¿Estás luchando contra el flash rust? Este fenómeno de óxido superficial, de aparición rápida y con repercusiones en la durabilidad y funcionalidad de las estructuras metálicas, es un problema común en la protección de metales, especialmente después de procesos de limpieza y preparación de superficies húmedas como el arenado con agua o el lavado a presión.
El flash rust, también conocido como oxidación instantánea o herrumbre fugaz, puede comprometer la adherencia y el desempeño de los recubrimientos protectores, afectando directamente la vida útil de las estructuras metálicas.
Comprender las causas subyacentes de su formación y aplicar estrategias efectivas de prevención del óxido es determinante para el tratamiento del óxido y el rendimiento del acabado de metales, particularmente en la industria de la protección anticorrosiva. En este artículo se diserta los mecanismos de formación del flash rust, los factores que contribuyen a su aparición y las estrategias clave para su prevención.
¿Qué es el flash rust?
El flash rust es un proceso corrosivo superficial que ocurre rápidamente en sustratos metálicos expuestos a la humedad, desencadenando una reacción inmediata con el oxígeno y comprometiendo la calidad del tratamiento y acabado de metales. A diferencia de la corrosión generalizada, este fenómeno se manifiesta como una capa superficial de óxido de color rojizo o anaranjado que puede aparecer en cuestión de minutos u horas.
Aunque es un fenómeno superficial, su presencia es problemática, interfiriendo significativamente en la interfase entre el sustrato metálico y los sistemas de protección aplicados. Esta capa de óxido superficial, modifica la energía superficial del metal y crea una barrera física que dificulta la correcta humectación y el anclaje mecánico de pinturas, recubrimientos protectores y otros acabados.
La consecuente reducción en la adhesión compromete la durabilidad y eficacia a largo plazo de la protección de metales, exponiendo los activos industriales a una corrosión prematura y al posible incumplimiento de sus especificaciones operacionales.
¿Cómo se forma el flash rust?
Su formación es un proceso electroquímico que ocurre cuando la superficie metálica tratada por limpieza o por corte y se expone al aire, entrando en contacto con la humedad y el oxígeno, dando lugar a oxidaciones instantáneas, la cual está compuesta principalmente por hidróxido de hierro. En estas condiciones, se establecen microcélulas de corrosión, donde se desarrollan reacciones anódicas y catódicas simultáneamente.
En las áreas anódicas, el hierro metálico (Fe) se oxida, liberando iones de hierro (Fe²⁺) al agua superficial:
- Reacción anódica (oxidación del hierro): Fe → Fe+2 + 2e− Estos iones Fe²⁺ disueltos migran hacia las áreas catódicas, donde reaccionan con el oxígeno disuelto en el agua y los electrones generados en la reacción anódica, formando iones hidróxido (OH⁻).
- Reacción catódica (reducción del oxígeno): O2 + 2H2O + 4e− → 4OH− A continuación, los iones Fe²⁺ reaccionan con los iones hidróxido (OH⁻) para formar hidróxido ferroso [Fe(OH)₂], que es inestable y, en presencia de oxígeno y agua, se oxida aún más para formar hidróxido férrico [Fe(OH)₃], el principal componente del óxido.
- Formación del óxido superficial: 4Fe(OH)2 + O2 + 2H2O → 4Fe(OH)3 (Amarillo, anaranjado brillante o rojizo-marrón son los colores característicos del flash rust) Este proceso ocurre rápidamente debido a la alta reactividad de la superficie metálica recién limpiada, junto con la presencia de una capa delgada de agua, que facilita el transporte de iones y las reacciones electroquímicas.
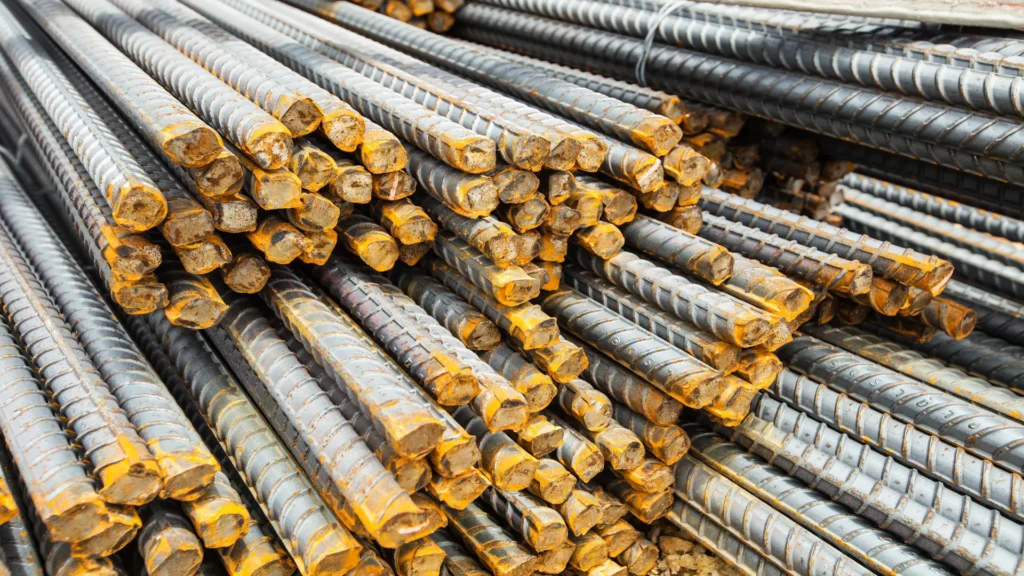
Factores que contribuyen a la formación del flash rust
Entre los factores más importantes que aceleran el proceso de oxidación instantánea, se encuentra:
- Humedad relativa: Para prevenir la oxidación instantánea es importante controlar la humedad. Un ambiente húmedo eleva y acelera el proceso electroquímico, favoreciendo la formación de óxidos superficiales.
- Temperatura: Las altas temperaturas aceleran las reacciones químicas, aumentando la velocidad de formación de óxidos.
- Contaminantes en el sustrato: Sales solubles como cloruros y sulfatos actúan como electrolitos, intensificando la corrosión. Estos contaminantes pueden quedar después de procesos de limpieza inadecuados.
- Calidad del agua utilizada en la limpieza: Si contiene iones corrosivos, acelera la oxidación.
- Acabado superficial del metal: Superficies rugosas o porosas retienen más humedad y contaminantes.
- Tipo de acero: Los aceros al carbono son más susceptibles al flash rust en comparación con los aceros inoxidables o aleados.
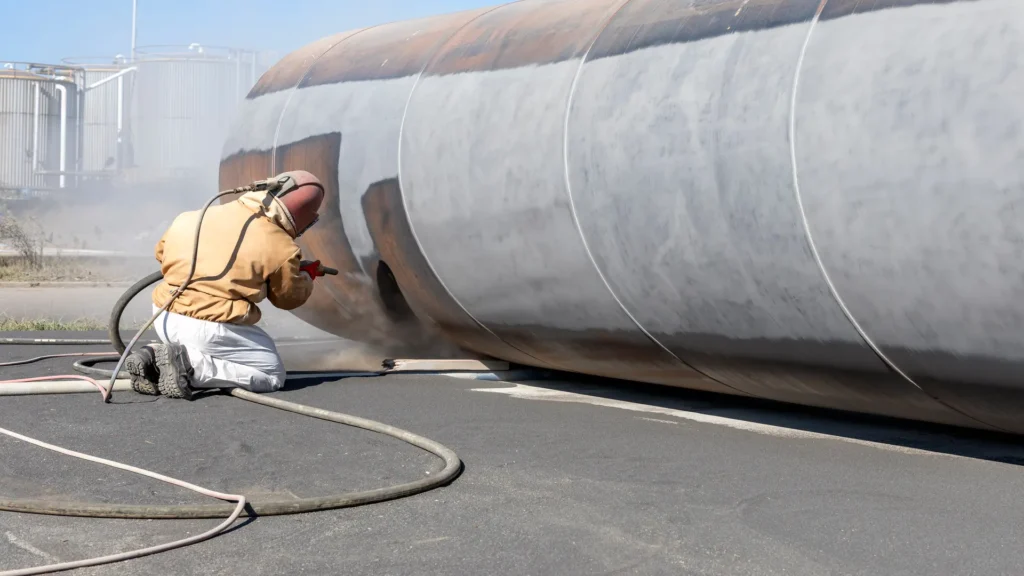
Estrategias para la prevención del flash rust
Para mantener las superficies metálicas en condiciones óptimas, es necesario implementar medidas de prevención del óxido superficial, prestando especial atención a las piezas manufacturadas de hierro, fundición o acero al carbono. Cuanto más sensible sea el metal, más fenómenos oxidativos se producirán.
- Control de la humedad ambiental: Al eliminar la humedad, se controla el proceso de corrosión, eliminando un elemento básico para el desarrollo del óxido.
- Secado rápido: Uso de aire comprimido seco o calor controlado tras la limpieza húmeda.
- Ajuste en la limpieza de superficies: Modificar las técnicas de limpieza, mediante el uso de agua desionizada para evitar la acumulación de sales solubles o reducir el tiempo de exposición, evitan la oxidación instantánea.
- Aplicación de inhibidores de óxido: Durante la limpieza de la superficie se recomienda aplicar aditivos y formadores de barreras químicas.
- Empleo de imprimaciones con inhibidores de corrosión: Un imprimador e inhibidor de corrosión de alta calidad puede evitar que el metal desnudo quede expuesto a la humedad y al oxígeno.
- Aplicación rápida de recubrimientos protectores: Una vez que la superficie metálica esté limpia y seca, la aplicación del recubrimiento protector primario debe realizarse de manera inmediata para aislar el metal del ambiente corrosivo.
- Cuidado de la superficie expuesta: Evitar la contaminación de la superficie limpia con sales, polvo o huellas dactilares, ya que estos actúan como puntos de inicio para la oxidación.
- Protección especial en zonas de corte: Las áreas donde el acero ha sido cortado, ya sea por medios mecánicos o térmicos, presentan susceptibilidad y puntos reactivos. Estas zonas requieren limpieza y la aplicación de inhibidores de óxido de manera inmediata para prevenir la rápida aparición de flash rust debido a la exposición del metal base sin la capa protectora original.
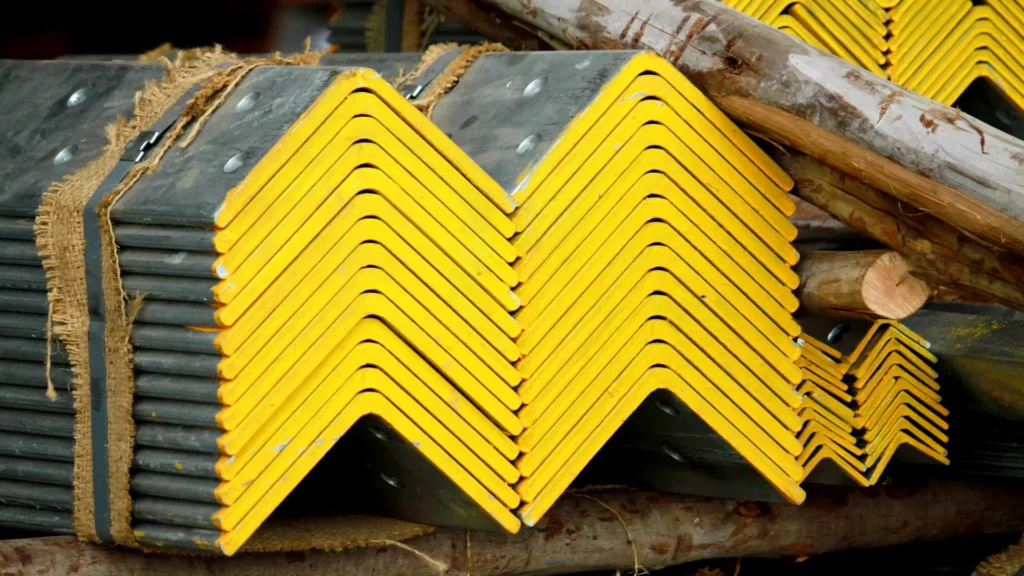
Inhibidores de óxido y su función en la prevención del flash rust
Los inhibidores de óxido son compuestos químicos que se añaden al agua de limpieza o se aplican directamente sobre superficies metálicas para retardar la oxidación. Su uso es fundamental y actúa mediante varios mecanismos:
- Formación de una barrera protectora: Estos compuestos crean una película delgada sobre la superficie del metal, impidiendo el contacto directo con la humedad y el oxígeno, factores básicos para la corrosión.
- Pasivación de la superficie metálica: Los inhibidores forman una capa pasiva que reduce su reactividad, dificultando el inicio de procesos corrosivos.
- Secuestro de iones corrosivos: Algunos inhibidores neutralizan o inmovilizan iones corrosivos presentes en el ambiente o en el agua de limpieza, evitando su interacción con el metal base.
- Inhibición de reacciones electroquímicas: Estos compuestos interfieren en las reacciones anódicas o catódicas que facilitan la corrosión, ralentizando el proceso.
La elección del inhibidor adecuado depende de factores como el tipo de metal, las condiciones ambientales y la compatibilidad con los recubrimientos posteriores.
Soluciones en inhibidores de óxido
La empresa Cortec Corporation, una empresa de química verde destacada por sus capacidades de I+D y su enfoque en la creación de soluciones innovadoras para la protección contra la corrosión, ha desarrollado el VpCI®-377 un inhibidor de óxido concentrado de base acuosa. Este aditivo cumple con estrictos requisitos antipolución y ofrece una amplia gama de diluciones con agua (0.5-20%), lo que permite personalizar la duración de la protección y el costo aplicado por unidad de área.
El VpCI®-377 forma una solución en agua y se aplica a superficies metálicas mediante pulverización o inmersión. No es necesario retirarlo, pero, puede eliminarse con limpiadores alcalinos convencionales; es especialmente eficaz en la prevención del flash rust, porque el óxido aparece mucho después de la limpieza con agua; debido a que forma una barrera protectora que aísla el metal del agua y el aire, y calma la superficie para que no se oxide tan rápido.
Tratamiento del óxido superficial
Si el flash rust ya se ha formado, se recomienda realizar las siguientes acciones previo a la aplicación del recubrimiento:
- Cepillado mecánico o abrasivo para remover el óxido superficial.
- Uso de removedores químicos diseñados para disolver el óxido sin dañar el metal.
- Aplicación de imprimaciones convertidoras de óxido que transforman la corrosión en una capa estable y recubrible.
Conclusión
El flash rust es un problema recurrente en la industria del tratamiento y acabado de metales, afectando la calidad y durabilidad de los recubrimientos protectores. La implementación de estrategias adecuadas de prevención del óxido, como el control de humedad, aplicación de inhibidores de óxido y recubrimientos protectores de alto rendimiento, es requerido para evitar fallos prematuros en la protección de metales.
Con estos conocimientos, los profesionales pueden optimizar los procesos de protección anticorrosiva y garantizar una mayor vida útil de los materiales metálicos en diversas aplicaciones industriales.
Referencias
- https://www.corrosionpedia.com/definition/519/flash-corrosion