adecuadas.
Metodología RBI en tanques de almacenamiento
La aplicación del RBI a tanques de almacenamiento requiere una consideración detallada de sus características únicas y los mecanismos de degradación específicos, superando los enfoques tradicionales basados en intervalos fijos como los establecidos en la API 653. La evaluación debe desglosarse por componentes principales, considerando los mecanismos de daño, factores de probabilidad y consecuencia de falla, y las técnicas de inspección apropiadas.
Fondo y anillo anular
- Mecanismos de daño: Corrosión del lado del suelo (contacto con la base/suelo húmedo), corrosión lado producto (corrosión influenciada microbiológicamente, fallas localizadas del revestimiento), corrosión atmosférica en el borde del fondo, picaduras, asentamientos diferenciales.
- Factores PoF: Edad del tanque, tipo y condición del revestimiento interno y sistema de protección catódica (si aplica), tipo de producto (presencia de agua libre/emulsionada), diseño y condición de la base, historial documentado de fugas, resultados de MFL/UT previos.
- Factores CoF: Volumen del tanque, tipo de producto (toxicidad, inflamabilidad), proximidad a acuíferos, áreas pobladas, diques de contención.
- Técnicas NDT comunes: Inspección visual, UT para medición de espesores puntuales, escaneo MFL (Magnetic Flux Leakage) y Ondas Guiadas en Fases (GWPA) para detección de corrosión general; Corrientes de Eddy Pulsados (PEC) para la inspección de la placa anular desde el exterior. Actualmente, existen equipos robotizados que inspeccionan el fondo sin vaciar el tanque.
Casco
- Mecanismos de daño: Corrosión externa (atmosférica, Corrosión Bajo Aislamiento – CUI en tanques aislados), corrosión interna (nivel de líquido variable, producto corrosivo), adelgazamiento general, agrietamiento).
- Factores de PoF: Edad, efectividad del sistema de pintura/aislamiento, condiciones ambientales (humedad, salinidad), temperatura de operación, corrosividad del producto.
- Factores de CoF: Altura del tanque, volumen, tipo de producto, ubicación (impacto de derrame).
- Técnicas NDT comunes: UT, VT, Termografía (para CUI), PEC.
Techo (Fijo o flotante)
- Mecanismos de daño: Corrosión interna (fase vapor), corrosión atmosférica, CUI (techos aislados), daños estructurales (acumulación de agua, viento).
- Factores de PoF: Diseño del techo, efectividad del recubrimiento, drenaje, condiciones ambientales.
- Factores de CoF: Riesgo de emisión de vapores, colapso estructural (raro pero severo), pérdida de producto por evaporación en techos flotantes.
- Técnicas NDT comunes: VT, UT, drones para inspección visual externa.
Boquillas y accesorios
- Mecanismos de daño: Corrosión localizada, erosión, fatiga por tensiones (vibración, asentamiento), agrietamiento en soldaduras.
- Factores de PoF: Diseño, cargas externas, historial de servicio.
- Factores de CoF: Tamaño de la boquilla, ubicación (cerca del fondo), tipo de servicio.
- Técnicas Comunes: UT, MT, PT, PAUT.
Integración de la matriz de riesgo
Para una evaluación integral del riesgo, se emplea una matriz de riesgo específica para tanques de almacenamiento. Esta matriz cruza la probabilidad de falla y la consecuencia de falla identificadas para cada combinación de componente y mecanismo de daño. La matriz de riesgo puede ser cualitativa, semicuantitativa o cuantitativa, dependiendo de la disponibilidad de datos y los objetivos del análisis. Su principal función es visualizar y clasificar los niveles de riesgo (por ejemplo, bajo, medio, alto, crítico), lo que a su vez permite priorizar las acciones de la inspección basada en riesgo en tanques y mantenimiento de manera estratégica, enfocando los recursos en las áreas de mayor riesgo.
Planificación estratégica del programa RBI
La planificación estratégica es la base sobre la cual se construye un programa RBI exitoso y sostenible. Mientras que la metodología describe la ejecución técnica, la planificación de la inspección RBI define el marco de trabajo, los recursos y la filosofía que guiarán todo el esfuerzo. Un plan preciso asegura que los objetivos sean claros, los recursos se asignen eficientemente y se utilicen herramientas adecuadas.
Componentes clave
- Alineación organizacional y definición de objetivos estratégicos
- Compromiso gerencial
- Establecimiento de metas claras y medibles (SMART)
- Definición del alcance inicial y planificación de expansión
- Estructura del programa, roles y recursos
- Formación de un equipo multidisciplinario
- Definición de roles y responsabilidades
- Asignación de presupuesto y herramientas requeridas
- Establecimiento del marco de gestión de datos
- Identificación de requisitos de datos esenciales
- Determinación de fuentes y validación de datos antes del modelado
- Selección e implementación de plataformas tecnológicas adecuadas
- Definición del marco metodológico y tolerancia al riesgo
- Selección de la metodología de análisis RBI (cualitativo, semicuantitativo, cuantitativo)
- Adaptación de criterios y establecimiento de la matriz de riesgo corporativa
- Proceso de revisión de mecanismos de daño (DMR)
- Estrategia de implementación, mitigación y sostenibilidad
- Desarrollo de un plan de implementación con cronograma realista
- Definición de la filosofía de mitigación adaptada a los diferentes niveles de riesgo
- Institucionalización del ciclo de revisión
Herramientas y soporte para la planificación de la inspección RBI
- Software RBI: Herramientas comerciales como PCMS, Capstone RBMI, SagePlus, API RBI Software, etc., facilitan los cálculos, la gestión de datos y la planificación.
- Normativas: API 580 (marco metodológico general), API 581 (metodología cuantitativa detallada), API 653 (Inspección, reparación y alteración de tanques), ISO 55000 (gestión global de activos).
RBI Evergreen: Manteniendo el modelo de riesgo vivo
El enfoque RBI Evergreen representa una evolución respecto al modelo tradicional de RBI. En lugar de realizar evaluaciones estáticas cada varios años, el modelo Evergreen se caracteriza por su capacidad para actualizarse continuamente con datos en tiempo real, permitiendo una gestión dinámica del riesgo.
Herramientas tecnológicas para un RBI Evergreen
La implementación efectiva de un modelo RBI Evergreen se apoya en diversas tecnologías que facilitan la recopilación, análisis y actualización continua de datos:
- Sensores IoT: Estos dispositivos permiten el monitoreo en tiempo real de variables críticas como temperatura, presión y corrosión, proporcionando datos actualizados sobre las condiciones operativas del activo.
- Plataformas de análisis predictivo: Utilizan algoritmos avanzados para analizar los datos recopilados, identificar patrones y predecir posibles fallas, permitiendo una planificación proactiva de las inspecciones y el mantenimiento.
- Software de gestión de RBI: Herramientas como GE Digital APM y DNV Synergi Plant integran datos de múltiples fuentes, automatizan el análisis de riesgos y facilitan la toma de decisiones informadas.
La norma API 580 enfatiza la importancia de mantener un programa RBI actualizado y dinámico, destacando que la gestión efectiva del riesgo requiere la integración de datos en tiempo real y la capacidad de adaptarse a cambios en las condiciones operativas. Asimismo, API 581 proporciona metodologías cuantitativas para evaluar la PoF y CoF, las cuales son integradas en plataformas tecnológicas para mejorar la precisión y eficiencia del programa RBI.
Cómo aplicar RBI a tanques de almacenamiento
Implementar un programa RBI para tanques sigue un flujo de trabajo estructurado:
Definir objetivos y alcance: Categorizar los tanques (ej., atmosférico, de techo cónico/flotante, presurizado), definir su criticidad operativa y establecer metas de fiabilidad y optimización de intervalos de inspección de estos equipos.
- Recopilar y validar datos: Reunir especificaciones de diseño (materiales, espesores nominales), historial de servicio (productos almacenados, temperaturas), datos de inspecciones previas (tasas de corrosión medidas, CMLs), estado de recubrimientos, registros de mantenimiento y reparación, y condiciones ambientales; la validación de datos es un punto estratégico en el RBI.
- Identificar los mecanismos de degradación: Para cada tanque y componente, identificar los mecanismos de daño activos y potenciales (ej., corrosión interna, corrosión atmosférica externa, picaduras en fondo por MIC). Agrupar tanques con condiciones similares optimiza el análisis.
- Calcular PoF y CoF: Aplicar modelos cualitativos, semicuantitativos o preferiblemente cuantitativos (ver API 581 Secciones 6 y 7 para metodologías detalladas de cálculo) para estimar la probabilidad de falla de cada mecanismo (edad, histórico, variables operacionales) y las consecuencias asociadas (ambientales, seguridad, económicas). Si los datos son limitados, se inicia con un enfoque cualitativo y se define a medida que se obtienen más datos a un enfoque cuantitativo.
- Evaluar y clasificar el riesgo: Combinar PoF y CoF en la matriz de riesgo para determinar el nivel de riesgo (bajo, medio, alto, crítico) de cada componente / mecanismo de daño. Esto permite la priorización de activos.
- Planificar la estrategia de inspección y mitigación: Basándose en el nivel de riesgo, definir:
- Frecuencia de inspección: Intervalos más cortos y/o inspecciones más exhaustivas para componentes de alto riesgo; extensión segura y justificada de intervalos para componentes de bajo riesgo.
- Alcance de la inspección: Definir qué porcentaje del componente se inspeccionará y dónde concentrar los esfuerzos (ej., inspección del 100% del fondo vs. UT puntual en CMLs del casco).
- Técnicas NDT apropiadas: Seleccionar las técnicas más efectivas para los mecanismos de daño dominantes (ej., MFL de alta resolución para fondos críticos, PAUT para soldaduras importantes).
- Acciones de mitigación prescritas: Definir acciones correctivas o preventivas específicas (ej., reparación de revestimiento, mejora de drenaje, aplicación de inhibidores, reemplazo planificado).
- Ejecutar y supervisar: Realizar las inspecciones según el plan. Considerar inspección no intrusiva / robótica para inspecciones internas o en altura sin sacar de servicio el equipo.
- Revisión y actualización post-inspección: El programa RBI debe actualizarse periódicamente con nuevos datos de inspección, cambios operativos, reparaciones o nueva información sobre mecanismos de daño. Esto mantiene el modelo «vivo» o Evergreen.
El resultado de una evaluación RBI es un plan de inspección. Este plan se fundamenta en la determinación de objetivos o límites de riesgo aceptables para cada componente evaluado. Cuando el riesgo estimado de un componente alcanza o supera estos objetivos, es importante implementar acciones específicas, como inspecciones o medidas de mitigación, para garantizar la integridad operativa del equipo.
Inspección tradicional (Basada en tiempo – API 653) vs. RBI (API RP 580 / 581)
Aspecto | Inspección tradicional | Inspección basada en el riesgo |
Frecuencia | Intervalos fijos predefinidos | Variable, basada en el riesgo calculado |
Enfoque | Uniforme para todos los activos similares | Prioridad en activos críticos o alto riesgo |
Base Decisión | Tiempo / calendario | Riesgo (PoF x CoF) y condición actual |
Costo | Potencialmente elevado (inspecciones innecesarias) | Optimizado, enfocado donde más se necesita |
Eficacia | Puede ser baja (inspeccionar lo no crítico) | Elevada (enfocada en prevenir fallas significativas) |
Flexibilidad | Baja, rígida | Alta, adaptable a cambios operativos y de condición |
Optimización | Limitada | Máxima optimización de recursos y seguridad |
RBI Estándar vs. RBI Evergreen
Aspecto | RBI estándar (Evaluación periódica) | RBI Evergreen (Modelo dinámico) |
Frecuencia / actualización | Cada 3-5 años o tras eventos mayores | Continuamente con nuevos datos |
Integración de datos | Manual y periódica | Automatizada (idealmente), integración continua |
Respuesta al cambio | Retrasada hasta la próxima revisión | Ajuste inmediato a cambios en condición |
Optimización inspección | Basada en «fotos» pasadas del riesgo | Refinada dinámicamente con últimas tendencias |
Asignación recursos | Reactiva a la última evaluación | Proactiva y basada en datos vivos |
Cumplimiento normativo | Cumple requisitos mínimos en el momento | Supera estándares mediante seguimiento en vivo |
La robótica en la inspección de tanques de almacenamiento basada en riesgos
La robótica es un habilitador estratégico para optimizar los programas RBI en tanques, especialmente para inspecciones no intrusivas. Robots autónomos u operados remotamente (sumergibles, flotantes, magnéticos) pueden:
- Realizar inspecciones internas (fondos, anillos anulares) sin necesidad de sacar el tanque de servicio, reduciendo costos y tiempos de parada.
- Recopilar datos de alta calidad para la evaluación de PoF: mediciones de espesor (UT, PAUT), detección de corrosión (MFL, GWPA , PEC), y uso de sistemas de visión artificial.
- Mejorar la seguridad al minimizar la entrada a espacios confinados.
- Integrar datos directamente en el software RBI, agilizando la actualización del modelo de riesgo y la toma de decisiones.
Mediante el uso de la tecnología robótica se logra obtener información sobre la condición real del activo, fundamental para refinar los cálculos de PoF, justificar la extensión de intervalos y enfocar el mantenimiento en los componentes más críticos. Empresas como Gecko Robotics han desarrollado robots trepadores equipados con sensores avanzados que permiten realizar inspecciones no destructivas en tanques; recopilan datos sobre el espesor de las paredes y otros indicadores de integridad estructural, integrándose con plataformas de software RBI para análisis en tiempo real.
Conclusión
La implementación de la Inspección Basada en Riesgo (RBI), fundamentada en el estándar API 580, permite priorizar inspecciones en función del riesgo real de los tanques, optimizando recursos técnicos y reduciendo intervenciones innecesarias. Este enfoque, complementado con los cálculos cuantitativos del API 581 y actualizado continuamente mediante la filosofía Evergreen, fortalece la toma de decisiones basada en datos confiables.
Referencias
- API Recommended Practice 580 – Risk Based Inspection
- API Recommended Practice 581 – Risk Based Inspection Technology
- API Standard 653 – Tank Inspection, Repair, Alteration, and Reconstruction
- https://www.iqpc.com/media/7466/10042.pdf