Tabla de Contenidos
- Introducción
- ¿Qué es y cómo funciona la soldadura por arco eléctrico?
- ¿Por qué la soldadura por arco eléctrico es tan popular?
- Principales tipos de soldadura por arco eléctrico
- Ventajas y desventajas de estos tipos de soldadura
- Innovaciones recientes en soldadura por arco eléctrico
- Conclusiones
- Referencias
Introducción
La soldadura por arco eléctrico es de suma importancia en la industria metalúrgica desde su creación a finales del siglo XIX. A lo largo del tiempo, ha evolucionado de un proceso rudimentario a una técnica avanzada que permite unir metales de manera eficiente, utilizando un arco eléctrico como fuente de calor. Inicialmente, se basaba en un electrodo de carbono, pero con el desarrollo de electrodos metálicos consumibles, el proceso adquirió mayor consistencia y capacidad de adaptación a diversas aplicaciones.
Actualmente, es fundamental para diversos sectores industriales, destacándose por su precisión, rapidez y capacidad de adaptación a distintos materiales y espesores. En este artículo, se presentan los principales procesos de soldadura por arco, sus aplicaciones y las innovaciones recientes que han mejorado su eficiencia y calidad.
¿Qué es y cómo funciona la soldadura por arco eléctrico?
Es un proceso que une metales mediante la fusión localizada producida por el intenso calor de un arco eléctrico, el cual se forma entre un electrodo (consumible o no) y el material base; a medida que el electrodo se funde, crea un material de relleno que forma la soldadura. El arco producido puede alcanzar temperaturas de hasta 6,000 °C, suficientes para fundir tanto el electrodo como el borde del metal base.
El uso de una fuente de alimentación, que puede ser de corriente alterna (CA) o corriente continua (CC), proporciona la energía necesaria para el proceso. La CC es preferida para materiales más delgados debido a su mayor estabilidad, mientras que la CA es utilizada en elementos de mayor espesor.
Durante el proceso, se emplea un gas protector o un revestimiento de fundente para evitar la contaminación atmosférica, asegurando la calidad de la unión. Tras la fusión, los metales se solidifican, creando una unión fuerte y duradera, características relevantes de un proceso de soldadura que puede aplicarse a una amplia variedad de metales y espesores.
Elementos que conforman este tipo de soldadura
- Arco eléctrico: Es lo que se genera entre el electrodo y la pieza de trabajo, proporcionando el calor necesario para fundir los metales y realizar la soldadura.
- Electrodo consumible: En muchos procesos de soldadura por arco, se utiliza un electrodo de metal que se consume durante el proceso y transfiere la corriente hacia el material base.
- Gas protector: Un gas, como argón o dióxido de carbono, se emplea para proteger el baño de soldadura del aire y evitar la oxidación.
- Fuente de energía: Se requiere una fuente eléctrica, como un transformador o un inversor, para generar la corriente que mantiene el arco.
- Baño de soldadura: El metal fundido por el calor del arco forma lo que se llama el baño de soldadura. Este metal luego se enfría y solidifica, formando la unión soldada.
¿Por qué la soldadura por arco eléctrico es tan popular?
Desde su origen a finales del siglo XIX, la soldadura por arco eléctrico ha sido fundamental en la industria metalúrgica. Introducida por Nikolay Benardos en 1881 con un electrodo de carbono, y perfeccionada por C.L. Coffin en 1890 con electrodos metálicos consumibles, este proceso ha evolucionado continuamente. Su popularidad radica en su versatilidad, permitiendo unir una variedad de metales y espesores en prácticamente cualquier posición.
Además, destaca por su alta velocidad de deposición y rentabilidad, adaptable tanto a procesos manuales como automatizados, lo que la convierte en una herramienta precisa para la producción en serie. Su precisión y eficiencia han mejorado constantemente gracias a innovaciones tecnológicas, consolidándose como la técnica de soldadura más utilizada en el mundo.
Principales tipos de soldadura por arco eléctrico
Este tipo de soldadura engloba una variedad de procesos, cada uno con características específicas y adaptado a diferentes aplicaciones industriales y tipos de materiales. A continuación, se detallan los principales:
Soldadura con electrodo revestido (SMAW)
También conocida como arco metálico protegido o stick welding, es uno de los métodos más convencionales, utilizando un electrodo revestido consumible que actúa como fuente de calor y material de aporte. El arco eléctrico se establece entre el electrodo y la pieza de trabajo, fundiendo ambos para formar el cordón de soldadura. El revestimiento del electrodo genera una atmósfera protectora que previene la oxidación durante el proceso.
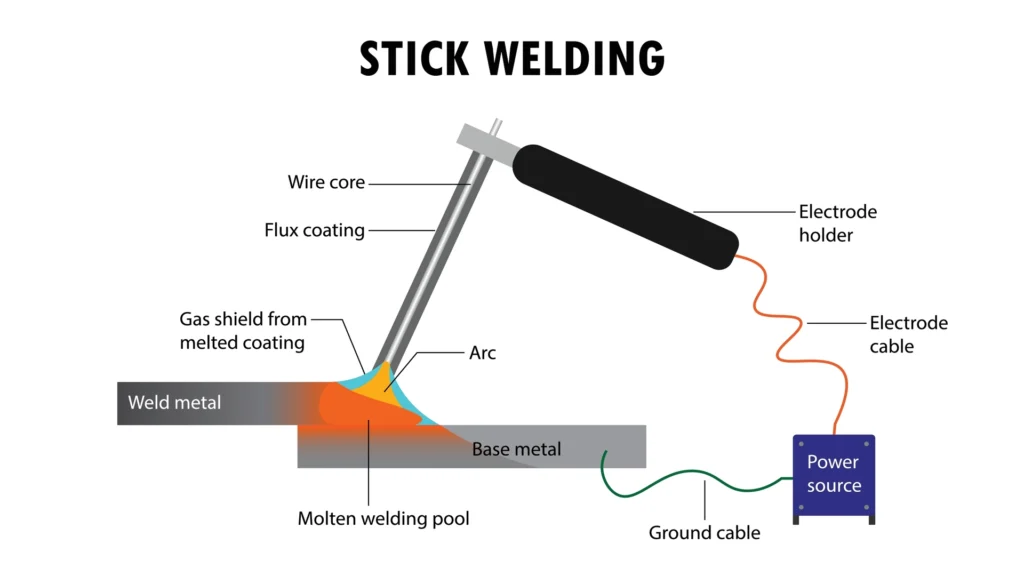
Es ampliamente utilizada en la construcción y la reparación, su portabilidad y simplicidad la hacen ideal para aplicaciones en ambientes exteriores, en metales con impurezas; siendo especial para soldaduras estructurales y de tuberías, donde las condiciones de trabajo pueden ser complicadas.
Soldadura por arco metálico con gas de protección (GMAW)
Este proceso de soldadura GMAW, utiliza un alambre continuo como electrodo y un gas de protección (inerte o activo) que rodea el arco, evitando la oxidación y contaminación. Este tipo de soldadura está conformada por dos tipos: MIG (Metal Inert Gas) que emplea un gas inerte como el argón, ideal para soldar aluminio y otros metales no ferrosos; y MAG (Metal Active Gas) donde se utiliza un gas activo como el dióxido de carbono o mezclas de gases, adecuado para soldar acero.
Estos métodos son valorados por su alta velocidad y eficiencia, siendo preferidos en industrias con producción en masa como la automotriz y la fabricación de estructuras metálicas, tuberías y equipos.
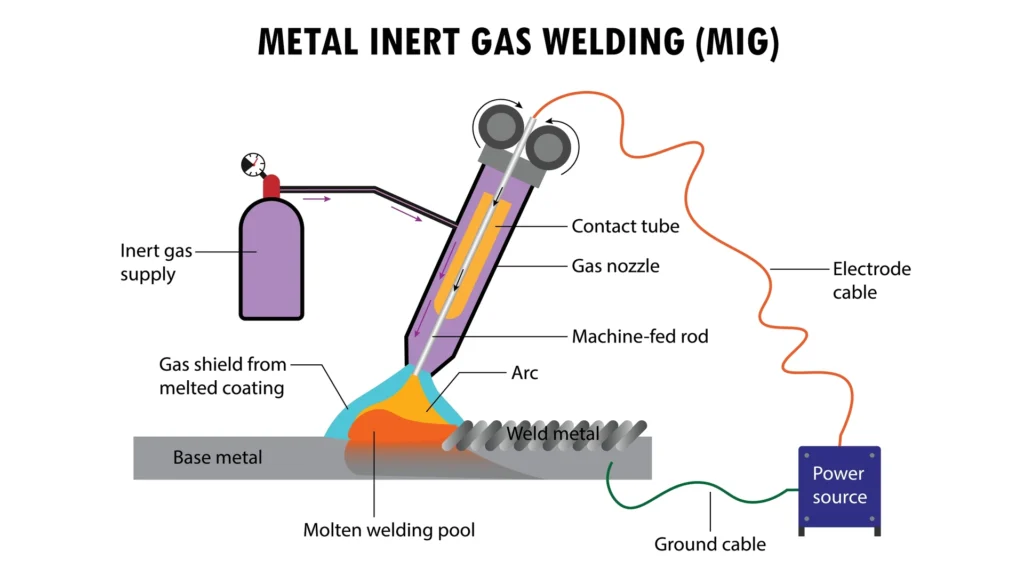
Soldadura por arco con tungsteno y gas inerte (GTAW)
También conocida como soldadura TIG (Tungsten Inert Gas), este proceso utiliza un arco eléctrico entre un electrodo de tungsteno no consumible y el material base, mientras un gas inerte, típicamente argón, protege el área de soldadura de la contaminación atmosférica. El material de aporte se introduce de manera externa, lo que permite un mayor control sobre el proceso y la cantidad de material depositado.
Es un método de soldadura lento, pero su alta precisión y calidad de acabado la hacen ideal para aplicaciones que requieren resistencia a la corrosión y acabados estéticos de alta calidad, como en la industria aeroespacial y la fabricación de tuberías críticas. El control preciso de las variables, como el calor y la velocidad, minimiza las deformaciones en materiales delgados.
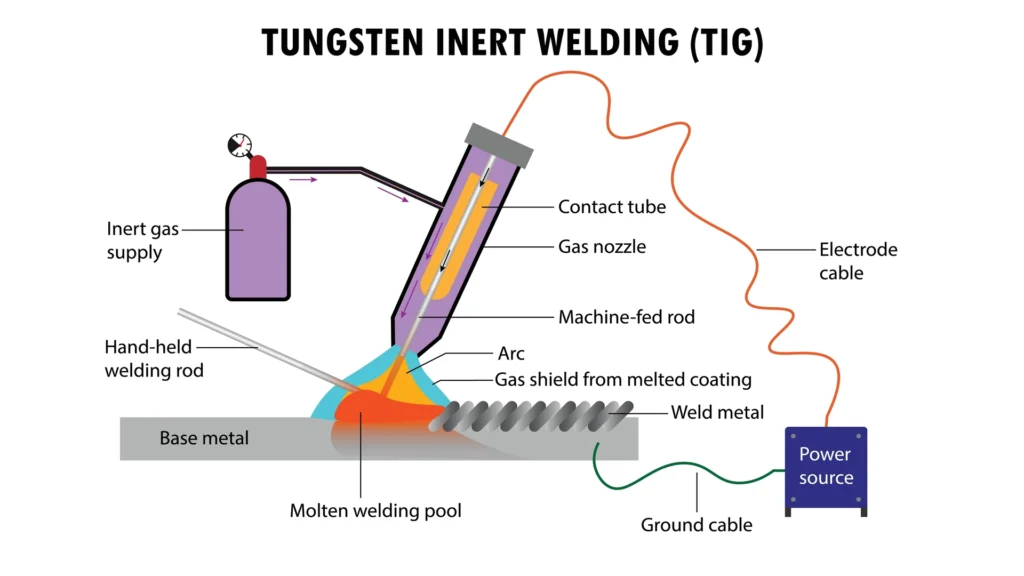
Soldadura por arco sumergido (SAW)
Este método es característico por utilizar un flujo granular que cubre completamente el arco, permitiendo que la soldadura se realice sin exposición al aire, lo que reduce las salpicaduras y aumenta la eficiencia. Es un proceso altamente eficiente y automatizado, ideal para aplicaciones industriales pesadas donde se requieren soldaduras largas y de alta resistencia, como en la fabricación de tuberías y estructuras metálicas. Además, este proceso permite una mayor penetración de la soldadura y una calidad consistente.
El siguiente video muestra el proceso «long stick-out» (LSO) es un método de soldadura por arco sumergido diseñado para maximizar la productividad. Su principio se basa en la resistividad natural del hilo de soldadura. Al aumentar la longitud del stick-out eléctrico (la distancia entre la boquilla de contacto y el punto de arco), el hilo se precalienta antes de entrar en el arco, lo que facilita su fusión. Este precalentamiento permite que, a un mismo amperaje, la tasa de deposición se incremente, incluso duplicándose en comparación con un stick-out convencional. Cortesía de: Lincoln Electric Asia Pacific.
Soldadura por arco con núcleo fundente (FCAW)
Es una variación de la soldadura por arco eléctrico tradicional, en el cual se utiliza un electrodo tubular con un núcleo fundente en su interior. La corriente eléctrica genera un arco entre el electrodo y el material base, generando el calor necesario para fundir el metal y formar la unión. El núcleo fundente del electrodo proporciona protección contra la oxidación al generar una atmósfera protectora, similar al proceso de la soldadura con electrodo revestido (SMAW), pero con mayor velocidad, eficiencia y aplicabilidad.
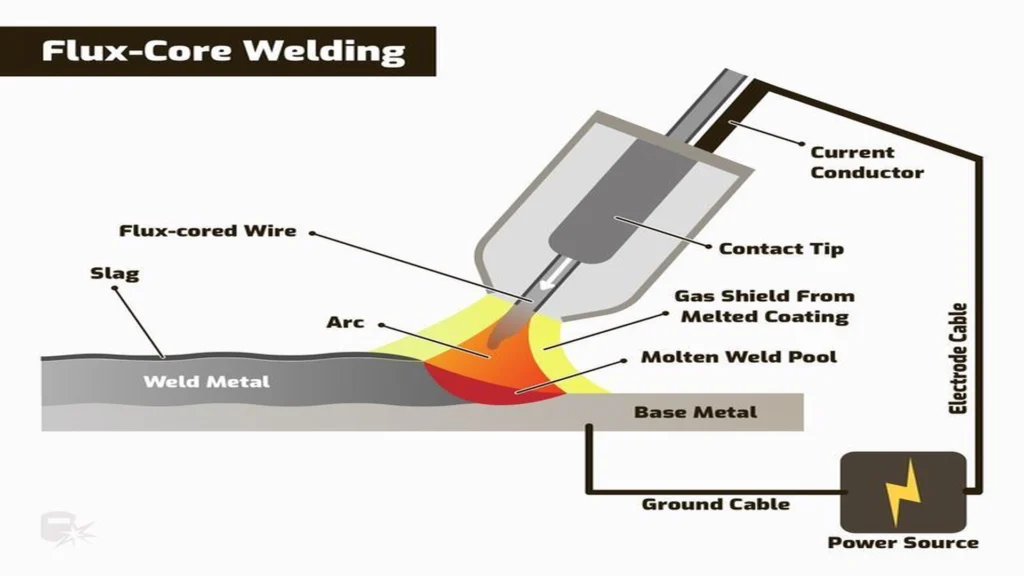
Ventajas y desventajas de estos tipos de soldadura
Este es un proceso de soldadura ampliamente utilizado en la industria, pero como cualquier técnica, tiene tanto ventajas como limitaciones que deben ser consideradas al elegir el método adecuado para cada aplicación.
Ventajas
- Versatilidad de procesos: Puede soldar diferentes tipos de metales (acero, aluminio, aleaciones) y adaptarse a múltiples procesos (SMAW, GMAW, GTAW, SAW, FCAW).
- Soldaduras de alta resistencia: La alta penetración del arco y el uso de gas o fundente protegen las uniones de la contaminación, proporcionando soldaduras fuertes y resistentes a tensiones mecánicas.
- Automatización eficiente: Se adapta fácilmente a sistemas automatizados, lo que mejora la precisión y la repetibilidad de las soldaduras, reduciendo la intervención manual y los errores humanos.
- Portabilidad: Los equipos de soldadura son ligeros y fáciles de transportar, ideales para reparaciones y trabajos en exteriores o ubicaciones remotas.
- Alta productividad: Permite una rápida deposición de metal, aumentando la eficiencia en la producción en serie y reduciendo los tiempos de ejecución.
- Soldadura de metales gruesos: Tiene la capacidad de soldar materiales de distintos espesores, desde láminas delgadas hasta grandes secciones, lo que la convierte en una opción útil para diferentes necesidades de fabricación.
- Capacidad para trabajar en condiciones adversas: Puede operar en condiciones climáticas difíciles, como viento o lluvia, sin comprometer la calidad de la soldadura, lo que la hace adecuada para trabajos al aire libre.
Desventajas
- Requiere alta habilidad técnica: La soldadura por arco eléctrico demanda operadores altamente capacitados para asegurar la calidad de las uniones, evitando defectos como porosidad y grietas.
- Emisión de humos y gases tóxicos: Durante el proceso se generan humos y gases nocivos que son peligrosos si no se cuenta con una ventilación adecuada.
- Limitaciones en materiales delgados: No es ideal para soldar metales de poco espesor, ya que el calor intenso puede causar distorsiones o deformaciones en las piezas.
- Generación de residuos: Produce más desperdicio y escoria en comparación con otros métodos, lo que puede aumentar los costos operativos y requerir limpieza adicional.
- Riesgos de seguridad: Existe riesgo de quemaduras por corriente eléctrica y daños oculares debido a las chispas y radiación ultravioleta, por lo que se requiere equipo de protección personal especializado.
- Impacto ambiental: Emite gases contaminantes como óxidos de nitrógeno y dióxido de carbono, contribuyendo a la contaminación del aire, y consume gran cantidad de energía eléctrica.
- Fragilización del metal: El proceso puede causar zonas endurecidas y quebradizas en la soldadura, aumentando la susceptibilidad a fisuras y fallas estructurales en el material.
Innovaciones recientes en soldadura por arco eléctrico
Las continuas innovaciones en soldadura por arco eléctrico se centran en mejorar la eficiencia, calidad y sostenibilidad del proceso. Entre los avances recientes destacan la automatización con cobots, junto con la inteligencia artificial (IA) y la visión artificial, que permiten una mayor precisión y la adaptación a geometrías complejas. La simulación y programación offline reduce tiempos de inactividad, mientras que los inversores de alta frecuencia optimizan los parámetros de soldadura, minimizando la distorsión térmica.
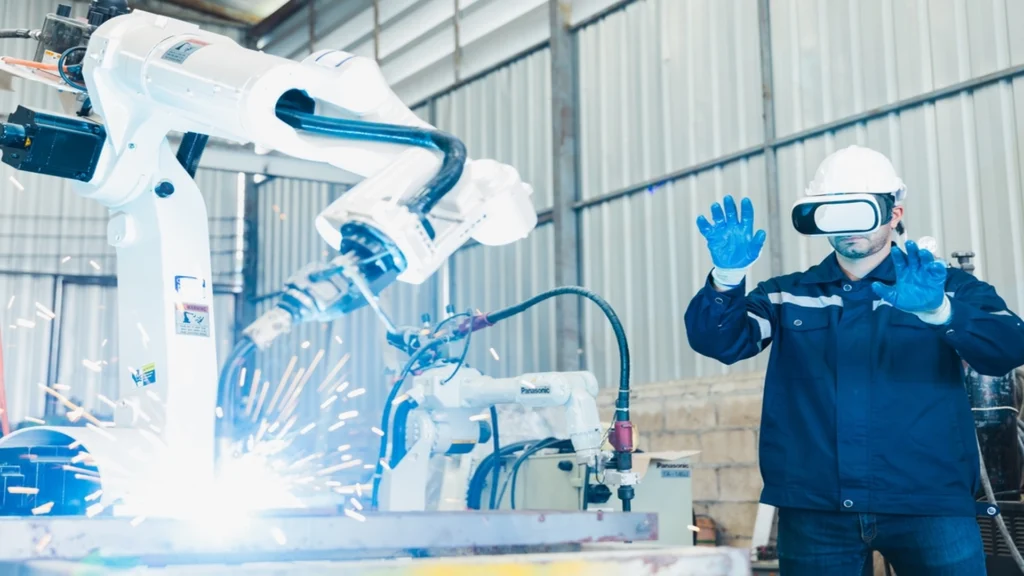
Los equipos multifuncionales y sistemas sinérgicos ajustan automáticamente las variables del proceso, lo que reduce errores. Además, se han desarrollado equipos más compactos, con interfaces intuitivas, y materiales de aporte mejorados, como alambres de relleno con aleaciones avanzadas que incrementan la resistencia mecánica y la resistencia a la corrosión. Los gases de protección de alta pureza mejoran la calidad final de las soldaduras.
En términos de eficiencia energética, las nuevas fuentes de alimentación disminuyen el consumo y las emisiones, mientras que los procesos se están volviendo más limpios y sostenibles. Un campo innovador es la integración de la soldadura por arco con la fabricación aditiva, que, junto con tecnologías como el láser, permite la creación de piezas con geometrías personalizadas.
Además, se han mejorado los sistemas de control numérico, lo que permite una mayor precisión y repetibilidad, especialmente en producciones a gran escala. La monitorización en tiempo real ha avanzado, permitiendo a los operadores detectar defectos o desajustes durante el proceso, mejorando la calidad y reduciendo el retrabajo.
El uso de nuevos materiales de soldadura, como los alambres con recubrimientos avanzados y los gases de protección optimizados, mejora la calidad de las uniones, reduce los tiempos de producción y los costos operativos en la industria.
Conclusiones
La soldadura por arco eléctrico es una de las técnicas más avanzadas y versátiles en la unión de metales, además de generar soldaduras de alta resistencia, su adaptabilidad a una amplia gama de materiales y espesores, la hacen fundamental en la industria de la soldadura. A lo largo de los años, las innovaciones tecnológicas han optimizado su eficiencia mediante el desarrollo de equipos automatizados, fuentes de energía más precisas y materiales de aporte avanzados.
Procesos como la soldadura GMAW, SMAW y TIG continúan ampliando el rango de aplicaciones industriales, mientras que la incorporación de sistemas de control numérico y automatización robótica garantizan una mayor precisión y repetibilidad. Estas mejoras, junto con una mayor sostenibilidad y reducción de emisiones, aseguran que este tipo de procesos mantenga su posición como una técnica necesaria en el desarrollo de infraestructuras modernas y manufactura avanzada.
Referencias
- https://www.taylor-studwelding.com/blog/types-of-arc-welding
- https://testbook.com/electrical-engineering/electric-arc-welding-diagram-principle-and-advantages
- https://ukmetalsexpo.com/5-exciting-innovations-in-welding/