Tabla de Contenidos
- ¿Qué es la dezincificación?
- Tipos de dezincificación: uniforme vs localizada
- Relevancia para la detección temprana y el diseño de materiales
- ¿Qué causa la dezincificación del latón?
- Señales y consecuencias de la dezincificación
- Métodos de detección temprana de la dezincificación
- ¿Cómo prevenir la dezincificación del latón ?
- Errores comunes en el diseño o mantenimiento que favorecen la dezincificación
- ¿Cómo revertir o reparar la dezincificación?
- Aplicaciones reales y estudios de caso
- Normativas y estándares internacionales aplicables
- Conclusiones
- Referencias
La corrosión es una preocupación crítica en la durabilidad y confiabilidad de los componentes metálicos, especialmente aquellos expuestos a entornos agresivos. Una forma particularmente insidiosa de corrosión que afecta a las aleaciones cobre-zinc es la dezincificación. Este fenómeno conduce a la degradación prematura del latón, un material ampliamente utilizado en sistemas de fontanería, tuberías industriales, herrajes marinos y diversos accesorios mecánicos.
La dezincificación, un tipo de corrosión galvánica, puede provocar fallas estructurales y funcionales significativas, que a menudo pasan desapercibidas hasta que se produce un daño visible o una fuga. A medida que la infraestructura envejece y las condiciones ambientales se vuelven más exigentes—como la presencia de dióxido de carbono, cloruros o agua blanda—el riesgo de este tipo de corrosión localizada aumenta.
Este artículo explora en profundidad qué es la dezincificación del latón, sus mecanismos subyacentes, las causas y las estrategias para prevenirla, proporcionando conocimientos esenciales para ingenieros, profesionales del mantenimiento y especialistas en materiales que buscan mejorar la vida útil y el rendimiento de los componentes de latón.
¿Qué es la dezincificación?
La dezincificación es una forma de lixiviación selectiva en la cual el zinc se elimina de las aleaciones de latón, dejando una matriz porosa y esponjosa de cobre. Este proceso ocurre cuando el latón se expone a un entorno corrosivo, en particular aquellos con agua ácida ó agua estancada, altas concentraciones de cloruros o presencia de dióxido de carbono.
Quiero resaltar el termino de agua estancada como el agua que no circula, queda retenida en tuberías o equipos y por ende, puede aumentar el tiempo de contacto con superficies metálicas y favorecer ambientes corrosivos (como acumulación de CO₂, cloruros, o caída de pH). Con el tiempo, la pérdida de zinc transforma la microestructura de la aleación, degradando gravemente su resistencia mecánica y apariencia visual.
Desde un punto de vista metalúrgico, la dezincificación es un mecanismo de corrosión por desaleación, en el que el elemento más reactivo (zinc) se disuelve preferentemente. El resultado es una capa debilitada y quebradiza compuesta principalmente de cobre, a menudo con un tono rosado, que es mecánicamente frágil y susceptible a una corrosión adicional.
La respuesta a “¿qué es la dezincificación?” no radica solo en su química, sino en su impacto: compromete la integridad, conductividad y tolerancia a la presión de los componentes de latón. En aplicaciones críticas como válvulas o accesorios de latón en sistemas de plomería, esta corrosión puede provocar fallas repentinas, contaminación del agua o reemplazos costosos.
Prevenir la degradación del latón por dezincificación es, por tanto, esencial en sistemas donde la durabilidad a largo plazo y la resistencia a la corrosión son vitales.
Tipos de dezincificación: uniforme vs localizada
Esta forma de corrosión se produce en aleaciones que contienen un metal menos noble que el otro. En este caso el elemento menos noble se elimina del material mas noble, dejando un material poroso con muy baja resistencia y ductilidad. El ejemplo más común de corrosión selectiva es la dezincificación del latón (Zn-Cu), que se produce por eliminación del zinc de la aleación. Las regiones empobrecidas en Zn presentan un característico color rojizo en contraste con el latón amarillo original.
La dezincificación del latón puede clasificarse en dos tipos principales:
a. Deszincificación uniforme, que se produce en presencia de un alto contenido de Zn y soluciones ácidas. b. Deszincificación localizada que se produce en presencia de un contenido de Zn más bajo y en soluciones neutras, alcalinas y ligeramente ácidas.
En la siguiente imagen se pueden apreciar ambos procesos de corrosion.
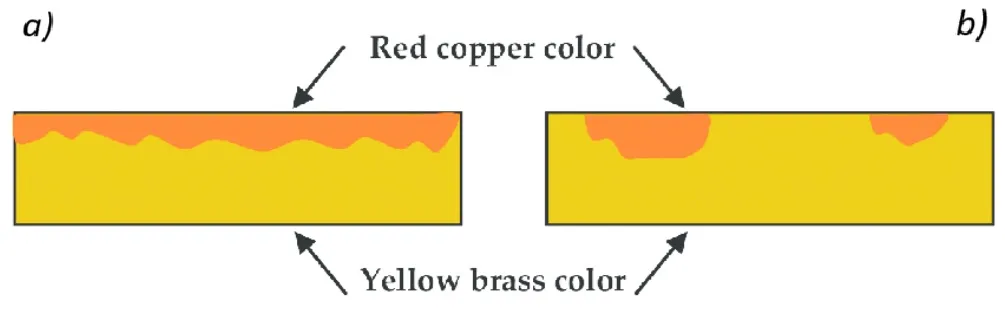
Dezincificación uniforme
Este tipo de ataque se caracteriza por una pérdida gradual y generalizada de zinc sobre grandes áreas de la superficie del latón. Aunque el daño puede parecer superficial, la eliminación progresiva del zinc genera una microestructura debilitada rica en cobre, de textura esponjosa y porosa, lo que compromete la integridad mecánica a mediano o largo plazo.
Características:
- Afecta áreas amplias de manera más o menos homogénea.
- La pérdida de resistencia es progresiva pero menos catastrófica en el corto plazo.
- Frecuentemente asociada a exposición prolongada a agua blanda, levemente ácida o con bajo contenido de cloruros.
Implicación práctica:
Aunque puede pasar desapercibida inicialmente, la dezincificación uniforme reduce la vida útil del componente y puede generar colapsos estructurales si no se inspecciona a tiempo.
Dezincificación localizada (plug-type)
En este caso, el ataque es puntual y severo, formándose cavidades profundas o «enchufes de corrosión » en zonas específicas del componente. Estos parches suelen desprenderse y dejar huecos críticos en la pared del material, lo que incrementa el riesgo de fallas repentinas, como fugas, fracturas o roturas bajo presión.
Características:
- Corrosión concentrada en zonas específicas.
- Daño estructural severo en puntos críticos, incluso si el resto de la pieza parece en buen estado.
- Frecuentemente favorecida por condiciones de agua estancada, altas concentraciones de cloruros o la presencia de dióxido de carbono disuelto.
Implicación práctica:
Este tipo de ataque es particularmente peligroso, ya que puede generar fallas inesperadas y localizadas en válvulas, acoplamientos y tuberías, sobre todo en sistemas de agua caliente o con mal diseño hidráulico.
Condiciones que favorecen cada tipo
Tipo de dezincificación | Condiciones favorecedoras |
Uniforme | Agua blanda, baja acidez, flujo continuo, temperatura moderada |
Localizada | Agua estancada, alta acidez, CO₂ disuelto, cloruros elevados, zonas de bajo flujo |
Relevancia para la detección temprana y el diseño de materiales
Comprender el tipo de dezincificación permite ajustar los métodos de inspección: la uniforme puede requerir medición de espesores o análisis metalográfico por muestreo; la localizada, en cambio, exige técnicas como inspección visual indirecta (videoscopia), radiografía o líquidos penetrantes, que detecten cavidades ocultas.
En cuanto al diseño de materiales, identificar el tipo de ataque más probable permite seleccionar la aleación adecuada (por ejemplo, latón DZR CW602N para condiciones críticas), aplicar revestimientos protectores y establecer protocolos de monitoreo preventivo más precisos.
¿Qué causa la dezincificación del latón?
La dezincificación ocurre debido a un mecanismo de lixiviación selectiva, donde el zinc se disuelve preferentemente del latón al estar expuesto a un ambiente corrosivo. El proceso es electroquímico y se activa cuando los componentes de latón entran en contacto con agua que contiene oxígeno, cloruros, dióxido de carbono (CO₂) o condiciones de bajo pH (ácidas).
El principal impulsor de lo que causa la dezincificación del latón es la diferencia galvánica entre el cobre y el zinc en la aleación. En presencia de electrolitos—como agua blanda, destilada o levemente ácida—los iones de zinc tienden a migrar fuera de la matriz del latón, dejando una capa debilitada rica en cobre.
Los factores ambientales que aceleran la dezincificación incluyen:
- Agua blanda o desmineralizada sin minerales amortiguadores.
- Altas concentraciones de cloruros, comunes en atmósferas marinas.
- CO₂ disuelto, que disminuye el pH y aumenta las tasas de corrosión.
- Malas condiciones de flujo, como agua estancada que se torna ácida en sistemas de plomería.
Ejemplos reales de dezincificación se observan frecuentemente en plomería doméstica, especialmente en viviendas antiguas con accesorios de latón no resistentes a la dezincificación (no-DZR), y en componentes marinos como válvulas y hélices expuestas al agua salada. El resultado no es solo una degradación visual, sino una profunda pérdida de integridad estructural que puede conducir a fallas catastróficas si no se aborda.
La ilustración muestra un tubo de latón (brass alloy) expuesto a un medio acuoso agresivo con cloruros (Cl⁻), dióxido de carbono (CO₂) y pH ácido, los cuales favorecen la lixiviación del zinc (Zn). A medida que los iones de zinc (Zn²⁺) migran hacia el entorno, la estructura del latón se transforma en una matriz porosa rica en cobre, debilitando significativamente el material. La flecha de flujo indica el movimiento del medio corrosivo a través del componente.
Señales y consecuencias de la dezincificación
Identificar la dezincificación a tiempo es clave para prevenir daños graves. Los signos visuales y físicos más comunes incluyen:
- Una decoloración rosada o rojiza en la superficie del latón debido al cobre remanente.
- Textura porosa o esponjosa al inspeccionar o raspar el material.
- Pérdida notable de resistencia, con componentes que se vuelven frágiles y quebradizos.
En sistemas de plomería, estas señales pueden indicar que un accesorio o válvula corre riesgo de fuga o ruptura, especialmente bajo presión. El riesgo se incrementa en circuitos de agua caliente y en secciones estancadas de las tuberías.
Las consecuencias económicas son significativas. La dezincificación no detectada puede causar daños por agua, paradas de sistema, reparaciones costosas o incluso riesgos para la salud y seguridad debido a la contaminación del agua. Para industrias o municipios, esto se traduce en costos de mantenimiento, incumplimiento normativo y preocupaciones de seguridad pública.
Métodos de detección temprana de la dezincificación
La detección temprana de la dezincificación es esencial para prevenir fallas catastróficas, reducir costos de mantenimiento y garantizar la confiabilidad operativa de los sistemas. Debido a que este tipo de corrosión puede progresar de manera silenciosa y afectar internamente la microestructura del latón antes de evidenciarse en la superficie, es necesario aplicar técnicas de inspección específicas, tanto destructivas como no destructivas (NDT).
Inspección visual y evaluación superficial
Aunque limitada, una inspección visual cuidadosa puede revelar signos iniciales como:
- Decoloración rojiza o rosada (indica acumulación de cobre superficial).
- Pérdida de brillo o aspecto mate en zonas normalmente pulidas.
- Presencia de grietas superficiales o desprendimiento de material.
Ventaja: Método rápido y de bajo costo.
Limitación: No detecta daños internos ni zonas críticas ocultas.
Pruebas destructivas y metalografía
En componentes seleccionados o en laboratorio, se puede aplicar:
- Corte transversal del material y análisis bajo microscopio óptico.
- Revelado químico para observar la matriz rica en cobre.
- Identificación de microgrietas, porosidad o zonas empobrecidas en zinc.
Ventaja: Permite confirmar el tipo y la severidad de la dezincificación.
Limitación: No aplicable en servicio. Requiere extraer muestras.
Técnicas no destructivas (NDT)
Ideales para inspecciones en campo o sobre componentes en operación.
a) Medición de espesor por ultrasonido
- Detecta pérdida de material estructural en zonas críticas.
- Útil para comparar áreas sospechosas con secciones de referencia.
b) Radiografía industrial (RT)
- Permite visualizar cavidades internas producidas por dezincificación localizada.
- Requiere acceso y control de seguridad radiológica.
c) Inspección con líquidos penetrantes (PT)
- Ideal para revelar grietas superficiales generadas por pérdida de integridad del latón.
- Complementa inspecciones visuales.
d) Inspección por videoscopia (borescope)
- Se introduce una cámara en el interior de válvulas, tuberías o acoplamientos.
- Permite observar en tiempo real daños internos, zonas erosionadas o coloración anómala.
Técnicas avanzadas de laboratorio
Cuando se requiere un diagnóstico detallado, se pueden aplicar métodos de caracterización a nivel elemental:
- Microscopía electrónica de barrido (SEM): Visualiza la microestructura corroída y la porosidad asociada.
- Espectroscopía por dispersión de energía (EDS o EDX): Confirma la pérdida de zinc y el enriquecimiento de cobre.
- Mapeo elemental: Evalúa la distribución del zinc y otros elementos para cuantificar el nivel de daño.
Estrategia recomendada
Aplicación | Método sugerido |
Inspección preventiva en campo | Visual + ultrasonido + borescope |
Diagnóstico detallado en laboratorio | Corte metalográfico + SEM + EDX |
Evaluación de fallas críticas | Radiografía industrial + análisis metalográfico |
¿Cómo prevenir la dezincificación del latón ?
Comprender cómo prevenir la dezincificación del latón comienza con la ingeniería de materiales. Una de las estrategias más eficaces es el uso de latones resistentes a la dezincificación (DZR), como las aleaciones que cumplen con normas como EN 12165 CW602N o ASTM B887. Estas aleaciones contienen pequeñas cantidades de arsénico, estaño o fósforo, que estabilizan la microestructura y reducen la lixiviación de zinc.
En este video, cortesía de Boshart Industries, se explica de forma sencilla qué es la dezincificación, cómo identificarla y qué materiales como el acero inoxidable o el latón DZR pueden ayudar a prevenirla.
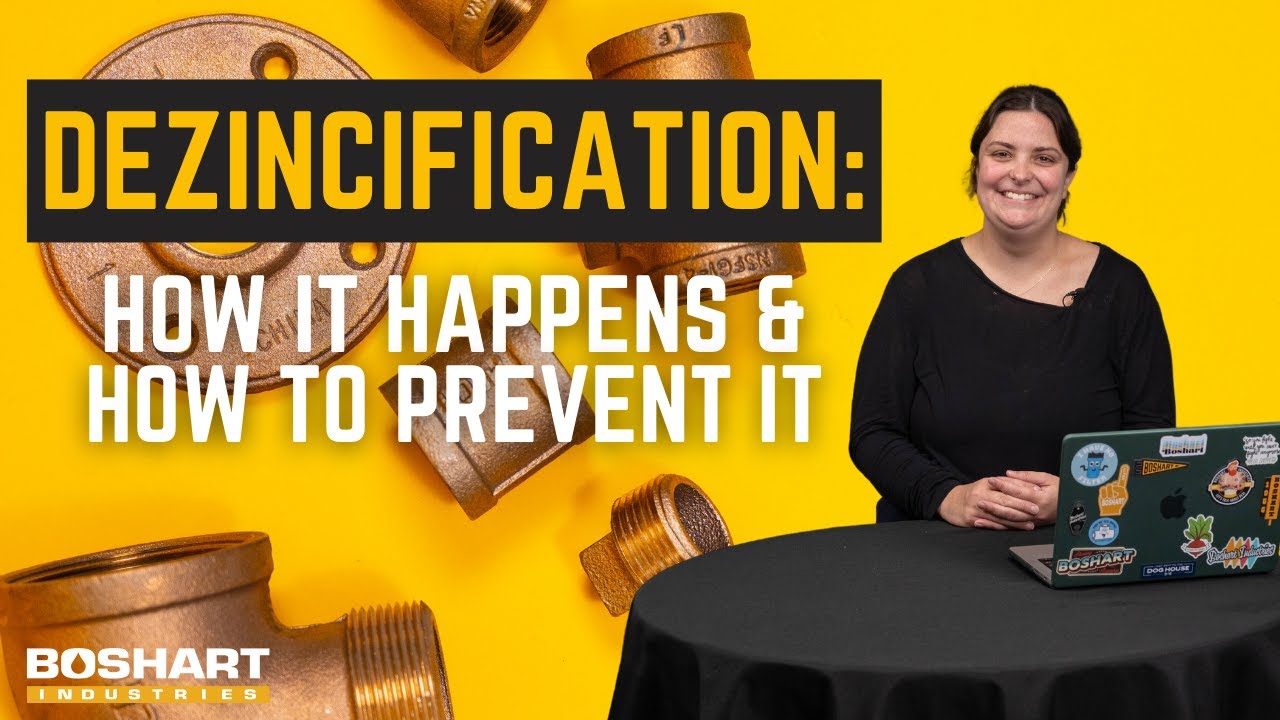
Métodos adicionales de prevención incluyen:
1. Tratamiento de agua y control ambiental
- Neutralizar agua blanda o ácida mediante ajuste de pH o enriquecimiento mineral.
- Reducir las concentraciones de cloruros y CO₂ en los sistemas de agua.
- Garantizar tasas de flujo adecuadas para evitar zonas estancadas.
2. Selección inteligente de materiales
- Evitar el uso de latón estándar en aplicaciones críticas como válvulas marinas, bombas industriales o circuitos de alta temperatura.
- Especificar latón DZR para accesorios en sistemas de agua caliente o áreas propensas a la corrosión.
3. Protección superficial
- Aplicar recubrimientos resistentes a la corrosión como pinturas epóxicas o recubrimientos de poliuretano.
- Usar protección catódica en entornos industriales o marinos a gran escala.
Seleccionar los materiales adecuados e implementar estrategias preventivas puede extender significativamente la vida útil de los componentes de latón, reducir el riesgo de fallas y garantizar la seguridad operativa en entornos corrosivos. El uso de materiales innovadores diseñados específicamente para resistir la lixiviación de zinc y la corrosión galvánica representa un avance clave en la ingeniería de sistemas duraderos
Errores comunes en el diseño o mantenimiento que favorecen la dezincificación
En la práctica industrial y residencial, muchos casos de dezincificación severa no se deben únicamente a condiciones ambientales adversas, sino a decisiones incorrectas en el diseño, selección de materiales o mantenimiento de los sistemas. Comprender estos errores recurrentes es fundamental para prevenir fallas costosas y garantizar la durabilidad de los componentes de latón en servicio.
Seleccionar latón estándar en entornos con agua blanda o clorada
Uno de los errores más frecuentes es utilizar latón estándar (no-DZR) en aplicaciones donde el agua presenta características que favorecen la lixiviación del zinc:
- Agua blanda o desmineralizada: carece de minerales amortiguadores, facilitando ambientes ligeramente ácidos.
- Agua clorada: el cloro y sus derivados aceleran procesos de corrosión localizada.
Consecuencia: El latón convencional es altamente susceptible a la dezincificación en estos entornos, especialmente si está en contacto continuo con agua estancada o caliente.
Recomendación: Especificar latón DZR (Dezincification Resistant Brass) certificado bajo normas como EN 12165 CW602N o ASTM B887 para garantizar resistencia comprobada.
Ignorar la química del agua durante el diseño hidráulico
Muchos sistemas son diseñados sin un análisis previo del agua que circulará por ellos, omitiendo factores como:
- pH
- Alcalinidad
- Cloruros y sulfatos disueltos
- CO₂ libre
Consecuencia: Se subestima el potencial corrosivo del medio, lo que conduce a la selección inadecuada de materiales o al diseño de sistemas sin protección suficiente.
Recomendación: Incluir el análisis químico del agua como parte obligatoria del proceso de diseño. Esta información permite definir la necesidad de tratamientos correctivos, selección de aleaciones resistentes o recubrimientos protectores.
Desconocer los límites de temperatura y presión del material
El latón tiene un rango operativo seguro, pero en muchos casos se emplea en sistemas que:
- Superan los 70–80 °C (temperaturas que aceleran la corrosión y la difusión del zinc).
- Operan bajo presiones elevadas sin considerar la pérdida de espesor por corrosión interna.
Consecuencia: La combinación de calor, presión y corrosión interna por dezincificación puede generar rupturas súbitas, especialmente en válvulas, niples y accesorios soldados o roscados.
Recomendación: Consultar las fichas técnicas del fabricante, verificar curvas de presión-temperatura y evitar el uso de latón estándar en circuitos de agua caliente o vapor.
Ausencia de mantenimiento preventivo en válvulas y tuberías
Muchos sistemas operan durante años sin inspecciones internas, limpieza o pruebas de presión, lo que permite que la dezincificación avance sin ser detectada.
Señales ignoradas frecuentemente:
- Pérdida de presión inexplicada
- Pequeñas fugas intermitentes
- Cambios de color en el agua
Consecuencia: Cuando el problema se identifica, el componente ya ha perdido integridad estructural y requiere reemplazo completo, lo que implica mayores costos y tiempos de inactividad.
Recomendación: Establecer un programa de mantenimiento preventivo que incluya:
- Inspección visual interna con borescope
- Pruebas de presión
- Sustitución periódica de accesorios en zonas críticas
- Registro histórico de materiales, condiciones de agua y vida útil
Error común | Acción recomendada |
Uso de latón estándar en agua blanda/clorada | Usar latón DZR certificado |
Ignorar química del agua | Análisis químico previo al diseño |
Exceder límites operativos | Verificar temperatura/presión de trabajo |
Falta de mantenimiento | Programas periódicos de inspección |
¿Cómo revertir o reparar la dezincificación?
Una pregunta común es cómo revertir la dezincificación del latón , especialmente en aplicaciones domésticas e industriales. Desafortunadamente, la dezincificación no es prácticamente reversible. Una vez que el zinc ha sido lixiviado de la aleación, la estructura rica en cobre resultante es frágil, porosa y está mecánicamente comprometida.
En la mayoría de los casos, el reemplazo del componente afectado es la solución más segura y rentable. Intentar reforzar o recubrir una pieza gravemente dezincificada no es recomendable debido a la pérdida de integridad estructural.
Protocolos de mantenimiento y recomendaciones al consumidor
En aplicaciones industriales, los programas de inspección periódica y mantenimiento preventivo pueden identificar señales tempranas de dezincificación, como decoloración, picaduras superficiales o disminución del rendimiento en sistemas de plomería.
Para los propietarios de viviendas que se preguntan cómo revertir la dezincificación del latón en casa, no existe una solución casera viable una vez que el daño es avanzado. Sin embargo, reemplazar tempranamente con accesorios de latón DZR y controlar la química del agua mediante filtración puede prevenir recurrencias.
El enjuague rutinario de líneas de agua estancadas, el uso de inhibidores de corrosión y el análisis de la calidad del agua son pasos preventivos prácticos. En resumen, el reemplazo proactivo, y no la reparación, sigue siendo el estándar en la industria.
Aplicaciones reales y estudios de caso
La dezincificación ha sido documentada en una variedad de contextos industriales y residenciales. En los sistemas de plomería, se observa con frecuencia en viviendas antiguas con accesorios de latón estándar expuestos a agua blanda o clorada. Las fallas en válvulas y acoplamientos pueden provocar fugas y daños por agua.
En plantas desalinizadoras, el alto contenido de cloruros del agua de mar representa un entorno agresivo. El uso de latón DZR y accesorios recubiertos con polímeros ha incrementado significativamente la longevidad de los equipos y reducido los costos de mantenimiento.
Los sistemas HVAC también enfrentan riesgos de corrosión debido a la condensación, agua estancada y alta humedad. En estos sistemas, se utilizan componentes resistentes a la dezincificación en enfriadores, intercambiadores de calor y conjuntos de válvulas para prevenir fallas mecánicas.
Métodos de prueba y verificación
- El análisis metalográfico revela la estructura característica empobrecida en zinc.
- La microscopía electrónica de barrido (SEM) ofrece imágenes detalladas de la porosidad y microgrietas.
- La espectroscopía de rayos X por dispersión de energía (EDX) confirma la pérdida de zinc a nivel elemental.
Estas herramientas de diagnóstico son fundamentales en el análisis de fallas y para validar la efectividad de materiales resistentes a la corrosión en campo.
Normativas y estándares internacionales aplicables
El cumplimiento con normas técnicas internacionales es un pilar fundamental en la selección, fabricación y aplicación de componentes de latón, especialmente en entornos donde la dezincificación representa un riesgo crítico. Estas normativas garantizan que las aleaciones utilizadas cumplan con requisitos estrictos de composición, desempeño mecánico y resistencia a la corrosión, facilitando decisiones de ingeniería confiables y trazables.
Normas ASTM (American Society for Testing and Materials)
- ASTM B858 – Standard Test Method for Determination of the Resistance of Copper Alloys to Dezincification: Establece el procedimiento para ensayos acelerados de resistencia a la dezincificación. Se utiliza para validar materiales mediante inmersión en soluciones corrosivas controladas.
- ASTM B887 – Standard Specification for Brass, High Strength, Dezincification Resistant (DZR): Define aleaciones de latón formuladas específicamente para resistir la lixiviación del zinc, como aquellas con pequeñas cantidades de arsénico, estaño o fósforo. Contempla aplicaciones en sistemas de agua caliente, válvulas y conexiones críticas.
- ASTM B927 – Standard Specification for Brass Rod, Bar, and Shapes for Forging and Extrusion (DZR): Aplica a materiales trabajados mecánicamente, como barras o formas, utilizados en componentes forjados o extruidos. Incluye criterios de control de calidad y composición para garantizar la resistencia a la corrosión .
Normas EN (Normativa Europea)
- EN 12164 / EN 12165 / EN 12167 / EN 1982: Estas normas cubren diferentes formas de productos de latón (barras, extrusiones, piezas fundidas), incluyendo la aleación CW602N, la más conocida por su resistencia a la dezincificación.
- CW602N: Contiene arsénico como inhibidor de lixiviación, excelente para sistemas de agua potable y ambientes agresivos.
- EN ISO 6509-1 – Determination of dezincification resistance of brass: Establece el método estandarizado para evaluar la resistencia del latón al ataque por dezincificación, basado en pruebas de inmersión y análisis metalográfico posterior.
Conclusiones
La dezincificación del latón representa una amenaza silenciosa pero devastadora para la integridad de componentes en sistemas hidráulicos, marítimos e industriales. Este fenómeno, impulsado por entornos corrosivos y una mala selección de materiales, puede causar fallas mecánicas inesperadas, pérdidas económicas significativas y riesgos para la seguridad.
Si bien la dezincificación no puede revertirse, sí puede prevenirse: el uso de latón resistente a la dezincificación (DZR), el tratamiento adecuado del agua, la protección superficial y el monitoreo constante son prácticas esenciales para extender la vida útil de los sistemas y equipos. Comprender y aplicar estas estrategias no solo mitiga el riesgo, sino que fortalece la confiabilidad operativa en sectores donde cada componente cuenta.
Más allá del desempeño técnico, la prevención de la dezincificación también tiene un impacto positivo en la sostenibilidad. Las fugas y reemplazos frecuentes implican desperdicio de agua, generación de residuos metálicos y mayor consumo energético. Al utilizar materiales DZR y mantener una gestión proactiva del sistema, no solo se preserva la integridad operativa, sino que se contribuye activamente a la eficiencia de recursos, la reducción del impacto ambiental y la prolongación del ciclo de vida de los activos.
En un mundo donde la infraestructura envejece y las condiciones operativas son cada vez más exigentes, prevenir la dezincificación no es una opción: es una necesidad técnica, económica y ambiental.
Referencias
- Dezincification by AMPP. https://www.ampp.org/technical-research/what-is-corrosion/forms-of-corrosion/dezincification?utm_source=chatgpt.com
- Dinnappa, R.K., and S.M. Mayanna. «The Dezincification of Brass and Its Inhibition in Acidic Chloride and Sulphate Solutions.» Corrosion Science 27,4 (1987).
- Dean, J.A. Lange’s Handbook of Chemistry, 14th ed. New York, NY: McGraw-Hill, 1992.
- Wieland Chase Explains Processes Leading to Improved Dezincification-Resistance by Larry Muller, Senior Technical Advisor, Wieland Chase, LLC