La corrosión es uno de los mayores problemas a nivel industrial, generando innumerables pérdidas económicas, debido al deterioro de los materiales metálicos afectando sus propiedades físicas.
En el caso de la industria naval, el problema crece exponencialmente, ya que los materiales están sometidos a altos niveles de corrosión por la exposición continua con el agua de mar, el electrolito corrosivo por naturaleza. El alto contenido salino que tiene hace que se comporte como una pila de corrosión. Existen varios tipos de corrosión, pero la más común es la galvánica o electroquímica. Se produce cuando dos elementos metálicos de diferente potencial eléctrico son conectados directamente entre sí con continuidad en presencia de un electrolito (PILA). De esta forma se genera un proceso electroquímico con creación de una corriente eléctrica que causa la corrosión de uno de los dos electrodos: aquel que está compuesto por el metal «menos noble» (es decir, aquel con electronegatividad mayor, ánodo) mientras que el otro, el cátodo, queda protegido.
Los factores que más afectan a la corrosión de las embarcaciones marinas se tienen la salinidad, la temperatura, contenido de oxígeno, cloruros, etc. La zona del buque más afectada por la corrosión será la zona de salpicaduras, ya que se encuentra cubierta intermitentemente por una fina capa de agua y está expuesta al oxígeno ambiental.
A medida que los buques y las estructuras de la plataforma envejecen, se deterioran por corrosión y fatiga. La corrosión externa de la plataforma se ha convertido en una preocupación importante para los propietarios y operadores.
Las placas de cubierta de embarcaciones marinas y las estructuras superiores de la costa están constantemente expuestas a un ambiente altamente corrosivo (medio salino), sin mencionar varias formas de acciones mecánicas. Estos mecanismos de erosión corrosión pueden debilitar o disminuir drásticamente la capacidad de resistencia de la plataforma.
Además, teniendo en cuenta las diversas formas de desgaste mecánico que actúan sobre ellos, no sorprende que las cubiertas deban ser reparadas o reemplazadas regularmente. Estos mecanismos de corrosión por erosión son importantes para consideraciones de resistencia estructural, ya que pueden debilitar drásticamente la capacidad de resistencia de la plataforma y crear paradas inesperadas en el funcionamiento del buque/ plataforma.
Para evitar este tipo de daño entre las soluciones más adecuadas se destacan:
Reemplazo total de la plataforma.
Algunas de las soluciones convencionales para reparar o restablecer la capacidad de carga de una placa de cubierta son el reemplazo de la plataforma existente o la soldadura de placas adicionales. El reemplazo de la plataforma permite quitar y reemplazar las secciones más corroídas de las placas de la plataforma y reemplazarlas con acero nuevo.
Esta solución garantiza una plataforma completamente nueva sin aumento de peso total en la estructura de la plataforma, pero es muy costosa y requiere mucho tiempo.
Además, la eliminación de las placas de cubierta comprometidas expondría la infraestructura y la maquinaria debajo de la cubierta, que podrían incluir equipos de la sala del generador de emergencia y la sala de máquinas. Tal equipo desprotegido, cuando se expone al medio ambiente altamente corrosivo, puede sufrir daños significativos, lo que resulta en tiempos de inactividad prolongados.
Reforzar las cubiertas dañadas.
Soldar placas adicionales para reforzar las placas de cubierta dañadas generalmente representa la solución más utilizada y reconocida debido a su bajo costo y respuesta rápida.
Como las nuevas placas se pueden instalar en parches, las reparaciones se pueden completar más rápido para que las operaciones de la plataforma se vean mínimamente afectadas. Sin embargo, la soldadura típicamente forma una unión alrededor del perímetro de la placa y el sustrato.
El área no unida puede volverse susceptible a la corrosión en grietas si la soldadura no es continua sino intermitente, permitiendo la penetración de humedad. Además, esta solución requiere un trabajo en caliente que no siempre es factible o permitido en entornos con productos químicos inflamables y explosivos, ya que las chispas y el metal caliente pueden viajar en cualquier dirección y provocar un posible incendio y/o explosión.
Cold Bonding o Soldadura en frio.
La técnica de soldadura en frio puede ser utilizar para reparar la placa de cubierta de los barcos. Esta consiste en la unión mecánica y polar de adhesivos químicos con diferentes materiales como metales, plásticos y cauchos. Con el tiempo estas soluciones han ido mejorando sus capacidades como adhesión, compresión y resistencia química a diferentes temperaturas.
Beneficios
El cold bonding se utiliza en conjunto con composite poliméricos, los cuales hoy en día son los productos más utilizados para esta técnica ya que puede ofrecer beneficios tales como:
- Elimina el riesgo de chispas o peligros eléctricos, evitará la necesidad de permisos de trabajo en caliente.
- Puede ser aplicada en sitio, y es una alternativa cuando el corte y la soldadura tradicional, están restringidos en atmósferas explosivas.
- El adhesivo utilizado se adapta a las formas irregulares de áreas irregulares, llenando los espacios huecos entre las superficies.
- Elimina la necesidad de mecanizado in situ, alivio de tensiones o tratamiento térmico posterior a la soldadura.
- Es una tecnica amigable y ecologica, no ocaciona contaminación al medio ambiente.
La placa metálica de refuerzo y los sustratos debilitados son los adherentes. La placa metálica unida refuerza el sustrato dañado y restablece su resistencia mecánica. Se aplica el agente de unión en la parte inferior de la placa metálica y el sustrato debilitado antes de que ambas superficies se unan.
Métodos de aplicación.
Sandwich de Compuesto: Se utiliza un producto adhesivo viscoso y se aplica contra el perfil de ambas superficies, previamente preparadas para aumentar su aspereza, permitiendo la unión de ambas superficies. luego se presiona firmemente para expulsar el material sobrante y eliminar el aire atrapado, figura 2.
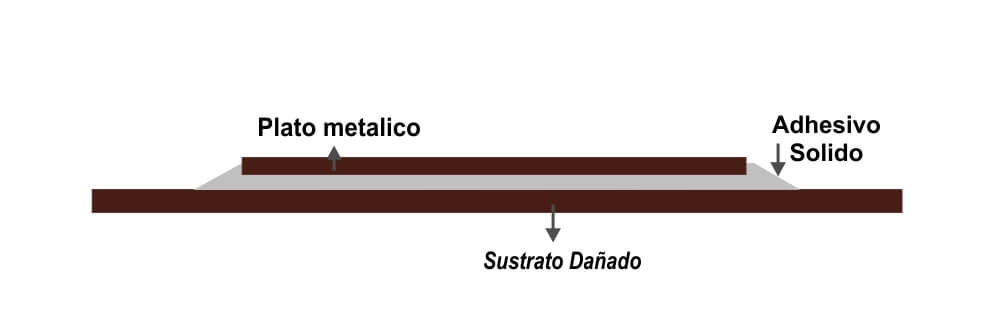
Inyección: Este metodo se aplica en superficies grandes. (Ej placas de refuerzo de 1m2 ), puede ser necesaria la inyección de material fluido a través de orificios preparados para esa finalidad, lo que asegurará un contacto pleno entre las dos superficies. En este caso, se usa una pasta para sellar los bordes y el material fluido se inyecta. Este fluye desde las esquinas hacia el interior hasta que empieza a salir por los orificios de ventilación, figura 3).
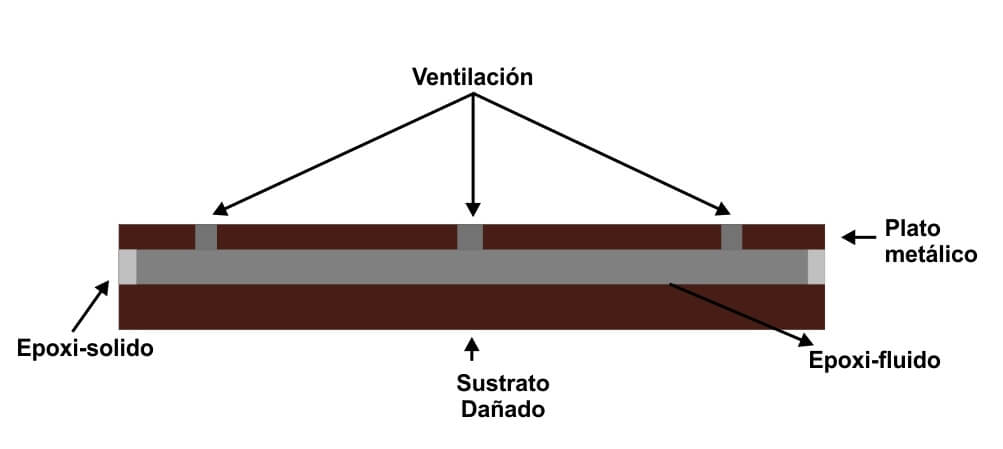
Conclusiones
La soldadura en frío es una alternativa a la soldadura térmica. Es muy versátil ya que permite reparar equipos o activos in situ, sin calor y de una manera fácil y segura. Ofreciendo el mejor compromiso entre costo y rendimiento en comparación con el reemplazo de la plataforma y la soldadura de placas adicionales a la plataforma. Es importante conocer los productos para cada soldadura en frío, para asegurar una utilización ajustada al tipo de reparación, con el objetivo de conseguir la mayor resistencia y el mejor acabado.
Referencias bibliográficas
- Nguyen, N. (2012). Micromixers: fundamentos, diseño y fabricación. Oxford: Elsevier / William Andrew.
- Callister, W. D. (2007). Ciencia e ingeniería de materiales: una introducción. Nueva York: John Wiley & Sons.
- Campbell, F. C. (2007). Procesos de fabricación de compuestos avanzados. Oxford: Elsevie
Para más artículos visita https://inspenet.com/articulos/.