Tabla de Contenidos
- ¿Qué es el proceso de recubrimiento?
- Etapas del proceso de recubrimiento en superficies de metal
- Mantenimiento post-aplicación del recubrimiento
- Tipos de recubrimientos industriales y sus aplicaciones técnicas
- Automatización y robótica en recubrimientos industriales
- Causas comunes de fallas en el proceso de recubrimiento
- Conclusiones
- FAQ (People Also Ask)
- ¿Qué es el proceso de recubrimiento?
- ¿Qué es el DFT en los recubrimientos?
- ¿Qué causa el fallo del recubrimiento?
- ¿Qué recubrimientos resisten la exposición a los rayos UV?
- ¿Qué es el perfil de la superficie en la preparación del recubrimiento?
- ¿En qué industrias se aplican los recubrimientos protectores?
La corrosión y el desgaste representan los principales desafíos para la integridad de la infraestructura industrial; por esa razón, el proceso de recubrimiento es la estrategia técnica de protección más efectiva para los activos metálicos, un procedimiento no es solo ‘pintar’, es la aplicación controlada de materiales que crean una barrera robusta, garantizando la durabilidad y el rendimiento de los activos en los diferentes sectores industriales.
Una correcta preparación de superficies es fundamental para garantizar la adherencia del recubrimiento y prolongar la vida útil del sustrato. A continuación, se describen las etapas clave del proceso, algunas de las tecnologías más recientes y los principales recubrimientos que se aplican a nivel industrial.
¿Qué es el proceso de recubrimiento?
Se define como un conjunto de operaciones que permite aplicar de manera uniforme una barrera protectora sobre superficies metálicas. Su función principal es prevenir el deterioro prematuro del metal por agentes como humedad, salinidad, productos químicos o fricción mecánica. Su garantía depende de una secuencia de cuatro etapas clave donde cada una cumple un propósito específico para garantizar la calidad fina: preparación del sustrato, aplicación, curado y control de calidad final.
Etapas del proceso de recubrimiento en superficies de metal
Preparación de superficies metálicas
Esta es la etapa más crítica del proceso, ya que la adherencia del recubrimiento depende directamente de la limpieza y la rugosidad del sustrato. La selección del método de preparación se rige por normas internacionales (como las de la SSPC, NACE e ISO 8501) y considera el tipo de metal y el recubrimiento a utilizar.
- Limpieza química o con solventes: Utiliza desengrasantes y solventes, según la norma SSPC-SP 1, para eliminar contaminantes como aceites, grasas y suciedad antes de la preparación mecánica.
- Limpieza mecánica: Emplea herramientas manuales (SSPC-SP 2) o eléctricas (SSPC-SP 3) para remover óxido y recubrimientos antiguos en áreas de difícil acceso.
- Chorreado abrasivo (granallado): Proyecta partículas abrasivas a alta velocidad (granalla de acero, arena, escoria). Es el método más eficaz para limpiar a fondo y generar un perfil de anclaje ideal para la adhesión, entre los más aplicados están (SSPC-SP 10, Limpieza a Metal Casi Blanco, o SSPC-SP 5, Limpieza a Metal Blanco); sus variantes modernas incluyen chorreado húmedo para reducir polvo y sistemas de granallado automatizado.
- Limpieza con agua a ultra alta presión (UHP Waterjetting): Utiliza agua a más de 30,000 psi para eliminar contaminantes solubles y recubrimientos viejos sin generar polvo. Las normas SSPC-SP WJ definen grados de limpieza según la presión aplicada.
Una empresa que ha modernizado algunos de estos procesos es RAM-100 del Sureste, que emplea unidades móviles, granallado automatizado y sistemas avanzados para limpieza superficial y aplicación de recubrimientos industriales bajo estándares como ISO 8501 o NACE.
Aplicación de recubrimiento
Una vez preparada la superficie, se aplica el recubrimiento usando la técnica más adecuada según el material y la geometría de la pieza.
- Brocha y rodillo: Usados en retoques, áreas pequeñas o geometrías complejas donde el spray no es viable.
- Pulverización (spray coating): Es el método más común en la industria, con varias tecnologías:
- Airless de alto volumen: Utiliza una bomba de alta presión para aplicar capas uniformes en grandes superficies de forma rápida y eficiente; es ideal para trabajos en campo.
- Equipos de múltiples componentes (plural component): Mezclan resina y endurecedor justo antes de la aplicación, la mejor opción para epóxicos o poliurea con vida útil muy corta.
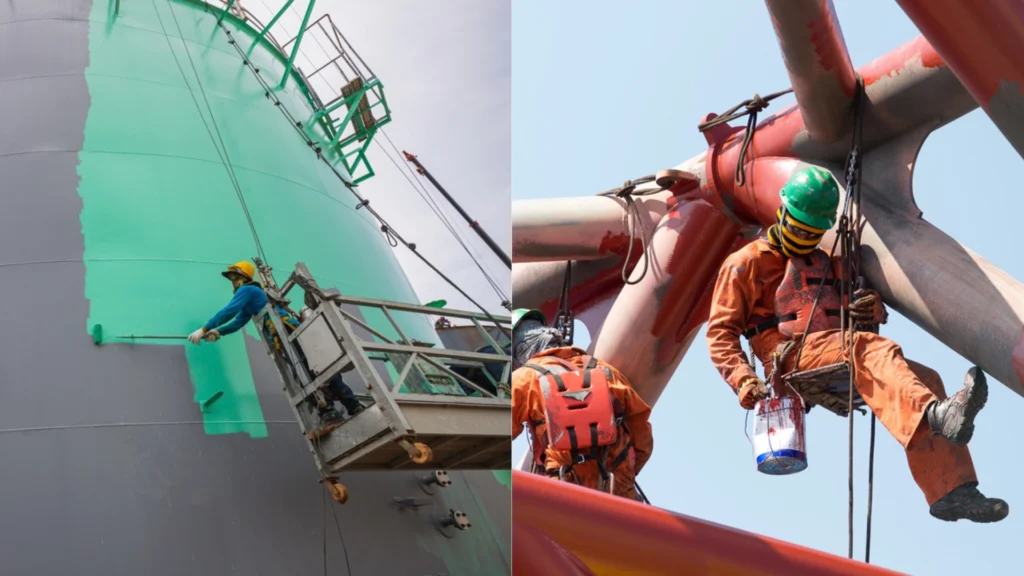
Curado o polimerización
El curado es el proceso por el cual el recubrimiento líquido se transforma en una película sólida y resistente. Los métodos varían según el entorno de aplicación.
- Curado ambiental o a temperatura ambiente: El método más común para recubrimientos aplicados en campo; donde este se cura por la evaporación de solventes o por una reacción química que ocurre a temperatura ambiente. La velocidad de curado puede variar según la temperatura, humedad y tipo de recubrimiento.
- Curado térmico: Típicamente utilizado en entornos de fábrica para polimerizar recubrimientos en polvo o termoestables. La pieza se introduce en un horno para acelerar el proceso.
- Curado por UV o LED: Utiliza luz ultravioleta o LED de alta intensidad para polimerizar recubrimientos especializados; es útil en la fabricación de piezas pequeñas o en reparaciones rápidas.
Inspección final
La inspección es el último paso para garantizar que el recubrimiento cumpla con las especificaciones técnicas. Algunos de los métodos de inspección incluyen:
- Medición de espesor de película seca (DFT): Se utilizan medidores de inducción magnética o tecnología avanzada de Fluorescencia de Rayos X (XRF). Las normas ASTM D1186 y ISO 2808 son referencias comunes.
- Pruebas de adhesión: Evalúan la fuerza del vínculo entre el recubrimiento y el sustrato. Las más comunes son las pruebas de corte en cuadrícula (cross-hatch) bajo la norma (ASTM D3359) o de arrancamiento (pull-off) bajo la norma (ASTM D4541).
- Prueba Holiday: Identifica porosidades o pinholes y otras discontinuidades con equipos de alto y bajo voltaje.
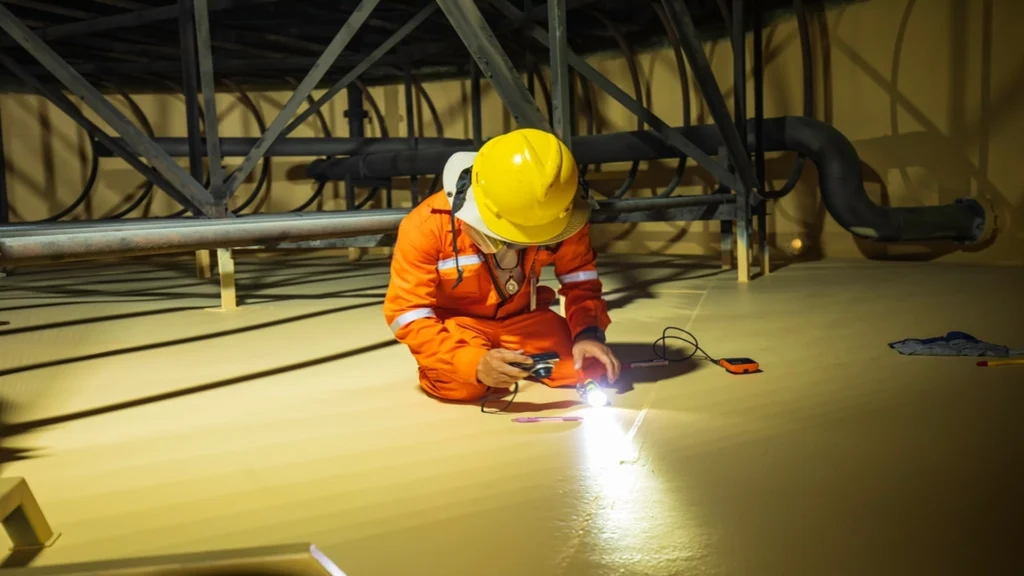
Mantenimiento post-aplicación del recubrimiento
El mantenimiento es una fase importante y proactiva, posterior a la aplicación y curado, diseñada para preservar la integridad del sistema de recubrimiento. A través de inspecciones periódicas y reparaciones puntuales, se identifican y corrigen pequeñas fallas como fisuras, ampollas o desgaste localizado, antes de que progresen y comprometan la protección del sustrato.
Establecer un plan de mantenimiento preventivo, basado en las condiciones operativas del activo y la naturaleza del recubrimiento, es la estrategia más efectiva para maximizar su eficiencia y extender su vida útil, reduciendo significativamente los costos a largo plazo y evitando fallas catastróficas.
Tipos de recubrimientos industriales y sus aplicaciones técnicas
Los recubrimientos se clasifican según su composición química, propiedades protectoras y condiciones de aplicación. La correcta selección del sistema depende del ambiente operativo, del sustrato y de los requisitos de desempeño.
- Recubrimientos epóxicos: Alta resistencia química, buena adherencia y durabilidad; común en interiores, tanques, plantas químicas y plataformas offshore.
- Recubrimientos de poliuretano: Excelente resistencia UV, brillo y acabado estético; se usan como capa final en estructuras expuestas al sol y en aplicaciones arquitectónicas.
- Recubrimientos ricos en zinc (zinc-rich): Ofrecen protección catódica al acero; son recomendados en estructuras metálicas exteriores, puentes, torres de transmisión y estructuras marítimas.
- Recubrimientos cerámicos: Tienen una altísima resistencia a la abrasión, químicos y temperaturas. Usados en la industria minera, papelera y siderúrgica.
- Recubrimientos en polvo: Aplicación seca por pulverización electrostática; estos no contienen solventes, lo que los hace ecológicos: mayormente usados en manufactura de autopartes y electrodomésticos.
- Recubrimientos de conversión química: Como el fosfatado y anodizado, mejoran adherencia de capas posteriores o proporcionan propiedades dieléctricas.
- Recubrimientos inteligentes (smart coatings): Estos recubrimientos incorporan propiedades autodiagnósticas, autocicatrizantes o autolimpiantes, revolucionando la protección. Actualmente en investigación para sectores aeroespaciales y electrónicos, prometen una gestión de la integridad metálica aún más avanzada.
Automatización y robótica en recubrimientos industriales
La integración de la robótica está transformando la industria del recubrimiento, optimizando la preparación de superficies y la aplicación de recubrimientos.
Robots de limpieza y preparación de superficies
La automatización en esta fase asegura resultados consistentes y mejora la seguridad laboral al eliminar la exposición del personal a riesgo.
- Chorreado abrasivo remoto: Estos robots utilizan imanes para adherirse a superficies verticales u horizontales, como tanques de almacenamiento o cascos de barcos. Equipados con boquillas de chorreado abrasivo, se desplazan de forma programada aseguran limpieza uniforme y perfil de anclaje óptimo.
- Limpieza con agua a presión robotizada: Similar a los sistemas de chorreado, estos robots limpian las superficies con chorros de agua a diferentes presiones y son utilizados en entornos sensibles donde la contención de partículas es obligatoria.
Robots de aplicación de recubrimientos industriales
La aplicación de recubrimientos mediante robots está optimizada para la uniformidad y el ahorro de material, superando las adversidades del trabajo manual.
- Uniformidad y repetibilidad: Siguen trayectorias programadas para cada tipo de estructura; estos robots eliminan las variaciones de espesor de película que pueden ocurrir con la aplicación manual, asegurando acabados precisos y duraderos.
- Pulverización de alta eficiencia: Son sistemas que con tecnologías como la pulverización electrostática, donde se cargan eléctricamente las partículas de pintura para mejorar eficiencia de transferencia y reducir desperdicio.
- Seguridad mejorada: Funcionan en cámaras de pintura con altas concentraciones de solventes y partículas, protegiendo a los operarios.
El siguiente video de INSPENET muestra un sistema robótico de VertiDrive, distribuido por BlastOne. Al utilizar un brazo robótico programable para el granallado, esta tecnología minimiza la exposición del personal a entornos peligrosos y asegura un tratamiento superficial uniforme y de alta calidad.

Causas comunes de fallas en el proceso de recubrimiento
A pesar de la tecnología disponible, los recubrimientos industriales pueden fallar si no se controlan adecuadamente ciertas variables durante su aplicación y operación. Algunas causas frecuentes incluyen:
- Mala preparación de la superficie: Un perfil de anclaje inadecuado, contaminantes residuales o humedad pueden afectar drásticamente la adherencia.
- Espesor incorrecto de película seca (DFT): Un DFT inferior al especificado reduce la resistencia a la corrosión; uno excesivo puede generar grietas comprimetiendo la adherencia a largo plazo o que puede provocar un curado incompleto.
- Aplicación inadecuada: Temperatura, humedad relativa y velocidad de aplicación influyen en la correcta formación de la película.
- Curado incompleto: El curado prematuro, incompleto o acelerado artificialmente puede impedir que la matriz polimérica se desarrolle correctamente.
- Condiciones ambientales severas no previstas: Ambientes con salinidad extrema, exposición UV intensa o ciclos térmicos violentos pueden acelerar el deterioro.
- Compatibilidad química deficiente: Al aplicar capas sucesivas sin verificar compatibilidad entre imprimaciones, intermedias y acabados, pueden surgir reacciones negativas.
Conclusiones
El proceso de recubrimiento de superficies metálicas es una estrategia fundamental para preservar la integridad de los activos industriales, que en su mayoría operan en ambientes agresivos y bajo especificaciones técnicas estrictas. Se ha demostrado que es una ciencia que combina preparación meticulosa y aplicación precisa.
La adopción de tecnologías avanzadas, como la robótica en la limpieza y la aplicación, ha mejorado la uniformidad y eficiencia, y también ha elevado los estándares de seguridad. La integración de la tecnología y el control preciso garantizan que los recubrimientos continúen siendo la principal herramienta para la protección de la infraestructura metálica moderna.
FAQ (People Also Ask)
¿Qué es el proceso de recubrimiento?
Es un conjunto de etapas para aplicar un recubrimiento protector a una superficie, incluyendo preparación, aplicación, curado e inspección.
¿Qué es el DFT en los recubrimientos?
Es el espesor de película seca, parámetro crítico para asegurar la protección adecuada del sustrato metálico.
¿Qué causa el fallo del recubrimiento?
Los fallos más comunes incluyen una preparación deficiente de la superficie, una aplicación inadecuada, un curado incompleto y entornos más agresivos de lo previsto.
¿Qué recubrimientos resisten la exposición a los rayos UV?
Los recubrimientos de poliuretano alifático y fluoropolímero ofrecen una alta resistencia a la radiación ultravioleta.
¿Qué es el perfil de la superficie en la preparación del recubrimiento?
Es la rugosidad generada en el sustrato para mejorar la adhesión del recubrimiento, medida en micras.
¿En qué industrias se aplican los recubrimientos protectores?
Sectores como oil u0026amp; gas, marítimo, petroquímica, automotriz, construcción y otras industrias, donde se seleccionan recubrimientos específicos según los requerimientos de resistencia y durabilidad.