Tabla de Contenidos
- ¿Qué es el análisis de vibraciones?
- ¿Para qué sirve el análisis de vibraciones?
- Principios físicos: amplitud, frecuencia y valor overall
- Definición técnica de la vibración mecánica
- Métodos de análisis de fallas de vibraciones
- Limites de crierios permisibles
- Buenas prácticas en monitoreo de condición
- Importancia del análisis en mantenimiento predictivo
- Frecuencia y amplitud como indicadores de falla
- Medición de vibración general (valor Overall)
- Casos prácticos de diagnóstico de fallas
- Sensores y herramientas en el análisis de vibraciones.
- Conclusiones
- Referencias
Mediante el análisis de vibraciones, los técnicos de mantenimiento predictivo de equipos rotativos, son capaces de monitorear, analizar las fallas y condición de los componentes de las maquinarias y obtener el diagnóstico más acertado posible.
En este artículo se realiza una breve exposición sobre los métodos de análisis típicos como, por ejemplo: dominio de tiempo, dominio de frecuencia, análisis modal, onda de tiempo, medición de fase, entre otros; así como, los conceptos más importantes y las herramientas necesarias para realizar el análisis de las maquinarias.
¿Qué es el análisis de vibraciones?
En el dinámico entorno de la industria moderna, donde la eficiencia operativa y la continuidad de servicio son prioridades estratégicas, el análisis y diagnóstico de vibraciones se ha consolidado como una de las herramientas más poderosas del mantenimiento predictivo.
Esta técnica permite detectar, interpretar y anticipar una amplia gama de fallas mecánicas en equipos rotativos (como bombas, compresores, turbinas y motores eléctricos) mediante la captura y evaluación de las señales vibracionales que generan durante su funcionamiento.
El comportamiento vibracional de un equipo es, en esencia, un reflejo de su condición interna. A través de acelerómetros, sensores de velocidad o proximidad, se pueden medir variables clave como amplitud, frecuencia y fase, cuya evolución revela la presencia de desbalances, desalineaciones, flojedad mecánica, cavitación, resonancia o problemas de lubricación, entre otros.
Gracias a algoritmos como la Transformada Rápida de Fourier (FFT) y otras herramientas de análisis espectral, estas señales son transformadas en información comprensible y accionable para el personal técnico.
¿Para qué sirve el análisis de vibraciones?
El análisis de vibraciones permite detectar una amplia gama de fallas mecánicas de manera anticipada. Entre los defectos más comunes que pueden identificarse se encuentran:
- Desalineación de ejes y acoplamientos
- Desbalance dinámico de rotores
- Holgura mecánica y estructural
- Fallas en rodamientos (Pitting, desgaste, grietas)
- Problemas de lubricación
- Cavitación en bombas
- Resonancia estructural
Más allá del simple monitoreo, el diagnóstico por vibraciones posibilita una gestión proactiva del mantenimiento, mejorando la confiabilidad de los activos, reduciendo tiempos de parada no programados y extendiendo la vida útil de componentes críticos.
En un mundo cada vez más digitalizado, esta disciplina también se está integrando con sistemas de monitoreo en línea, sensores inteligentes (IoT) y algoritmos de inteligencia artificial para lograr una supervisión continua, precisa y en tiempo real. Esta herramienta es fundamental en el mantenimiento predictivo, ya que evita paradas no programadas, reduce costos de reparación y aumenta la vida útil de los activos
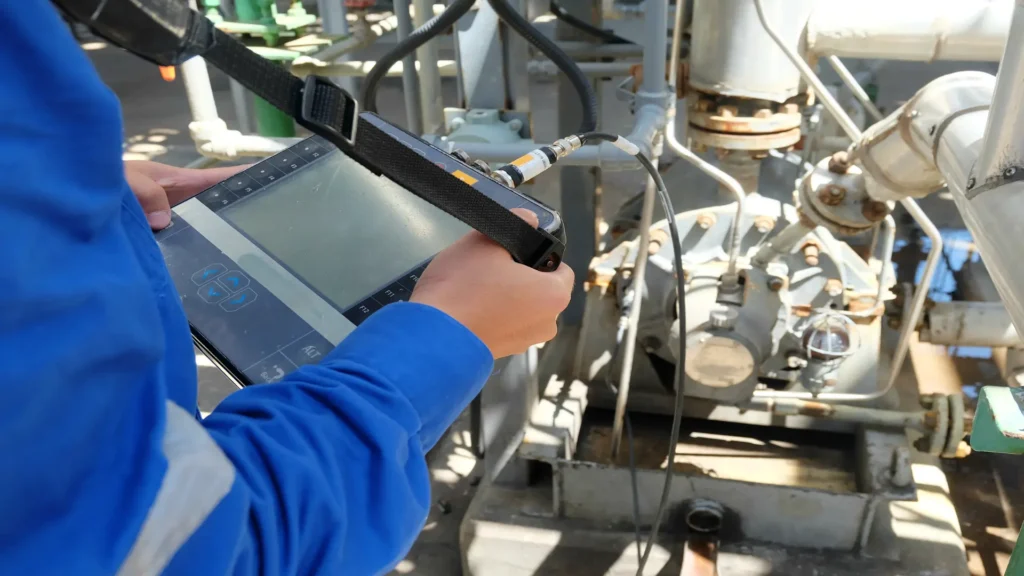
El análisis de vibraciones es una disciplina que permite identificar y anticipar fallas mecánicas antes de que se conviertan en paradas costosas. Cada medición registrada por los sensores (como acelerómetros) alimenta un proceso de interpretación espectral que, bien aplicado, transforma datos crudos en conocimiento confiable.
Este proceso exige una actitud crítica, meticulosa e investigativa por parte del especialista. No basta con detectar una frecuencia anómala; se requiere comprender su origen, correlacionarla con el comportamiento dinámico del equipo y traducirla en una recomendación técnica certera.
Principios físicos: amplitud, frecuencia y valor overall
Amplitud y frecuencia son los dos parámetros principales en vibración. La frecuencia indica cuántas veces ocurre una vibración en un tiempo determinado, y está asociada al tipo de falla. La amplitud indica la energía de la vibración y representa la gravedad del defecto.
El valor Overall es un indicador global del nivel vibracional, medido generalmente en mm/s RMS. Este valor es comparado contra criterios de severidad (como los de ISO 10816 o API 610) para evaluar el estado general del equipo.
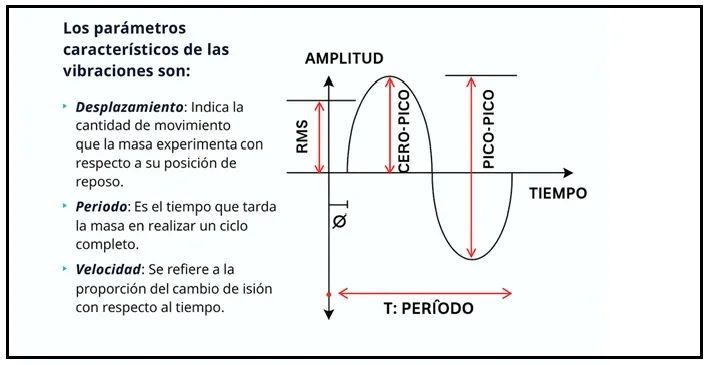
Definición técnica de la vibración mecánica
La vibración se define como el movimiento oscilatorio de un componente mecánico sometido a excitaciones internas o externas. Esta respuesta puede medirse como una función del tiempo o de la frecuencia, permitiendo identificar patrones que alerten el deterioro incipiente de elementos críticos, como rodamientos, ejes o acoplamientos.
Métodos de análisis de fallas de vibraciones
Existen diversas metodologías de análisis, entre ellas:
- Dominio del tiempo: evaluación de la forma de onda cruda.
- Dominio de la frecuencia: análisis espectral mediante FFT (Transformada Rápida de Fourier).
- Análisis modal: determinación de modos naturales y resonancias estructurales.
- Medición de fase: empleada para confirmar desalineaciones y problemas de montaje.
- Envelope detection: muy eficaz en detección temprana de fallas en rodamientos.
Los diagramas de tiempo y frecuencia de las señales recibidas ondas incidentes transversal y la onda longitudinal generadas individualmente, se muestran en la siguiente imagen.
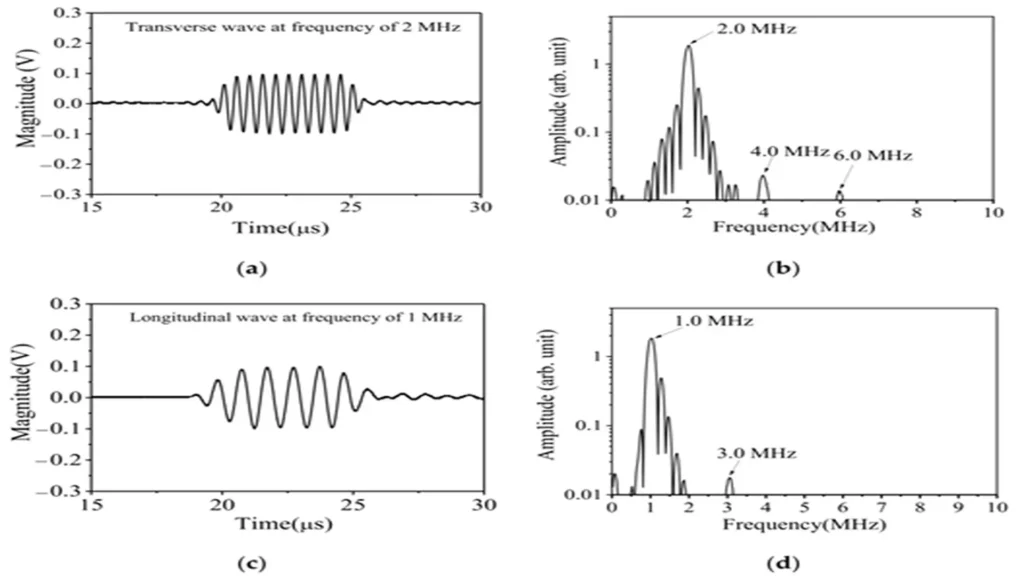
Tabla 1. Relación entre fallas típicas y su firma espectral.
Falla común | Frecuencia esperada | Síntoma en espectro | Severidad típica |
---|---|---|---|
Desbalanceo | 1X RPM | Pico dominante a 1X | Baja |
Desalineación | 2X–3X RPM | Armónicos múltiples | Media |
Holgura mecánica | Baja frecuencia | Pico de baja frecuencia + armónicos | Alta |
Falla de rodamiento | Alta frecuencia (10–20 kHz) | Bandas laterales (Envelope) | Alta |
Limites de crierios permisibles
Vibraciones: criterios de severidad
Los valores vibratorios aceptables están definidos por normas como ISO 10816-3 e ISO 20816-1, y API 610 para bombas centrífugas. A continuación, se presenta una guía básica:
Tabla 2. Niveles de severidad según ISO 10816 (en mm/s RMS)
Tipo de máquina | Bueno | Aceptable | Inaceptable |
---|---|---|---|
Bombas pequeñas (<15 kW) | <1.8 | 1.8–2.8Time domain signals (a,c) and amplitude-frequency curves (b,d). | >2.8 |
Bombas medianas (15–75 kW) | <2.8 | 2.8–4.5 | >4.5 |
Bombas grandes (>75 kW) | <3.5 | 3.5–5.6 | >5.6 |
Es importante considerar que algunos equipos tienen patrones vibracionales únicos, por lo que deben establecerse valores de referencia propios (baseline). El equilibrado dinámico, es el proceso mediante el cual se reduce la vibración provocada por un exceso de masa en una zona del rotor que provoca que su centro de masa se aleje de su centro geométrico.
Existen 3 formas de evaluar un buen balanceo:
- Norma ISO-1940 (grado de calidad en bases flotantes)
- Norma ISO-10816 (por Clases de Maquinaria)
- Desbalance Residual (en g.mm/kg)
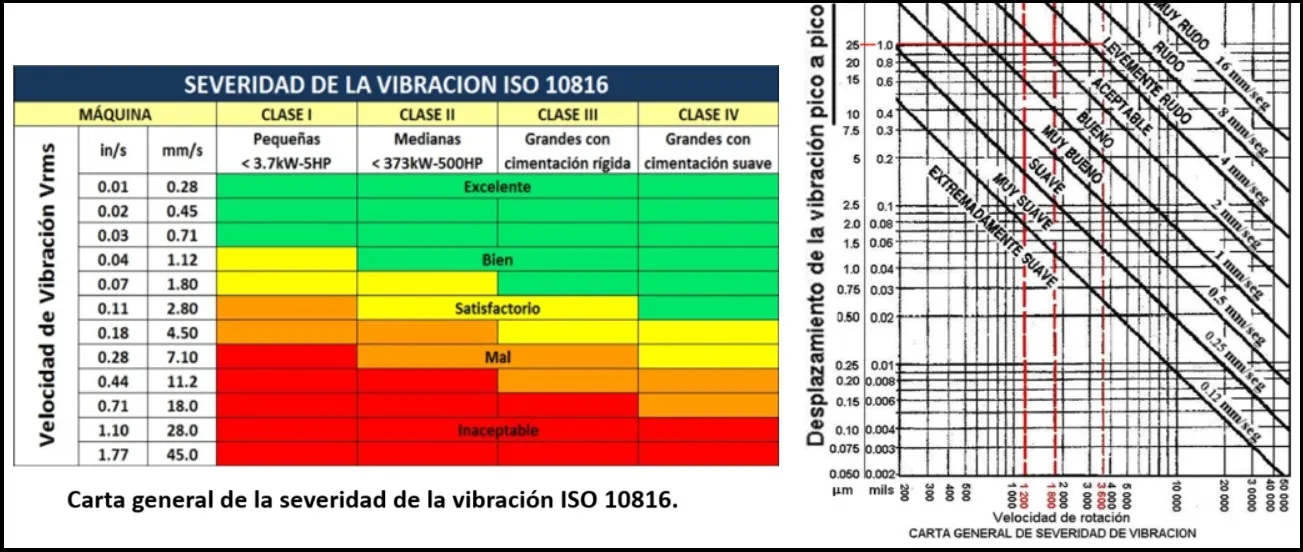
Buenas prácticas en monitoreo de condición
- Conocer el comportamiento vibracional normal de cada máquina.
- Observar tendencias para detectar desviaciones.
- Instalar sensores sobre superficies rígidas y en puntos críticos (horizontal, vertical, axial).
- Usar protecciones térmicas y de seguridad al medir cerca de tuberías o sellos calientes.
- Evitar interferencias en la ruta del cableado.
Importancia del análisis en mantenimiento predictivo
En programas de mantenimiento predictivo, el monitoreo continuo mediante análisis de vibraciones permite detectar fallas antes de que se materialicen en paradas no programadas.
No basta con reemplazar componentes defectuosos; es fundamental identificar la causa raíz para evitar reincidencias. El análisis vibracional aporta datos objetivos para ejecutar acciones correctivas efectivas.
La frecuencia es el número de veces que ocurre un evento en un periodo dado (un periodo denotado por T), es el tiempo necesario para que un ciclo completo de vibración pase por un punto dado. Siendo el evento un ciclo de vibración.
Frecuencia y amplitud como indicadores de falla
La correcta identificación de las frecuencias presentes en el espectro vibracional permite asociarlas a mecanismos de falla específicos. La amplitud, por su parte, ofrece una estimación cuantitativa de la gravedad del problema. Ambos factores deben interpretarse conjuntamente para un diagnóstico certero.
La frecuencia a la que se produce la vibración indica el tipo de fallo. Es decir, ciertos tipos de fallas presentan un comportamiento típico que ocurren a ciertas y determinadas frecuencias. Cuando logramos establecer la frecuencia a la que se produce la vibración, obtenemos una imagen más definida de lo que podría estar causándola.
La amplitud es el tamaño de la señal de vibración. Esta amplitud determina la gravedad de la falla. Cuanto mayor sea la amplitud, mayor será la vibración y obviamente será mayor el problema.
Medición de vibración general (valor Overall)
El valor Overall es un indicador global del nivel vibracional dentro de un rango de frecuencias. Comparar esta lectura con criterios de severidad establecidos permite evaluar el estado general del equipo. Incrementos en este valor sugieren la aparición o evolución de fallas mecánicas.
Es la energía de vibración total medida dentro de un rango de frecuencia. Cuando procedemos a medir la vibración general de la máquina (overall) de una máquina y comparamos esa lectura con su valor normal determinado en las tablas de criterios de severidad de vibración para las máquinas, esta nos indicara el estado actual de la máquina. Una lectura overall más alta de lo normal obviamente nos estará indicando que algo está ocasionando que algún componente de la máquina vibre más.
La vibración es considerada como el mejor parámetro operativo para medir las condiciones dinámicas de baja frecuencia, como el desbalance, la holgura mecánica, la desalineación, la resonancia estructural, la base blanda, la deflexión del eje, el desgaste de los cojinetes. Los límites de vibración permisibles para bombas centrífugas se pueden encontrar en la norma API 610 o ISO 10816-7.
Casos prácticos de diagnóstico de fallas
Un rodamiento con desgaste puede generar un pico de alta frecuencia detectable mediante análisis FFT. Pero si no se corrige una desalineación previa, el nuevo rodamiento también fallará.
Caso de una bomba P-2101 B de alimentación de una planta de Flexicoker
Ejemplo: en una bomba centrífuga, un valor overall que supera los 4.5 mm/s en dirección axial puede indicar un acoplamiento rígido mal alineado. La correcta interpretación de estos datos permite tomar decisiones de mantenimiento efectivas.
Este fue el caso de una bomba P-2101 B de alimentación de una planta de Flexicoker, que presento niveles anormales de vibración y después de su evaluación y análisis se determinó que un mal alineamiento estaba ocasionando ese comportamiento del equipo. La recomendación fue alinear utilizando un equipo tipo laser y se corrigió esa anormalidad. La bomba volvió a sus niveles normales de funcionamiento.
Caso práctico de diagnóstico vibración de un soplador
La vibración alta en el soplador de una caldera debido a un desbalance es un problema común y puede solucionarse mediante varias medidas correctivas. A continuación, se presenta un enfoque paso a paso que se utilizó en el soplador de una caldera en una instalación de Servicios Industriales de una Refinería de petróleo, para diagnosticar y solucionar el problema eficazmente.
Paso para balancear un soplador y por qué es importante?
Durante el balanceo del rotor del soplador, los técnicos utilizan una máquina de balanceo para medir la amplitud de vibración del soplador y determinar dónde aumenta su frecuencia. Posteriormente, limpian el ventilador y realizan los ajustes necesarios para balancearlo, mejorando así su eficiencia.
1. Inspeccione si hay materiales extraños y suciedad: Como primer paso revise si hay residuos: Inspeccione el rotor del soplador en busca de residuos, polvo o acumulaciones (como aislante, papel u otros materiales extraños) que puedan causar un desbalance. Incluso una pequeña cantidad acumulada de residuos puede ocasionar vibraciones significativas.
2. Limpie a fondo: Retire cualquier material adherido al rotor del soplador y asegúrese de que todas las superficies estén limpias y libres de polvo o residuos.
3. Verifique si hay daños físicos: Inspección visual: Busque aspas dobladas, agrietadas o desgastadas, o cualquier deformación física del rotor o el cubo.
4.Repare o reemplace: Si encuentra algún daño, repare o reemplace el rotor del soplador según sea necesario para restablecer el balance adecuado.
5. Inspeccione el montaje: Apriete: Asegúrese de que todos los pernos de anclaje estén bien apretados. Un rotor con pernos de anclaje flojos, puede simular o empeorar los síntomas de desbalance.
6. Estado del soporte: Verifique la integridad de las superficies y estructuras de montaje. Los soportes dañados o inadecuados pueden contribuir a la vibración.
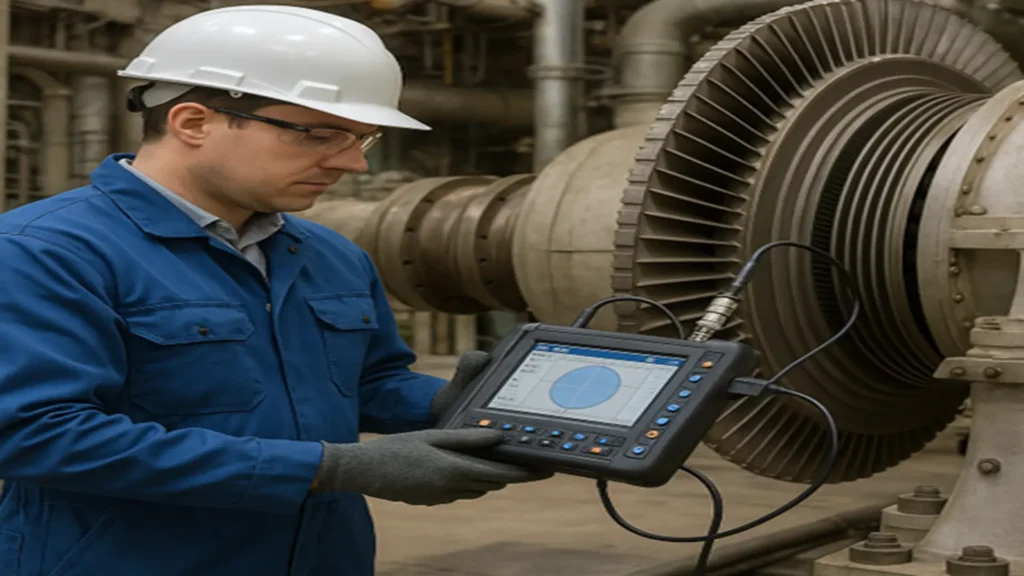
7. Realice el balanceo del rotor: El mejor método de balanceo para un rotor depende de su longitud y velocidad de operación. Para rotores cortos y velocidades bajas, el balanceo estático puede ser el más adecuado. Para rotores largos y que trabajan a velocidades altas, se requiere un balanceo dinámico, que puede ser en uno o dos planos.
Existen las máquinas balanceadoras, que pueden ser estáticas o dinámicas, y los analizadores de vibración con sensores y software especializado, son los equipos necesarios para realizar un balanceo satisfactorio. Reinstalar y probar: Una vez terminado el trabajo de balancear, vuelva a instalar el rotor del soplador y fíjela firmemente. Haga funcionar el soplador a máxima velocidad para confirmar que se haya reducido la vibración.
Sensores y herramientas en el análisis de vibraciones.
1. Acelerómetros: Los acelerómetros son sensores piezoeléctricos o MEMS diseñados para medir la aceleración vibratoria (m/s² o g) de una superficie. Funcionan mediante un cristal piezoeléctrico que genera una carga eléctrica proporcional a la aceleración cuando se somete a fuerzas dinámicas.
- Aplicaciones típicas: Detección de desbalance, desalineaciones, fallas en rodamientos y holguras mecánicas.
- Captura de frecuencias medias y altas (>10 Hz hasta 10-15 kHz).
- Buenas prácticas:
- Fijación rígida mediante tornillo o base magnética.
- Cableado blindado.
- Montaje sobre superficies rígidas.
2. Sensores de Proximidad: Estos sensores sin contacto detectan la variación en la distancia entre el sensor y una superficie conductiva, típicamente el eje del equipo, utilizando el principio de corrientes parásitas.
- Aplicaciones típicas:
- Monitoreo de turbinas, compresores y maquinaria crítica.
- Medición directa del desplazamiento del eje.
- -Análisis de órbitas y fenómenos dinámicos del rotor.
- Buenas prácticas:
- Calibración según API 670.
- Alineación precisa del sensor.
- Verificación periódica del gap y señal.
3. Velocidad RMS (Root Mean Square): La velocidad RMS representa la energía vibratoria total de una señal, expresada en mm/s o in/s. Es ideal para evaluar la severidad general de la vibración.
- Aplicaciones típicas:
- Evaluación del estado general de la máquina.
- Comparación con normas ISO 10816/20816.
- Uso en monitoreo continuo.
- Buenas prácticas:
- Medición en tres direcciones.
- Establecimiento de umbrales de alarma.
- Filtrado adecuado del rango de frecuencia (10 Hz a 1 kHz).
Conclusiones
El análisis de vibraciones es mucho más que una técnica de diagnóstico: es una herramienta estratégica que permite al ingeniero y al especialista de predictivo descifrar el lenguaje oculto de las máquinas.
A través de la medición precisa de las oscilaciones mecánicas (captadas mediante acelerómetros y analizadas con espectros de frecuencia) es posible no solo detectar fallas incipientes, sino también entender su naturaleza, su evolución y su posible impacto operativo. Esta capacidad analítica, cuando se aplica con rigurosidad e inteligencia técnica, transforma la práctica del mantenimiento predictivo en una ciencia de anticipación y fiabilidad.
Adoptar una postura investigativa, inquisitiva y meticulosa en la interpretación de firmas espectrales permite al especialista no limitarse a detectar un síntoma, sino profundizar en la causa raíz, proponer acciones correctivas ajustadas y elevar el nivel de confiabilidad operativa.
En este contexto, el análisis del comportamiento de una maquina a través de su firma vibratoria deja de ser una rutina para convertirse en un arte de precisión técnica, donde cada frecuencia revelada es una pista, y cada patrón, una oportunidad para mejorar el desempeño, prevenir paradas costosas y proteger activos críticos.
Además, el análisis de vibraciones se integra eficientemente con otras técnicas de monitoreo de condición como el análisis de aceite, termografía infrarroja y ultrasonido. Esta integración permite construir sistemas de mantenimiento basados en confiabilidad (RCM), mejorando la capacidad de pronóstico y planificación de paradas.
Referencias
- Web Site: www.skfreliability.com
- Moubray JM, Development in Reliability – centred Maintenance.
- Bowers, SV; Integrated Strategy for Predictive Maintenance of AC induction motors.
- David Trocel GTS Confiabilidad C.A. www.confiabilidad.com.ve
- https://www.cambridge.org/core/books/abs/dynamics-of-rotating-machines/introduction-to-vibration-analysis
- https://www.researchgate.net/publication/354476610_Detection_and_Location_of_Surface_Damage_Using_Third-Order_Combined_Harmonic_Waves_Generated_by_Non-Collinear_Ultrasonic_Waves_Mixing