Autor: Ph.D. Yolanda Reyes, 13 julio 2022.
Introducción
La Emisión Acústica (EA) es un Método de Ensayo no Destructivo (END), basado en un fenómeno físico que tiene lugar en el interior de los materiales. Atendiendo al fenómeno físico, la Emisión Acústica se define como la energía espontánea emitida por un material, en forma de ondas elásticas transitorias [1].
La aplicación de esfuerzos, condiciones ambientales severas sobre un material metálico, pueden producir cambios en su estructura interna, tales como: el crecimiento de grietas, deformación local plástica, corrosión o cambios de fase que, normalmente, están acompañados de la emisión de ondas elásticas en su interior. Estas ondas, por tanto, contienen valiosa información sobre su comportamiento interno. Asimismo, un ensayo de EA es útil para controlar la formación de defectos en un material mediante la detección y análisis de las ondas de emisión acústica generadas.
Este tipo de ensayo se diferencia del resto de los END en dos aspectos fundamentales: La primera radica en el origen de la señal de EA, ya que se trata de un método pasivo, detecta la energía que se libera en el propio material, mientras que los otros métodos necesitan aportación artificial de energía para la detección de defectos (por ejemplo: rayos X, rayos gamma, ultrasonidos, energía térmica o microondas).
La segunda, es que revela fenómenos dinámicos. Esta característica es, especialmente relevante, ya que durante el ensayo sólo se detectan fenómenos activos, como puede ser el crecimiento de grietas, y no discontinuidades geométricas como hacen el resto de métodos END. El ensayo de EA es efectivo para detectar el comportamiento de la fractura y fatiga en diversidad de materiales como metales, materiales compuestos avanzados, plásticos, hormigón, madera, etc.
En este sentido, el ensayo resulta útil para supervisar la integridad de estructuras de forma no invasiva, así como para la caracterización de materiales sometidos a deformación y/o fractura. Algunas aplicaciones en que el uso de este ensayo es común son la detección de fallos y/o fugas en depósitos a presión, sistemas de tuberías, tanques de almacenamiento, control de soldaduras, detección de procesos de corrosión, inspección de estructuras o maquinaria.
Mediante el ensayo de EA se puede medir, sólo cualitativamente, la cantidad de daño que se produce en una estructura o componente. Con el fin de obtener resultados cuantitativos sobre el tamaño, profundidad y aceptabilidad del daño es necesario combinar este ensayo con otros métodos.
Otro inconveniente es la sensibilidad al ruido de fondo, tanto mecánico como eléctrico, por lo que su uso en entornos de servicio severos es complicado. Para garantizar el éxito del ensayo, es crucial la discriminación y reducción de las señales de ruido, considerado éste como las señales generadas por todos los mecanismos irrelevantes al ensayo que se está realizando.
Análisis de los resultados de la técnica de EA
El análisis de emisiones acústicas es capaz de revelar procesos de daños en materiales durante todo el historial de carga, es obvio que el registro de procesos de daño desde la escala microscópica hasta la macroscópica produce grandes conjuntos de datos incluso durante períodos de tiempo relativamente cortos [2].
El número de eventos puede ser de unos varios miles durante una prueba. El alto número de emisiones acústicas es un hecho que debe tenerse en cuenta durante el procedimiento de análisis, debido a la a menudo baja relación señal-ruido de la señal, se necesitan varios pasos adicionales de procesamiento de datos antes de obtener resultados interpretables.
Aunque su dominio requiere un entrenamiento considerado de alto nivel, y personal con ciertas calificaciones, la confiabilidad de sus resultados y la data en tiempo real que permite registrar, la hace de un alto valor agregado. Sumado a eso la versatilidad que ofrece, como por ejemplo el estudio de comportamiento bajo carga de estructuras y obras civiles además de una amplísima variedad de equipos y componentes de industrias como petroleras y aeronáuticas, aumenta su atractivo en lo que a servicios a prestar se refiere.
Hay que tener claro un par de principios básicos respecto al rendimiento de la AE, ya que de ellos depende su desempeño.
Por su propia naturaleza, difiere de los métodos convencionales volumétricos de inspección No Destructiva en ciertos aspectos. El primer aspecto a considerar es que, un defecto o discontinuidad como una grieta tiene forzosamente que estar propagándose, y liberando energía para que los sensores puedan captar este evento e identificar la zona. Una grieta “estática” que no está liberando energía, al no producir ninguna emisión, no será susceptible de detección con esta técnica, por ende.
Métodos como UT o RT detectan estos defectos por la comunicación de energía al material, la que interactúa con el mismo. En el caso de AE la energía proviene de una carga aplicada, en muchos casos típica del trabajo que realiza la estructura en sí.
El segundo aspecto importante a considerar es, que esta técnica detecta procesos dinámicos fuertemente vinculados a los mecanismos de deterioro de la integridad estructural en tiempo real.
En la Figura. 1, se puede apreciar como el arreglo de sensores permite establecer la localización de las fuentes de los eventos.
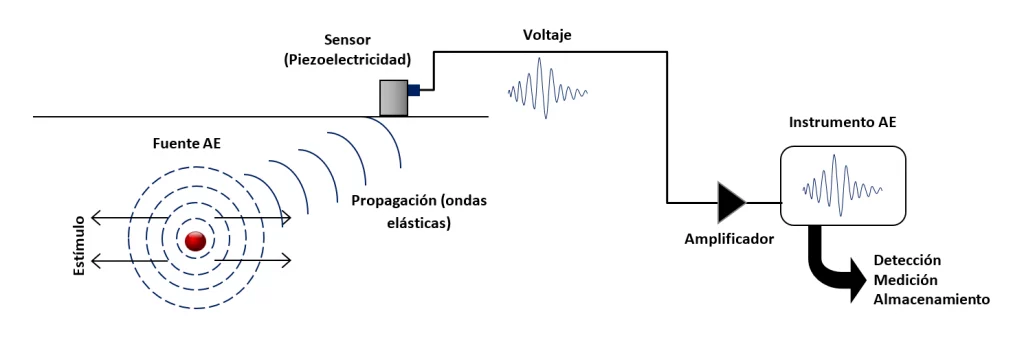
¿Por qué las pruebas de emisiones acústicas son importantes?
Debemos concienciarnos de que realizar pruebas de emisiones acústicas de calidad ayudará a reducir los gastos en el futuro, ya que conseguiremos reducir los costes de mantenimiento y reparación. Además, de ayudar a garantizar la seguridad de los equipos e instalaciones, verificando la calidad de los mismos.
Como ejemplo podemos citar el caso de los tanques de almacenamiento atmosférico (AGST por sus siglas en inglés), en la industria de producción petrolera.
El ensayo permite efectuar una jerarquización de los tanques pertenecientes a un patio de almacenamiento, en base a la condición de integridad que presenten durante el ensayo. Es especialmente adecuado para verificar la integridad de las láminas de piso. De existir fugas o filtraciones a través del piso, serán detectadas de inmediato.
Igualmente ocurre con la existencia de procesos corrosivos, ya que los subproductos del proceso de corrosión generan eventos que son detectados durante el monitoreo. Estos subproductos poseen una estructura físicamente mucho más frágil que el acero y el desprendimiento de este residuo bajo carga es lo que produce dichos eventos Figura 2. Las ventajas de la técnica son enormes, desde el punto de vista operativo, ya que evita tener que sacar el tanque fuera de servicio para proceder con la inspección del piso. Se procede con el monitoreo mediante AE y se establecen las condiciones de acuerdo a la evaluación de los resultados obtenidos.
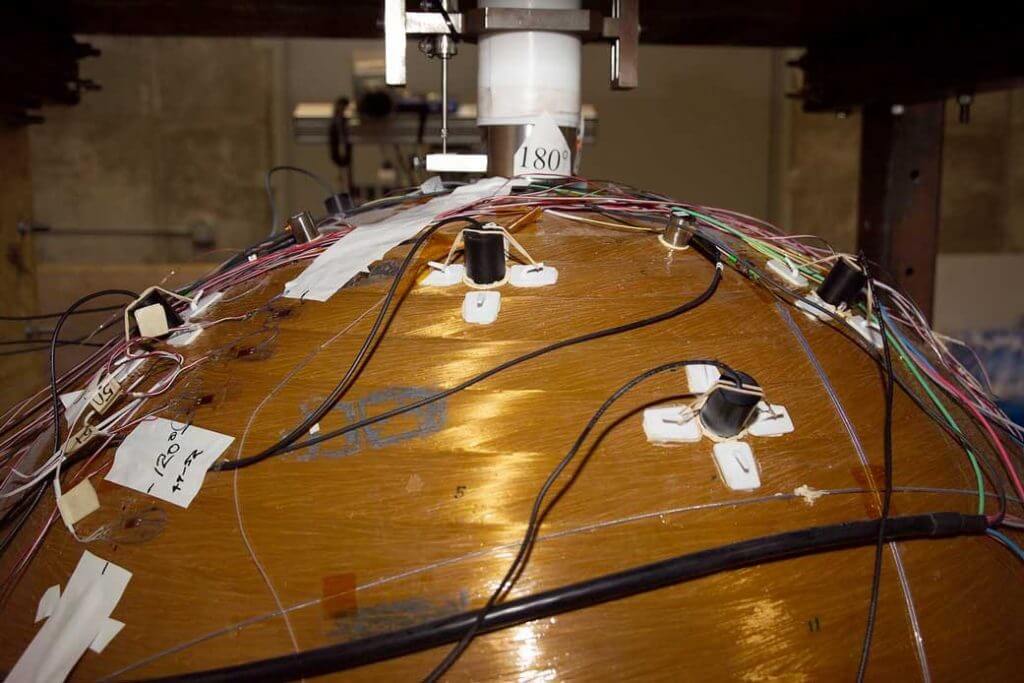
Ámbito de Aplicación de la Emisión Acústica
Una de las características más impresionantes de la Emisión Acústica es el amplio rango dinámico de las señales observadas. Se pueden detectar señales desde unas pocas décimas de micro-Volts inducidas por procesos de micro-deformaciones, hasta señales de varios Volts generadas por procesos de fractura. Esta característica permite el desarrollo de una gran variedad de aplicaciones.
En el laboratorio, el método de Emisión Acústica es una herramienta utilizada para el estudio de procesos de deformación y fractura. En el sector industrial se emplea para la inspección de recipientes a presión, tanques de almacenamiento, aeronaves y vehículos espaciales, utilería de plantas eléctricas, puentes, tanques cisterna de ferrocarril y grúas para izaje. La emisión acústica se emplea típicamente para la detección de grietas, corrosión, defectos de soldadura, y fragilización del material.
A continuación, se resumen algunas de las aplicaciones más extendidas de este método de END:
- Ensayo y caracterización de materiales diversos: metales, materiales compuestos avanzados, plásticos, madera, hormigón, material biológico, etc.
- Industria química y petrolífera: ensayos de integridad en recipientes a presión, ensayos de tanques de almacenamiento, tanques criogénicos, pruebas de tiempo de reutilización de los reactores termales, torres, columnas y sistemas de tuberías, ensayos del fondo de tanques, detección de corrosión en tiempo real, ensayo de tanques de FRP, inspección en la red de tuberías, detección de fugas en válvulas y en tuberías enterradas, detección de arena en las tuberías de alta mar y auscultación en las plataformas “offshore”
- Diagnóstico de centrales eléctricas
- Industria aeronáutica y aeroespacial: ensayos en aviones, ensayos de envejecimiento de aviones, ensayos de fatiga de componentes, detección de corrosión bajo las alas, inspección in-situ de partes del tren de aterrizaje, ensayo de álabes y palas en helicópteros, detección de grietas en el fuselaje, etc.
- Industria metalúrgica: desgaste de herramientas y detección de roturas, detección de contacto entre piezas, control de calidad de procesos de trabajo en metales, detección de colisiones y prevención en procesos de fabricación.
- Ingeniería civil: inspección de la estructura de edificios de hormigón, ensayos en puentes y túneles, la vigilancia continua de daños o propagación de grietas, ensayos de las grúas, etc.
- Aplicaciones en el transporte: detección y localización de fallos en remolques, vagones y camiones cisternas, detección de grietas en materiales y estructuras ferroviarias, pruebas de integridad de puentes y túneles, control del estado de los rodamientos y cojinete de camiones y trenes, detección de grietas en las ruedas y los ejes de los trenes, etc.
- Otras aplicaciones: control de soldaduras, aplicaciones geológicas y sismológicas, supervisión del estado del motor, control de procesos “on-line” de máquinas rotativas, etc.
Conclusión
Este método es muy eficaz cuando se utiliza para detectar fatiga y el comportamiento de la fractura en metales, materiales compuestos avanzados, plásticos, fibra de vidrio, materiales cerámicos, hormigón y madera. Con el equipo adecuado y personal capacitado, se pueden detectar fallos a escala micro-métrica. Sus numerosas ventajas y aplicaciones han hecho que la EA sea un método de END consolidado y fiable para la evaluación del daño y la prevención de fallos en un material. Este método puede ayudar a evitar costes asociados con las reparaciones de estructuras dañadas si no se detecta un defecto.
Sobre el autor
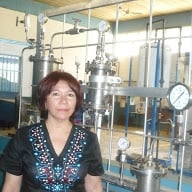
Ph.D, en Electroquímica y Corrosión, con más de 30 años de experiencia y un amplio y versátil conocimiento en Ciencias de la Corrosión y Tecnología Química a nivel Académico e Industrial. Asesor de planes de programas de mantenimiento en la industria en empresas petroleras, al frente de obras de servicios de limpiezas químicas y mecánicas de equipos tales como: calderas, tanques, intercambiadores de calor entre otros. leer mas