Tabla de Contenidos
- Corrosión como fenómeno multivariable y no lineal
- Limitaciones de los métodos tradicionales
- ¿Cómo la inteligencia artificial revoluciona el diagnóstico de corrosión?
- Flujo de trabajo típico de un sistema predictivo en corrosión
- Casos de aplicaciones reales en industria
- Beneficios para la gestión predictiva de activos
- Retos, consideraciones éticas y futuro del ML en corrosión.
- Conclusiones
- Referencias
La acción del medio corrosivo representa uno de los enemigos silenciosos más costosos y persistentes en la industria moderna. Afecta la vida útil de tuberías, tanques de almacenamiento, plataformas offshore, intercambiadores de calor y un gran numero de activos industriales. A pesar de los esfuerzos tradicionales de monitoreo e inspección, muchas fallas estructurales aún ocurren sin previo aviso, generando paradas no programadas, altos costos de reparación y riesgos para la seguridad operativa.
El fenómeno corrosivo es altamente complejo, multivariable y no lineal. Factores como la química del agua, la temperatura, la presión, el pH, la presencia de cloruros y el dióxido de carbono interactúan de formas que los modelos determinísticos convencionales no pueden predecir con precisión1.
En este escenario, la inteligencia artificial (IA) emerge como una herramienta transformadora. A través del aprendizaje automático (machine learning), es posible analizar grandes volúmenes de datos históricos y en tiempo real para detectar patrones ocultos y anticipar el deterioro antes de que ocurra. Esto marca una transición desde una gestión correctiva hacia una gestión predictiva de activos, revolucionando la forma en que se preserva la integridad mecánica en entornos industriales exigentes.
En las siguientes secciones, exploraremos cómo la IA está revolucionando el diagnóstico de corrosión, con casos de uso reales, arquitectura de modelos y comparativas con métodos tradicionales. El futuro del mantenimiento comienza hoy y está impulsado por algoritmos.
Corrosión como fenómeno multivariable y no lineal
La corrosión industrial no es un proceso aislado ni lineal, es el resultado de múltiples variables que interactúan de forma compleja y, a menudo, impredecible. Entre las más influyentes se encuentran:
- Cloruros disueltos (presentes en ambientes marinos o aguas industriales).
- CO₂ libre (que acidifica el medio).
- Temperatura del fluido.
- Humedad relativa del ambiente.
- Velocidad de flujo (o falta de flujo, como en agua estancada),
- pH del entorno.
- Potencial electroquímico de la superficie metálica.
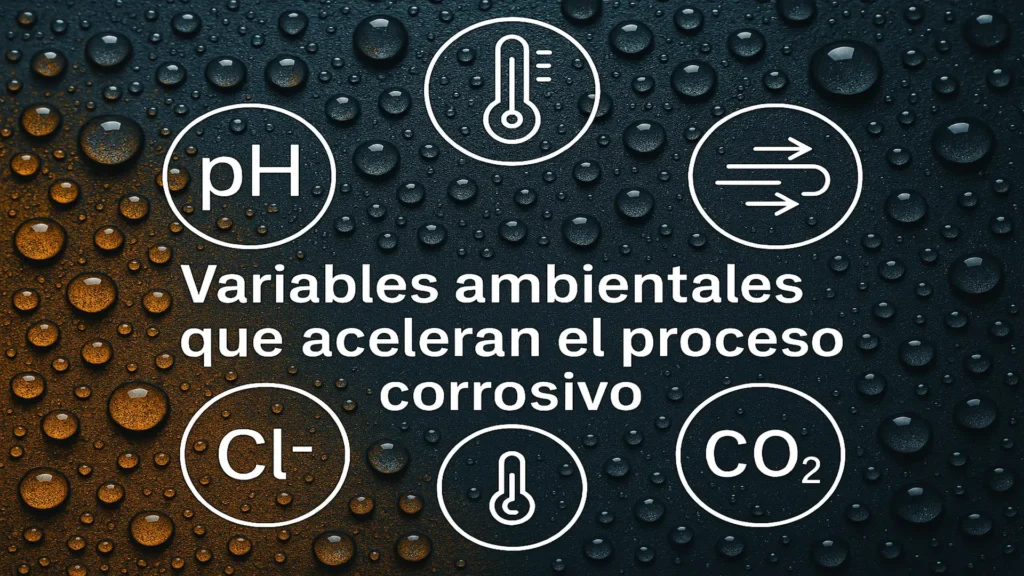
Estas variables varían entre sistemas, con el tiempo, modificando el potencial corrosivo del entorno. Las combinaciones de factores pueden desencadenar mecanismos de corrosión localizada, picaduras, grietas inducidas por esfuerzo y, especialmente, procesos de corrosión galvánica cuando hay materiales diferentes en contacto.
Limitaciones de los métodos tradicionales
Los métodos convencionales de detección de corrosión —como la inspección visual, el ultrasonido (UT), la radiografía (RT) y los análisis metalográficos— han sido pilares durante décadas. Sin embargo, presentan limitaciones clave:
- Son métodos reactivamente costosos, pues dependen de inspecciones periódicas manuales.
- No predicen fallas, solo diagnostican cuando el daño ya está presente.
- Su efectividad depende en gran medida de la experiencia del operador.
- Requieren tiempos de parada y acceso físico al activo.
Además, la mayoria de estos métodos carecen de una visión holística del comportamiento corrosivo en función del tiempo. Aquí es donde las soluciones basadas en machine learning ofrecen un enfoque disruptivo: anticiparse al daño antes de que sea visible.
¿Cómo la inteligencia artificial revoluciona el diagnóstico de corrosión?
El machine learning (ML) permite entrenar algoritmos para identificar patrones ocultos en datos multivariables. En el contexto de la corrosión, estos algoritmos aprenden a partir de datos históricos, inspecciones anteriores, mediciones de sensores IoT, variables de operación y hasta imágenes generadas por videoscopios o drones.
En lugar de depender exclusivamente del juicio humano, los modelos predictivos procesan millones de registros para generar predicciones sobre cuándo, dónde y bajo qué condiciones es más probable que ocurra una falla por corrosión.
Entre los datos que suelen alimentar estos modelos se incluyen:
- Resultados históricos de UT, RT o EDX.
- Registros ambientales (temperatura, humedad, cloruros).
- Fluctuaciones de presión o caudal en líneas de flujo.
- Imágenes térmicas o visuales de equipos.
- Alarmas de sensores de corrosión o pitting.
Este enfoque posibilita la implementación de alertas tempranas ante el deterioro corrosivo, antes de que sea visible.
Tipos de modelos aplicables
Los algoritmos más utilizados para predecir fallas por corrosión incluyen:
- Random Forest: Algoritmo de aprendizaje automático que utiliza múltiples árboles de decisión para analizar conjuntos de datos complejos con variables categóricas y numéricas. Es altamente robusto frente a valores atípicos y ruido.
- Máquinas de Vectores de Soporte (SVM): Modelo de aprendizaje supervisado utilizado para clasificar puntos de datos en categorías. Es especialmente eficaz para detectar y separar estados de deterioro en sistemas de ingeniería.
- Redes Neuronales Artificiales (ANN): Tipo de modelo de aprendizaje profundo inspirado en el cerebro humano, capaz de identificar patrones no lineales complejos en los datos. Ideal para la predicción de fallas y detección de anomalías.
- Deep Learning (CNN y LSTM): las Redes Neuronales Convolucionales (CNN) son ideales para analizar imágenes y detectar patrones visuales complejos, mientras que las Long Short-Term Memory (LSTM) son un tipo de red neuronal recurrente diseñada para trabajar con series temporales y reconocer secuencias de datos en el tiempo, como los registros de sensores.
Estos modelos son aplicables en entornos altamente variables y condiciones de operación cambiantes. A diferencia de las ecuaciones deterministas, los algoritmos de IA evolucionan, mejoran su precisión y se adaptan a nuevas condiciones conforme se alimentan con más datos.
Flujo de trabajo típico de un sistema predictivo en corrosión
Implementar un sistema predictivo de corrosión basado en inteligencia artificial no es solo cuestión de instalar sensores: requiere una arquitectura integral de datos, modelos y validación. El flujo de trabajo típico involucra varias etapas críticas que transforman la información bruta en decisiones operativas accionables.
Recolección de datos
El primer paso es capturar datos relevantes de distintas fuentes:
- Sensores IoT instalados en campo (pH, cloruros, humedad, temperatura, potencial electroquímico).
- Pruebas NDT periódicas (UT, RT, corrientes inducidas).
- Historial de mantenimiento, alarmas, registros de fallas previas.
- Imágenes o videos de inspección visual (borescopia, drones, cámaras térmicas).
Esta fase requiere una infraestructura robusta de adquisición de datos (DAQ systems), redes industriales y conectividad en tiempo real.
Preprocesamiento de datos
Los datos crudos rara vez son utilizables directamente. Es necesario:
- Filtrar valores atípicos o inconsistentes.
- Sincronizar fuentes heterogéneas (tiempo, ubicación).
- Normalizar escalas de medición.
- Aplicar técnicas de feature engineering (derivar variables útiles como tasa de corrosión, tendencia de pérdida de espesor, etc.).
Un buen preprocesamiento mejora la precisión del modelo y reduce errores por ruido.
Selección y entrenamiento del modelo
Dependiendo del tipo de activo, entorno y disponibilidad de datos, se elige el algoritmo más adecuado:
- Random Forest para interpretabilidad y robustez.
- SVM cuando hay pocos datos pero bien definidos.
- Redes neuronales profundas (Deep Learning) para imágenes o series temporales complejas.
Se entrenan los modelos utilizando técnicas como cross-validation y se ajustan hiperparámetros para optimizar métricas clave como exactitud, precisión y sensibilidad.
Evaluación y validación
Se evalúa el desempeño del modelo usando indicadores como:
- Curva ROC-AUC (discriminación).
- Precision/Recall (detección efectiva de fallas).
- Matriz de confusión (errores de clasificación).
Modelos poco precisos se reentrenan o combinan en ensamblajes (ensembles).
Implementación en campo
Finalmente, el modelo se despliega en una plataforma de monitoreo, integrándose con:
- Tableros predictivos (con alertas tempranas).
- Sistemas SCADA o DCS para decisiones en línea.
- Aplicaciones móviles para técnicos de mantenimiento.
Esta integración permite una gestión predictiva de activos, reduciendo costos operativos, previniendo fallas y extendiendo la vida útil de equipos críticos.
Casos de aplicaciones reales en industria
Las aplicaciones de inteligencia artificial para predecir fallas por corrosión ya están transformando diversas industrias. Desde estructuras expuestas a ambientes extremos hasta activos críticos con altos costos de inactividad, la IA permite un monitoreo proactivo con base en datos reales.
Plataformas offshore y plantas químicas
En entornos submarinos, la corrosión por cloruros y microorganismos representa una amenaza constante. Modelos predictivos alimentados con datos de sensores de espesor, temperatura, salinidad y presión permiten anticipar pérdida de material y riesgo de perforación en pilotes y líneas umbilicales.
En plantas químicas, la IA se aplica para detectar corrosión bajo aislamiento (CUI) mediante imágenes térmicas y algoritmos de visión computacional. Esto reduce la necesidad de retirar recubrimientos y mejora la eficiencia operativa.
Uno de los ejemplos más innovadores proviene de AISUS Offshore Ltd, que junto a la Universidad Robert Gordon (Reino Unido), desarrolló una solución robótica potenciada por inteligencia artificial y aprendizaje profundo para inspeccionar estructuras offshore, especialmente en zonas críticas como la splashzone. La herramienta analiza imágenes y datos ultrasónicos recolectados en campo y predice defectos con un 92% de precisión. Este enfoque ha revolucionado su forma de inspeccionar y tomar decisiones técnicas. Ver el caso completo en el siguiente video de North of Scotland KTP Centre:

Inspección de activos offshore mediante IA.
Tuberías y tanques de almacenamiento
Los modelos entrenados con mediciones de ultrasonido más condiciones operativas (flujo, temperatura, pH) permiten mapear zonas críticas en tiempo real. Así, se anticipan fallas antes de las inspecciones programadas, optimizando el mantenimiento basado en riesgo (RBI). Este enfoque se ha implementado exitosamente en sistemas de transporte de hidrocarburos y terminales de almacenamiento, disminuyendo costos y mejorando la seguridad.
Refinerías e instalaciones térmicas
La IA permite combinar datos térmicos y geoquímicos para predecir fenómenos como la sulfidación y la corrosión ácida. En calderas e intercambiadores de calor, los modelos identifican patrones anómalos que indican pérdida acelerada de material.
Estas herramientas han demostrado ser útiles en refinerías donde los ciclos térmicos y los compuestos agresivos aceleran el deterioro de equipos metálicos.
Comparativa: Métodos tradicionales vs. Inteligencia Artificial
Método tradicional | IA predictiva |
Requiere contacto físico | No invasiva, continua |
Inspección por intervalos | Monitoreo en tiempo real |
Depende del operario | Basado en datos objetivos |
Alto costo en campo | Costos iniciales, ROI escalable |
La inspección tradicional de corrosión se basa en técnicas como ultrasonido, radiografía o visual, que requieren contacto físico con el componente, tiempo de parada y personal capacitado. Si bien son confiables, solo ofrecen una fotografía estática del estado del equipo en un momento puntual.
Por contraste, los sistemas de IA permiten una supervisión constante a través de sensores IoT y plataformas digitales. Estos modelos aprenden de los datos operacionales y ambientales para predecir fallas antes de que ocurran. Además, eliminan la subjetividad del operador, estandarizando los criterios de alerta y respuesta. Esto se traduce en una toma de decisiones más rápida, basada en evidencia. La eficiencia y anticipación que ofrece la IA reducen el riesgo de fallas catastróficas, optimizan recursos y mejoran el retorno sobre la inversión en mantenimiento predictivo.
Beneficios para la gestión predictiva de activos
La integración de IA en la predicción de corrosión eleva la gestión de activos a un nuevo nivel. Gracias a su capacidad para procesar grandes volúmenes de datos y detectar patrones complejos, las empresas pueden:
- Mejorar la toma de decisiones estratégicas en mantenimiento, priorizando intervenciones donde el riesgo es mayor.
- Reducir paradas no programadas, al anticipar fallas con base en condiciones reales de operación.
- Optimizar la asignación de recursos, enfocando las inspecciones y reparaciones en puntos críticos previamente identificados.
- Extender la vida útil de los activos, al prevenir deterioro corrosivo severo mediante alertas tempranas.
Esta transformación digital permite transitar de un enfoque correctivo a uno predictivo y basado en datos, alineado con los principios de la industria 4.0.
Retos, consideraciones éticas y futuro del ML en corrosión.
Pese a sus múltiples beneficios, la adopción de inteligencia artificial en el monitoreo de corrosión conlleva desafíos importantes:
- Calidad y volumen de los datos: Los modelos necesitan grandes cantidades de datos confiables para funcionar correctamente. La mala calibración o el ruido pueden afectar su precisión.
- Sesgos en los modelos: Un modelo entrenado en un entorno puede no generalizar bien en otros. Se requieren bases de datos representativas y diversidad de escenarios.
- Falta de estándares técnicos: La ausencia de normas internacionales unificadas para la validación de modelos genera dudas en sectores regulados.
- Talento híbrido: La implementación efectiva exige profesionales con conocimientos tanto en ciencia de datos como en ingeniería de corrosión.
El futuro apunta hacia modelos de autoaprendizaje continuo, combinados con sensores inteligentes y plataformas cloud, que integren mantenimiento, control de procesos y análisis predictivo.
En este nuevo paradigma, la corrosión dejará de ser una amenaza silenciosa para convertirse en una variable predecible, controlable y optimizable.
Conclusiones
La corrosión continúa siendo uno de los desafíos más complejos en la gestión de activos industriales, especialmente por su carácter multivariable, no lineal y difícil de predecir mediante métodos convencionales. En este contexto, el uso de inteligencia artificial y machine learning no solo representa una ventaja tecnológica, sino un cambio estratégico en la forma de abordar la integridad mecánica. Estos modelos permiten anticipar fallas, optimizar recursos y extender la vida útil de los equipos críticos, desde tuberías hasta plataformas offshore.
Adoptar una cultura de mantenimiento predictivo es clave para reducir paradas no programadas y aumentar la seguridad operacional. Esto requiere romper los silos tradicionales entre áreas: los especialistas en corrosión, ingenieros de datos y equipos de IT deben colaborar para crear soluciones integradas, robustas y escalables.
El futuro de la integridad mecánica dependerá de la capacidad de las organizaciones para aprovechar estas herramientas disruptivas, combinando experiencia técnica con analítica avanzada. En este camino, plataformas como Inspenet juegan un rol fundamental al ofrecer contenidos especializados, espacios de capacitación y difusión de las últimas tendencias en inteligencia artificial aplicada al mantenimiento y la gestión de activos.
El momento de evolucionar hacia la predicción inteligente es ahora.
Referencias
1.Dong, Z., Ding, L., Meng, Z. et al. Machine learning-based corrosion rate prediction of steel embedded in soil. Sci Rep 14, 18194 (2024). https://doi.org/10.1038/s41598-024-68562-w