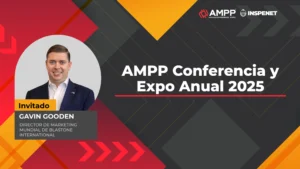
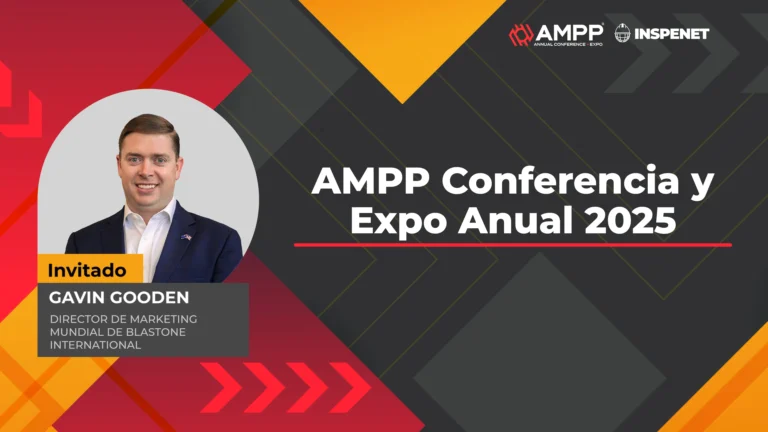
Robótica y datos inteligentes impulsan el chorro abrasivo industrial
Durante el evento AMPP 2025, el equipo de Inspenet tuvo la oportunidad de entrevistar a Gavin Gooden, Director Global de Marketing de BlastOne International, quien dejo en claro que el futuro del chorro abrasivo está en la automatización. La empresa, con más de 15 años en Estados Unidos y raíces australianas, ha desarrollado soluciones para enfrentar lo que considera un entorno de trabajo polvoriento, sucio y peligroso, a traves de la robótica industrial al servicio de la seguridad y productividad.
El ejemplo más claro es el VertiDrive, un robot que sostiene hasta tres boquillas de granallado de alta capacidad y es capaz de subir por paredes de tanques industriales, haciendo el trabajo de entre tres y cinco operarios. Un caso reciente mostró que una tarea que normalmente tomaba 14 días con 8 personas, se completó en 6 días con solo 3 operarios gracias al VertiDrive.
Sectores que ganan con la automatización del chorro abrasivo
El sector oil & gas lidera la adopción de estas tecnologías, con usos en tanques de almacenamiento y grandes estructuras metálicas, como las de astilleros y ferrocarriles, se benefician directamente de la robótica por su escala y la necesidad constante de mantenimiento de superficies.
En refinerías, donde los dueños de activos buscan reducir el trabajo en altura, la automatización ha dejado de ser una opción para convertirse en una prioridad. Al utilizar estos robots, es posible automatizar hasta el 95% del trabajo en altura, reduciendo drásticamente la exposición de los trabajadores a riesgos.
Seguridad laboral con sistemas robóticos
El gran impacto de estos sistemas no es solo económico, sino también humano, es por ello que BlastOne ha diseñado sus robots pensando en minimizar los peligros físicos del chorro abrasivo manual. Equipos como el Q-Layers permiten pintar superficies de tanques sin necesidad de andamios ni cestas, encapsulando la pintura para evitar la sobrepulverización, mientras que el BlastMan, utilizado en salas de granallado fijas, puede procesar hasta 2,000 libras de abrasivo por hora, reduciendo significativamente los tiempos y el contacto directo con partículas peligrosas.
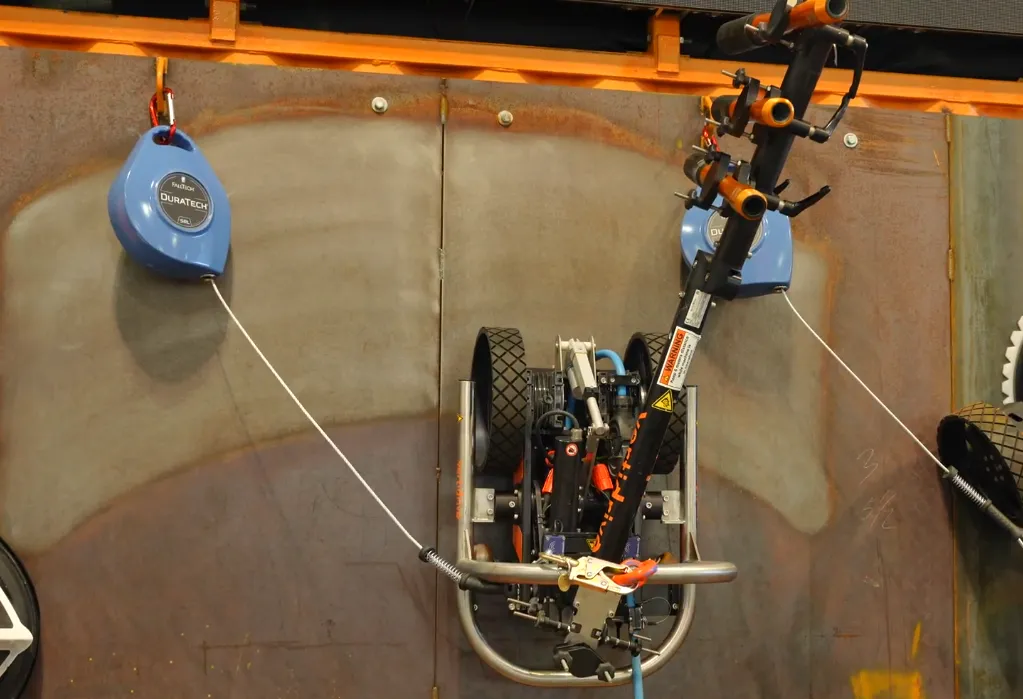
Inteligencia artificial y monitoreo con IntelliBlast
Además de la robótica, BlastOne ha incorporado sistemas inteligentes para el monitoreo remoto, como su tecnología IntelliBlast, que permite registrar en tiempo real tres métricas clave: presión del chorro, horas efectivas de trabajo y consumo de abrasivo. Supervisores pueden acceder a estos datos desde cualquier lugar, lo que evita pérdidas operativas por errores como presiones incorrectas o fugas no detectadas.
Este tipo de soluciones no solo evita gastos innecesarios, también empodera a los equipos de campo con retroalimentación inmediata y control total del rendimiento del sistema.
Para más contenido de AMPP 2025, visita nuestro canal de YouTube y perfil de LinkedIn.
Fuente: Inspenet.