Tabla de Contenidos
- Análisis de la situación
- Criterios para la definición de planes de inspección
- Efecto de las condiciones de operación sobre la integridad y fiabilidad disponibilidad y uso de mediciones de temperaturas
- Planes de inspección en función de posibles mecanismos de daño
- Opciones adicionales de medición para el aumento de la fiabilidad
- Discusión y conclusiones
- Referencias
En este artículo se plantea una propuesta a considerar, para pasar de una rutina de inspecciones regulatorias periódicas y un control operacional tradicional enfocada en el aseguramiento de la producción de vapor requerida, basada en la metodología de Evaluación de Condición (Condition Assessment), mediante el análisis de los mecanismos de daño posibles y creíbles en cada componente de la caldera, que permite definir Planes de Inspección y Mantenimiento a corto y mediano plazo, e incluir en las rutinas operacionales mediciones de temperaturas y condición de combustión, que en tiempo real generen acciones correctivas acertadas e inmediatas, además de información que alimente el plan de inspección, para de manera integral se optimicen la eficiencia, disponibilidad y la Gestión de Mantenimiento, asegurando la Condición, Fiabilidad, Salud Operativo y la Seguridad de las Calderas.
Análisis de la situación
Los mantenimientos de las calderas, a nivel de muchas industrias y centrales termoeléctricas a vapor, donde las calderas son equipos esenciales para la producción y/o la generación, suelen ser del tipo Reactivo (correctivo) o una variante de este, incluso en instalaciones donde se aplica Mantenimiento Proactivo o Mantenimiento Centrado en Fiabilidad a los Equipos Rotativos (Turbina, Ventiladores y Bombas).
La planificación de los mantenimientos de las Calderas suele basarse en la relación de las Fallas más Recientes y Frecuentes, a pesar de que en función de sus tiempos de funcionamiento, condiciones y regímenes operacionales se van generando y evolucionando una cierta variedad de mecanismos de daños no siempre evidentes ante una inspección visual.
Criterios para la definición de planes de inspección
Cuando se habla de fiabilidad de calderas, el propietario o usuario de estos equipos algunas veces se limita a lo que requieren los Reglamentos de Seguridad de la Jurisdicción en que la caldera está instalada. Los requerimientos reglamentarios como Inspecciones Periódicas de Control se centran en inspección visual, prueba hidrostática, verificación de la actuación de las válvulas de alivio de presión (seguridad) y en algunos países la evaluación de las alarmas y disparos del sistema de control y seguridad.
En ciertos reglamentos se dan indicaciones de hacer una evaluación de condición, haciendo uso de ensayos no destructivos o ensayos suplementarios, luego de un tiempo determinado. En España el Real Decreto 2060/2008 de 12 de diciembre y sus Instrucciones Técnicas Complementarias (en revisión y para el momento de redactar este artículo está en periodo de alegaciones), se dan indicaciones tales como:
Cuando la inspección visual y los antecedentes de funcionamiento de las calderas, muestran irregularidades y resulten indicios para sospechar que en alguna parte, elemento o componente de la caldera puedan existir defectos importantes, deben realizarse los ensayos suplementarios que el responsable de la inspección por parte de la Agencia de Inspección u Organismo de Control Autorizado deberá acordar con el usuario o con el técnico designado por este (1).
Normalmente, cuando se plantea llevar a cabo un “plan de inspección” o realizarse ensayos suplementarios de una caldera, se observa que se desarrolla un mapeo de espesores, con lo que se está asumiendo como único criterio de evaluación el desgaste por erosión y/o corrosión de todos los componentes de la caldera, sin considerar posibles mecanismos de daños mecánicos y/o de envejecimiento, que normalmente no manifiestan pérdidas de espesores; o se llevan a cabo inspecciones cuyos enfoques o alcances se limitan a las áreas de las calderas que han manifestado fallas recientes y repetitivas.
Efecto de las condiciones de operación sobre la integridad y fiabilidad disponibilidad y uso de mediciones de temperaturas
Las calderas por su condición de ciclados operacionales, por requerimientos de la red eléctrica para las centrales de generación o por los turnos de trabajo o planes de producción en la industria en general; por el uso de combustibles fuera de especificación, buscando reducir costos de producción o usando los que se encuentran en el mercado, que producen irregularidades de las condiciones de combustión, balances térmicos y comportamiento general de la caldera; además de observar aceleración de los daños por corrosión y erosión, las calderas entran en condiciones que favorecen el desarrollo preferencial de mecanismos de daño tales como fatigas mecánica y/o térmica, envejecimiento o degradación térmica de diferentes tipos, entre otros, y ninguno de ellos son detectables tomando mediciones de espesores. Estas condiciones no siempre son prevenidas y pasa a ser un problema de pérdida de fiabilidad, disponibilidad e incluso de seguridad.
En la operación normal y/o rutinaria de calderas, los operadores básicamente llevan el seguimiento de los parámetros de producción: flujo de combustible, agua y vapor, sus temperaturas y presiones y adicionalmente se lleva la supervisión del nivel de agua dentro de la caldera y en calderas de mayor capacidad que operan a mayor presión, se lleva la verificación de porcentajes de apertura o consumo de agua de atemperación y temperaturas en la parte baja y alta del domo superior, porque así lo establece el manual del fabricante o procedimientos de operación.
Estos parámetros se consideran suficientes para supervisar la caldera, pero además de estos, en muchos casos las calderas cuentan con mediciones de temperaturas tanto de fluidos (gases, agua y/o vapor) en varios de sus pasos, como de piel de tubos y/o componentes esenciales, que aportan información sobre condiciones de operación irregulares e ineficiencia de la caldera que podría y deberían ser corregidas de manera inmediata, pero que en muchas instalaciones estas temperaturas no se monitorean.
Resulta muy conveniente el monitoreo, control, registro y análisis de estas temperaturas, pocas veces aprovechadas, que permiten visualizar en el tiempo, evaluando las tendencias, si en uno de los componentes de la caldera puede estar generándose de manera prematura, algún mecanismo de daño específico.
Si las mismas fueran utilizadas en tiempo real y se analizara no solamente al momento de hacer estudios de vida remanente, cuando la caldera ya tiene 20 o 30 años de funcionamiento, durante la operación rutinaria se podrían corregir tendencias y condiciones operacionales irregulares, mantener una eficiencia óptima, asegurar la fiabilidad, prevenir degradación y/o fallas inesperadas con paradas no programadas, cumplir con la expectativa de vida de los varios componentes de las calderas e incluso optimizar la seguridad de la misma.
Planes de inspección en función de posibles mecanismos de daño
Adicionalmente, al momento de querer definir un plan de inspección, basado en metodologías equivalentes a “Evaluación de Condición” (Condition Assessment) de la EPRI, para la determinación del estado real de integridad y fiabilidad de la caldera, en busca de la presencia y grado de evolución de los varios mecanismos de daño probables en los diferentes componentes críticos, conociendo la relación que existe entre las temperaturas antes citadas, en las diferentes condiciones operacionales (arranques, paradas, durante variaciones de cargas, etc.) y dichos mecanismos, resulta muy conveniente y práctico ampliar los parámetros operacionales a monitorear y regular, entre ellos valores de temperaturas de los que en muchas oportunidades se tiene la medición, pero que no se utilizan como parámetros de seguimiento rutinario.
Algunos de los mecanismos de daño que se deben considerar en los diferentes componentes de la caldera y que influyen en las fallas imprevistas y vida de servicio remanente, podrían ser:
- Termo fluencia (Creep), Ablandamiento (Esferoidización), Envejecimiento por deformación,
- Decarburización, Carburización,
- Sobrecalentamiento rápido,
- Transformación por enfriamiento rápido (Temple),
- Fatiga mecánica,
- Fatiga térmica,
- Erosión,
- Corrosión (local o general)
- Lado agua – vapor,
- Lado gases de combustión (parte caliente y parte fría),
- Bajo aislamiento térmico,
- Corrosión bajo depósitos
- Daño por hidrógeno,
- Corrosión fatiga,
- Corrosión bajo tensión,
- Sensitización en caso de inoxidables,
- Fragilización caustica,
- Corrosión – Erosión
Se debe resaltar en la definición del Plan de Inspección con ensayos suplementarios (que componentes inspeccionar, que mecanismos buscar y que ensayos no destructivos utilizar), que son muy pocos los mecanismos de daños que pueden ser determinados haciendo solamente uso de inspección visual y la medición de espesores.
Más de una técnica de inspección puede ser utilizada para detectar y caracterizar un mecanismo de daño específico. Asimismo, una misma técnica de inspección puede ser capaz de detectar y caracterizar varios tipos de mecanismos de daño, pero ninguna técnica sola es capaz de detectar y caracterizar todos los mecanismos de daño.
Para llevar adelante la realización de tal plan de ensayos suplementarios haciendo una evaluación previa de los antecedentes de funcionamiento de las calderas, es necesario en una Primera Fase hacer un levantamiento y evaluación de información relacionada con el diseño original de fabricación de la caldera; años de servicio; variaciones en el diseño; condiciones y hábitos de operación que alejan a la caldera de los procedimientos recomendados por el fabricante y las mejores prácticas; los registros de parámetros y régimen operacional o ciclado (“Ver Figura 1”); periodos fuera de servicio y controles en los métodos de preservación, históricos de control químico (“Ver Figura 2”); inspecciones, exámenes y pruebas previas; validación de los mecanismos de daños y análisis de las causas de fallas ya observados en años anteriores, en los varios componentes de la caldera (“Ver Figura 3”); reparaciones (definitivas y temporales) y alteraciones.
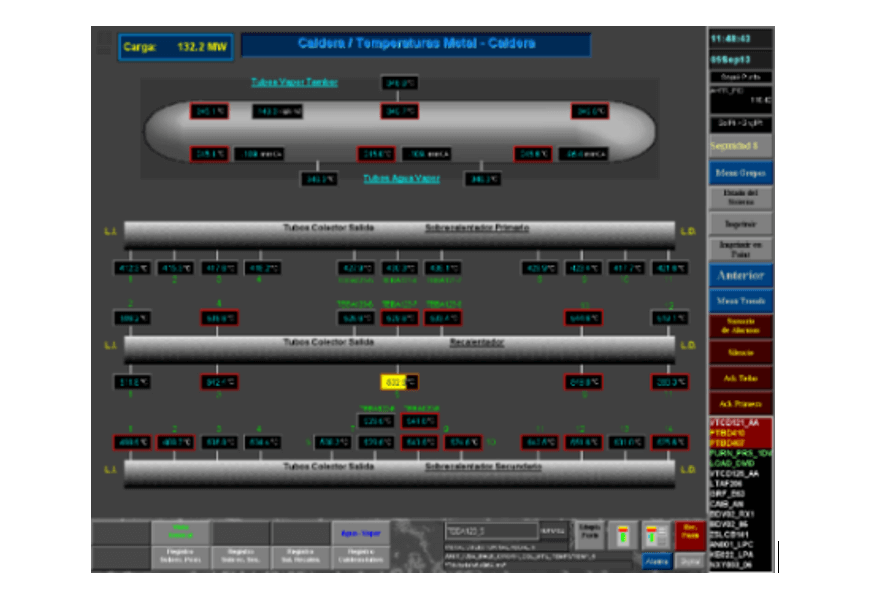
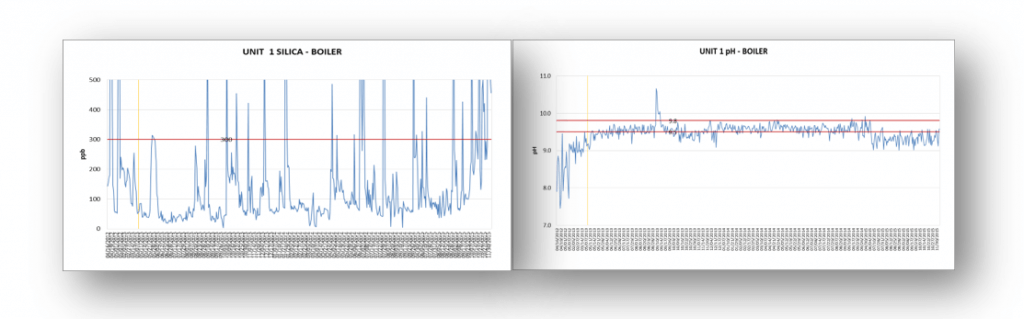
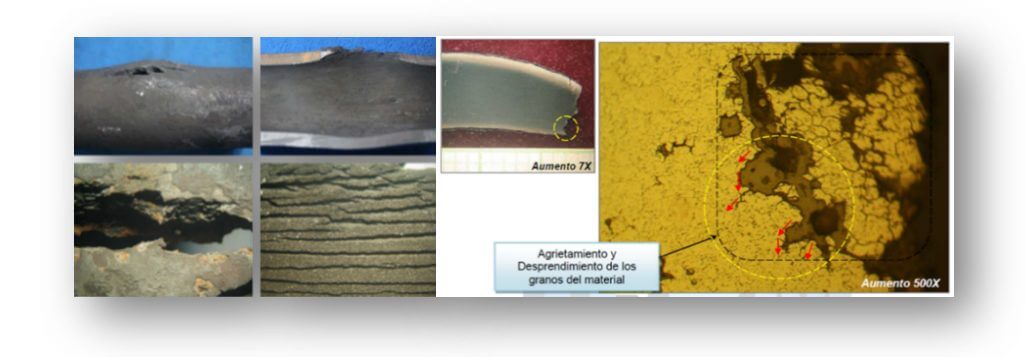
Figura 3. Caso particular de mecanismos de daño reportados en componentes de calderas.
Se considera importante, desde el punto de vista operacional, para la evaluación de tendencias de la eficiencia o desempeño de las calderas, el monitorear de temperaturas de los fluidos (gases de combustión, agua o vapor) a las diferentes cargas o condiciones de la caldera, siguiendo lo indicado por el manual de operación y mantenimiento del fabricante, pero debe considerarse muy importante que el operador tenga noción de la correlación de estas mediciones y las temperaturas de los metales en los varios componentes y en otros casos directamente las mediciones de las temperaturas de los metales de tubos, que pueden dar información muy fiable sobre la evolución de mecanismos de daños específicos en componentes particulares, ejemplos:
Economizador:
- Diferencial mayor a 93°C de temperaturas entre el agua de alimentación a la entrada y los gases de combustión a la salida del economizador, puede incentivar la generación fatiga térmica, sobre todo si el colector de entrada está ubicado dentro del paso de los gases;
- Temperaturas bajas del agua de alimentación, a la entrada del economizador, que llegan a condensar ácidos transportados por los gases de combustión;
En la Figura 1 antes mostrada, se pueden observar valores de temperaturas de metal con indicación de alarmas (en rojo), por encima del valor clasificado como límite en el sistema de control:
Domo superior:
El diferencial de temperaturas entre su parte superior e inferior durante los procesos de arranques (calentamiento) y paradas (enfriamiento), pudieran llevar a tensiones deferenciales y generación de agrietamientos por fatiga o alineación de picaduras por oxígeno o CO2 en las líneas de esfuerzos.
Paredes del hogar de la caldera
- Exposición de los metales de tubos del hogar, normalmente aceros de bajo contenido de carbón, a temperaturas por encima de las consideradas como máximas – según código de fabricación ASME 1.000°F (538°C), puede acelerar el envejecimiento de los tubos por termofluencia lenta o creep, pero también:
- secamientos localizados (steam blanketing) e incrustación de los sólidos disueltos y suspendidos, aumentos de concentración y ataques por corrosión cáustica.
- cuando la caldera opera a presiones por encima de los 1000 psi, puede ser susceptible a daños por hidrógeno bajo una serie de condiciones.
Es importante resaltar que por lo crítico que esto es, en algunas calderas de termoeléctricas el fabricante, instala desde un inicio termopares para monitorear las temperaturas de piel de tubos en el hogar, pero incluso en estas instalaciones estas mediciones no son utilizadas de forma cotidiana.
Cabe resaltar que este tipo de cuidados de medición de temperaturas pueden ser implementados en varios puntos del hogar de calderas industriales tipo paquete (“Ver Figura 4”).
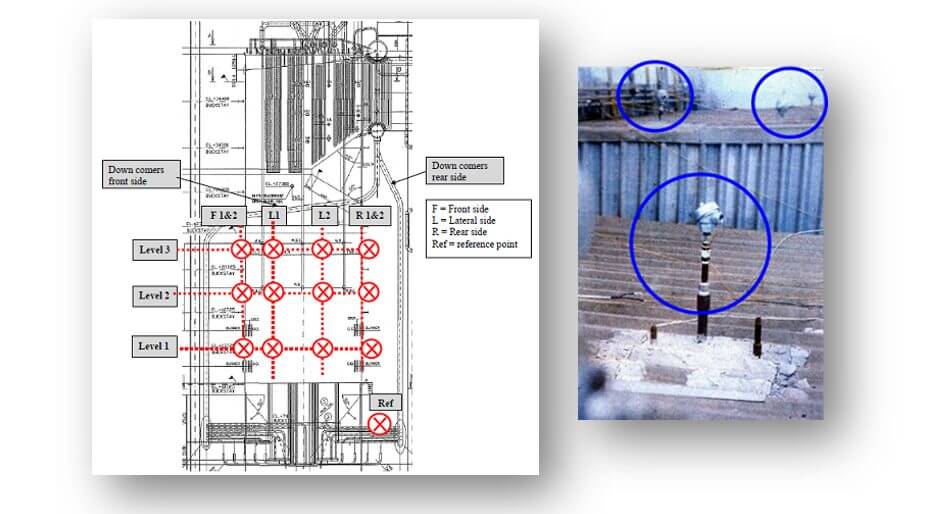
Figura 4. Izquierda: Disposición de termopares en áreas críticas del horno de la caldera,
Derecha: Vista exterior de la caldera acuatubular industrial con termopares.
Si los termopares a ser instalados en las paredes del horno son del tipo Chordal, será posible monitorear la evolución de las temperaturas límites de oxidación y creep del material del tubo y tomar decisiones como el momento adecuado para planificar una limpieza química (“Ver Figura 5”).
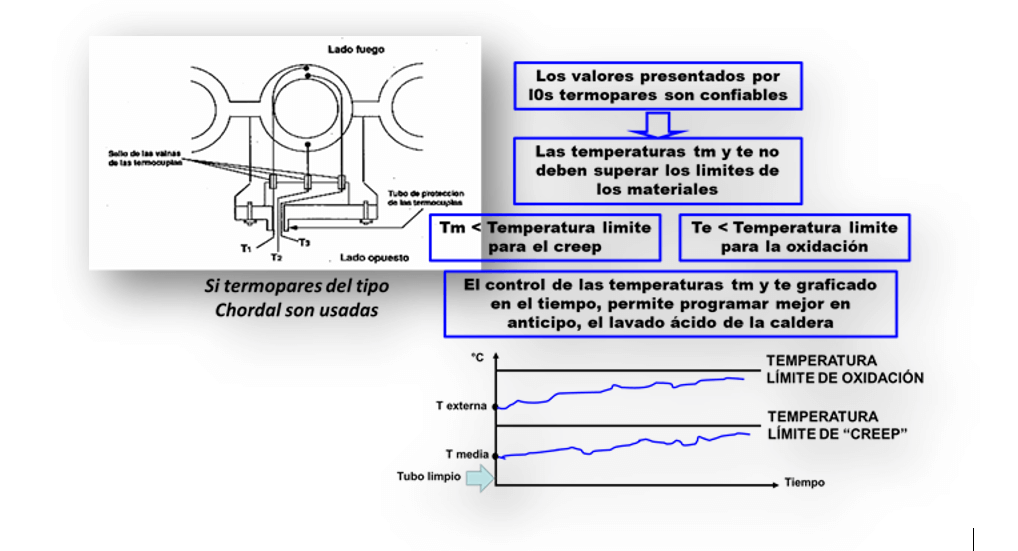
Colectores de sobre-calentadores
Aunque están ubicados en cámaras aisladas del paso de los gases de combustión, el ingreso de gases y superación de las temperaturas máximas de los materiales de estos colectores, puede acelerar el envejecimiento de los tubos por termofluencia lenta o creep.
Colector de salida de vapor del sobre-calentador secundario
Diferencias de temperaturas entre el lado derecho y el lado izquierdo en el colector de salida del vapor sobrecalentado – vapor producto, puede llegar a generar problemas de diferencias de dilatación y fatiga térmica en las uniones entre el colector y los tubos.
Tubos de los sobre-calentadores
- Cuyos materiales pueden ir desde aceros al carbono (temperatura máxima 1.000°F (538°C)), pasando por aceros bajo aliados (temperaturas máximas entre 1.000°F (538°C) y 1.200°F (649°C)) que en caso de igualar o superar estas temperaturas, puede acelerar el envejecimiento de los tubos por termofluencia lenta o creep.
Para el caso de los aceros inoxidables (temperaturas máximas en el orden de 1.500°F (816°C)) si las temperaturas de operación superasen estas temperaturas máximas puede acelerarse el proceso de envejecimiento por Sensitización.
Opciones adicionales de medición para el aumento de la fiabilidad
En la actualidad se dispone de la tecnología para el control avanzado del desempeño de la combustión, directamente en cada uno de los quemadores de la caldera, basado en el monitoreo de la composición del gas de combustión, con lo que pueden tomar las acciones operacionales correctivas en cada quemador individualmente en tiempo real, superando el control aproximado y con retraso (delay) de la señal que se tendría si la medición de los gases de combustión se hacen como tradicionalmente con base en una medición de gases en un área del ducto a la salida de la caldera (“Ver Figura 6”).
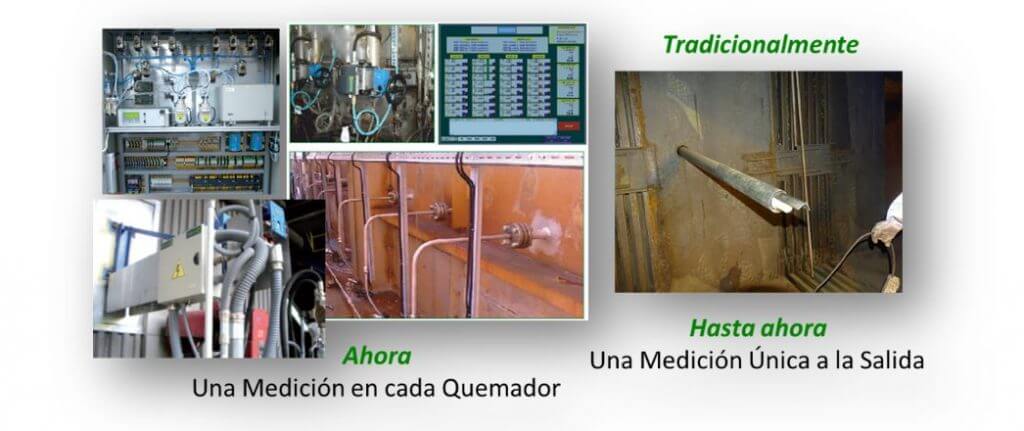
de la caldera.
Con esta opción, el operador cuenta con la posibilidad de aumentar la eficiencia, disponibilidad y seguridad. Adicionalmente, combinando esto con las mediciones de temperaturas de los elementos metálicos de los diferentes componentes de la caldera también se podrá prevenir áreas de alto flujo de calor y la aceleración de muchos de los mecanismos de daño que deberían esperarse con los años de operación.
Discusión y conclusiones
De acuerdo a la opinión de especialistas en el área de fiabilidad, existe la posibilidad de que la aplicación de mantenimiento proactivo o mantenimiento centrado en fiabilidad a calderas se vea limitado porque los propietarios o usuarios de estos equipos limitan sus acciones de mantenimiento e inspección a los requerimientos de los reglamentos donde la caldera esté instalada.
En el presente trabajo se plantea la conveniencia de llevar adelante planes de inspección de calderas, basándose en antecedentes de funcionamiento, que además de los históricos de control químico y contaminaciones, procesos de preservación, antecedentes de fallas, mantenimientos, reparaciones, regímenes de operación (ciclado), entre otra información, están muy relacionados con los valores de temperaturas de los fluidos (gases de combustión, agua y vapor) y de los metales de componentes críticos de la caldera en diferentes condiciones operacionales (arranques, paradas, condiciones de ciclado y condiciones normales). Esto permitirá definir los posibles mecanismos de daños a generarse en cada componente de la caldera.
Los planes de inspección no pueden limitarse a inspecciones visuales y mediciones de espesores, ya que existe una variedad de mecanismos de daño que no serán detectados y cuantificados haciendo uso únicamente de estos métodos.
Cada componente es susceptible a mecanismos de daños específicos
El incluir en las mediciones, supervisión y ajustes operacionales rutinarias, las mediciones de temperaturas de metal de los tubos y elementos críticos de la caldera, y además lograr una combustión controlada de manera más efectiva en tiempo real sobre cada uno de los quemadores, permitirán además de llevar adelante correcciones inmediatas para optimizar la eficiencia y la disponibilidad de las calderas, aumentar la fiabilidad y la integridad de las mismas.
Referencias
1) Real Decreto 2060/2008, de 12 de diciembre, Instrucción Técnica Complementaria (ITC EP1 y 2) Anexos “Inspecciones y Pruebas” Ensayos Suplementarios, BOE Núm 41, España 2009 [Real Decreto]
2) R. Tilley, “Boiler Condition Assessment Guideline”, EPRI (Electric Power Research Institute), Fifth Edition, USA 2011 [Reporte Final]
3) The Babcock & Wilcox Company “Steam its generation and use”, Capítulo 46, Edición 42, USA 2015 [Libro]
4) C. Lasarte, “Optimización del Plan de Inspección de Calderas para Alcances de Mantenimientos más Acertados y Mayor Fiabilidad”, ID AEND-3926, 14° Congreso Nacional de Ensayos No Destructivos, Vitoria – España junio 2019 [Artículo]
5) C. Lasarte, “Recommended Practice for Corrosion Management on Power Boilers of Medium and High Pressure”. ID 191720, EUROCORR 2019, Sevilla, España septiembre 2019 [Artículo]