Introducción
El fouling en las columnas de vacío es un problema en términos de calidad y flujo del producto debido a la acumulación de suciedad; lo cual; se traduce en altos costos y baja eficiencia en los procesos de refinación de crudos. Afectando negativamente tanto la capacidad de producción como la calidad del producto, donde el rendimiento en la etapa de separación y purificación del producto es fundamental.
Durante el proceso de refinación, una vez que el crudo ha sido desalinizado, es enviado como corriente de alimentación hacia una unidad de procesamiento donde se llevarán a cabo las primeras separaciones efectivas. La carga de alimentación atravesará el haz de tubo de precalentamiento, generalmente en el lado de la carcasa, donde absorberá calor de una corriente ya procesada dando lugar a la formación de un tipo de coque de refinería. Es en esta etapa donde es necesario llevar a cabo la descontaminación de la torre de vacío. Aunque las temperaturas no alcanzan niveles suficientemente altos para formar carbono, el depósito generado sigue siendo extremadamente resistente a la eliminación química.
Este artículo tiene como objetivo exponer los problemas asociados con el ensuciamiento de las torres de destilación al vacío, aportando las soluciones más adecuadas para controlar y mitigar el fouling en las columnas de vacío.
¿Qué es la destilación al vacío?
La destilación al vacío es un proceso de refinación del petróleo en la industria Oil & Gas, para separar y purificar componentes de alto punto de ebullición, como los residuos pesados, con el fin de obtener productos más ligeros. Se realiza bajo presiones inferiores a la atmosférica para disminuir los puntos de ebullición y evitar la descomposición térmica de los hidrocarburos1.
Proceso de destilación al vacío
En la figura 1, se aprecia un diagrama representativo del proceso de destilación al vacío.
- Residuos atmosféricos: Estos son alimentados a la torre de destilación al vacío después de pasar por unidades de pretratamiento para eliminar impurezas como agua y sedimentos.
- Torre de destilación al vacío: El crudo entra en la torre de destilación al vacío, donde se calienta mediante vapor y se somete a un vacío alto (presión reducida) para disminuir sus puntos de ebullición.
- Separación por fracciones: En la torre de destilación al vacío, los componentes de alto punto de ebullición, como los residuos pesados, se separan en diferentes fracciones. Las fracciones más pesadas se recogen en la parte inferior de la torre.
- Condensación: Las fracciones destiladas se condensan en unidades de condensadores y se recolectan para su posterior procesamiento y refinado.
- Productos: Los productos destilados al vacío y los intermedios como: aceite lubricante, aceite de vacío, y el residuo de vacío, se recolectan en función de su peso molecular y punto de ebullición en diferentes puntos de la torre.
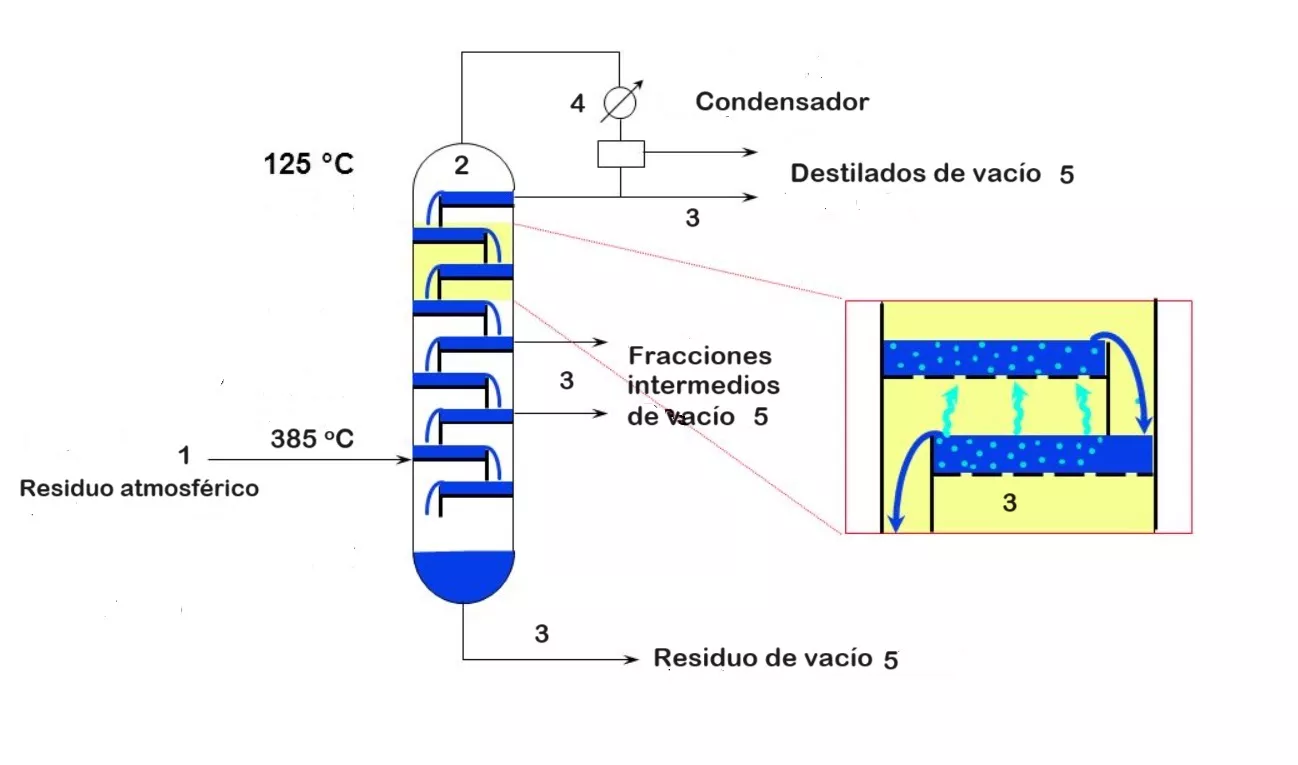
La separación de hidrocarburos pesados puede generar problemas como el fouling, que afecta la eficiencia y la calidad de las operaciones. Es importante entender este proceso para realizar un mantenimiento de limpieza efectivo, con el fin de conocer las causas del fouling en las columnas de vacío y buscar las estrategias para controlar el fouling en las torres de destilación al vacío, donde se separan los hidrocarburos de cadena larga, se pueden generar problemas como depósitos, que afecta la eficiencia y la calidad de las operaciones.
Causas del fouling en las columnas de vacío
El servicio de incrustaciones implica la necesidad de tener un conocimiento sobre el mecanismo de formación de incrustaciones y cómo afecta al proceso. La presencia de contaminación puede ocasionar un aumento en el consumo de energía, disminución de la transferencia de calor del proceso y una disminución en la capacidad de producción de la columna, la utilización de aditivos químicos y, en algunos casos, períodos prolongados de inactividad.
Entre las causas más importantes se mencionan las siguientes:
- Altas temperaturas a la salida del horno, pueden causar craqueo y una coquificación severa en la zona de lavado y el fondo de la columna.
- Disminución del reflujo en la zona de lavado.
- Un mal diseño de la zona de lavado.
- Altos tiempos de residencia favorecen a la formación de coque.
- Depósitos por corrosión.
En la figura 2, se muestran posibles puntos donde se observan varios tipos de corrosión en diferentes regiones de la torre de destilación al vacío por ataque del ácido nafténico 2.
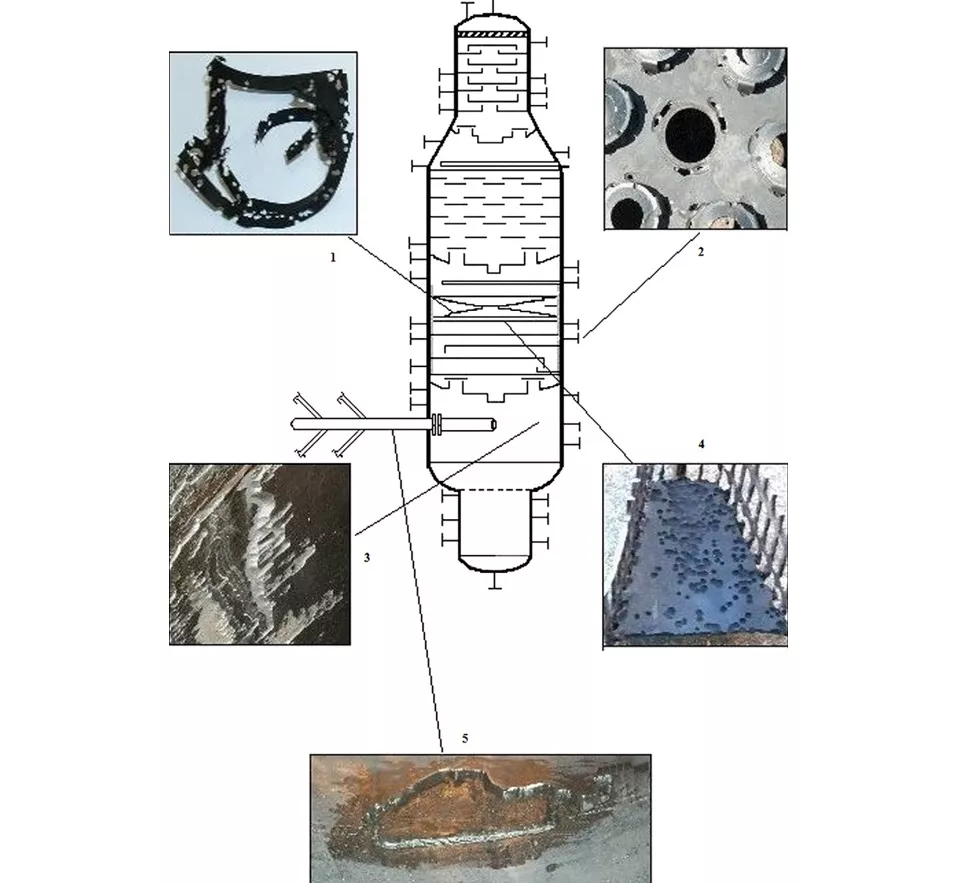
¿Qué problemas causa el ensuciamiento en la torre de vacío?
Los depositos en la torre destiladora de vacío es un problema en términos de calidad y flujo del producto debido a la presencia de contaminantes. Las incrustaciones se forman durante el procesamiento de crudo pesado. El flujo de entrada a la torre contiene no solo productos de refinación, sino también depósitos tanto orgánicos como inorgánicos, como ceras y asfaltos pesados, contribuyendo a la contaminación y al ensuciamiento de la torre de vacío.
La incrustaciones en la torres atmosféricas causan varios problemas. Por ejemplo, los intercambiadores de precalentamiento pueden ensuciarse con depósitos orgánicos pesados y coque. Como resultado, los intercambiadores tienen una capacidad de intercambio de calor reducida. De manera similar, el haz de tubos de los intercambiadores puede obstruirse con una mezcla de hierro, sílice y compuestos orgánicos. Entre los compuestos orgánicos se incluyen asfaltenos, ceras y algunos polímeros lineales y ramificados. Como resultado, los intercambiadores han reducido el flujo de crudo.
Además, las numerosas bandejas interiores y secciones empaquetadas de la torre atmosférica pueden contaminarse con depósitos orgánicos pesados, de esta forma se produce un mal contacto entre los vapores que ascienden por la torre y el líquido; lo cual, reduce la calidad de los productos generales. Los hervidores y los condensadores de reflujo presentan los mismos depósitos.
La torre puede tener además un alto contenido de H2S y hierro pirofórico y otras sustancias orgánicas inflamables, generando un importante problema de seguridad, ya que suponen un riesgo de incendio.
Estrategias para controlar el fouling en las columnas de vacío
Uno de los aspectos más difíciles del ensuciamiento es que los contaminantes y los procesos a menudo son exclusivos del proceso. Para resolver un problema de incrustación, generalmente es imperativo conocer los componentes de incrustación en el proceso, así como el mecanismo que causa el problema de incrustación. A continuación, se analizan varios métodos para combatir las incrustaciones.
Mantener el material incrustante fuera de la columna
La prevención suele ser más eficaz que el tratamiento posterior en muchos problemas, incluida la contaminación de columnas. Mantener los materiales contaminantes fuera del proceso y del equipo es la solución preferida, la filtración es comúnmente el método más utilizado, como en el caso de los contactores y regeneradores de aminas. Sin embargo, la filtración puede resultar costosa y llevar mucho tiempo monitorear, reemplazar o lavar los filtros.
En ocasiones, la cantidad de material a filtrar puede ser excesiva o los componentes contaminantes no se vuelven sólidos hasta formarse dentro de la columna. Aunque la filtración es un método efectivo para tratar los materiales contaminantes, a menudo puede ser poco práctico como solución, debido a la caída de presión del sistema de filtrado.
Control del proceso para evitar incrustaciones
Si el ensuciamiento se debe a la reacción o degradación de los productos de alimentación dentro de la columna, la prevención implica controlar las condiciones del proceso para evitar entrar en la región operativa problemática. Esto puede resultar ineficiente y costoso, ya que desviarse de las condiciones óptimas puede afectar negativamente la calidad del producto, el rendimiento y el consumo de energía. Por ejemplo, en una columna de vacío de una refinería, se utiliza la presión de vacío más baja posible en la sección de lavado para evitar el craqueo de hidrocarburos pesados.
La confiabilidad del equipo auxiliar también puede ser un problema. Una pérdida temporal de la bomba puede dejar una sección de la torre demasiado caliente o seca, lo que provoca la formación rápida de incrustaciones o coquización. Una vez que comienza la incrustación, tiende a crecer rápidamente y puede generar problemas graves e irreversibles en muy poco tiempo disminuyendo la operatividad de la planta.
Uso de antiincrustantes
En algunas aplicaciones seleccionadas, los antiincrustantes se pueden utilizar eficazmente. En procesos como la producción de olefinas, el uso de antiincrustantes es bastante común y, a menudo, eficaz. El objetivo principal de los antiincrustantes es inhibir la polimerización con el proceso que provocará la incrustación. Los inhibidores de la corrosión también podrían denominarse antiincrustantes, ya que los productos de la corrosión pueden formar incrustaciones y otros materiales que pueden ensuciar el interior de la columna.
Generalmente, el uso de antiincrustantes es bastante especializado y pueden ser un beneficio en algunos servicios, entre los que se pueden mencionar:
Partes internas resistentes a las incrustaciones
Si no es posible evitar la incrustación en la alimentación o mediante ajustes operativos, entonces es necesario abordar el material incrustante dentro de la columna. Una estrategia preferida consiste en diseñar partes internas que permitan que el material incrustante pase a través de la columna sin acumularse. En algunos casos, se utilizan dispositivos abiertos y menos eficientes, como bandejas deflectoras o empaquetaduras de rejilla, diseñadas para que el material incrustante no tenga oportunidad de acumularse.
Bandejas: Las bandejas con pestañas, se pueden usar para evitar que se acumulen sólidos en las bandejas. Estas son bandejas convencionales con bajantes de líquido, pero tienen pestañas direccionales de vapor en la plataforma de la bandeja. El flujo de vapor dirigido hacia adelante desde las pestañas puede ser bastante efectivo para empujar sólidos de una plataforma de bandeja a otra y luego, finalmente, hacia el fondo de la columna.
Empaquetaduras y distribuidores: Cuando se utilizan empaquetaduras en servicios de incrustaciones, generalmente se usan empaquetaduras de rejilla porque tienen aberturas grandes y áreas de superficie más bajas. Las grandes aberturas son difíciles de tapar y, por tanto, permiten que los sólidos pasen a través del lecho. La baja superficie garantiza que toda la superficie del embalaje esté completamente humedecida y evita que los sólidos se sequen en la superficie y provoquen incrustaciones.
Tratamiento superficial
También se pueden utilizar tratamientos superficiales como recubrimientos o electropulido. Las bandejas de doble flujo no tienen bajantes y generalmente son muy activas en la plataforma, por lo que los materiales contaminantes tienden a pasar a través de ellas. La superficie electropulida es muy lisa y limita la capacidad de los materiales contaminantes de adherirse a las plataformas.
Conclusiones
La gestión efectiva del fouling en las columnas de vacío es fundamental para mantener la eficiencia y la rentabilidad en las operaciones de refinado de petróleo. Se han desarrollado diversas estrategias para abordar este desafío, desde la prevención mediante el control de condiciones operativas hasta el diseño de partes internas que permitan el paso libre de materiales incrustantes. Sin embargo, cada estrategia tiene sus consideraciones y limitaciones, como el costo energético asociado con la creación de vacío o la eficiencia reducida de dispositivos abiertos.
Es importante implementar un enfoque integral que combine técnicas de prevención, monitoreo y mantenimiento para optimizar el rendimiento de las columnas y prolongar su vida útil. Además, el avance continuo en tecnologías de diseño y control ofrece oportunidades para mejorar la gestión del fouling y garantizar la operación eficiente de las instalaciones de refinado en el futuro.
Referencias
- Alan S. Foust, Leonard A. Wenzel, Curtis W. Clump, Louis Maus, L. Bryce Andersen; «Principios de Operaciones Unitarias»; 2Nd Ed 2008.
- Alvisi P. Pío, Lins VFC; «Una descripción general de la corrosión del ácido nafténico en una planta de destilación al vacío»; Análisis de fallas de ingeniería 18(5):1403-1406, junio 2011.