El Mantenimiento Centrado en Confiabilidad (RCM por sus siglas en inglés) es una metodología ampliamente reconocida y de uso extendido para elaborar planes de mantenimiento de equipos industriales en asegurar las funciones del equipo para la satisfacción del usuario o propietario.
El RCM asegura un programa efectivo de mantenimiento que se centra en que la confiabilidad original inherente al equipo se mantiene como un proceso utilizado para determinar qué se debe hacer para asegurar que cualquier activo continúe, haciendo lo que sus usuarios quieren que realice dentro de sus límites operacionales.
En este contexto, a continuación, se expone el caso de adquisición de un compresor de gas húmedo para la unidad de Craqueo Catalítico (FCC) de una refinería petrolera.
Caso de éxito en la aplicación del Mantenimiento Centrado en Confiabilidad
El compresor adquirido, luego de un largo proceso de licitación que garantizara la calidad al mejor precio, una vez en planta es instalado siguiendo rigurosamente todas las normas y directrices establecidas. Cada paso fue supervisado por personal de operaciones y mantenimiento con capacitación adecuada, evaluándose aspectos de criticidad del equipo, asegurando que cada componente se ensamblara de manera precisa, con el objetivo de alcanzar un rendimiento óptimo y sostenible; lo cual, sumado a su diseño robusto, garantizarán la confiabilidad de este equipo de altísima criticidad para la planta.
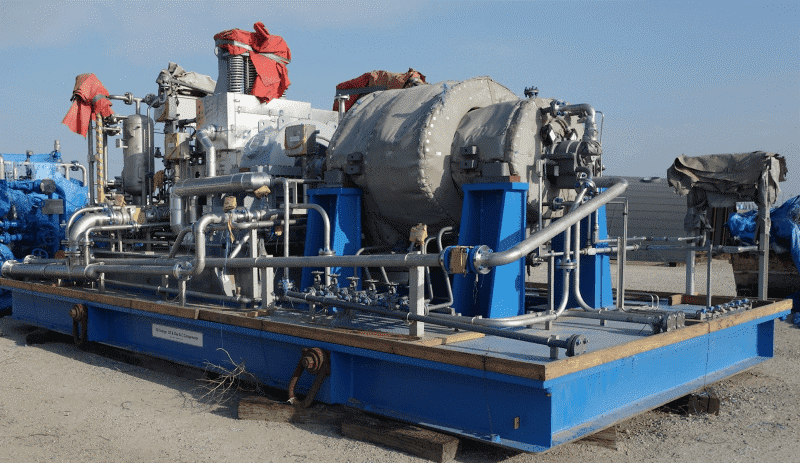
Durante la revisión de los manuales de mantenimiento con el propósito de planificar futuras intervenciones en este equipo, que operará de manera continua durante los 4 años de la corrida de la planta, se descubrió que las tareas de mantenimiento preventivo, deben iniciarse a los 6 meses con la revisión de cojinetes, seguidas por actividades más invasivas que requieren detener el equipo al año de operación.
Esta información llevó, incluso a los expertos más experimentados en estos equipos, a cuestionarse si el equipo, fabricado por uno de los fabricantes más reconocidos a nivel mundial, sería capaz de mantener su rendimiento durante toda la corrida de 4 años.
Por suerte, la respuesta a esta interrogante fue afirmativa. Existen numerosas plantas de Craqueo Catalítico (FCC) que emplean el mismo modelo y fabricante, lo cual ha sido corroborado a través de referencias recopiladas desde las fases iniciales de licitación.
Entonces, ¿por qué los manuales no vienen adaptados para la corrida de 4 años? La razón es que el fabricante proporciona únicamente un manual estándar y espera que el usuario, al igual que la mayoría, lo ajuste según su entorno operativo específico.
Bien, ¿cómo se lleva a cabo esa adecuación al contexto real de operación de este equipo?
Aquí surgen interrogantes acerca de las posibles alternativas para lograrlo.
- ¿Saltándose las actividades invasivas de 6, 12, 18, 36 meses y llevando todo a 48 meses?
- ¿Repensar todo el asunto de mantenimiento, incluyendo actividades que compensen las que no podrán realizarse?
Esta organización actuó acertadamente, siguiendo el enfoque adoptado por las principales compañías líderes a nivel global. Reunió a un equipo de expertos provenientes de diversas áreas, como operaciones, mantenimiento en todas sus especialidades, ingeniería, equipos dinámicos, seguridad y medio ambiente. Se les encomendó la tarea de desarrollar un plan de mantenimiento óptimo que asegurara la confiabilidad y disponibilidad óptima de este compresor.
Hoy día, y desde ya unos años atrás, la metodología más adecuada y por suerte seleccionada para esta misión, es el RCM o MCC: Mantenimiento Centrado en Confiabilidad.
El proceso es muy laborioso y toma mucho tiempo. Por esta razón, la mayoría de las ocasiones solo alcanza a aplicarse en los equipos altamente críticos. Fueron 2-3 meses, reuniéndose 2-3 veces por semana, acompañados de un asesor y una metodología adecuada, pero con un resultado ampliamente satisfactorio, que podría resumirse en:
- Logro de un plan de mantenimiento óptimo, consensuado con todo el equipo y donde cada uno expresó estar de acuerdo con todas las actividades listadas y sus frecuencias.
- Reforzado el trabajo en equipo: ahora se dispone de un equipo de personas comprometidas, que se apoyan unos con otros, donde es muy visible la sinergia y la empatía.
- Durante el proceso se resolvieron algunos aspectos del día a día de operación del equipo, como problemas de comunicación, comprensión de procesos y procedimientos e inclusive se resolvieron algunos aspectos de diseño.
- Todo el personal de mantenimiento ahora conoce los aspectos más importantes de los procesos operativos del compresor y sus equipos auxiliares, lo que les permitirá prestarle un mejor servicio y atención.
- El personal de operaciones ahora tiene mayor comprensión sobre aspectos de mantenimiento, que antes desconocía y limitaba en su interacción con el personal de las distintas especialidades.
- Todas las acciones de los departamentos de Mantenimiento y Operaciones tienen total trazabilidad, priorización y justificación.
La experiencia resultó totalmente positiva. En esa refinería hoy nadie cuestionaría la gran cantidad de horas hombre consumidas por este proyecto. La refinería continuó aplicando exitosamente el RCM al resto de sus equipos críticos. Inclusive aplicó RCM en equipos de mediana criticidad, aprovechando el trabajo adelantado (plantillas) para los de alta criticidad.
Referencias
Fuente propia.
Sobre el autor:
Emilio Trejo Petit, Ingeniero mecánico con especialización en Confiabilidad de Sistemas Industriales. Cuenta con 17 años de experiencia en la industria petrolera venezolana y más de 15 años en el área de consultoría y cursos en Análisis Causas Raíz, Mantenimiento Centrado en Confiabilidad, Ing. de Confiabilidad, en las que ha dictado cursos a más de 2000 personas y participado en más de 100 proyectos en Venezuela, México, Colombia, Perú, Ecuador, en las principales empresas petroleras de la región y en empresas como la de cemento, alimentos, automotriz, entre otras.