Los sensores permanentes juegan un papel considerable en el análisis de riesgos industriales, ya que se necesita abordar de manera precisa y proactiva los riesgos asociados con las operaciones industriales para lograr un desarrollo óptimo. Aunque eliminar por completo los riesgos en este contexto implica retos constantes, como la optimización de la seguridad, la identificación y gestión eficiente de los peligros potenciales y problemas operacionales en tiempo real.
Estos dispositivos avanzados permiten la detección a tiempo de posibles riesgos, contribuyendo así a la prevención de incidentes y la mejora de la seguridad industrial. Además, al monitorear constantemente las condiciones operativas, los sensores permanentes posibilitan un mantenimiento predictivo, aumentando la eficiencia y prolongando la vida útil de los equipos, recopilan datos en tiempo real, facilitan la toma de decisiones informadas y mejoran la eficacia operativa reduciendo los tiempos de inactividad.
Estos dispositivos pueden percibirse como la clave para una evaluación continua y precisa de los riesgos, al permitir una respuesta ágil ante cualquier desviación en los sistemas industriales. Este enfoque técnico fortalece la capacidad de las empresas para enfrentar los desafíos de seguridad en entornos complejos. A continuación, se detallan algunos aspectos relevantes de estos sensores, y su influencia en las evaluaciones de riesgos
¿Qué es un sensor permanente?
Se trata de un dispositivo de medición instalado de manera permanente en una infraestructura específica, como por ejemplo un pozo petrolífero, con el propósito de proporcionar una vigilancia continua y precisa de variables, tales como: presión, temperatura y caudal, a lo largo de la producción. Este tipo de sensores, inspirados en el concepto del medidor permanente de fondo de pozo (PDG) introducido en 19631, representan una tecnología fundamental en la monitorización y caracterización de yacimientos petrolíferos.
Los medidores de fondo de pozo DataCan mostrados en la figura 1, registran parámetros fundamentales del pozo, como la presión, temperatura y flujo, con el propósito de obtener detalles sobre el rendimiento del pozo y ofrecer información relevante para mejoras en la productividad. Estos medidores de memoria pueden recopilar datos durante unas pocas horas o durante meses o incluso años.
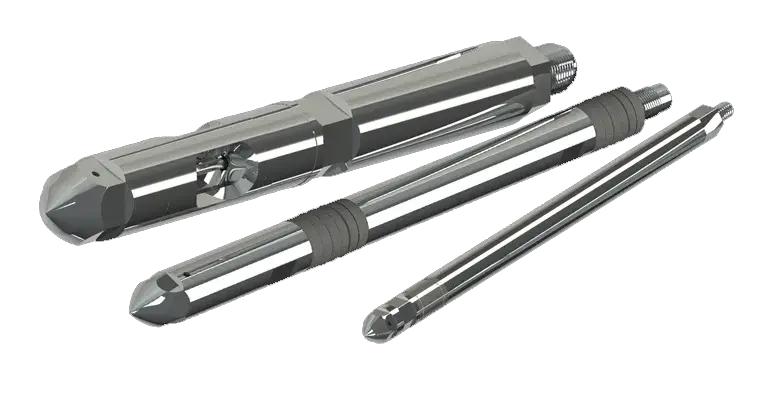
Los medidores de fondo de pozo ( Figura 2), están diseñados para resistir las condiciones más agresivas, incluidas altas presiones y temperaturas en ambientes corrosivos. Estos tipos de medidores tienen aplicaciones en pozos de petróleo, gas y geotérmicos para determinar las características de los fluidos.
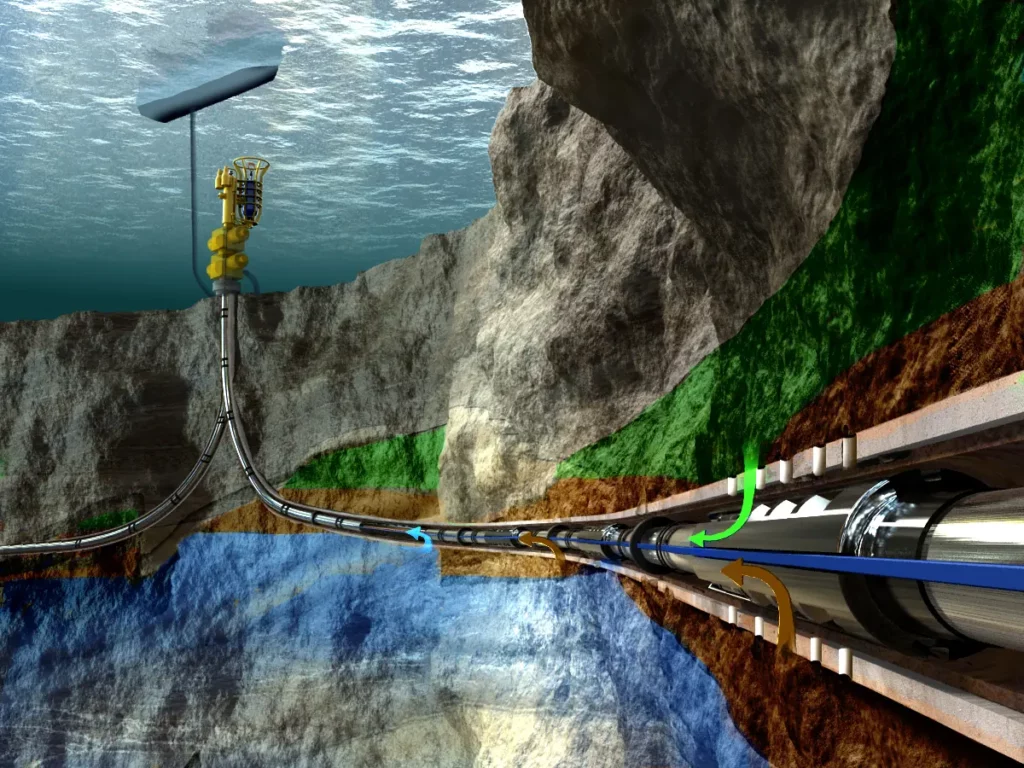
Su instalación permanente permite la obtención de datos continuos sobre el rendimiento de los yacimientos, brindando información valiosa para la interpretación y análisis de pruebas de pozos. En el ámbito industrial, los sensores permanentes se destacan por su contribución significativa a la comprensión y optimización de procesos mediante la recopilación continua de datos críticos.
Uso de sensores permanentes en análisis de riesgos industriales
- Monitorización continua de parámetros críticos: Este tipo de sensores permiten la supervisión ininterrumpida de variables como presión, temperatura y caudal en entornos industriales, identificando posibles desviaciones y riesgos.
- Detección de anomalías: Al proporcionar mediciones en tiempo real, se facilita la identificación inmediata de comportamientos no deseados en los procesos industriales, contribuyendo a una respuesta proactiva.
- Evaluación de yacimientos: En el sector petrolífero, son necesarios a la hora de evaluar yacimientos, esto se debe a la constante proporción de datos sobre el rendimiento de pozos y facilitando la toma de decisiones informada.
- Análisis de datos históricos: La recopilación continua de datos a lo largo del tiempo permite la creación de historiales detallados, ideal para el desarrollo de análisis retrospectivos para la identificación de patrones, tendencias y posibles mejoras en los procedimientos de gestión de riesgos.
- Validación de modelos de riesgos: La información constante proporcionada representa una fuente valiosa para validar y mejorar modelos de riesgos existentes, garantizando una evaluación más precisa y ajustada a la realidad.
Ventajas de utilizar sensores permanentes
Mejoramiento de la seguridad industrial
La detección de posibles amenazas como el aumento imprevisto de presión o problemas de sellado del cemento tras el revestimiento del pozo son ejemplos de la importancia que representan los sensores permanentes en las operaciones industriales. Principalmente, porque estos sistemas proporcionan información crítica para la seguridad de sistemas de producción y optimización de pozos.
Uno de sus mayores impactos se presenta en la gestión de la integridad de revestimientos de pozos, ya que la detección a tiempo de aumentos de presión es crucial para prevenir el deterioro de los revestimientos, las migraciones de petróleo y gas, y posibles explosiones de gas. El monitoreo constante de los fondos de pozos, en conjunto con estos sensores, contribuye significativamente con la mejoría de los estándares de seguridad en este tipo de operaciones industriales.
Reducción de costos
La implementación de los sensores en el análisis de riesgos industriales puede generar una optimización del tiempo del equipo de trabajo, esto se traduce en ahorros significativos al eliminar los costos asociados a inspecciones in situ y supervisión manual del nivel de fluido.
Algunos de estos sistemas de medición de fondo de pozo ofrecen datos en tiempo real y permiten la supervisión y control remotos, sustituyendo gastos relacionados con logísticas, combustible y seguros. Además, la protección mejorada de los equipos de fondo de pozo gracias a datos fiables en tiempo real puede evitar costosos procesos de sustitución.
Para procesos como la fracturación hidráulica y drenaje por gravedad asistido por vapor, donde los recursos utilizados son considerables, la gestión eficiente facilitada por los sensores permanentes optimiza la producción. La manera de lograrlo es por medio de la eliminación picos y descensos de variables como el caudal, presión y la temperatura, asegurando un uso efectivo de recursos y maximizando la rentabilidad.
Optimización de la producción y rentabilidad
Implementar estos sensores permanentes también se traduce en una optimización significativa de la producción y rentabilidad en operaciones. Frente a los costosos desafíos asociados a operaciones como la perforación de nuevos pozos, los sistemas permanentes funcionan como una alternativa eficaz con un coste menor, incrementando la rentabilidad al aumentar la producción e ingresos en todos los pozos en funcionamiento, de manera equiparable al desarrollo de nuevos proyectos, pero a una fracción del costo.
En entornos donde la liquidez es un desafío y los recortes de personal son inevitables, los sistemas de medición permanente permiten una reasignación efectiva de responsabilidades. Los datos en tiempo real posibilitan que el personal se enfoque en proyectos críticos, mientras que los sensores permanentes gestionan y supervisan el rendimiento del pozo de forma eficiente.
Esta estrategia rentable ofrece a las empresas energéticas la capacidad de aumentar rápidamente su producción e ingresos sin comprometer la calidad y eficiencia operativa, por lo que se considera como una de las mayores ventajas de utilizar sensores permanentes.
Análisis de datos de sensores permanentes en el manejo de riesgos industriales
Si bien la recolección constate de datos críticos por medio de sensores permanentes es un factor importante para garantizar la mitigación de riesgos industriales, resulta imprescindible analizar correctamente la información obtenida. Esto se debe a que, a partir del análisis de datos, se pueden llevar a cabo las medidas necesarias para asegurar una óptima resolución de problemas.
Diversos autores han contribuido al ofrecer distintos aspectos del análisis de datos de los sensores permanentes de fondo de pozo, los cuales pueden ser implementados en la gestión de riesgos industriales. Uno de estos fue Athichanagorn (1999), quien presentó una metodología para efectuar análisis de datos a largo plazo de medidores permanentes de fondo de pozo, abarcando una serie de pasos para lograr una efectiva interpretación de los datos2. Estas fases son:
1. Eliminación de valores atípicos: Los valores atípicos se definen como observaciones que se apartan significativamente de la tendencia general de los datos. Su identificación y eliminación de estas forma parte del proceso de filtrado, utilizando propiedades tanto antes como después de dichos valores atípicos. Esta eliminación implica la aplicación de transformaciones Wavelet.
2. Eliminación de ruido: El término «ruido» se refiere a las dispersiones y variaciones presentes en la tendencia general de los datos. Al igual que los valores atípicos, el ruido es eliminado a través de transformaciones Wavelet anulando el coeficiente de detalle Wavelet de baja frecuencia, lo que resulta en la reducción del ruido de alta frecuencia en la señal de datos. En la figura 3, se puede observar una comparación entre una señal original y su resultado luego de la eliminación del ruido.
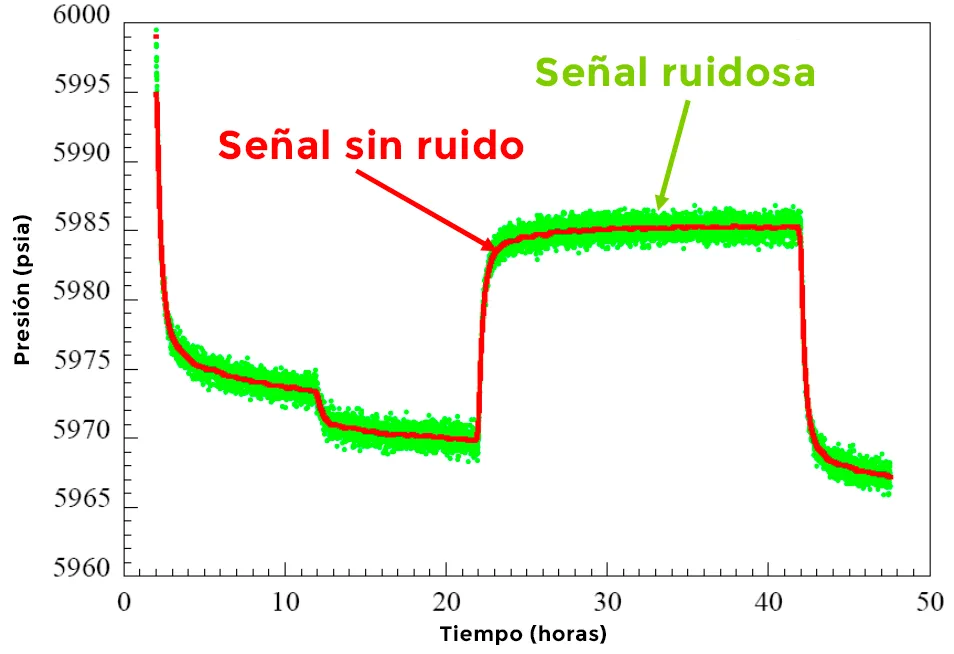
3. Identificación de transitorios: Implica la subdivisión del conjunto de datos en distintos periodos de la variable, como por ejemplo el caudal, estos conjuntos son conocidos como transitorios. Este proceso requiere la identificación de puntos de interrupción, que marcan el inicio y el fin de cada transitorio. La identificación se logra mediante la detección de cambios abruptos en los datos de presión, indicando así variaciones en el caudal del pozo.
4. Reducción de datos: Con el propósito de gestionar la gran cantidad de datos obtenidos por los sensores.
5. Reconstrucción del flujo histórico: Involucra el cálculo de caudales ausentes mediante un análisis de regresión, ya que suele ser imposible obtener un historial completo del caudal3.
6. Filtrado por comportamiento: Se trata de la identificación y exclusión de segmentos de datos que se apartan de la tendencia general de las medidas. Basándose en la inferencia de un modelo de yacimiento apropiado, este proceso utiliza la varianza entre los datos y la respuesta modelada como criterio de selección
7. Interpretación de datos: Para llevar a cabo esta fase final se necesita de la aplicación de una técnica fundamentada en ventanas deslizantes. Esta metodología considera la potencial variación de las propiedades de yacimiento y del fluido durante el proceso de recuperación3. Para finalizar, se realiza un análisis mediante regresión no lineal, para extraer las conclusiones relevantes.
Esta metodología proporciona un enfoque para optimizar el manejo de riesgos industriales al aprovechar datos precisos y contextualizados en la toma de decisiones estratégicas.
Conclusiones
El uso de sensores permanentes en el análisis de riesgos industriales se puede percibir como una estrategia integral para optimizar la seguridad y eficiencia en operaciones industriales. Estos dispositivos no solo posibilitan la monitorización continua de parámetros críticos como presión, temperatura y caudal, sino que también permiten la detección inmediata de anomalías y la evaluación exhaustiva de yacimientos petrolíferos, ideal para la identificación de amenazas presentes en los procesos industriales.
Adicionalmente, su contribución se refleja en la mejora de diferentes aspectos organizacionales, como la gestión de la integridad de revestimientos de pozos, la reducción de costos y la optimización de la producción y rentabilidad. Demostrando que los datos proporcionados son de gran valor para la gestión y optimización operativa.
Cabe destacar que es necesario realizar una correcta implementación y análisis de los datos obtenidos por los sensores permanentes. Dado que una adecuada manipulación de la información conseguida, terminará ofreciendo un enfoque sólido para enfrentar los desafíos de seguridad y eficiencia en entornos industriales.
Referencias
- W. A. Nestlerode. The use of pressure data from permanently installed bottomhole pressure gauges (SPE paper 590). In SPE Rocky Mountain Joint Regional Meeting, Denver, Colorado, USA, 1963.
- Athichanagorn, S., Horne, R. N. y Kikani J. » Processing and Interpretation of Long-term Data from Permanent Downhole Pressure Gauges.» Documento presentado en la Conferencia y Exposición Técnica Anual de la SPE, Houston, Texas, octubre de 1999.
- Thomas, O. (2002). THE DATA AS THE MODEL: INTERPRETING PERMANENT DOWNHOLE GAUGE DATA WITHOUT KNOWING THE RESERVOIR MODEL.