Tabla de Contenidos
- Introducción
- ¿Qué es un reactor?
- Tipos de reactores y su rol en los procesos de refinación de hidrocarburos
- Procesos en la refinación y sus reactores asociados
- Factores que influyen en la selección de reactores
- Rol en los reactores en los procesos de refinación de hidrocarburos
- Desafíos y tendencias en el diseño de reactores
- Conclusión
- Referencias
Introducción
La refinación de hidrocarburos es un proceso diseñado para transformar el petróleo crudo en productos de alto valor comercial, como combustibles, lubricantes y productos petroquímicos. En el núcleo de estos procesos industriales se encuentran los reactores, dispositivos que facilitan las transformaciones químicas necesarias para obtener productos específicos. Este artículo explorará los tipos de reactores más utilizados en la industria de la refinación de hidrocarburos, su rol esencial y las particularidades que los hacen efectivos en aplicaciones específicas.
¿Qué es un reactor?
En los procesos de refinación de hidrocarburos, un reactor es un recipiente a presión diseñado para que en su interior ocurran reacciones químicas controladas. Estas reacciones implican transformaciones químicas en las que diferentes sustancias, conocidas como reactivos, interactúan bajo condiciones específicas de temperatura, presión y, en muchos casos, con la ayuda de catalizadores para producir productos de alto valor agregado. Los reactores son fundamentales en la refinación de los hidrocarburos, ya que facilitan la fabricación de una amplia variedad de productos, como combustibles (gasolina, diésel, queroseno), lubricantes y productos químicos básicos utilizados en diversas aplicaciones industriales.
Tipos de reactores y su rol en los procesos de refinación de hidrocarburos
Existen diversos tipos de reactores quimicos utilizados en la refinación de hidrocarburos, cada uno diseñado para satisfacer necesidades específicas según el tipo de reacción y las características del proceso. Los más destacados incluyen:
Reactores de lecho fijo: Son comúnmente empleados en procesos de hidrotratamiento y reformado catalítico. En este tipo de reactor, el catalizador permanece inmóvil, mientras el flujo de hidrocarburos atraviesa el lecho.
- Ventajas: Proporcionan un contacto uniforme entre los reactivos y el catalizador, lo que mejora la conversión y la selectividad.
- Aplicaciones: Hidrotratamiento, desulfuración y reformado catalítico.
- Limitaciones: Pueden presentar problemas de acumulación de coque, lo que afecta la actividad del catalizador.
Reactores de lecho fluidizado: En este diseño, el catalizador está en forma de partículas finas que se suspenden mediante un flujo ascendente de gas o líquido. Este tipo de reactor es ampliamente utilizado en el craqueo catalítico.
- Ventajas: Excelente transferencia de calor y masa, alta capacidad de procesamiento y posibilidad de regeneración continua del catalizador.
- Aplicaciones: Craqueo catalítico, procesos de alquilación.
- Limitaciones: Requiere sistemas complejos para la separación del catalizador del producto.
Reactores tubulares: Son alargados y de sección transversal pequeña donde los reactivos fluyen a través de un tubo que puede estar revestido con catalizador. Son ideales para reacciones endotérmicas debido a su capacidad de disipar calor.
- Ventajas: Control preciso de la temperatura y la posibilidad de manejar altas presiones.
- Aplicaciones: Reformado catalítico y procesos de oxidación.
- Limitaciones: Alta complejidad en el diseño y mantenimiento.
Reactores de tanque agitado: Este tipo de reactor utiliza un agitador para mezclar los reactivos y el catalizador, garantizando un contacto uniforme. Se emplean en procesos donde la homogeneidad es crucial.
- Ventajas: Flexibilidad en la operación y diseño, y buena transferencia de calor.
- Aplicaciones: Hidrogenación, síntesis química.
- Limitaciones: Limitados a escalas pequeñas y medianas.
Procesos en la refinación y sus reactores asociados
Craqueo catalítico: Es un proceso endotérmico que rompe moléculas grandes de hidrocarburos en fracciones más pequeñas, como gasolinas y olefinas. Para este proceso, se utilizan reactores de lecho fluidizado de partículas catalíticas en movimiento continuo, ya que ofrecen una alta eficiencia de conversión y permiten la regeneración continua del catalizador.
Hidrotratamiento: Este proceso catalítico elimina impurezas como el azufre, nitrógeno y metales pesados de los hidrocarburos. Se utilizan reactores de lecho fijo debido a su capacidad para manejar flujos constantes de reactivos y su facilidad de operación en altas presiones y temperaturas.
Hidrocraqueo: Es un proceso catalítico que combina hidrogenación y craqueo para convertir fracciones pesadas de hidrocarburos en productos de mayor valor, como gasolinas, diésel y queroseno. Este proceso se lleva a cabo en reactores de lecho fijo que operan a altas presiones y temperaturas. Los reactores están diseñados para manejar flujos constantes de hidrógeno y permitir una distribución uniforme de los reactivos sobre el catalizador, lo que asegura una alta conversión y un control eficiente de las reacciones secundarias.
Reformado Catalítico: El reformado catalítico es un proceso endotérmico utilizado para mejorar la calidad de las naftas mediante el incremento del índice de octano. Se lleva a cabo en reactores de lecho fijo o continuo, donde se emplean catalizadores a base de platino y renio para promover reacciones como la isomerización, deshidrogenación y ciclización de los hidrocarburos. Estos reactores están diseñados para mantener una temperatura uniforme y controlar las condiciones de presión, garantizando la estabilidad del catalizador y la optimización de la producción de gasolina de alto octanaje y compuestos aromáticos.
Alquilación: La alquilación es un proceso exotérmico que combina olefinas ligeras, como el propileno y butileno, con isobutano en presencia de un catalizador ácido, como ácido sulfúrico o fluorhídrico. Los reactores utilizados en este proceso son de tipo continuo, con diseños que aseguran una mezcla eficiente de los reactivos y el control preciso de la temperatura para evitar reacciones secundarias no deseadas. Este proceso produce alquilatos de alto octanaje con baja emisión de contaminantes.
Craqueo Térmico (Coking): El craqueo térmico, o coking, es un proceso endotérmico en el que se descomponen hidrocarburos pesados a altas temperaturas sin uso de catalizadores para producir productos más ligeros, como naftas y gasóleo. Se utiliza un reactor de lecho fluido o de tipo horno tubular diseñado para soportar temperaturas extremas y minimizar la formación de coque en las paredes. Este proceso genera coque como subproducto sólido, el cual es separado del flujo principal y puede ser utilizado como fuente de energía o material precursor para otras industrias.
Isomerización: La isomerización es un proceso utilizado para convertir hidrocarburos lineales en sus isómeros ramificados, mejorando el índice de octano de las gasolinas. Los reactores empleados en este proceso son de lecho fijo y trabajan en condiciones moderadas de presión y temperatura, con catalizadores a base de platino o zeolitas. Estos reactores aseguran un flujo uniforme de reactivos, lo que optimiza la conversión y minimiza la formación de subproductos indeseables.
Reactor Claus: El proceso Claus es utilizado para la recuperación de azufre a partir de gases ricos en sulfuros de hidrógeno (H₂S). Los reactores Claus consisten en cámaras de reacción diseñadas para manejar reacciones exotérmicas de combustión parcial y conversión catalítica. Se emplean catalizadores específicos que maximizan la producción de azufre elemental al tiempo que aseguran una alta eficiencia en la eliminación de contaminantes gaseosos. El diseño del reactor incluye etapas de enfriamiento y condensación para facilitar la separación del azufre producido.
Desintegración Catalítica Hidrotérmica (H-Oil): Combina hidrotratamiento y craqueo catalítico en un reactor de lecho suspendido. Este reactor está diseñado para manejar fracciones pesadas de crudo y convertirlas en productos más ligeros, como gasóleos y combustibles destilados. La configuración del lecho suspendido asegura un contacto eficiente entre los reactivos y el catalizador en presencia de hidrógeno, lo que mejora la conversión y minimiza la formación de coque. Este diseño es ideal para manejar alimentaciones con altos niveles de impurezas y residuos.
Factores que influyen en la selección de reactores
La selección de reactores para un proceso específico depende de varios factores, como:
Naturaleza de la reacción química: Reacción catalítica o no catalítica: Si la reacción requiere un catalizador, se eligen reactores como los de lecho fijo o lecho fluidizado.
Reacción endotérmica o exotérmica: Procesos que involucran transferencia de calor, como el reformado catalítico (endotérmico) o el hidrotratamiento (exotérmico), requieren reactores con control térmico eficiente, como los de haz tubular o multitubulares.
Características de los reactivos y productos: Si los reactivos están en fase líquida, gaseosa o mixta, influye en el diseño del reactor. Por ejemplo, para reacciones gas-líquido, se prefieren reactores de tanque agitado o con lecho fluidizado.
Propiedades físico-químicas: Factores como viscosidad, densidad y reactividad determinan si se usa un reactor con alta agitación o alta presión.
Velocidad y selectividad de la reacción: Reacciones rápidas pueden requerir reactores pequeños con alta eficiencia de transferencia de calor y masa. Procesos donde se busca alta selectividad en productos, como alquilación, demandan reactores que minimicen la formación de subproductos no deseados.
Temperatura y presión: Reactores diseñados para condiciones extremas, como los de hidrocraqueo, deben ser resistentes y proporcionar seguridad operativa.
Tiempo de residencia: Dependiendo de la cinética de la reacción, se elige un diseño que optimice el tiempo de contacto entre reactivos y catalizador.
Tipo de catalizador: El catalizador empleado influye directamente en el diseño del reactor. Catalizadores sólidos utilizan reactores de lecho fijo o fluidizado, catalizadores líquidos o gaseosos requerir reactores con mezcla continua o configuración especial para minimizar pérdidas.
Costo y eficiencia económica: Los reactores deben balancear costo de instalación, mantenimiento y operación. Procesos complejos pueden justificar reactores de mayor inversión si generan un mayor rendimiento o reducen costos operativos.
Requerimientos de seguridad y ambientales: Reactores para procesos peligrosos (como la alquilación) deben estar diseñados con sistemas de seguridad avanzados. Los factores ambientales, como la generación de subproductos o emisiones, también influyen en la selección.
Escala del proceso: En refinerías de gran escala, se prefieren reactores modulares o de diseño optimizado para facilitar el mantenimiento y la expansión futura.
Rol en los reactores en los procesos de refinación de hidrocarburos
Los reactores tienen una función esencial en la mejora de la calidad de los productos refinados al transformar el petróleo crudo y sus fracciones en productos más valiosos y específicos. Esto se logra mediante reacciones químicas controladas, optimizadas por el diseño y las condiciones operativas del reactor. A continuación, se detallan los mecanismos mediante los cuales los reactores contribuyen a mejorar la calidad de los productos refinados:
Eliminación de Impurezas: Los reactores catalíticos eliminan compuestos no deseados como, azufre y metales pesados que afectan el rendimiento de los combustibles produciendo productos con menores emisiones contaminantes y mejor rendimiento en motores.
Incremento del octanaje: Los reactores de reformado producen compuestos aromáticos que elevan el octanaje de las gasolinas, mejorando su eficiencia y calidad.
Reducción del peso molecular: El craqueo en reactores convierte fracciones pesadas en combustibles más ligeros y útiles como gasolina y diésel.
Optimización del peso específico y la viscosidad: Los reactores que realizan reacciones de hidrotratamiento e hidrocraqueo modifican las propiedades físicas de los productos refinados, reduciendo la viscosidad de fracciones pesadas y ajustan el peso específico de combustibles para garantizar compatibilidad con estándares de motores.
Generación de productos específicos: El diseño y las condiciones de operación del reactor permiten obtener productos con bajo azufre para aplicaciones marítimas y terrestres, gasolina de alto octanaje mediante alquilación y reformado y lubricantes de alta pureza, mejorando la estabilidad térmica y química.
Control de reaccione térmicas y selectividad: Los reactores están diseñados para controlar la temperatura y presión, optimizando reacciones endotérmicas (Ej.: reformado catalítico) que producen productos de alto valor sin degradación térmica y exotérmicas (Ej.: alquilación) que controlan la liberación de calor para evitar la formación de subproductos no deseados.
Aprovechamiento de catalizadores: Los reactores potencian la acción de los catalizadores, que son fundamentales para aumentar la velocidad de reacción, mejorar la eficiencia del proceso y mejorar la selectividad hacia productos deseados, minimizando la formación de impurezas y residuos.
Producción de combustibles más Limpios y eficientes: La capacidad de los reactores para optimizar la química de los combustibles reduce su impacto ambiental y mejora el rendimiento de los diésel y gasolina.
Flexibilidad para procesar crudos de diferente calidad: En refinerías modernas, los reactores permiten procesar crudos pesados o con altos niveles de impurezas:
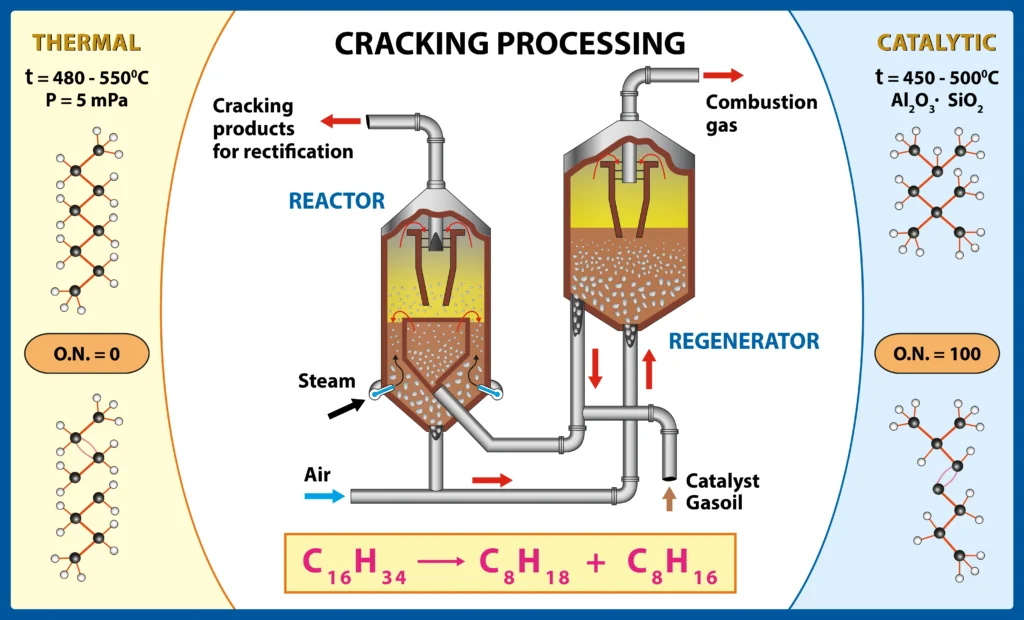
Desafíos y tendencias en el diseño de reactores
Con los avances tecnológicos, los reactores deben adaptarse a las demandas de sostenibilidad y eficiencia. Los diseños actuales se centran en:
- Mejorar la transferencia de calor y masa.
- Incrementar la vida útil de los catalizadores.
- Reducir las emisiones asociadas a los procesos de refinación.
Un ejemplo de innovación es el uso de simulaciones computacionales para optimizar el diseño y la operación de los reactores, lo que permite prever problemas y maximizar el rendimiento.
Conclusión
Los reactores desempeñan un papel crucial en la refinación de hidrocarburos, determinando la calidad y cantidad de los productos obtenidos. La selección del tipo de reactor y del catalizador adecuado es esencial para el éxito de los procesos industriales, como el craqueo catalítico y el hidrotratamiento. A medida que la industria evoluciona, los avances en diseño y tecnología seguirán transformando el panorama de los procesos de refinación, permitiendo una operación más eficiente, segura y sostenible.
Referencias
- https://www.chemengghelp.com/fixed-bed-reactor/
- https://es.slideshare.net/slideshow/fluidized-cataltic-cracking/111603643
- https://www.researchgate.net/figure/Alkylation-reactor-module_fig2_359178152
- https://www.biorender.com/template/stirred-tank-reactor-design
- https://www.shutterstock.com/es/image-vector/producing-fuel-crude-oil-catalytic-cracker-1311074066