Introducción
Los motores diésel han sido una pieza clave en la industria moderna debido a su eficiencia, durabilidad y capacidad para operar en diversas condiciones exigentes. Su presencia es fundamental en sectores como el transporte de carga, la generación de energía, la minería y la construcción, donde se requieren motores de alta potencia y bajo consumo de combustible. En particular, los motores de 4 tiempos han demostrado ser altamente eficientes en estas aplicaciones, y su funcionamiento está estrechamente vinculado al uso de aire comprimido en la combustión.
Desde su invención por Rudolf Diesel en el siglo XIX, estos motores han experimentado un desarrollo significativo, mejorando su eficiencia y reduciendo las emisiones contaminantes. La evolución tecnológica ha dado paso a sistemas de inyección electrónica, turboalimentación avanzada y filtros de partículas diésel (DPF), permitiendo un desempeño más limpio y sostenible sin sacrificar la potencia. Además, el uso de aire comprimido en estos motores mejora la eficiencia de la combustión y reduce la emisión de gases contaminantes.
Este artículo profundiza en el principio de funcionamiento de los motores diésel, sus tecnologías más innovadoras y sus principales aplicaciones industriales. Además, abordaremos los desafíos ambientales y las tendencias futuras que definirán el papel de estos motores en la industria, destacando la relevancia de los motores de 4 tiempos y el impacto del aire comprimido en su rendimiento.
Principio de funcionamiento de los motores diésel
Los motores diésel funcionan bajo el principio de combustión por compresión, lo que los distingue de los motores de gasolina, que operan mediante encendido por chispa. En un motor diésel, el aire es comprimido a alta presión, alcanzando temperaturas lo suficientemente elevadas para que el combustible se encienda espontáneamente al ser inyectado. Este proceso depende en gran medida del aire comprimido, el cual facilita una combustión eficiente y uniforme
El ciclo de combustión en motores diésel a 4 tiempos
El ciclo de los motores de 4 tiempos consta de cuatro fases principales:
- Admisión: Se abre la válvula de admisión y el pistón desciende, permitiendo la entrada de aire comprimido sin mezcla de combustible.
- Compresión: La válvula de admisión se cierra y el pistón asciende, comprimiendo el aire hasta que su temperatura es lo suficientemente alta para encender el diésel. El uso de aire comprimido en esta etapa es crucial para mejorar la eficiencia térmica del motor.
- Expansión (Combustión): En el punto máximo de compresión, el sistema de inyección introduce el combustible diésel pulverizado. La mezcla se inflama instantáneamente debido al calor generado por la compresión, provocando una explosión controlada que impulsa el pistón hacia abajo y genera la fuerza mecánica.
- Escape: El pistón vuelve a subir, abriendo la válvula de escape para expulsar los gases de combustión fuera del cilindro. En algunos sistemas modernos, el aire comprimido es utilizado en esta etapa para mejorar la evacuación de los gases y reducir la resistencia en el ciclo del motor.
Diferencias clave con los motores de gasolina
- Encendido: Mientras que los motores de gasolina requieren una bujía para la ignición, los motores de 4 tiempos diésel generan la combustión mediante la compresión del aire.
- Eficiencia térmica: Los motores de 4 tiempos diésel tienen una mayor eficiencia térmica, lo que significa que convierten más energía del combustible en trabajo útil.
- Consumo de combustible: Gracias a su diseño y a la mayor relación de compresión, los motores de 4 tiempos diésel consumen menos combustible en comparación con los de gasolina para la misma cantidad de energía generada.
- Durabilidad: Al operar a menores revoluciones por minuto (RPM) y utilizar materiales más robustos, los motores de 4 tiempos tienden a tener una vida útil más prolongada.
El papel del aire comprimido en la combustión
El aire comprimido juega un papel fundamental en el proceso de combustión de los motores de 4 tiempos diésel. Cuanto mayor es la compresión del aire, más alta es su temperatura, lo que permite que el diésel se encienda sin necesidad de chispa. Esta característica es clave para el rendimiento del motor, ya que una mayor compresión mejora la eficiencia energética y reduce el consumo de combustible.
En el siguiente videos verás como funciona un motor diésel, el ciclo de combustión y sus principales componentes. Mira la animación detallada aquí. Fuente: Automotive System.
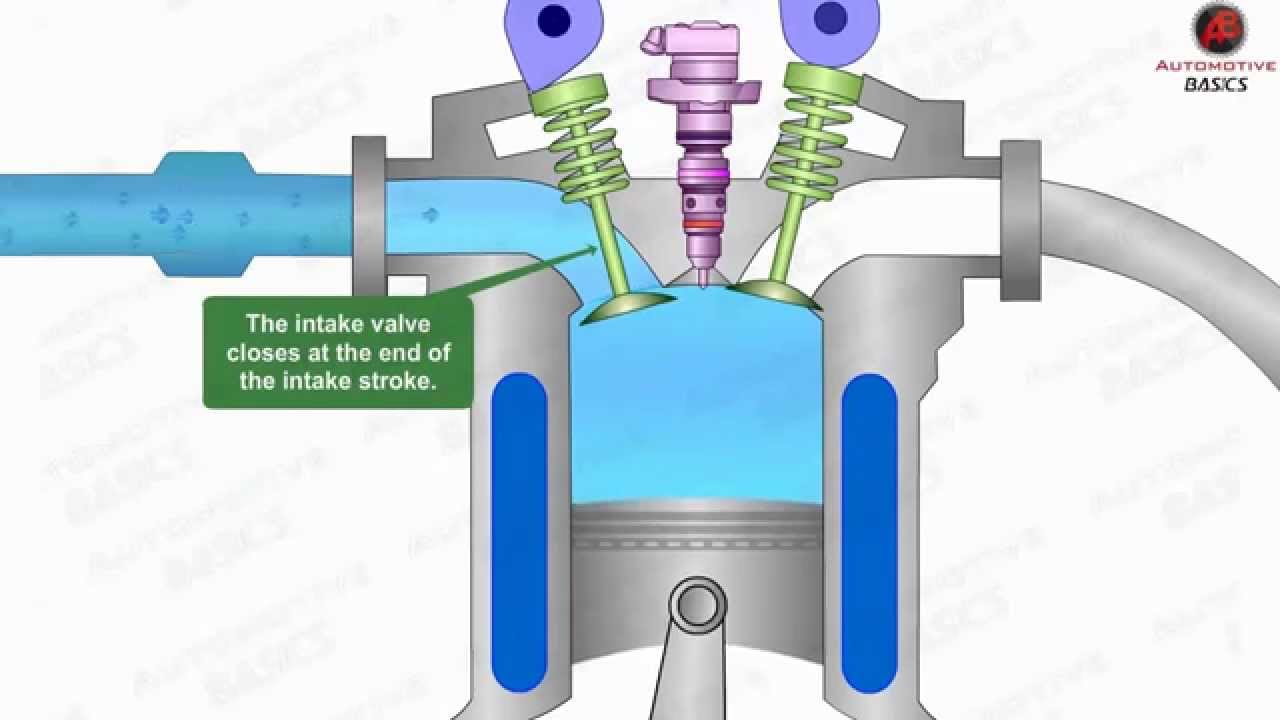
Tecnologías modernas en motores diésel
La evolución tecnológica ha permitido que los motores diésel sean más eficientes, potentes y ecológicos. A continuación, se analizan las innovaciones más importantes en estos motores.
Evolución de la inyección de combustible
Uno de los avances más importantes en los motores diésel ha sido la mejora de los sistemas de inyección de combustible. Originalmente, estos motores utilizaban inyección mecánica, que si bien era efectiva, no permitía un control preciso sobre la cantidad y el momento de la inyección.
Hoy en día, la mayoría de los motores modernos utilizan el sistema Common Rail, que ofrece ventajas significativas:
- Mayor eficiencia: Permite la inyección de combustible a alta presión en múltiples fases, optimizando la combustión.
- Menores emisiones: Reduce la producción de óxidos de nitrógeno (NOx) y partículas contaminantes.
- Menor ruido y vibraciones: Proporciona una combustión más uniforme y silenciosa.
Turboalimentación en los motores diésel
La turboalimentación se ha convertido en un estándar en los motores diésel modernos debido a los beneficios que ofrece en términos de potencia y eficiencia.
Ventajas de la turboalimentación en motores diésel
- Aumento de potencia: Un turbo permite introducir más aire en el cilindro, lo que mejora la combustión y aumenta la potencia del motor sin necesidad de incrementar su tamaño.
- Eficiencia en el consumo: Al aprovechar los gases de escape para alimentar el turbo, se reduce el desperdicio de energía y se mejora el rendimiento del combustible.
- Reducción de emisiones contaminantes: Mejora la mezcla aire-combustible, reduciendo la cantidad de partículas y gases nocivos.
Turbocompresores de geometría variable (VGT)
Una de las innovaciones más avanzadas en este campo es el uso de turbocompresores de geometría variable (VGT), que permiten ajustar el flujo de aire en función de las necesidades del motor. Esto se traduce en:
- Mejor respuesta a bajas revoluciones: Eliminando el retraso en la entrega de potencia (turbo lag).
- Mayor eficiencia en todo el rango de operación: Optimizando la combustión en diferentes condiciones de carga.
Filtros de partículas diésel (Diésel Particulate Filters – DPF)
El uso de filtros de partículas diésel (DPF) ha sido crucial en la reducción de emisiones contaminantes, atrapando partículas de hollín antes de que sean liberadas al ambiente. Sin embargo, su funcionamiento óptimo depende del uso de Diésel Ultra Bajo en Azufre (ULSD), ya que este combustible minimiza la acumulación de residuos en el filtro, prolongando su vida útil y reduciendo la necesidad de mantenimiento. Para conocer más sobre este combustible limpio y su impacto en la industria, puedes leer nuestro artículo sobre el Diésel Ultra Bajo en Azufre (ULSD).
Funcionamiento del DPF
- Atrapan y almacenan las partículas de hollín en su estructura porosa.
- Cuando el filtro alcanza su capacidad máxima, se activa un proceso de regeneración, en el cual las partículas atrapadas se queman a altas temperaturas.
Desafíos y mantenimiento del DPF
- Obstrucción del filtro: Si la regeneración no ocurre adecuadamente, el filtro puede bloquearse, reduciendo la eficiencia del motor.
- Consumo adicional de combustible: La regeneración forzada requiere más combustible para alcanzar la temperatura óptima de combustión del hollín.
- Soluciones tecnológicas: Nuevos diseños incluyen sensores de presión y temperatura para optimizar la regeneración y mejorar la vida útil del filtro.
Aplicaciones industriales de los motores diésel
Los motores diésel han sido un pilar fundamental en la industria debido a su alta eficiencia energética, gran capacidad de carga y durabilidad en condiciones extremas. Gracias a su diseño robusto y su bajo consumo específico de combustible, son la opción preferida en múltiples sectores que requieren potencia confiable y autonomía prolongada. A continuación, se detallan las principales aplicaciones industriales de estos motores.
Transporte de carga y logística
El transporte de carga pesada depende en gran medida de los motores diésel debido a su alta eficiencia y capacidad para operar durante largas jornadas sin interrupciones. Su presencia es notable en:
- Camiones de carga: La mayoría de los camiones de largo recorrido utilizan motores diésel debido a su mejor rendimiento en consumo de combustible y su capacidad para mover grandes volúmenes de mercancía.
- Trenes diésel-eléctricos: En regiones donde la electrificación ferroviaria no es viable, los trenes equipados con motores diésel generan la electricidad necesaria para su funcionamiento, proporcionando autonomía y potencia.
- Embarcaciones y buques de carga: El sector marítimo emplea motores diésel por su alta confiabilidad y eficiencia en trayectos de larga distancia. Motores de gran cilindrada y bajo régimen de revoluciones aseguran una operación continua con menor desgaste.
Sector energético
Los motores diésel desempeñan un papel crucial en la generación de energía, especialmente en aplicaciones donde la red eléctrica es inestable o inexistente. Entre sus principales usos en este sector destacan:
- Generadores eléctricos de respaldo: Hospitales, centros de datos, aeropuertos e industrias críticas utilizan generadores diésel como fuente de energía auxiliar para garantizar el suministro en caso de fallas en la red.
- Plantas de generación autónomas: En zonas remotas o aisladas, como plataformas petroleras y bases mineras, los motores diésel proporcionan energía confiable sin depender de infraestructuras eléctricas externas.
- Micro-redes y generación distribuida: En sistemas híbridos con energía renovable, los motores diésel se combinan con fuentes solares o eólicas para estabilizar la generación eléctrica y suplir demanda en períodos de baja producción renovable.
Industria de la construcción y minería
La maquinaria pesada utilizada en construcción y minería se basa en motores diésel debido a su gran capacidad de tracción y resistencia en entornos hostiles. Entre las aplicaciones más comunes se encuentran:
- Excavadoras, cargadores frontales y retroexcavadoras: Necesitan motores con alto torque para mover grandes volúmenes de material con eficiencia.
- Camiones volquetes para minería: Vehículos de gran tonelaje que operan en condiciones extremas requieren motores de alto desplazamiento y gran resistencia.
- Equipos de perforación y trituración: Utilizados en minería para extraer minerales, donde la confiabilidad y la autonomía son esenciales.
Sector agrícola
En el sector agroindustrial, los motores diésel han sido fundamentales para mejorar la eficiencia operativa y la mecanización de las labores agrícolas. Entre los equipos que dependen de estos motores se incluyen:
- Tractores agrícolas: Equipados con motores diésel a 4 tiempos que garantizan fuerza constante para arado, siembra y cosecha.
- Cosechadoras y sembradoras: Estas máquinas requieren motores con alto torque y durabilidad para operar en terrenos exigentes.
- Sistemas de riego: Bombas de agua impulsadas por motores diésel permiten la irrigación de grandes extensiones agrícolas sin depender de redes eléctricas.
El uso de motores diésel en estos sectores se debe a su capacidad para proporcionar gran potencia, bajo mantenimiento y autonomía en zonas remotas, factores esenciales en industrias que dependen de equipos robustos y confiables.
Desafíos y futuro de los motores diésel
A pesar de su eficiencia y versatilidad, los motores diésel enfrentan una serie de desafíos en un contexto donde la sostenibilidad ambiental y la reducción de emisiones se han convertido en prioridades globales. La industria ha respondido con innovaciones tecnológicas y el desarrollo de combustibles más limpios para garantizar la viabilidad de estos motores en el futuro.
Regulaciones ambientales y transición hacia energías más limpias
Las normativas ambientales, como la Norma Euro 6 en Europa y las regulaciones de la EPA en Estados Unidos, han impuesto límites estrictos a las emisiones de óxidos de nitrógeno (NOx) y partículas contaminantes generadas por los motores diésel. Para cumplir con estas regulaciones, los fabricantes han implementado tecnologías como:
- Sistemas de Reducción Catalítica Selectiva (SCR): Utiliza un aditivo de urea (AdBlue) para reducir las emisiones de NOx.
- Filtros de partículas diésel (DPF): Atrapan y eliminan el hollín generado por la combustión.
- Motores diésel híbridos: Integran sistemas eléctricos para mejorar la eficiencia y reducir el consumo de combustible.
Desarrollo de biocombustibles y combustibles sintéticos para motores diésel
La transición hacia combustibles alternativos es una de las estrategias clave para reducir la huella de carbono de los motores diésel. Entre las opciones más prometedoras destacan:
- Biodiésel (B100, B20): Derivado de aceites vegetales y grasas animales, puede ser utilizado en motores diésel convencionales con modificaciones mínimas.
- Diésel sintético (HVO – Hydrotreated Vegetable Oil): Un combustible renovable con propiedades similares al diésel fósil, pero con menor impacto ambiental.
- E-fuels y diésel sintético a base de hidrógeno: Desarrollados mediante procesos de captura de carbono y electrólisis, ofrecen una alternativa sostenible con combustión más limpia.
Innovaciones en reducción de emisiones y eficiencia térmica
El futuro de los motores diésel también se centra en mejorar su eficiencia térmica y reducir su impacto ambiental mediante innovaciones como:
- Motores de alta presión con mayor relación de compresión: Optimizan la combustión y reducen el consumo de combustible.
- Nuevas tecnologías de inyección múltiple: Permiten una pulverización más fina del combustible, mejorando la eficiencia y reduciendo emisiones.
- Hibridación y electrificación parcial: Combinar motores diésel con sistemas eléctricos para mejorar la eficiencia energética y reducir las emisiones en aplicaciones industriales y de transporte.
A pesar de los desafíos ambientales y regulatorios, los motores diésel continúan evolucionando con tecnologías más limpias y alternativas de combustible sostenible. Su papel en la industria sigue siendo crucial, especialmente en aplicaciones donde la eficiencia y la autonomía son primordiales. En el futuro, es probable que veamos una combinación de motores diésel avanzados, combustibles renovables y soluciones híbridas, garantizando su viabilidad en un mundo en transición hacia la sostenibilidad.
Protección contra la corrosión en motores diésel
Para prolongar la vida útil y garantizar la confiabilidad de los motores diésel, especialmente durante períodos de inactividad, almacenamiento o transporte, el uso de Inhibidores Volátiles de Corrosión (VCI) se ha vuelto cada vez más relevante.
Cortec Corporation ha desarrollado el VpCI®-706, un aditivo formulado para uso en combustibles diésel y biodiésel. Este innovador producto protege eficazmente las superficies metálicas ferrosas en contacto con el combustible y aquellas expuestas a la fase de vapor, mitigando el riesgo de corrosión. Su aplicación en los tanques de combustible de equipos pesados garantiza protección durante el almacenamiento, transporte y operación.
Conclusión
Los motores diésel han sido, y continúan siendo, una pieza clave en la industria moderna debido a su eficiencia energética, durabilidad y capacidad de carga. Su presencia en sectores como el transporte de carga, la generación de energía, la construcción, la minería y la agricultura evidencia su papel insustituible en aplicaciones que requieren potencia confiable y operación prolongada. A lo largo de los años, han evolucionado significativamente, adoptando tecnologías innovadoras como la inyección Common Rail, la turboalimentación avanzada y los filtros de partículas diésel (DPF), mejorando tanto el rendimiento como el impacto ambiental.
Sin embargo, los desafíos ambientales y regulatorios exigen una transformación continua. Normativas más estrictas han impulsado el desarrollo de sistemas de reducción de emisiones, así como la integración de biocombustibles y combustibles sintéticos, que ofrecen una alternativa más sostenible sin comprometer la eficiencia y autonomía de estos motores. La industria también ha apostado por soluciones híbridas y mejoras en la eficiencia térmica, garantizando su viabilidad en un futuro donde la sostenibilidad es prioridad.
En conclusión, aunque la electrificación avanza en diversas áreas, los motores de 4 tiempos seguirán desempeñando un rol crucial en la industria global. La combinación de tecnología avanzada, combustibles renovables y regulaciones ambientales más estrictas permitirá que estos motores evolucionen y continúen siendo una opción viable en el panorama energético y de transporte del futuro. Además, la implementación del aire comprimido en distintos procesos de combustión y escape continuará optimizando la eficiencia de estos motores, asegurando su adaptabilidad a nuevas exigencias industriales y ambientales.
Referencias
Fuente propia