Tabla de Contenidos
En la industria petrolera, los hornos de procesos son relevantes para la transformación de recursos fósiles en productos refinados. Estos equipos térmicos son sumamente importantes, porque al fallar su servicio se detienen los procesos de las plantas, lo que indica que se debe llevar una operación eficiente y segura, para lo se requiere una evaluación integral y regular. El objetivo de este artículo es exponer en detalle la importancia de la evaluación de los hornos en la industria petrolera, las técnicas utilizadas y cómo mejorar la eficiencia de estos equipos.
¿Qué es un horno de procesos?
Es un equipo utilizado en la industria para aplicar calor a recursos fósiles o productos intermedios con el fin de llevar a cabo reacciones químicas específicas. Estos hornos están diseñados para alcanzar y mantener temperaturas elevadas de manera controlada, lo que facilita la evaporación, la descomposición térmica y otras transformaciones necesarias en los procesos como el de refinación del petróleo.
Configuración y partes de un horno de procesos
Los hornos de procesos en la industria petrolera están diseñados para optimizar la transferencia de calor hacia los fluidos que se procesan. Estos constan de varias partes esenciales: cámaras de combustión, donde se queman los combustibles para generar calor; cámaras de convección, que inician el calentamiento de los tubos mediante los gases de combustión; y tubos de intercambio térmico, por donde circula el fluido a calentar. Además, incluyen quemadores, sistemas de control para regular la temperatura y el flujo de aire, y aislamiento térmico que ayuda a prevenir las pérdidas de calor.
Principales partes de un horno de procesos
En la figura 1 se muestra un esquema del horno y sus componentes principales.
- Quemadores: Mezclan el combustible con el aire y generan la llama necesaria para el calentamiento. Deben ser capaces de manejar diferentes tipos de combustibles y ofrecer una llama estable y eficiente.
- Tubos: Elementos por donde circula el producto a ser calentado, permitiendo la transferencia de calor del fuego y los gases calientes a los tubos. Están fabricados en materiales resistentes a altas temperaturas y a la corrosión.
- Curvas o cabezales en los extremos de los tubos: Estos elementos están ubicados en los extremos de los tubos y se encargan de dirigir el flujo por cada uno de ellos. También permiten la conexión segura entre tubos y otras secciones del proceso.
- Refractario: Material que reviste el interior del horno, protegiendo las estructuras metálicas del calor y ayudando a mantener una temperatura interna uniforme y a minimizar la pérdida de calor.
- Paredes metálicas: Componen la estructura externa del horno y proporcionan a los componentes internos, además de ayudar a contener el calor dentro del horno.
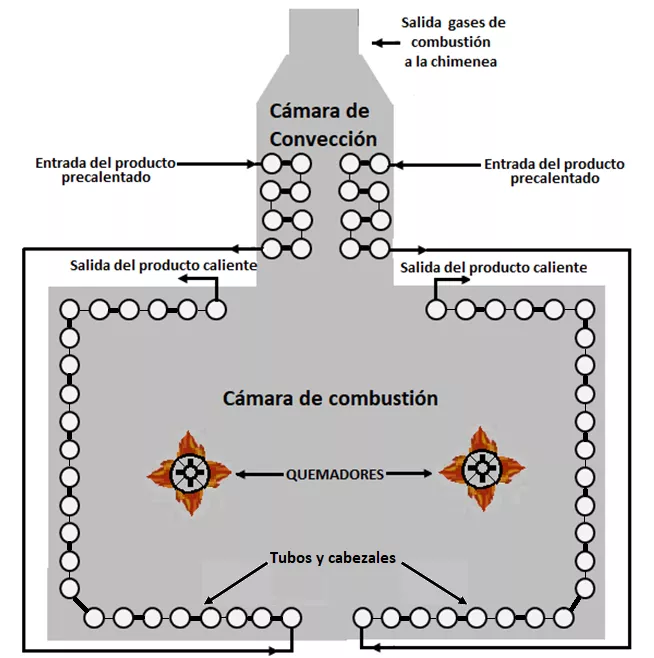
Eficiencia de los hornos en la industria petrolera
Se define como la capacidad que tiene el horno para transferir efectivamente el calor generado hacia el proceso deseado (como el calentamiento de crudo o derivados) con el mínimo consumo de energía y emisiones. Varios parámetros son fundamentales para asegurar y evaluar esta eficiencia:
- Eficiencia térmica: Se refiere a la proporción del calor generado que se utiliza efectivamente en el proceso. La eficiencia térmica es crítica y se puede mejorar con un diseño adecuado del horno, buen mantenimiento y operación eficiente.
- Relación aire-combustible: Una mezcla óptima de aire y combustible es esencial para una combustión completa y eficiente. Un exceso de aire puede llevar a pérdidas de calor no aprovechadas y la insuficiencia de aire puede resultar en una combustión incompleta, aumentando las emisiones de compuestos nocivos.
- Control de la combustión: Los sistemas de control avanzados permiten ajustar la operación del horno en tiempo real para optimizar la combustión, mejorar la transferencia de calor y reducir el consumo de energía y las emisiones.
- Aislamiento y mantenimiento del refractario: El mantenimiento adecuado del material refractario que recubre internamente el horno es vital para minimizar las pérdidas de calor y el sobrecalentamiento de las paredes metálicas. Un refractario en mal estado puede significar una eficiencia térmica significativamente reducida.
- Integridad estructural y diseño del horno: La forma y el tamaño del horno deben ser diseñados para maximizar la eficiencia de la transferencia de calor. Esto incluye la disposición de los tubos, la ubicación de los quemadores y la geometría general del horno.
- Monitoreo y mantenimiento regular: La eficiencia de un horno puede degradarse con el tiempo debido al desgaste, la acumulación de depósitos y otras condiciones operativas. Un programa de inspección de monitoreo constante y el mantenimiento regular ayuda a mantener la eficiencia operativa y a prevenir fallos.
- Capacidad de respuesta a las variaciones de carga: La capacidad del horno para ajustar eficazmente su operación en respuesta a las variaciones en la demanda de calor es muy importante para mantener la eficiencia en diferentes condiciones operativas.
Importancia de la evaluación de hornos de procesos en refinerías
La inspección de hornos de procesos en refinerías se realiza utilizando una variedad de metodologías y técnicas de ensayos no destructivos (END), que van desde inspecciones visuales hasta pruebas más avanzadas. Estas metodologías permiten detectar y evaluar diferentes tipos de daños y deterioros, como corrosión, erosión, fisuras, deformaciones y fallos en los revestimientos refractarios.
Al identificar y abordar estos problemas de manera oportuna, se pueden prevenir fallas imprevistas, minimizar tiempos de inactividad no planificados y reducir los costos de mantenimiento y reparación. La API 573 (Inspection of Fired Boilers and Heaters) es una de las prácticas recomendadas más importantes para la iInspección de hornos.
Técnicas de END para evaluar hornos industriales
Existen varios métodos y técnicas de ensayos no destructivos (END) desempeñan un papel fundamental en la inspección de hornos. Estas técnicas permiten inspeccionar la integridad de los equipos sin comprometer su funcionamiento o seguridad. Algunos de los métodos de END más comunes utilizadoas para evaluar hornos de procesos en la industria petrolera incluyen:
- Inspección visual: Es la metodología más básica e importante para la evaluación de hornos en la industria petrolera, detectando signos visibles de daño, como grietas, corrosión o deformaciones en la estructura del horno, desprendimiento de refractario y deformaciones longitudinales y diametrales de los tubos. Los inspectores utilizan herramientas como cámaras, calibradores, martillo de inspección y comparadores, entre otras, y según los resultados de la inspección se puede determinar si es necesario utilizar otras técnicas adicionales a las planificadas.
- Ultrasonido: Se utiliza para medir los espesores de los tubos y detectar defectos internos como grietas u otros tipos de discontinuidades, mediante el envío de ondas ultrasónicas a través del material del horno y registrando los ecos.
- Radiografía industrial: Esta metodología utiliza radiación ionizante para crear imágenes de alta resolución del interior del horno, lo que permite detectar defectos internos como grietas, inclusiones de material extraño o corrosión.
- Partículas magnéticas: Implica la aplicación de partículas magnéticas en la superficie del material a evaluar para detectar discontinuidades superficiales y subsuperficiales.
- Líquidos penetrantes: Son sustancias químicas que se aplican en los materiales penetrando en las grietas y discontinuidades abiertas a la superficie. Después de un tiempo de penetración, se limpia el exceso de líquido y se aplica un revelador para visualizar las discontinuidades.
- Termografía infrarroja: Es una técnica que utiliza cámaras especiales para capturar y visualizar el calor, detectando la radiación en el espectro infrarrojo y la convierten en una imagen visual (termograma, Figura 2). Su uso principal en los hornos de procesos es para monitorear las temperaturas externas en las paredes del horno para ubicar posibles daños en el refractario, igualmente para la evaluación de la eficacia de la transferencia de calor, la uniformidad de la temperatura dentro del horno y para detectar puntos calientes de los tubos que puedan ocasionar creep a los mismos.
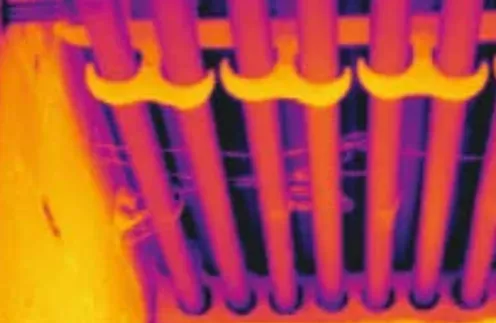
Eficiencia de los hornos de procesos
Además de garantizar la integridad estructural y la seguridad operativa de los hornos de procesos, también es importante evaluar y mejorar su eficiencia. La eficiencia de un horno se refiere a su capacidad para producir la cantidad deseada de calor o energía con el menor consumo de combustible y recursos posibles. Mejorar la eficiencia de los hornos de procesos puede tener varios beneficios, incluyendo la reducción de costos operativos, la minimización del impacto ambiental y la mejora de la competitividad en el mercado.
Para evaluar la eficiencia de un horno de proceso, es necesario considerar varios factores, incluyendo su diseño, tamaño, capacidad de carga, combustible utilizado, sistema de combustión, aislamiento térmico y mantenimiento. Algunas estrategias comunes para mejorar la eficiencia de los hornos de procesos incluyen:
- Optimización del combustible: Utilizar combustibles más eficientes y limpios, como el gas natural o el gas de proceso, en lugar de combustibles fósiles más contaminantes como el fueloil.
- Mejora del aislamiento térmico: Instalar materiales aislantes de alta calidad en el horno para reducir las pérdidas de calor y mejorar la retención de energía.
- Optimización del sistema de combustión: Ajustar los parámetros de combustión, como la relación aire-combustible, la distribución del aire y la temperatura de la llama, para maximizar la eficiencia y minimizar las emisiones.
- Implementación de tecnologías de recuperación de calor: Instalar sistemas de recuperación de calor para aprovechar el calor residual del horno y utilizarlo para precalentar el aire de combustión o generar vapor.
- Mantenimiento preventivo y correctivo: Es recomendable realizar la inspección de hornos regularmente, realizar limpiezas y mantenimientos de rutina para garantizar un funcionamiento óptimo del horno y prevenir problemas de eficiencia.
Conclusión
La evaluación integral de hornos en la industria petrolera es esencial para garantizar su operación segura y eficiente. Mediante técnicas avanzadas de ensayos no destructivos y análisis exhaustivos, es posible identificar y abordar problemas potenciales antes de que se conviertan en fallas costosas. Además, la mejora continua en la eficiencia de los hornos de procesos reduce los costos operativos y contribuye a la sostenibilidad ambiental al minimizar el consumo de energía y las emisiones de gases de efecto invernadero. Invertir en la evaluación integral de hornos es una estrategia para optimizar el rendimiento y la fiabilidad de las operaciones en la industria petrolera.
Referencias
- https://www.flir.com/discover/instruments/furnace-boiler/petroval ↩︎