Los equipos de proceso como intercambiadores de calor, torres, tambores, hornos y calderas de las plantas de refinación típicamente se vuelven menos eficientes con el paso del tiempo, porque durante el periodo operacional se van depositando incrustaciones en el interior de los mismos, ocasionando una disminución de la eficiencia operativa por debajo a su valor de diseño y comprometiendo la calidad de los procesos; es por eso, que la limpieza de equipos de proceso es clave para una mayor productividad.
El óptimo funcionamiento de los equipos estáticos de proceso en la gestión productiva de una refinería, es fundamental ya que afecta directamente su capacidad para operar de manera segura, eficiente y sostenible. La limpieza periódica de los equipos es una necesidad para restaurar y mantener la operatividad de los sistemas en los procesos de refinación.
Adicionalmente la limpieza también es un requisito previo e indispensable para realizar inspecciones y trabajos de mantenimiento. En las siguientes secciones, abordaremos la importancia de los equipos de proceso, causas de ensuciamiento, tipos de limpieza de equipos de proceso y las tecnologías de limpieza aplicadas.
Principales equipos de proceso y su importancia
Los equipos de refinería se utilizan indefinidamente en los procesos para convertir el petróleo crudo en productos útiles como: gasolina, combustible diésel, lubricantes, gas licuado de petróleo y otros derivados. Los principales equipos estáticos que conforman los sistemas en una refinería incluyen intercambiadores de calor, torres/columnas, tambores/separadores, filtros, hornos, calderas entre otros.
En las plantas de refinación cada uno de estos equipos influyen directamente en la eficiencia operacional de los procesos. Inicialmente los hornos tienen la función de suministrar calor con una alta eficiencia energética a diversas corrientes del proceso, estos calientan el crudo antes de su entrada a las unidades de destilación para facilitar las reacciones químicas durante la conversión; los intercambiadores de calor transfieren calor entre fluidos, ya sea para calentar o enfriar corrientes de proceso donde los controles de las temperaturas deben ser precisos.
Por su parte, en las torres de destilación ocurre el fraccionamiento de los componentes del petróleo crudo y otras mezclas de hidrocarburo basándose en sus diferentes puntos de ebullición, esto ocurre mediante procesos de vaporización y condensación controlados, donde los componentes más volátiles se separan de los menos volátiles, con el fin de obtener una variedad de derivados; los tambores almacenan y separan líquidos y gases en diferentes etapas para procesamiento posterior, mientras que las calderas generan vapor a alta presión y temperatura para varios procesos, y la generación de energía. Así mismo existen otros equipos importantes como los filtros, reactores, tambores de coque y tanques de almacenamiento.
Causas de ensuciamiento más comunes
La suciedad en las refinerías de petróleo tiende a ser más compleja en comparación con otras instalaciones de procesamiento, principalmente debido al uso intensivo de aceros al carbón. Estos materiales son protegidos contra la corrosión mediante la formación de películas protectoras formadas bajo ciertas condiciones de presión y temperatura; sin embargo, durante la operación normal o adversa, estas capas pueden desprenderse, y formar depósitos o incrustaciones en los sistemas operativos.
Las causas de ensuciamiento relacionada a los procesos de refinación comúnmente provienen de uno o más factores, tales como: Productos de reacción y corrosión, compuestos de hidrocarburos, polímeros orgánicos, residuos de coque y materia de carbono, sales inorgánicas, incrustaciones, aditivos de proceso, sedimentos o residuos sueltos. A continuación, se describen algunos equipos o partes de equipos donde se puedan encontrar estos tipos de suciedad:
El ensuciamiento producido por la corrosión se encuentra en casi todas las zonas de alta temperatura incluyendo tubos de intercambiadores, líneas de transferencia, parte inferior de las torres destiladoras; y generalmente contienen sulfuro de hierro y cloruros. Mientras que, en las secciones de baja temperatura como los topes de las torres de destilación y equipos de condensación, se presenta una mezcla de sulfuros de hierro.
Los productos de reacción pueden ensuciar los equipos por diversas razones. Por ejemplo, vapores de azufre producidos por sulfuro de hidrógeno provenientes de plantas de azufre con elevadas temperaturas, depositan una capa de azufre que se solidifica. Los residuos sueltos usualmente se encuentran en la forma de catalizadores finos, trozos de recubrimientos de sprays, fragmentos provenientes de los revestimientos orgánicos, secciones corroídas de interiores de recipientes o interiores de bombas.
Los compuestos de hidrocarburos los conforman residuos oleosos, lodos y residuos viscosos; estos suelen ser los principales constituyentes de la suciedad en tanques de almacenamiento y tambores de separadores. Los residuos de coque y la materia de carbono se producen por la degradación térmica de diversos hidrocarburos; comúnmente se depositan en los tubos de intercambiadores y secciones inferiores de torres destiladoras.
Los polímeros orgánicos causan ensuciamiento en los tubos de los intercambiadores de precalentamiento de las unidades de destilación de crudo y en unidades de hidrotratamiento de nafta; también contribuyen con el ensuciamiento de los tubos de calentadores a fuego directo. Los polímeros orgánicos disminuyen la transferencia de calor en el equipo afectado y actúan como aglutinantes para productos de corrosión y depósitos de sal.
Las incrustaciones de depósitos provenientes de los procesos son originadas por la inyección de agua para lavado, el vapor de proceso, o las fugas de agua de los sistemas de refrigeración. En los equipos de las destiladoras de crudo, la desalinización tiende a ocasionar deposición de incrustaciones en intercambiadores de precalentamiento y en tubos de calentador de crudo. Los depósitos de sales inorgánicas que están relacionadas al proceso se originan con ciertos productos de reacción.
Los inhibidores de corrosión, aditivos o neutralizadores, son reconocidos como contaminantes de equipo de proceso en áreas cercanas a su punto de inyección. Por ejemplo, el ensuciamiento ocurre cuando el inhibidor sin diluir es inyectado en una línea de vapor sobrecalentado, o en una línea de reflujo y termina depositado en la parte superior de una torre destiladora. Respecto a los sedimentos, estos entran a las unidades destiladoras de petróleo crudo y contribuye al ensuciamiento de tubos de intercambiadores de precalentamiento y recipientes para desalinización.
¿Por qué es importante la limpieza de equipos de proceso?
Durante las operaciones la mayoría de los equipos de proceso se ensucian por diferentes causas, por lo que la limpieza de los equipos de procesos es importante porque garantiza la eficiencia operativa, la seguridad, la calidad del producto y el cumplimiento normativo en las operaciones industriales. Los depósitos y las incrustaciones acumuladas durante el funcionamiento son inevitables, es por eso que los equipos de proceso de una refinería requieren limpiarse periódicamente como parte de los programas de mantenimiento y en ocasiones por emergencias operacionales.
La limpieza de equipos de proceso radica en restaurar su capacidad mediante la remoción de residuos acumulados o incrustaciones adheridas que comprometen la transferencia de calor, obstruyen el fluido, bloqueen los sistemas, generen corrosión, minimicen la eficiencia operativa, disminuyen la calidad de los productos terminados o aumentan el riesgo de accidentes. Adicionalmente, este practica es obligatoria para realizar las inspecciones que determinan la integridad mecánica de los mismo.
El ensuciamiento o depósitos de incrustaciones puede ocasionar problemas de transferencia de calor, como por ejemplo el ensuciamiento de los tubos de la zona de convección de los hornos para precalentamiento de crudos, como se aprecia en la figura 1, puede ocasionar sobrecalentamiento significativo del proceso1.
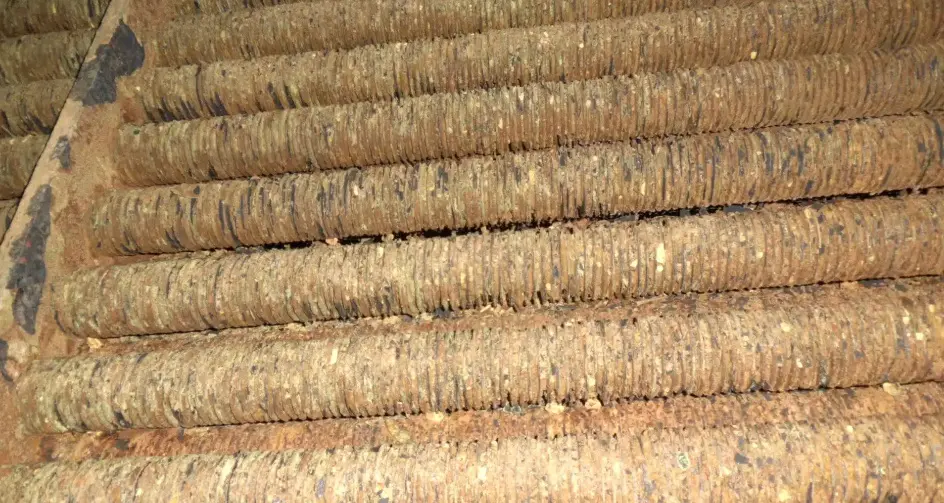
Por consiguiente, la limpieza periódica de equipos de proceso es solo una de muchas operaciones necesarias de mantenimiento que deben ser planeadas y llevadas a cabo en intervalos programados; para obtener un mejor rendimiento del proceso y optimizar del consumo energético.
Limpieza de equipos para inspección
Los equipos de proceso son inundados con vapor y lavados con agua antes de abrirse a la atmósfera. El aire en el vapor o el agua de lavado explica la presencia de diversos depósitos en la parte interna de los mismos, es por eso que la limpieza de equipos de proceso para fines de inspección y mantenimiento es necesaria para la entrada segura del personal.
Estas son actividades que deben realizarse bajo procedimientos aprobados que aborden la remoción de sedimentos, neutralización, dilución y eliminación de químicos peligrosos, así como la ventilación de vapores tóxicos hacia medios de contención adecuados.
Limpiar los equipos de proceso para realizar tareas de inspección y aplicación de Ensayos No Destructivos (END), asegura una evaluación precisa de su condición y funcionamiento. Se requieren eliminar los residuos que pueden ocultar defectos como grietas, corrosión o desgaste, permitiendo una inspección detallada y previniendo fallas futuras. Además, facilita el mantenimiento, mejora la seguridad operacional y prolonga la vida útil del equipo.
Tipos de limpieza de equipos
Los diversos equipos de refinería requieren de métodos específicos de limpieza. Estos métodos, están adaptados a las necesidades y tipos de depósitos a remover en los equipos. Entre los tipos de limpieza de equipos más comunes se encuentran:
Limpieza con agua a alta presión (hidroblasting): La fuerza y el flujo se refiere a la presión y la cantidad de agua que se necesita para eliminar los depósitos solidos e incrustaciones que perjudican el equipo; el material a remover determinará qué herramienta se debe utilizar con este tipo de limpieza. Este método es ampliamente utilizado por su eficiencia, y es probablemente el medio más eficaz para eliminar residuos de coque.
En este contexto, a continuación, se presenta un video que muestra cómo llevar a cabo la limpieza de intercambiadores de calor utilizando sistemas de chorro de alta presión, cortesía de la empresa Falch.
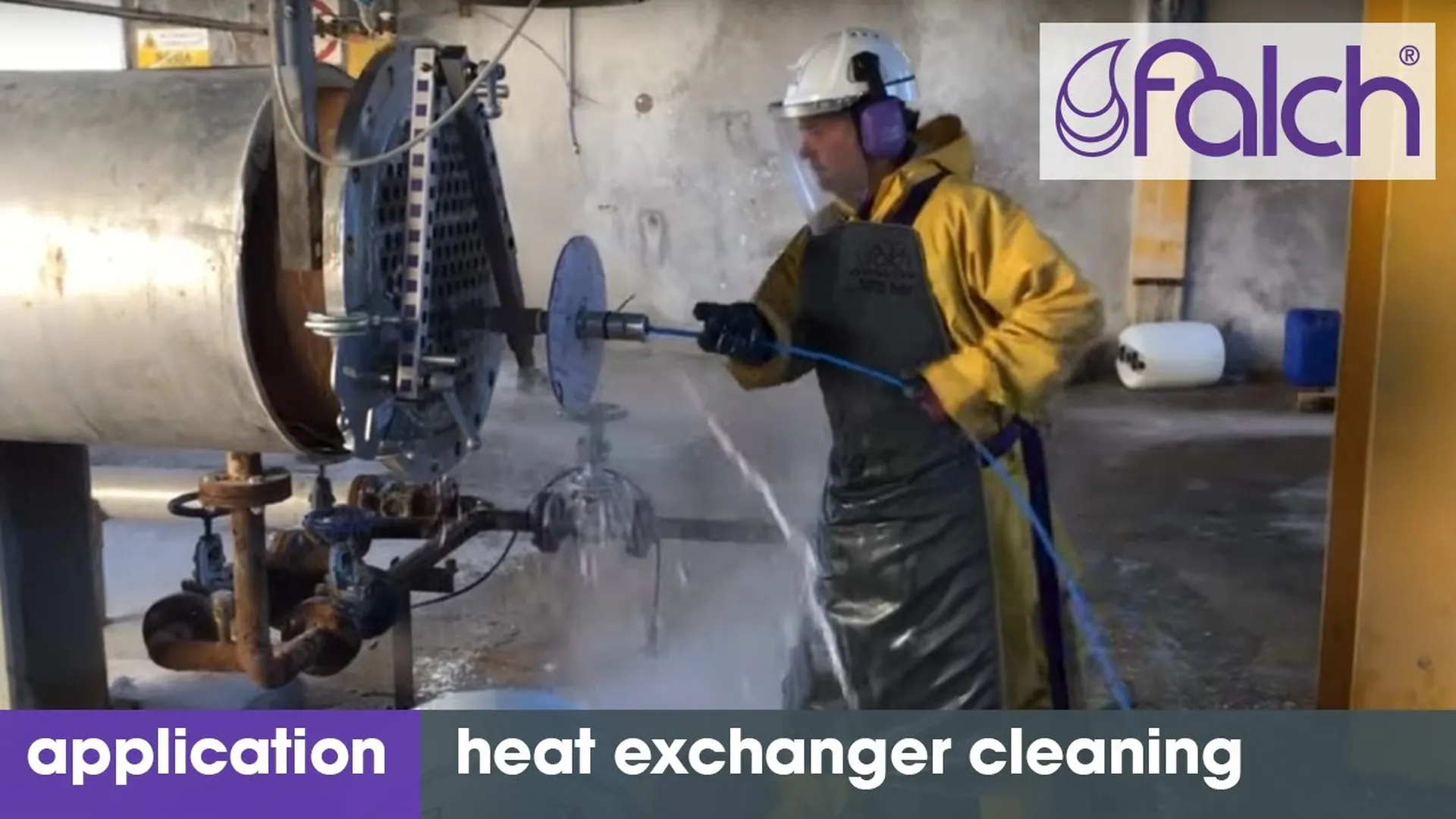
Limpieza profesional de intercambiadores de calor con sistemas de chorro de alta presión.
Limpieza química: Se utilizan productos químicos especializados para descomponer y eliminar depósitos y partículas orgánicas e inorgánicas que se acumulan con el tiempo en la superficie interna de los equipos, en la mayoría de los casos se aplica en intercambiadores de calor, calderas, recipientes a presión. Este tipo de limpieza requiere de equipos especializados y los productos químicos que se utilizan suelen ser peligrosos y corrosivos, y requieren el cumplimiento estricto de los protocolos y normas de seguridad.
Limpieza con vapor: Mediante esta limpieza se aplica vapor a alta temperatura para disolver y eliminar depósitos grasosos y aceitosos, este método es eficaz para una limpieza y desinfección profundas, lo que lo convierte en la opción principal para ciertos tipos de equipos de refinería. También se utiliza vapor a limpiar recipientes contaminados por sustancias orgánicas mediante la aplicación de disolventes en fase vapor.
Limpieza por inmersión: Consiste en sumergir completamente los componentes o partes de un equipo en un baño químico o solución de limpieza. Es efectiva para eliminar residuos, depósitos de coque, incrustaciones y otros de contaminantes. La solución utilizada varía dependiendo del tipo de suciedad y del material del equipo, incluye soluciones alcalinas, ácidas, solventes o detergentes especializados. La inmersión permite una limpieza profunda y uniforme de superficies complejas y de difícil acceso.
Limpieza con aire: Implica el uso de aire comprimido para eliminar partículas sueltas y polvo de las superficies del equipo, es un paso preliminar en varios procedimientos de limpieza, preparando el equipo para métodos de limpieza más intensivos. También es utilizada en los los colectores industriales, para la limpieza en la caja de filtros, evitando así la saturación de los mismos.
Limpieza mecánica: Utilizada para elimina partículas sólidas, incrustaciones duras, residuos y otros tipos de contaminación física que requieren métodos de limpieza donde se aplique fuerza física durante el proceso. Como es el caso del pigging mecánico donde se utiliza una herramienta llamada pigs para remover y eliminar los depósitos de coque y carbón del interior de las tuberías.
Limpiezas especiales: La limpieza especial abarca técnicas como limpieza ultrasónica, criogénicas y de espuma. Estos métodos requieren conocimientos y equipos especializados, pero ofrecen soluciones de limpieza específicas. En la figura 2, se muestra la aplicación de uno de estos tipos de limpieza para tubos de intercambiadores de calor.
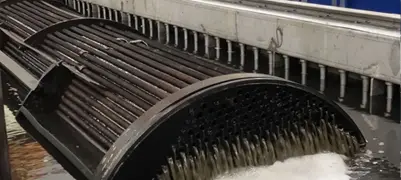
Muchas operaciones de limpieza de equipos de proceso, involucra la combinación de dos o más tipos de limpieza de equipos para obtener el resultado requerido; como en los casos de los hornos donde se aplica una mezcla de aire-vapor a alta temperatura para descarboniazar los ductos y tubos, mediante este proceso se remueven los depósitos de coque y carboncillo del área interna de las tuberías.
Implementar productos y prácticas adecuadas durante este proceso, cumpliendo con las especificaciones operacionales y los procesamientos predeterminados, garantiza la efectividad de la limpieza para los objetivos específicos establecidos.
Tecnologías de limpieza
Para la limpieza de la sección de convección de calentadores de combustión fue desarrolla una tecnología robótica por la empresa Tube Tech3, para lograr una limpieza donde estos equipos alcancen su máximo rendimiento. Por su configuración, estos equipos son difíciles de limpiar, ya que la mayoría de los métodos tradicionales de limpieza no alcanzan el área total a limpiar. Acceder a limpiar lo profundo y entre los bancos de filas de tubos aletados no se lograba como hasta ahora.
Esta tecnología de limpieza con robots, puede limpiar a profundidad entre filas de tubos de convección con disposición cuadrada y triangular, obteniendo un alto nivel de limpieza y en tiempo mejorados. Este tipo de tecnologías de limpieza robótica reemplazan las técnicas tradicionales de limpieza que incluyen: limpieza química, lavado a presión de agua, chorro abrasivo y hielo seco, debido a que puede eliminar depósitos extremadamente duros en lo profundo de cada fila de tubos y también proporcionar informes de inspección antes, durante y después de la limpieza3.
A continuación, se presenta un video sobre la tecnología de limpieza con robots, cortesía de Tube Tech International.
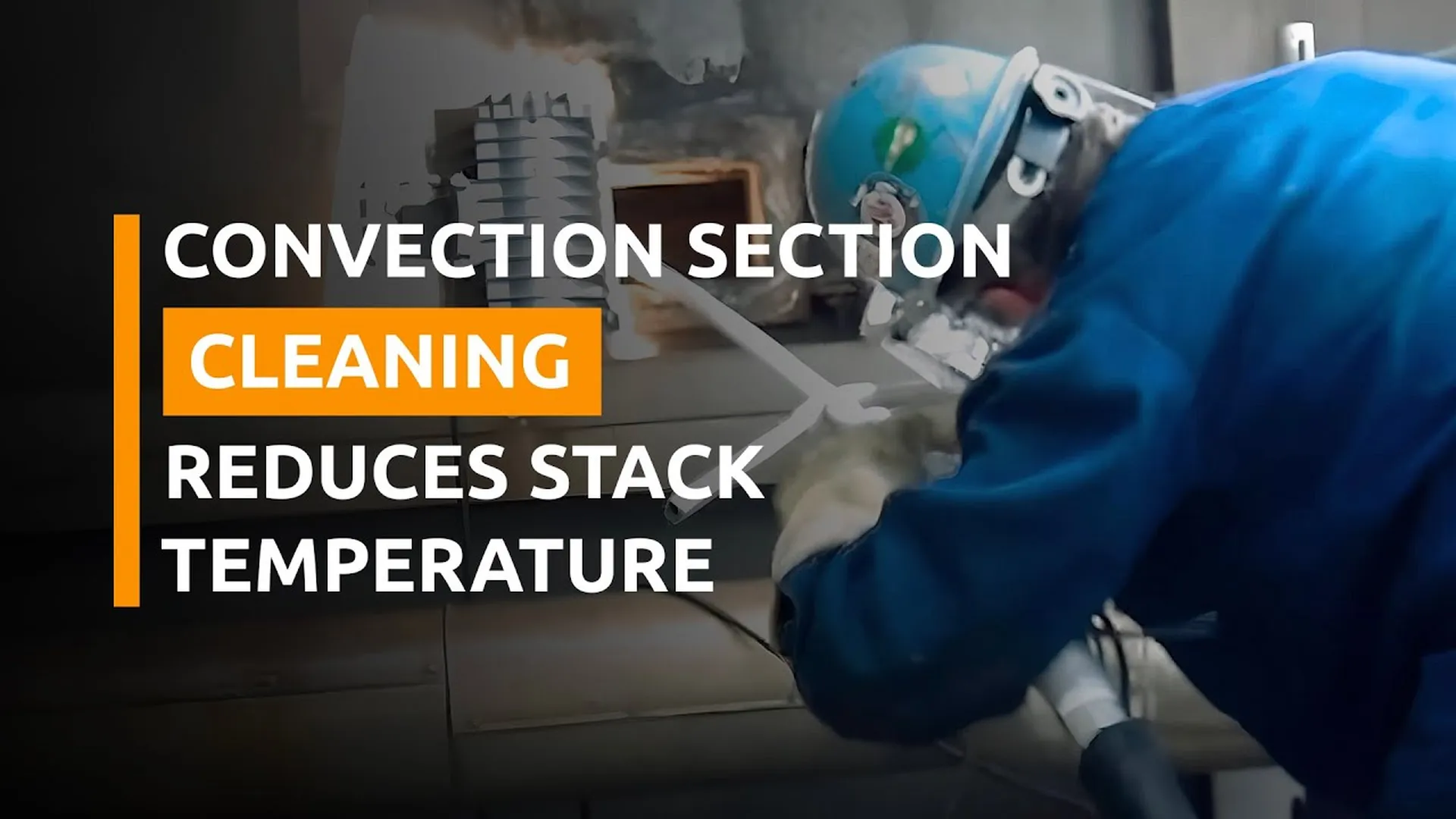
Limpieza de la sección de convección de calentadores de combustión/hornos de Tube Tech.
La misma empresa, ha mejorado sus tecnologías de limpieza con el recientemente lanzamiento del sistema Rover Mark 7, un robot innovador para limpiar el área de convección de los calentadores4, el cual es capaz de eliminar remotamente más del 90 % de las incrustaciones que se encuentran en esta zona. Desarrollado en el Reino Unido, este sistema posee dos patentes, que incluyen: sistema de ruedas y sistema deflector y transversal, que le permiten arrastrarse sobre placas de soporte de tubos intermedias y a través de estos.
El nuevo Rover automatizado utiliza tecnología Lidar para detectar distancias y detectar bloqueos u obstrucciones. Las imágenes en vivo HD ofrecen al operador retroalimentación en tiempo real, así mismo pueden utilizar imágenes y vídeos para informes y análisis4.
Medidas de seguridad
Los métodos de limpieza de equipos de proceso normalmente presentan numerosos peligros para el personal involucrado y las instalaciones. Los peligros varían dependiendo si la actividad se ejecuta con la planta en servicio, durante una parada, en sitio o en talleres; pero en líneas generales existen riesgos potenciales incendios y explosiones debido a los gases inflamables que evolucionan durante las operaciones, reacciones entre ciertos residuos del proceso y los químicos de limpieza.
Otros peligros potenciales incluyen caídas y lesiones corporales causadas por el uso inadecuado de equipo y herramientas, exposición a gases y químicos tóxicos, que se despliegan durante las operaciones de limpieza. En el contexto de las operaciones de una planta, resulta necesario adoptar medidas de seguridad adecuadas que minimicen la posibilidad de incidentes durante o derivados de las actividades de limpieza.
Las múltiples medidas de seguridad deben ser constantemente revisadas y actualizadas por el personal de involucrado antes del inicio de cualquier actividad. No hay razones inherentes para que la limpieza de un equipo de proceso deba ser menos segura que otra operación de mantenimiento.
Conclusión
La limpieza de equipos de proceso en las plantas de refinación es una operación necesaria que va más allá de la simple eliminación de residuos; es una práctica que mejora la eficiencia operacional de los sistemas, permite la inspección integral de los equipos, mantiene estándares de calidad en los productos refinados y genera seguridad al entorno de trabajo.
A medida que la industria continúa evolucionando, la implementación de prácticas efectivas y seguras para la limpieza de equipos de procesos, apoyadas por tecnología avanzada, se mantendrá como un requerimiento necesario para el éxito y la sostenibilidad de las operaciones de refinación.
Referencias
- IGS; “Increasing Furnace Efficiency With Hot Convection Cleaning”; https://integratedglobal.com/case_studies/increasing-furnace-efficiency-with-hot-convection-cleaning/; consultado 20 febrero 2024.
- Clean As New; https://cleanasnew.com/faq, consultado el 20 febrero 2024.
- Tube Tech International; https://www.youtube.com/watch?v=mNM50U_kKWo; consultado el 18 febrero 2024
- IGS “Tube Tech Launches Mark 7 Convection Section Cleaning Rover”; https://integratedglobal.com/igs-tube-tech-launches-convection-section-cleaning-rover/