Tabla de Contenidos
- ¿Qué es una localización de monitoreo de condiciones?
- Tipos de monitoreo: Monitoreo continuo vs. monitoreo periódico
- Beneficios del monitoreo de condiciones para prevenir fallas
- ¿Cómo seleccionar puntos para el monitoreo de la condición en tuberías de proceso?
- Clases de servicio de tuberías
- Criterios para la asignación de CMLs
- Corrosión Bajo Aislamiento Térmico (CUI)
- Métodos aplicados para el monitoreo de condiciones
- Técnicas de monitoreo de corrosión directas e intrusivas
- Estrategias avanzadas para el monitoreo de la corrosión
- Conclusión
- Referencias
La corrosión es una amenaza importante para la integridad y el rendimiento de los sistemas de tuberías en diversas industrias. Con el tiempo, puede ocasionar fallas costosas, riesgos de seguridad e interrupciones operativas. El monitoreo de condiciones es fundamental y desempeña un rol en la detección de la corrosión en sus primeras etapas y prevenir fallas. Un aspecto crucial de este enfoque es la selección estratégica de las ubicaciones de monitoreo de condiciones (CMLs, por sus siglas en inglés) dentro del sistema de tuberías.
En este artículo se plantean las estrategias para seleccionar los CMLs, los factores clave que influyen en su colocación, los ensayos no destructivos y las técnicas avanzadas para un monitoreo efectivo de la corrosión en tuberías de proceso, basados principalmente en la información provista por el código de inspección de tuberías API 570.
¿Qué es una localización de monitoreo de condiciones?
Definición y objetivos del monitoreo de condiciones
Consiste en la evaluación sistemática del estado físico de los sistemas de tuberías o recipientes a presión a lo largo del tiempo. Su objetivo principal es detectar la degradación, en particular por la corrosión, antes de que alcance un nivel crítico que pueda resultar en fugas, rupturas u otras fallas. El monitoreo ayuda a garantizar la operación segura y eficiente de los sistemas de tuberías al proporcionar datos que pueden ser utilizados para programar el mantenimiento y evitar paradas no programadas.
Mientras que la inspección aleatoria proporcionaría información sobre la condición actual, la inspección repetida en las CML permite recopilar datos sobre el cambio en la condición e, idealmente, también sobre la tasa de ese cambio1.
Ejemplos de diferentes condiciones que deben monitorearse en los CMLs incluyen el espesor de la pared, el agrietamiento por tensión, CUI y ataque de hidrógeno a alta temperatura.
Definición localización de monitoreo de condiciones (CML)
Según el API 570 un CML se define como: “Un área designada en los sistemas de tuberías donde se realizan exámenes periódicos para evaluar y monitorear directamente la condición del sistema de tuberías utilizando una variedad de métodos y técnicas de examen basados en la susceptibilidad del mecanismo de daño2.”
De lo anterior, la selección de la ubicación de estas áreas es una actividad crítica, pues estas zonas son representativas de todo el sistema de tubería donde una degradación del material puede ocurrir. Ejemplos de diferentes condiciones que deben monitorearse en los CMLs incluyen el espesor de la pared, el agrietamiento por tensión, CUI y ataque de hidrógeno a alta temperatura.
Tipos de monitoreo: Monitoreo continuo vs. monitoreo periódico
El monitoreo de condiciones puede dividirse en dos categorías principales:
- Monitoreo continuo: Implica el uso de sensores y sistemas automatizados para proporcionar datos en tiempo real sobre el estado del sistema de tuberías. El monitoreo continuo es beneficioso para detectar cambios repentinos o desarrollos agresivos de corrosión en áreas de alto riesgo, permitiendo tomar acciones inmediatas en cuanto al conocimiento de las causas y la normalización de las condiciones. Este tipo de seguimiento recurre a sistemas de monitoreo instalados permanentemente, tales como transductores de ultrasonido, anillos de transductores de ondas guiadas, cámaras termográficas, entre otros, los cuales transmiten información sobre la condición de la tubería de forma continua. En la figura 1 se muestra un ejemplo de sensores ultrasónicos que miden continuamente el espesor de la tubería y remotamente se reciben los datos de espesor mediante transmisión inalámbrica.
- Monitoreo periódico: Consiste en inspecciones y evaluaciones programadas utilizando técnicas como la prueba ultrasónica o la radiografía. Es menos costoso, pero puede no detectar cambios rápidos en las tasas de corrosión entre inspecciones.
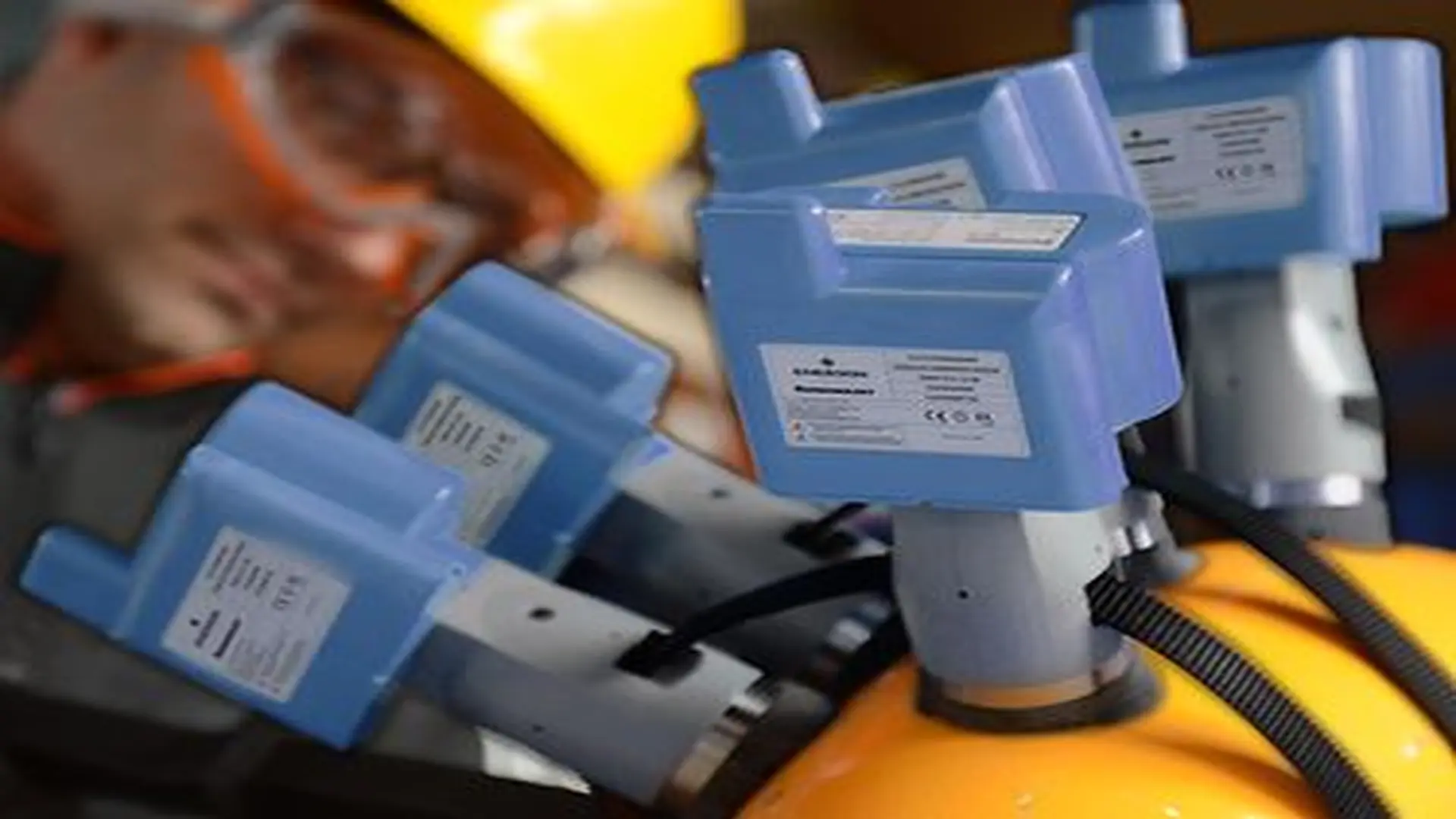
Beneficios del monitoreo de condiciones para prevenir fallas
El principal beneficio del monitoreo de condiciones es la capacidad de predecir fallas antes de que ocurran, a través de un enfoque proactivo que permita una planificación acertada para el mantenimiento y reparaciones oportunas, reduciendo la probabilidad de eventos catastróficos. Además, el monitoreo de condiciones ayuda a extender la vida útil de los sistemas de tuberías y mejora la eficiencia operativa general.
¿Cómo seleccionar puntos para el monitoreo de la condición en tuberías de proceso?
La asignación del CML debe basarse en el mecanismo de daño específico que potencialmente puede desarrollarse en la tubería. Documentos como el API 574 y el API 571 sirven de guía para pronosticar el mecanismo de daño. Un CML corresponde a un “lugar de monitoreo de condición” el cual es un área de la tubería como, por ejemplo, una sección del mismo, un codo u otro accesorio, donde se pueden realizar múltiples mediciones. Soldaduras también pueden ser designadas como CMLs si el mecanismo de daño potencial a desarrollarse es, por ejemplo, agrietamiento bajo tensiones.
El CML no debe confundirse con “puntos de examen”, los cuales son lugares específicos donde se toman lecturas individuales que corresponden a pequeños puntos para realizar, por ejemplo, mediciones de espesores por ultrasonido, los cuales deben estar bien identificados con el objeto de realizar siempre estas mediciones en los mismos sitios, esto con el objeto de medir confiablemente las tasas de cambio de condición (espesor del tubo).
Clases de servicio de tuberías
Previo a la definición de las ubicaciones para el monitoreo de condiciones, las tuberías de proceso deben ser clasificadas en función del grado de las consecuencias potenciales en caso de fallar, excepto las tuberías que hayan sido planificadas en base a la metodología RBI. En función de las consecuencias potenciales y según lo establecido en API 570, las clases de servicio de las tuberías son:
- Clase 1: Representan los servicios con el mayor potencial para resultar en una emergencia inmediata si ocurriera una fuga están en la tubería. Ejemplos de servicios de tuberías dentro de esta clase son:
- Servicios inflamables que pueden autorrefrigerarse y provocar fracturas frágiles.
- Servicios presurizados que pueden vaporizarse rápidamente durante la liberación, creando vapores que pueden acumularse y formar una mezcla explosiva, como corrientes de C2, C3 y C4.
- Sulfuro de hidrógeno (más del 3 % en peso) en corriente gaseosa.
- Cloruro de hidrógeno anhidro.
- Ácido HF (por ejemplo, en unidades de alquilación de HF, como se analiza en API 751, etc.).
- Tuberías sobre agua o adyacentes a ella y tuberías sobre vías públicas.
- Clase 2: Los servicios no incluidos en otras clases están en la Clase 2. Esta clasificación incluye la mayoría de las tuberías de proceso unitario y tuberías externas seleccionadas2.
- Clase 3: Son servicios inflamables pero que no se vaporizan significativamente cuando tienen fugas, es decir, por debajo del punto de inflamación, o inflamables, pero se encuentran en áreas remotas y operan por debajo del punto de ebullición.
- Clase 4: Son servicios esencialmente no inflamables y no tóxicos, al igual que la mayoría de los servicios utilitarios sin impacto ambiental o a la seguridad.
Agregar más CML en ubicaciones apropiadas a tuberías de mayores consecuencias sujetas a tasas de corrosión más altas o corrosión localizada y monitorear esas CML con mayor frecuencia puede reducir la probabilidad de eventos de altas consecuencias3.
Criterios para la asignación de CMLs
Para decidir la ubicación, así como el tipo, número de las CMLs, se debe tomar en cuenta el histórico de los resultados de inspecciones previas, los patrones típicos de corrosión y daño que se esperan en la tubería, y las posibles consecuencias en caso de ocurrencia de una pérdida de contención.
En situaciones donde el servicio produce un tipo de corrosión uniforme, como es el caso de corrosión por sulfuros, la cantidad de CML necesarias para monitorear un circuito será menor que las necesarias para monitorear circuitos sujetos a pérdidas de metal más localizadas. Este escenario requiere de una mayor atención debido a la aceleración del daño, para lo cual es necesario de técnicas de ensayos no destructivos (END) apropiadas, que permitan generar un mapeo de corrosión que asegure la identificación y dimensionamiento de picaduras.
En tuberías donde puede ocurrir estancamiento de agua, un programa de inspección podría enfatizar los puntos bajos para monitorear la corrosión por dióxido de carbono (CO₂), la corrosión debajo del depósito o la corrosión influenciada microbiológicamente (MIC)1. Cuando las velocidades de los fluidos y/o el contenido de sólidos hacen que la erosión sea la amenaza más probable a la integridad, los lugares de cambio de velocidad, como los codos, proporcionarían los datos de inspección más útiles.
Los CML deben distribuirse por el sistema de tuberías para proporcionar una cobertura de monitoreo adecuada de todo tipo de componentes y accesorios. Las mediciones de espesor en CML tienen como objetivo establecer tasas de corrosión generales y localizadas en diferentes secciones de los circuitos de tuberías2.
En cualquier caso, todas estas decisiones deben ser consultadas con el especialista en corrosión.
Corrosión Bajo Aislamiento Térmico (CUI)
En la selección de las CMLs para detección y evaluación de CUI, deben considerarse ciertos aspectos que pudiesen indicar el desarrollo de este mecanismo de daño, entre los cuales se tienen.
- Condición visual de la cubierta exterior y del aislamiento, manchas de óxido, crecimiento biológico, revestimiento impermeable, abultado, abollado o perforado.
- Evidencia de fuga de fluido (por ejemplo, goteos o vapores).
- Evidencia de áreas de aislamiento húmedo.
- Puntos bajos de líneas caídas.
- Fondo del tubo vertical.
- Proximidad a equipos que podrían aumentar la humedad local (por ejemplo, torres de enfriamiento).
- Área donde los regímenes de temperatura entran y salen del rango de temperatura susceptible al CUI.
- Componentes de tuberías (por ejemplo, niples, boquillas, soportes y patas muertas) que forman parte del sistema de tuberías pero que penetran el aislamiento o pueden pasar al rango CUI.
Puntos de mezcla: Áreas de especial interés son los puntos de mezcla, los cuales son ubicaciones en los sistemas de tuberías donde se encuentran dos o más corrientes diferentes. La diferencia en composición, temperatura o cualquier otro parámetro en las corrientes encontradas, pueden contribuir al deterioro, corrosión acelerada o localizada y/o fatiga térmica durante condiciones de operación normales o anormales.
Puntos de inyección: Los puntos de inyección son lugares designados donde los operadores pueden inyectar productos químicos en una corriente de proceso para prevenir o mitigar la corrosión o el agrietamiento. Los puntos de inyección pueden estar sujetos a daños acelerados y/o localizados debido a condiciones de funcionamiento normales y anormales.
Métodos aplicados para el monitoreo de condiciones
Los métodos de Ensayos No Destructivos (NDT, por sus siglas en inglés), se utilizan comúnmente para evaluar el estado de los sistemas de tuberías sin causar daño, la elección del método depende principalmente del tipo de corrosión. A continuación, se exponen algunos de importante consideración:
Ultrasonido (UT): Este método es efectivo para detectar adelgazamiento causado por corrosión uniforme. Estas mediciones se realizan en los “puntos de examen” ya definidos en la sección o accesorios de la tubería para el seguimiento de la pérdida de espesor.
UT es apropiado también para la detección de grietas en soldaduras. Técnicas de pulso eco, o más avanzadas como el Ensayo de Ultrasonido por Arreglo de Fases (PAUT) o Tiempo de Vuelo de la Onda Difractada (TOFD), son apropiadas para este propósito. TOFD es más apropiado para hacer un seguimiento a la evolución de la grieta cuando se apliquen metodologías como Aptitud Para el Servicio (FFS).
Mapeos de Corrosión con PAUT: Es apropiado para la detección y evaluación de zonas con corrosión localizada, al proveer imágenes cuantificables tanto de la sección transversal de la tubería (B-Scan) como una vista de planta del mismo (C-Scan). En la figura 2 se muestra un ejemplo de mapeo de corrosión por PAUT.
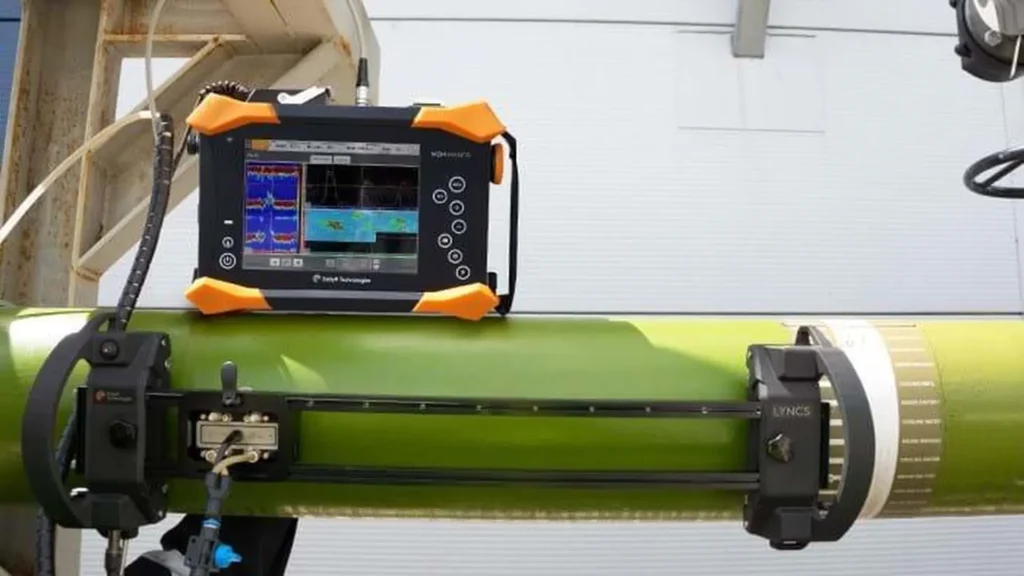
Radiografía Industrial (RT): Puede usarse para identificar picaduras y corrosión localizada, es ideal en tuberías aisladas para inspecciones CUI (Radiografía tangencial para la evaluación de picaduras de la pared exterior aisladas), siendo la técnica de Radiografía Digital (DR) especial para esta última condición. RT también puede usarse para la detección de grietas gestadas en soldaduras.
Corrientes Eddy (ECT): Esta técnica dentro del método de ensayo electromagnético aplicada en materiales no ferromagnéticos, es efectiva para detección y evaluación defectos superficiales o cercanos a la superficie, y agrietamientos en soldaduras. En espesores relativamente bajos, la detección incluye aquellas discontinuidades dentro del volumen y cercanos a la superficie interna de la pieza de ensayo.
Matriz de Corrientes Eddy Pulsadas (PECA): Esta variante avanzada de la técnica de corrientes Eddy (ECT), y evolución de las corrientes Eddy Pulsadas (PEC), es adecuada l para identificar zonas con corrosión bajo aislamiento térmico (CUI), con una visualización en escala de colores de la superficie debajo de esta (C-Scan), dando una estimación cercana del espesor remanente. Una vez detectado la zona corroída, puede requerirse remover el aislamiento para una evaluación más detallada de la corrosión externa de la tubería con pit-gage, método láser 3D, o medición de espesores con UT. En la figura 3 se muestra un ejemplo de aplicación de PECA.
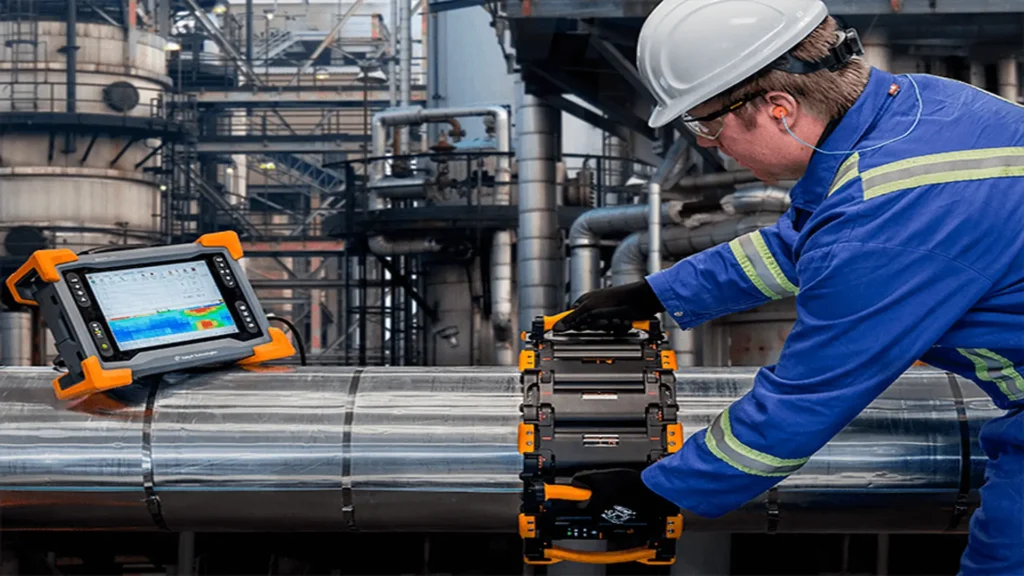
Ondas Guiadas (GWT): El ensayo de ondas guiadas es utilizado para la detección de cambios en el área de la sección transversal indicativos de pérdida de metal siendo ideal para CUI y tramos de tubería de difícil acceso como es el caso de secciones debajo de puentes o tuberías aéreas como por ejemplo líneas de cabecera en topes de destilación. A través de técnicas más avanzadas como Ondas Guiadas de Corto Alcance (SRGWT) y uso de Transductores Acústicos Electromagnéticos (EMAT), puede cuantificarse el grado de corrosión (pérdida de espesor), siendo ideal para aplicaciones como la evaluación de la Corrosión Bajo Soportes de Tubería (CUPS).
Termografía infrarroja (IRT): Ideal para el seguimiento de temperatura en ciertos sistemas de tubería, donde un aumento en el valor de la temperatura de operación pueda promover algún mecanismo de corrosión. La termografía infrarroja también permite ubicar zonas con posible acumulación de humedad en el aislamiento térmico externo de la tubería al detectar temperaturas más bajas, lo que ayuda a definir CMLs para evaluaciones CUI.
Técnicas de monitoreo de corrosión directas e intrusivas
Técnicas de monitoreo de la corrosión directas e intrusivas o en contacto con el fluido, a través de medios físicos como los cupones de prueba o pérdida de masa y resistencia eléctrica, o a través de medios electroquímicos (electrodos) tales como resistencia a la polarización lineal (servicio de agua y gas + agua) y ruido electroquímico, son muy útiles para el monitoreo de la corrosión.
A través del uso de cupones de prueba puede determinarse, aparte de la velocidad de la corrosión, el mecanismo de daño que está afectando a la tubería. Técnicas como la resistencia a la polarización lineal tienen la capacidad de medir la velocidad de corrosión en el instante en que se realiza la corrosión.
Otros ensayos como el de Líquidos Penetrantes (PT) y Partículas Magnéticas (MT), también pueden ser utilizados para el monitoreo de condiciones, sin embargo, quedan limitadas a la detección de fallas gestadas en el servicio que ya han avanzado a través del material de la tubería, por lo que no son efectivas para la detección temprana de estas discontinuidades.
Estrategias avanzadas para el monitoreo de la corrosión
Tecnologías de monitoreo basadas en IoT (Internet de las Cosas)
La integración de esta tecnología permite la recopilación continua de datos de sensores permanentes ubicados en las CMLs. Estos sensores fijos, tales como transductores ultrasónicos para medición de espesores por UT y anillos transductores para GWUT, transmiten datos de forma inalámbrica y continua, lo que permite un análisis en tiempo real y el monitoreo remoto de la corrosión. Los sistemas basados en IoT pueden detectar anomalías tempranas, activando alertas para que los equipos de mantenimiento actúen antes de que ocurra una falla.
Uso de Inteligencia Artificial para el análisis predictivo de la corrosión
La inteligencia artificial (IA) puede procesar grandes cantidades de datos generados por los sensores IoT para predecir tendencias futuras de corrosión. Los algoritmos de aprendizaje automático analizan datos históricos de corrosión, condiciones operativas y factores ambientales para identificar patrones y hacer predicciones sobre cuándo y dónde es probable que ocurra corrosión. Esta capacidad predictiva permite a los operadores programar el mantenimiento de manera más efectiva y reducir el riesgo de fallas inesperadas.
En el siguiente video se muestran las ventajas del sistema de monitoreo de instalación permanente gPIMS; el cual, es un sensor GWT que se instala de forma permanente en la tubería. Cortesía de: GGUL – Guided Ultrasonics Ltd.
Sensores avanzados para la detección de corrosión
El desarrollo de sensores avanzados, como sensores electroquímicos y de fibra óptica, ha mejorado la precisión y confiabilidad en la detección de la corrosión. Estos sensores pueden proporcionar datos en tiempo real sobre factores como el pH, la humedad y la temperatura, que influyen en las tasas de corrosión. Los sensores de fibra óptica, en particular, son altamente sensibles y pueden detectar cambios mínimos en el entorno que pueden señalar el inicio de la corrosión.
Conclusión
El monitoreo efectivo de la corrosión en los sistemas de tuberías de proceso requiere un enfoque estratégico en la selección de ubicaciones de monitoreo de condiciones. Al centrarse en áreas de alto riesgo, utilizar tecnologías de monitoreo avanzadas e implementar mejores prácticas a través de capacitacion en corrosion, las organizaciones pueden reducir significativamente el riesgo de fallas relacionadas con la corrosión. Aunque existen desafíos, los beneficios a largo plazo del monitoreo continuo superan con creces los costos, convirtiéndolo en un componente crítico de las estrategias modernas de gestión de activos.
Referencias
- VIKING ENGINEERING. Choosing & Using Condition Monitoring Locations (CMLs); Consultado el 01 de Octubre de 2024. https://www.gate.energy/the-brainery/choosing-amp-using-condition-monitoring-locations-cmls
- AMERICAN PETROLEUM INSTITUTE. API 570, Piping Inspection Code: In-service Inspection, Rating, Repair, and Alteration of Piping Systems; Consultado el 02 de Octubre de 2024.
- AMERICAN PETROLEUM INSTITUTE. API 574, Inspection Practices for Piping System Components; Consultado el 03 de Octubre de 2024.