Tabla de Contenidos
- Definición de una buena soldadura vs. mala soldadura
- Características de una buena soldadura
- Características de una mala soldadura
- Técnicas de inspección de soldaduras
- Proceso de soldadura y parámetros clave
- Recomendaciones prácticas para Identificar y prevenir defectos de soldadura
- Conclusiones
- Referencias
La soldadura es una técnica fundamental en diferentes industrias, desde la construcción y la manufactura hasta la automotriz y la aeroespacial. Es el proceso que une materiales, generalmente metales o termoplásticos, mediante la coalescencia. La calidad de una soldadura es crítica para asegurar la integridad estructural de las piezas y la seguridad de las personas que las utilizan.
Una soldadura bien ejecutada proporciona una unión fuerte y duradera, mientras que una soldadura defectuosa puede llevar a fallos estructurales y costosas reparaciones. Entender las características que diferencian una buena soldadura vs. mala soldadura es fundamental para cualquier profesional en el campo.
En este artículo, exploraremos los aspectos clave que definen una buena soldadura vs. mala soldadura, los defectos comunes a evitar y las técnicas de inspección que garantizan la calidad de las uniones soldadas, asegurando así la fiabilidad y seguridad de las estructuras soldadas.
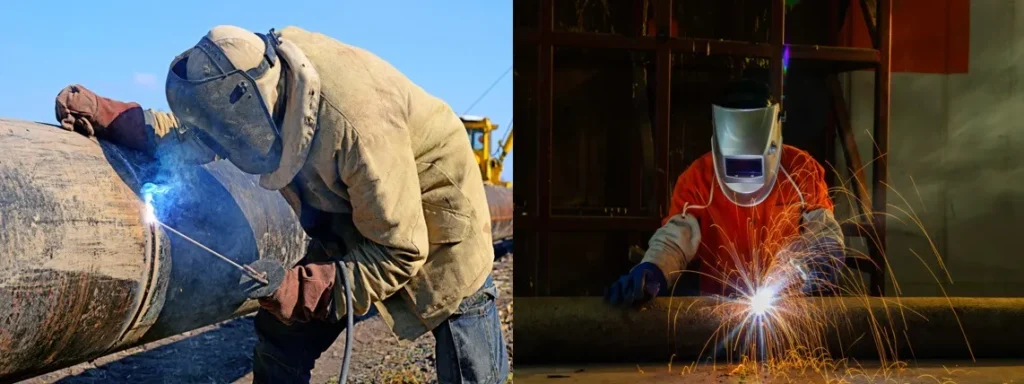
Definición de una buena soldadura vs. mala soldadura
Una buena soldadura vs. mala soldadura se caracteriza por diferentes criterios. Una buena soldadura es conocida por su integridad estructural y apariencia uniforme. Los criterios generales para evaluar la calidad de una soldadura incluyen una penetración adecuada del metal de soldadura, la correcta fusión de los materiales base y la ausencia de defectos como porosidad, grietas o inclusiones de escoria. Visualmente, una buena soldadura debe tener un cordón uniforme, con un perfil liso y consistente, libre de socavados o exceso de material. Estos atributos aseguran que la soldadura pueda soportar las cargas y tensiones a las que estará sometida durante su vida útil.
En contraste, una mala soldadura presenta fallos en uno o más de estos aspectos. Los defectos comunes en una mala soldadura incluyen falta de fusión, penetración insuficiente, porosidad excesiva, grietas y deformaciones. Estos defectos comprometen la resistencia estructural y pueden llevar a fallos prematuros, resultando en riesgos de seguridad y mayores costos operativos.
La identificación temprana y la corrección de estos defectos son esenciales para mantener la calidad y fiabilidad de las estructuras soldadas. Entender las diferencias en una buena soldadura vs. mala soldadura ayuda a los profesionales a asegurar los más altos estándares en sus proyectos de soldadura.
Características de una buena soldadura
Entender las características de una buena soldadura vs. mala soldadura es crucial. Una buena soldadura se destaca por su apariencia visual y su integridad estructural. Visualmente, debe tener un cordón uniforme, libre de socavados, exceso de material o salpicaduras. El perfil debe ser liso y consistente, con una penetración adecuada del metal de soldadura, asegurando una fusión completa de los materiales base. La uniformidad y la ausencia de discontinuidades visibles son indicadores clave de una buena soldadura.
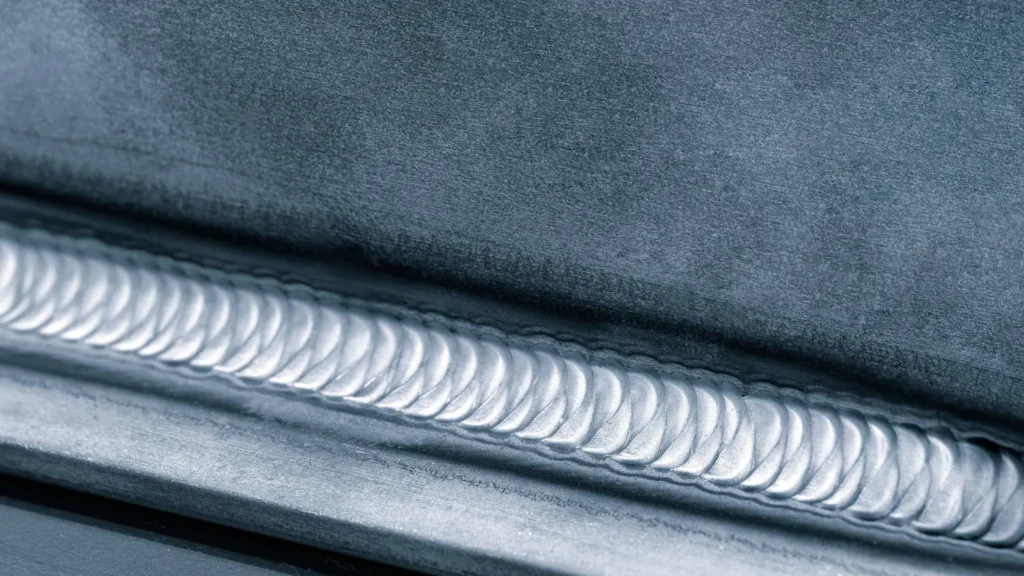
Los parámetros de soldadura que influyen en la calidad incluyen la temperatura, la velocidad de soldadura y los materiales utilizados. La temperatura debe ser lo suficientemente alta para fundir los materiales base y el metal de soldadura, pero no tanto como para causar deformaciones o defectos. La velocidad de soldadura debe ser constante para evitar variaciones en la penetración y la formación de defectos. Los materiales deben ser de alta calidad y compatibles entre sí para asegurar una unión fuerte. Utilizar materiales de baja calidad puede introducir impurezas y defectos en la soldadura, comprometiendo su integridad.
Las herramientas y equipos de soldadura también juegan un papel crucial en la calidad de la soldadura. Utilizar equipos modernos y bien mantenidos, como soldadores MIG (Metal Inert Gas) o TIG (Tungsten Inert Gas), puede ayudar a asegurar una soldadura de alta calidad. La soldadura MIG utiliza un electrodo de alambre consumible y un gas protector que evita la contaminación del metal fundido. Es ideal para soldar materiales más delgados y se usa comúnmente en la fabricación y reparación de automóviles.
La soldadura TIG utiliza un electrodo de tungsteno no consumible y un gas inerte, como argón o helio, para proteger el área de soldadura. Es preferida por su precisión y la calidad de la soldadura que produce, siendo ideal para trabajos detallados y materiales más delgados.
El uso de gases protectores es fundamental en estos procesos. En la soldadura MIG, el gas protector (generalmente argón, CO2 o una mezcla de ambos) forma una barrera que evita la oxidación y la contaminación del metal fundido. En la soldadura TIG, el gas inerte (principalmente argón) no solo protege el metal fundido sino también el electrodo de tungsteno, asegurando una soldadura limpia y fuerte.
Un ejemplo de una buena soldadura vs. mala soldadura se puede observar en la fabricación de estructuras metálicas para la industria aeroespacial, donde la integridad y la precisión son cruciales. Los estudios de caso han demostrado que las soldaduras bien ejecutadas en estas aplicaciones pueden soportar tensiones extremas y condiciones adversas sin fallar. La calidad de los materiales utilizados, la precisión en los parámetros de soldadura y el uso adecuado de equipos y gases protectores son esenciales para lograr estos resultados.
Características de una mala soldadura
Una mala soldadura se caracteriza por la presencia de defectos que comprometen la integridad y la seguridad de la estructura. Entender las características de una buena soldadura vs. mala soldadura ayuda a identificar estos problemas. Los defectos comunes incluyen porosidad, grietas, inclusiones de escoria, falta de fusión y penetración insuficiente. Cada uno de estos defectos puede tener consecuencias significativas para la calidad y durabilidad de la soldadura.
- Porosidad: La porosidad se manifiesta como pequeños agujeros en el cordón de soldadura, causados por gases atrapados durante el proceso de solidificación. Este defecto puede debilitar la soldadura, reduciendo su resistencia y capacidad para soportar cargas. Además, la porosidad puede facilitar la corrosión al permitir la entrada de humedad y contaminantes.
- Grietas: Las grietas son rupturas en la soldadura que pueden ocurrir durante o después del enfriamiento. Pueden ser superficiales o internas y son causadas por tensiones residuales, enfriamiento rápido o una técnica de soldadura incorrecta. Las grietas son especialmente peligrosas porque pueden propagarse bajo cargas dinámicas, resultando en fallos inesperados y catastróficos.
- Inclusiones de escoria: Las inclusiones de escoria son materiales no metálicos atrapados en la soldadura, generalmente provenientes de residuos del proceso de soldadura o impurezas en los materiales base. Estas inclusiones debilitan la unión y pueden actuar como puntos de concentración de tensiones, aumentando la probabilidad de fallo bajo carga.
- Falta de fusión: Este defecto ocurre cuando el metal de soldadura no se fusiona adecuadamente con el material base. Puede ser causado por una insuficiente entrada de calor, una velocidad de soldadura demasiado rápida o una técnica incorrecta. La falta de fusión resulta en una unión débil que no puede soportar cargas adecuadas, comprometiendo la integridad estructural.
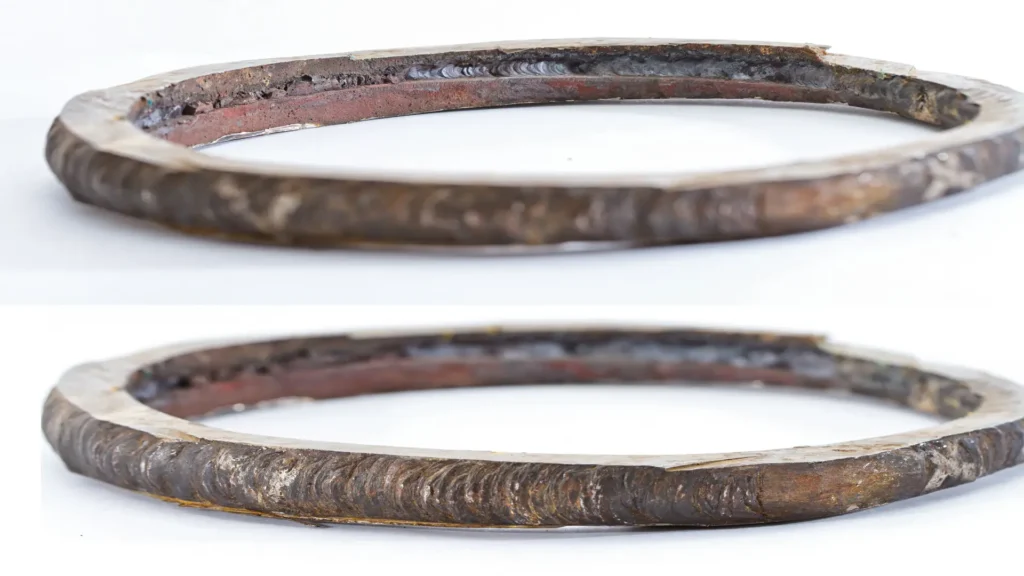
- Penetración insuficiente: La penetración insuficiente se refiere a la falta de profundidad del metal de soldadura en el material base. Similar a la falta de fusión, puede ser causada por una incorrecta configuración de los parámetros de soldadura. La penetración insuficiente reduce la resistencia de la soldadura y aumenta el riesgo de fallos estructurales.
Las consecuencias de estos defectos pueden ser severas. Por ejemplo, en la construcción de puentes o edificios, una mala soldadura con grietas o falta de fusión puede llevar al colapso bajo condiciones de carga normales, poniendo en peligro vidas y causando pérdidas económicas significativas.
Un estudio de caso notable es el colapso de una plataforma offshore debido a defectos en las soldaduras. La investigación reveló que las soldaduras presentaban grietas y falta de fusión, lo que comprometió la integridad de la estructura bajo condiciones de operación normales. Este incidente subraya la importancia de técnicas adecuadas de soldadura y control de calidad para evitar fallos catastróficos.
Al comprender y evitar los defectos comunes asociados con las malas soldaduras, los profesionales pueden mejorar significativamente la seguridad y durabilidad de las estructuras soldadas.
Ver video donde se enseñan los diferentes defectos en soldaduras. Fuente: Material Welding.

Diferentes defectos en soldaduras.
Técnicas de inspección de soldaduras
La inspección de soldaduras es crucial para garantizar su calidad y seguridad. Las técnicas de inspección no destructiva (END) permiten evaluar la integridad de las soldaduras sin dañar el material. Entre las técnicas más comunes se encuentran la inspección visual, el ultrasonido, los rayos X, las partículas magnéticas y los líquidos penetrantes.
Inspección visual
Un componente esencial de la inspección es la inspección visual, que se realiza en varias etapas del proceso de soldadura: durante la preparación, durante la soldadura y al finalizar la soldadura.
- Inspección visual durante la preparación: Antes de comenzar a soldar, se inspeccionan los materiales y las superficies a soldar para asegurarse de que estén limpias, libres de óxido, grasa y otras contaminaciones. Se verifica el ajuste y alineación de las piezas y se revisan las herramientas y equipos para asegurarse de que estén en condiciones óptimas.
- Inspección visual durante la soldadura: Mientras se realiza la soldadura, el inspector observa el proceso para detectar problemas como la incorrecta aplicación del cordón, variaciones en la velocidad de soldadura y la presencia de salpicaduras. Se utiliza iluminación adecuada y lupas para mejorar la visibilidad de la soldadura en curso.
- Inspección visual al finalizar la soldadura: Una vez completada la soldadura, se examina el cordón para verificar la uniformidad, la penetración y la ausencia de defectos visibles como grietas, porosidad y socavados. Herramientas como lupas, luces portátiles, medidores de perfil y reglas se emplean para esta inspección detallada.
Ultrasonido
Esta técnica utiliza ondas sonoras de alta frecuencia para detectar discontinuidades internas en la soldadura. Las ondas se transmiten a través del material y se reflejan en los defectos, lo que permite su identificación. Las ventajas del ultrasonido permiten detectar defectos internos y su portabilidad. Sin embargo, requiere operadores altamente capacitados y puede ser difícil de interpretar en materiales complejos.
Las técnicas para el examen ultrasónico de soldaduras descritas en la Práctica Estándar para el examen ultrasónico por contacto de soldaduras (ASTM- E 164– 03), están destinadas a proporcionar un medio de examen de soldaduras para discontinuidades tanto internas como superficiales dentro de la soldadura y la zona afectada por el calor. La práctica se limita al examen de geometrías de soldadura específicas en material forjado o forjado.
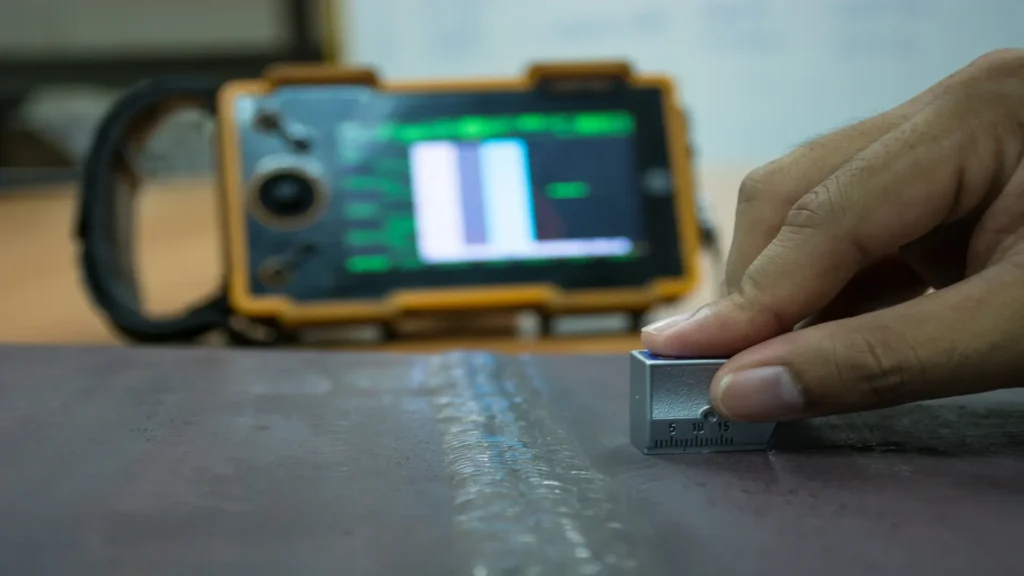
Radiografía industrial
Los rayos X son utilizados para obtener una imagen de la soldadura y revelar defectos internos como porosidad, inclusiones y grietas. La principal ventaja es su alta resolución y capacidad para inspeccionar soldaduras en áreas difíciles de alcanzar. No obstante, es una técnica costosa y requiere medidas de seguridad estrictas debido a la radiación.
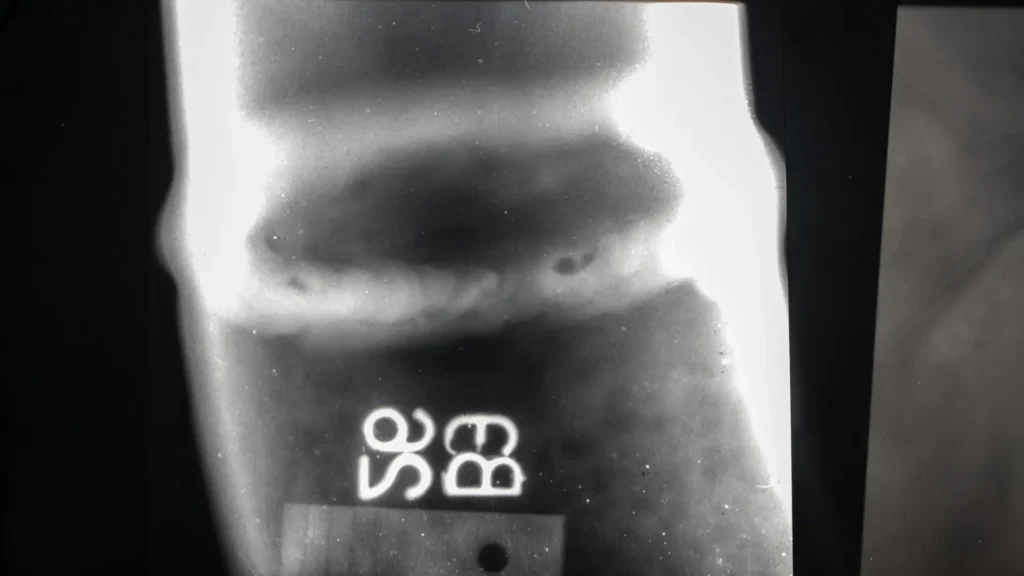
Partículas magnéticas
Esta técnica se usa para detectar defectos superficiales y subsuperficiales en materiales ferromagnéticos. Un campo magnético se aplica a la soldadura y las partículas magnéticas se adhieren a las áreas con discontinuidades. Es una técnica rápida y relativamente económica, pero no es aplicable a materiales no ferromagnéticos.
Líquidos penetrantes
Utilizada para detectar defectos superficiales, esta técnica implica la aplicación de un líquido penetrante sobre la soldadura. Después de un tiempo de espera, el exceso de líquido se elimina y se aplica un revelador para visualizar las discontinuidades. Es una técnica simple y económica, pero solo detecta defectos abiertos en la superficie.
Cada técnica tiene sus propias ventajas y desventajas, y la elección de la técnica adecuada depende de la naturaleza de la soldadura, el tipo de material y los requisitos específicos del proyecto.
Proceso de soldadura y parámetros clave
El proceso de soldadura implica la unión de materiales mediante la aplicación de calor y, a veces, presión, para fundir y fusionar los materiales base. Los parámetros críticos que deben controlarse durante el proceso de soldadura incluyen la temperatura, la velocidad de soldadura, el tipo de corriente y el flujo de gas protector.
- Temperatura: La temperatura debe ser suficientemente alta para fundir los materiales sin causar sobrecalentamiento o deformaciones.
- Velocidad de soldadura: Una velocidad constante asegura una penetración uniforme y la formación de un cordón de soldadura adecuado.
- Tipo de corriente: La corriente continua (CC) y la corriente alterna (CA) se utilizan dependiendo del tipo de soldadura y los materiales. La elección del tipo correcto de corriente influye en la estabilidad del arco y la calidad de la soldadura.
- Gas protector: En procesos como la soldadura MIG y TIG, el uso de gases protectores (como argón, helio o CO2) es esencial para evitar la oxidación y contaminación del metal fundido.
La formación y certificación de los soldadores son fundamentales para asegurar que se sigan las mejores prácticas y se mantengan los estándares de calidad. Los soldadores certificados tienen el conocimiento y la habilidad para ajustar los parámetros según las especificaciones del proyecto y resolver problemas que puedan surgir durante el proceso.
El impacto de los equipos y herramientas de soldadura en la calidad final no debe subestimarse. Equipos bien mantenidos y de alta calidad aseguran una operación eficiente y la producción de soldaduras consistentes y de alta calidad.
Recomendaciones prácticas para Identificar y prevenir defectos de soldadura
¿Cómo identificar una buena y una mala soldadura?
Para identificar una buena soldadura vs. mala soldadura, observe el cordón de soldadura: debe ser uniforme, liso y libre de socavados, salpicaduras o exceso de material. La penetración debe ser adecuada y visible, sin discontinuidades. Por el contrario, una mala soldadura mostrará porosidad, grietas, inclusiones de escoria, falta de fusión y penetración insuficiente.
Consejos prácticos para profesionales de la soldadura
- Inspección visual: Realice una inspección visual en todas las etapas del proceso de soldadura. Utilice herramientas como lupas y medidores de perfil para detectar defectos superficiales.
- Parámetros correctos: Asegúrese de que los parámetros de soldadura, como la temperatura, la velocidad y el flujo de gas protector, estén bien ajustados.
- Equipo de calidad: Utilice equipos y consumibles de alta calidad y manténgalos en buen estado.
- Formación continua: Capacite a los soldadores en técnicas de soldadura y actualice sus certificaciones regularmente.
Preguntas adicionales sobre prevención de defectos
1. ¿Cómo prevenir la porosidad?
Asegúrese de que las superficies a soldar estén limpias y secas, y utilice un gas protector adecuado.
2. ¿Cómo evitar las grietas?
Controle la velocidad de enfriamiento y utilice la técnica de soldadura adecuada.
3. ¿Qué mantenimiento requiere el equipo de soldadura?
Realice revisiones periódicas y calibra el equipo para garantizar su correcto funcionamiento.
Estas recomendaciones prácticos ayudarán a los profesionales a identificar y prevenir defectos de soldadura, mejorando la calidad y la seguridad de sus proyectos.
Conclusiones
La calidad de las soldaduras es fundamental para garantizar la integridad estructural y la seguridad. Una buena soldadura se caracteriza por su uniformidad y ausencia de defectos, mientras que una mala soldadura presenta fallos como porosidad, grietas e inclusiones de escoria, que pueden comprometer seriamente la seguridad y funcionalidad de las estructuras.
Los parámetros de soldadura, la formación de los soldadores y el uso de equipos adecuados juegan un papel fundamental en la calidad final de la soldadura. La comprensión y prevención de defectos en las soldaduras, practicas y tecnicas de inspeccion, se grantiza la seguridad de las personas; asi como, la eficiencia operativa y económica en diversos sectores industriales.
Referencias
Fuente propia