Tabla de Contenidos
- Principio de funcionamiento de un horno rotatorio
- Ventajas de un horno rotatorio
- ¿Qué diferencias existen entre un horno rotatorio de calor directo y uno de calor indirecto?
- ¿Cómo influye la velocidad de rotación en la eficiencia térmica del horno?
- Modelos de hornos rotatorios
- ¿Cuáles son las principales industrias que utilizan hornos rotatorios y para qué procesos?
- Innovaciones y tendencias en el diseño de hornos rotatorios
- Conclusión
- Referencias
El horno rotatorio es un equipo de procesamiento térmico de carácter continuo ampliamente utilizado en operaciones industriales que requieren altas temperaturas y un tratamiento uniforme del material. Su diseño, basado en un tambor cilíndrico giratorio con control preciso de parámetros como la velocidad de rotación, la inclinación y el flujo de calor, permite realizar procesos de calcinación, secado, sinterización o incineración con elevada eficiencia térmica y operativa. Este tipo de horno juega un papel crucial en industrias como la cementera, la minera, la química y la del tratamiento de residuos, destacándose por su versatilidad, escalabilidad y capacidad de adaptación a distintas condiciones de operación.
En este artículo se analiza de manera técnica y detallada el principio de funcionamiento de un horno rotatorio, los modelos disponibles, sus aplicaciones industriales, así como las innovaciones más recientes en su diseño. Se responderán preguntas sobre su utilidad, ventajas operativas y criterios de diseño que inciden directamente en su desempeño térmico y en la calidad del producto final. Aplicaciones industriales. A través de un enfoque técnico y actualizado, se busca ofrecer una visión completa sobre su importancia y evolución en los procesos de producción térmica.
Principio de funcionamiento de un horno rotatorio
El principio de funcionamiento de un horno rotatorio se basa en la transferencia de calor a través de un tambor cilíndrico giratorio, ligeramente inclinado con respecto a la horizontal. El tambor gira lentamente sobre su eje longitudinal, permitiendo que los materiales procesados se mezclen y se expongan uniformemente a las fuentes de calor. El tratamiento térmico continuo se logra mediante la aplicación de calor directo o indirecto, dependiendo del diseño del equipo.
El cuerpo del horno está compuesto por un revestimiento interno de refractario que protege la estructura metálica externa del calor extremo y mejora la eficiencia térmica al mantener la temperatura constante durante el procesamiento. Los parámetros generales que manejas son los siguientes:
- Sistema de rotación: El cuerpo cilíndrico del horno está montado sobre rodamientos o llantas de apoyo (tyres) que descansan sobre ruedas de soporte (rollers). Un motor eléctrico, acoplado a través de un reductor de velocidad, impulsa un piñón que engrana con una corona dentada montada en el cilindro del horno. Este mecanismo convierte el movimiento del motor en una rotación lenta pero constante del tambor.
- Velocidad de rotación: Generalmente, varía entre 0.2 y 5 revoluciones por minuto (rpm), dependiendo del proceso y del tipo de material tratado. La rotación lenta permite un tiempo de residencia adecuado y asegura que todo el material esté expuesto de manera uniforme al calor.
- Efecto de la inclinación: El horno está inclinado con una pendiente del 1% al 4%, lo que facilita que, a medida que gira, el material avance por gravedad desde el extremo de carga (frío) hasta el extremo de descarga (caliente).
- Flujo de calor: En la mayoría de los casos, el horno opera con flujos en a contracorriente, es decir, los gases calientes del quemador se mueven en dirección opuesta a la carga. Esto mejora la eficiencia térmica y permite un aprovechamiento gradual del calor.
- Quemador y zona de combustión: En el extremo de descarga se encuentra el quemador principal, que puede funcionar con combustibles líquidos, sólidos o gaseosos, generando altas temperaturas necesarias para los procesos de calcinación, fusión, sinterización o incineración.
- Zonificación del horno: El horno puede dividirse térmicamente en varias zonas (secado, precalentamiento, calcinación, enfriamiento) dependiendo del proceso industrial, cada una de las cuales, está diseñada para lograr reacciones específicas.
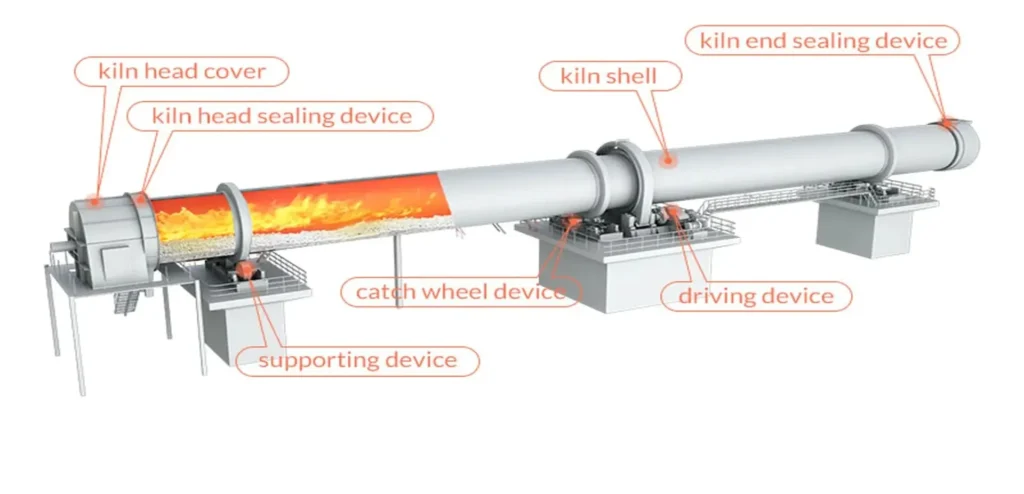
Ventajas de un horno rotatorio
Los hornos rotatorios ofrecen numerosas ventajas técnicas y operativas:
- Tratamiento térmico continuo: Facilitan un flujo constante de material y una producción ininterrumpida.
- Homogeneidad del producto final: La acción giratoria promueve una mezcla uniforme.
- Flexibilidad en el diseño: Se pueden adaptar a distintos tipos de procesos y materiales.
- Eficiencia térmica: Diseños modernos minimizan la pérdida de calor y reducen el consumo energético.
- Control de emisiones: Equipados con sistemas de filtrado y control de gases.
¿Qué diferencias existen entre un horno rotatorio de calor directo y uno de calor indirecto?
- Horno rotatorio de calentamiento directo: El calor se aplica directamente al material mediante la combustión interna de gases, siendo ideal para materiales que no se alteran químicamente al contacto con los gases calientes.
- Horno rotatorio de calentamiento indirecto: El calor se transfiere a través de la pared del tambor, sin contacto directo con los gases de combustión; este modelo es preferido para procesos donde se requiere una atmósfera inerte o para materiales sensibles.
¿Cómo influye la velocidad de rotación en la eficiencia térmica del horno?
La velocidad de rotación del horno rotatorio afecta directamente el tiempo de residencia del material dentro del tambor, y, por tanto, su eficiencia térmica. Una velocidad demasiado alta reduce el tiempo de exposición al calor, impidiendo un tratamiento adecuado. Por el contrario, una rotación muy lenta puede generar acumulación de material y puntos fríos. El equilibrio entre estos factores permite una transferencia de calor óptima y una calidad constante del producto final.
Modelos de hornos rotatorios
Existen diferentes modelos de hornos rotatorios diseñados para aplicaciones específicas. Los más comunes incluyen:
- Llama directa: Utiliza quemadores en el interior del tambor. Alta eficiencia para procesos como la producción de cemento y cal.
- Llama indirecta: Diseñado con una cámara externa de combustión. Ideal para el tratamiento de residuos o materiales delicados.
- Con intercambiador de calor: Incluye sistemas de recuperación energética que reutilizan el calor residual.
- Modulares: Diseños compactos y flexibles, usados en laboratorios o plantas piloto.
Estos modelos de hornos rotatorios responden a la necesidad de optimizar procesos térmicos con diferentes requisitos de temperatura, tiempo y tipo de material.
¿Cuáles son las principales industrias que utilizan hornos rotatorios y para qué procesos?
Estos equipos tienen aplicaciones en múltiples industrias debido a su operatividad de manera continua, controlar temperaturas extremas y asegurar una mezcla homogénea de materiales durante el tratamiento térmico. A continuación, se describen las principales industrias que los emplean, junto con los procesos específicos:
- Industria cementera: Para la calcinación del crudo (mezcla de caliza, arcilla y otros aditivos) y la obtención de clinker. El material crudo es sometido a temperaturas que superan los 1400 °C, provocando la sinterización y formación de clinker, el componente principal del cemento Portland.
- Minería y metalurgia: En pirometalurgia para la reducción de minerales y transformación de minerales metálicos como el hierro, níquel, cobre y litio. También son fundamentales para la fusión y aglomeración de concentrados metálicos.
- Industria química: Para la deshidratación, cloración, sulfatación y piroprocesamiento. Los hornos rotatorios permiten llevar a cabo reacciones químicas a alta temperatura, como la producción de óxidos metálicos, la fabricación de fertilizantes (por ejemplo, nitrato de amonio o sulfato de amonio), y el tratamiento térmico de productos intermedios en síntesis industrial.
- Gestión de residuos: Incineración, gasificación o carbonización de residuos urbanos, industriales o en hospitales. Se emplea para destruir residuos peligrosos bajo condiciones controladas de temperatura y tiempo. Gracias a su diseño cerrado y la rotación constante, asegura una combustión homogénea y completa.
- Industria cerámica y de materiales refractarios: Tratamiento térmico para endurecer, estabilizar o modificar propiedades físico-químicas con el fin de sinterizar materiales cerámicos, la cocción de ladrillos refractarios, la activación térmica de arcillas y la formación de fases minerales estables. Las temperaturas de operación varían entre 900 y 1600 °C, dependiendo del producto final.
Innovaciones y tendencias en el diseño de hornos rotatorios
Las tecnologías recientes han permitido el desarrollo de hornos rotatorios más eficientes, sostenibles y adaptables:
- Automatización y control digital: Sistemas SCADA permiten una supervisión en tiempo real del proceso térmico.
- Materiales refractarios avanzados: Mejoran la durabilidad del revestimiento y reducen pérdidas de calor.
- Diseño energéticamente eficiente: Uso de intercambiadores de calor y combustibles alternativos.
- Sistemas de reducción de emisiones: Tecnologías de depuración que minimizan el impacto ambiental.
- Modularidad y movilidad: Equipos compactos para instalaciones temporales o de investigación.
Conclusión
El horno rotatorio es una herramienta significativa en los procesos de calcinación industrial, tratamiento de residuos y procesamiento térmico en múltiples sectores. La diversidad de modelos de hornos rotatorios y su capacidad para operar de forma continua con alta eficiencia lo convierten en un recurso indispensable en la industria moderna. La incorporación de innovaciones tecnológicas asegura su relevancia en un contexto industrial cada vez más exigente y orientado a la sostenibilidad.
Referencias
Fuente propia