Tabla de Contenidos
- Calentadores de coque vs. Calentadores de coque retardado
- Diferencia clave: Transferencia de calor vs. ruptura térmica controlada
- Desafíos comunes en los calentadores de coque retardado
- Importancia de la inspección en los calentadores de coque retardado
- Métodos de inspección recomendados
- Mejores prácticas para la gestión de riesgos
- Casos de éxito y lecciones aprendidas
- Conclusiones
- Referencias
Los calentadores de coque retardado desempeñan un papel crítico en la industria de refinación de hidrocarburos, especialmente en el proceso de coquización retardada, que permite maximizar la conversión de residuos pesados en productos valiosos como gasolina, diésel y coque de petróleo. Estos equipos se encargan de transferir el calor necesario para descomponer térmicamente los hidrocarburos más pesados, promoviendo su conversión en fracciones más ligeras y coque.
Sin embargo, los calentadores de coque retardado están sometidos a condiciones extremas, como altas temperaturas, presión y la presencia de compuestos corrosivos. Estas condiciones incrementan el riesgo de formación de depósitos de coque en los serpentines, corrosión en los materiales internos y fatiga térmica. Fallos en estos equipos no solo reducen la eficiencia operativa, sino que también representan graves riesgos de seguridad y pérdidas económicas significativas.
El propósito de esta guía es ofrecer un enfoque práctico y técnico para la inspección y el mantenimiento de los calentadores de coque retardado, asegurando su óptimo desempeño, minimizando riesgos y maximizando la eficiencia en la refinación de hidrocarburos.
Calentadores de coque vs. Calentadores de coque retardado
En la industria de refinación, los calentadores juegan un papel clave en la conversión de residuos pesados en productos más valiosos. Dentro del proceso de coquización, es fundamental diferenciar entre un Coker Heater (calentador de coker) y un Delayed Coker Heater (calentador de coquización retardada), ya que cada uno cumple funciones específicas en la transformación térmica de los hidrocarburos pesados.
Calentador de coque: Transferencia de calor general para el proceso de coquización
El Coker Heater es un calentador de proceso convencional utilizado en diversas etapas de la coquización y en otras aplicaciones de refinación. Su función principal es transferir calor a los hidrocarburos residuales antes de que ingresen a la siguiente fase de procesamiento, facilitando la descomposición térmica de los compuestos pesados y mejorando la eficiencia de separación de productos.
- Ubicación en el proceso: Puede encontrarse en diferentes puntos dentro de una unidad de coquización o en otros procesos térmicos.
- Operación: Trabaja con temperaturas elevadas, pero sin un diseño específico para la conversión directa de residuos pesados en coque.
- Aplicación: Se emplea en refinerías para calentar flujos de hidrocarburos sin necesariamente participar en la formación de coque dentro de los tambores de coquización.
Calentador de coque retardado: ¿Qué son los calentadores de coque retardado?
El Delayed Coker Heater o calentador de coque retardado está diseñado específicamente para el proceso de coquización retardada, donde se maximiza la conversión de residuos pesados en fracciones más ligeras y coque de petróleo. Su función principal es elevar la temperatura de la alimentación hasta el punto de ruptura térmica, garantizando que la coquización ocurra dentro de los tambores de coque y no en los serpentines del calentador.
- Ubicación en el proceso: Justo antes de los tambores de coquización, asegurando que la carga entre con la energía térmica adecuada para su conversión.
- Operación: Maneja altas temperaturas (480-500°C) y trabaja con cargas residuales con alto contenido de asfaltenos, evitando la formación prematura de coque en el propio calentador.
- Aplicación: Específico para unidades de coquización retardada, donde la alternancia entre tambores de coque requiere un control térmico preciso para evitar bloqueos y pérdida de eficiencia.
Elementos que componen los calentadores de coque retardado
Los calentadores de coque retardado se componen de varios elementos claves que son:
- Los serpentines: Tubos internos donde circulan los hidrocarburos que serán calentados.
- Las cámaras de combustión: Áreas donde se genera el calor mediante quemadores.
- Los intercambiadores de calor: Sistemas que optimizan la transferencia térmica para reducir pérdidas de energía.
Diferencia clave: Transferencia de calor vs. ruptura térmica controlada
Mientras que un Coker Heater puede utilizarse en distintas etapas de refinación para calentar hidrocarburos sin forzar la formación de coque, el Delayed Coker Heater está diseñado para operar en condiciones extremas dentro del proceso de coquización retardada, asegurando que la transformación de los residuos en coque ocurra exclusivamente en los tambores. Su diseño debe prevenir la acumulación de coque en los serpentines, lo que hace que su inspección y mantenimiento sean críticos para la seguridad y eficiencia de la unidad.
Esta diferenciación es fundamental para entender la relevancia de la inspección y el mantenimiento de los calentadores de coquización retardada, los cuales operan en un entorno de altas temperaturas y condiciones severas que demandan estrategias avanzadas de monitoreo y limpieza. En los siguientes apartados, exploraremos los principales desafíos operativos, las metodologías de inspección y los mejores enfoques para el mantenimiento preventivo de estos equipos esenciales en la refinación moderna.
Desafíos comunes en los calentadores de coque retardado
Los calentadores de coque retardado enfrentan varios problemas operativos debido a las condiciones extremas de operación. Entre los principales desafíos se incluyen:
- Formación de coque en los serpentines: La acumulación de coque en los tubos disminuye la eficiencia térmica, obstruye el flujo de hidrocarburos y aumenta el riesgo de fallos catastróficos por sobrecalentamiento.
- Sobrecalentamiento y desgaste de materiales: La exposición prolongada a temperaturas elevadas provoca la degradación de los materiales internos, afectando la integridad estructural y reduciendo la vida útil de los componentes.
- Corrosión interna: La presencia de compuestos ácidos en los hidrocarburos, como el ácido sulfhídrico, puede causar daños severos en las superficies internas de los serpentines y otros componentes del calentador.
- Fatiga térmica: Los cambios frecuentes de temperatura durante los ciclos de operación generan tensiones térmicas en los materiales, lo que puede derivar en fisuras o fallos estructurales.
El impacto de estos problemas no solo afecta la productividad de la planta, sino que también representa riesgos significativos para la seguridad operativa. Una inspección y mantenimiento regulares son esenciales para mitigar estos desafíos y garantizar un rendimiento eficiente y seguro en el procesamiento de hidrocarburos.
Importancia de la inspección en los calentadores de coque retardado
La inspección regular de los calentadores de coque retardado es fundamental para prevenir fallos catastróficos y garantizar el cumplimiento de las normativas internacionales, como API 530 y ASME Section VIII. Estos equipos operan bajo condiciones extremas de temperatura y presión, lo que aumenta su vulnerabilidad a problemas como el desgaste, la corrosión y la acumulación de coque de petróleo en los serpentines.
El objetivo principal de la inspección es asegurar la seguridad operativa, maximizar la eficiencia térmica y prolongar la vida útil de los equipos. Esto se logra a través de varias acciones clave:
- Detectar desgaste o corrosión: Identificar áreas donde los materiales presentan pérdida de espesor o degradación debido a condiciones operativas adversas.
- Identificar fallas en uniones soldadas y serpentines: Las inspecciones permiten localizar grietas, fugas o defectos en las soldaduras que puedan comprometer la integridad del sistema.
- Evaluar la integridad estructural: Verificar que los componentes principales, como los serpentines y las cámaras de combustión, puedan soportar las condiciones de operación.
El cumplimiento de normas como API 530 garantiza que las inspecciones se realicen con procedimientos estandarizados, asegurando resultados consistentes y reduciendo riesgos asociados con fallos inesperados.
Métodos de inspección recomendados
Inspección visual
La inspección visual es el método más básico y esencial para evaluar el estado de los calentadores de coque retardado. Este proceso incluye:
- Procedimientos básicos: Identificar grietas, deformaciones, acumulación de depósitos de coque o desgaste visible en los serpentines y otras superficies internas.
- Herramientas especializadas: Uso de cámaras de inspección para áreas de difícil acceso, como los tubos internos, para detectar irregularidades con mayor precisión.
Pruebas no destructivas (NDT)
Las pruebas no destructivas o ensayos no estructivos (END) son fundamentales para obtener información detallada sin comprometer la integridad del equipo:
- Ultrasonido (UT): Evalúa el espesor de las paredes de los serpentines y detecta corrosión interna antes de que se convierta en un problema crítico.
- Radiografía industrial (RT): Identifica defectos en las soldaduras, como grietas o porosidades, utilizando rayos X o gamma.
- Partículas magnéticas (MT): Detecta grietas superficiales en materiales ferromagnéticos mediante la aplicación de partículas magnéticas.
- Líquidos penetrantes (PT): Revela fisuras o grietas en las superficies externas al aplicar líquidos contrastantes.
Monitoreo en línea
El monitoreo en tiempo real es una solución avanzada para supervisar continuamente el estado de los calentadores:
- Sensores: Detectan variaciones en presión, temperatura y emisiones, lo que permite una respuesta inmediata a posibles anomalías.
- Sistemas IoT: Proveen alertas tempranas sobre condiciones operativas fuera de los parámetros seguros, reduciendo el riesgo de fallos catastróficos.
Programa de mantenimiento preventivo
Diseño de un plan de mantenimiento efectivo
Un programa de mantenimiento bien diseñado asegura que los calentadores de coque retardado operen de manera eficiente y segura:
- Identificación de puntos críticos: Determinar las áreas más vulnerables, como serpentines, soldaduras y quemadores.
- Frecuencia recomendada: Realizar inspecciones y limpiezas regulares según las condiciones operativas y normativas aplicables.
- Registro histórico: Documentar todas las actividades de mantenimiento para identificar patrones y optimizar futuros procedimientos.
Limpieza de los serpentines (Decoking)
El proceso de decoking o limpieza de serpentines es esencial para eliminar depósitos sólidos de coque, mantener la eficiencia térmica y prevenir obstrucciones.:
- Métodos mecánicos: Uso de raspadores internos y externos para eliminar depósitos sólidos de coque acumulado en los tubos.
- Métodos químicos: Aplicación de solventes específicos que disuelven el coque sin dañar los materiales de los serpentines.
Para entender mejor el proceso de limpieza de serpentines en los calentadores de coque retardado, aquí tienes un video explicativo de la empresa DDT Technology, que muestra tecnologías avanzadas para la eliminación de coque en tubos industriales:
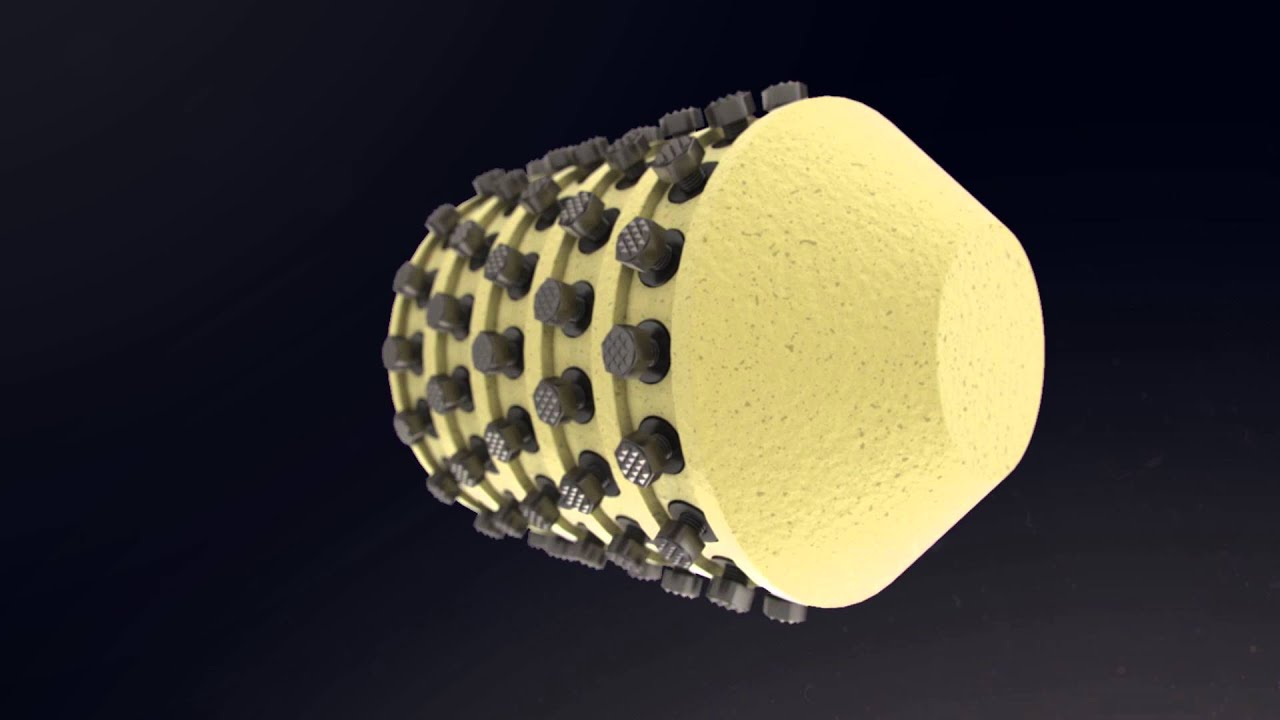
Tecnologías avanzadas en la eliminación de coque.
Reparación y reemplazo de componentes
Mantener los componentes en óptimas condiciones evita interrupciones en la operación:
- Reemplazo seguro: Sustitución de serpentines, juntas y otros componentes siguiendo procedimientos estandarizados y normativas como API 530.
- Reparación de soldaduras: Uso de técnicas aprobadas para garantizar la integridad de las uniones.
Revisión de quemadores y cámaras de combustión
El mantenimiento de los sistemas de combustión asegura una transferencia de calor eficiente:
- Calibración y ajuste: Optimización de los quemadores para maximizar la eficiencia térmica y reducir el consumo de combustible.
- Limpieza y reparación: Retiro de acumulaciones en los refractarios de las cámaras de combustión y reparación de daños estructurales.
Implementar un programa de mantenimiento preventivo basado en estas acciones garantiza que los calentadores de coque retardado operen de manera segura, eficiente y conforme a los estándares de la industria.
Mejores prácticas para la gestión de riesgos
La gestión de riesgos en los calentadores de coque retardado es esencial para garantizar la seguridad, minimizar interrupciones y maximizar la eficiencia operativa en el procesamiento de hidrocarburos. Una de las principales prácticas es la implementación de auditorías regulares de seguridad durante las actividades de inspección y mantenimiento. Estas auditorías permiten identificar riesgos potenciales, asegurar el cumplimiento de normativas internacionales como API 530 y ASME, y garantizar que las operaciones se realicen en condiciones seguras.
Otro aspecto clave es la formación del personal técnico, asegurando que los operadores y técnicos estén capacitados en procedimientos avanzados de inspección, mantenimiento y manejo de equipos críticos. Esto no solo mejora la calidad de las inspecciones, sino que también reduce el riesgo de errores humanos.
El uso de tecnología avanzada, como los gemelos digitales, también es una herramienta invaluable para prever fallos y optimizar las operaciones. Los gemelos digitales permiten simular condiciones operativas reales, analizar escenarios de estrés térmico y evaluar el impacto de cambios en los parámetros operativos, lo que facilita la toma de decisiones basada en datos.
Adoptar estas prácticas reduce riesgos y mejora la seguridad y productividad de las operaciones relacionadas con los calentadores de coque retardado.
Casos de éxito y lecciones aprendidas
BECHT
- Especialización: BECHT es una firma de ingeniería y consultoría con amplia experiencia en la optimización de procesos industriales, incluida la mejora del rendimiento de calentadores de coque retardado.
- Casos comprobables: BECHT ha implementado soluciones como análisis de integridad mecánica, evaluación de fatiga térmica, limpieza química personalizada y sistemas de monitoreo continuo mediante IoT. Su enfoque está basado en normativas internacionales como API y ASME, lo que asegura la calidad de sus resultados.
Honeywell UOP
- Especialización: Honeywell UOP desarrolla tecnologías para procesos de refinación, incluyendo sistemas de mantenimiento y operación de calentadores de coque retardado.
- Casos comprobables: UOP ha liderado proyectos donde se han mejorado los diseños de calentadores para aumentar la eficiencia energética y reducir el mantenimiento correctivo, mediante la integración de herramientas de monitoreo remoto y análisis de datos.
Siemens Energy
- Especialización: Siemens Energy se enfoca en soluciones digitales y tecnologías de monitoreo avanzado para equipos de refinación.
- Casos comprobables: Siemens ha implementado sistemas IoT para el monitoreo en tiempo real de calentadores de coque retardado, facilitando la detección de fallos y la planificación de mantenimiento preventivo.
Estas empresas han demostrado resultados tangibles en la optimización de calentadores de coque retardado, implementando prácticas de inspección y mantenimiento basadas en tecnología avanzada y normativas internacionales. Si necesitas casos específicos de alguna de estas compañías, puedo profundizar en sus logros o referencias documentadas.
Conclusiones
la inspección y mantenimiento de los calentadores de coque retardado son fundamentales para garantizar el desempeño óptimo en la refinación de hidrocarburos. Los principales desafíos operativos, como la acumulación de coque, la corrosión interna y la fatiga térmica, requieren soluciones avanzadas. La aplicación de pruebas no destructivas y el monitoreo en línea permiten detectar fallas tempranas, optimizando la vida útil del equipo y reduciendo el riesgo de fallos catastróficos. La implementación de estrategias de mantenimiento basadas en datos es clave para mejorar la eficiencia y seguridad en estos sistemas críticos.
La implementación de programas preventivos y el uso de tecnologías avanzadas, como gemelos digitales y sensores IoT, permiten anticipar problemas y reducir costos a largo plazo. La inspección y el mantenimiento son esenciales para prevenir fallos catastróficos, y representan una inversión estratégica para maximizar la productividad, eficiencia térmica y seguridad operativa de las refinerías.
Recomendamos establecer alianzas con proveedores especializados en inspección industrial, como BECHT, Honeywell UOP y Siemmens Energy, quienes han demostrado un historial comprobable de éxito en la optimización de estos equipos. Estas colaboraciones aseguran acceso a soluciones innovadoras y prácticas alineadas con normativas internacionales como API y ASME, mejorando el rendimiento y la sostenibilidad en el procesamiento de hidrocarburos.
Referencias
Fuente propia