Introducción
En el ámbito de la ingeniería y diseño de intercambiadores de calor, la norma API 660 se ha erigido como un estándar indiscutible. Este documento ha sido la brújula para profesionales y empresas en la fabricación de intercambiadores de calor de tubo y carcasa, garantizando calidad, seguridad y eficiencia. Este artículo se adentra en el desarrollo histórico de la API 660, desglosando sus características clave y las implicaciones de sus últimas actualizaciones.
Orígenes de la API 660
La norma API 660, también conocida como «shell-and-tube heat exchangers», tiene sus raíces en las décadas de 1950 y 1960, un período testigo de un crecimiento exponencial en la industria del petróleo y gas. Originada por el American Petroleum Institute (API), esta norma surgió como respuesta a la necesidad crítica de estandarizar la fabricación y el diseño de intercambiadores de calor de tubo y carcasa, componentes esenciales en numerosos procesos industriales. Antes de su implementación, la industria enfrentaba desafíos significativos debido a la falta de uniformidad en los estándares, lo que a menudo resultaba en problemas de eficiencia, seguridad y compatibilidad.
La API 660 fue concebida para abordar estas cuestiones, proporcionando un conjunto coherente y detallado de directrices que aseguraran la calidad y el rendimiento de los intercambiadores de calor. Desde su primera edición, se ha centrado en promover prácticas de diseño y fabricación que no solo cumplan con las exigencias operativas, sino que también mejoren la seguridad y la eficiencia. A lo largo de los años, la norma ha evolucionado, pero sus orígenes siguen siendo un testimonio del compromiso de la industria con la estandarización y la mejora continua, asegurando que los intercambiadores de calor se fabriquen según los más altos estándares de calidad.
Características fundamentales de la norma API 660
La norma API 660, reconocida por su rigurosidad y exhaustividad, establece un marco integral para el diseño, fabricación y operación de intercambiadores de calor de tubo y carcasa. Sus características fundamentales son el pilar sobre el cual se construye la confiabilidad y eficiencia de estos equipos críticos en la industria del petróleo y gas. A continuación, se profundiza en estas características esenciales:
- Diseño y construcción: La norma especifica criterios detallados para el diseño térmico y mecánico. En el aspecto térmico, establece cómo deben calcularse las cargas, la transferencia de calor y la caída de presión, asegurando que el intercambiador cumpla con los requisitos operativos específicos y maneje eficientemente las variaciones de temperatura y presión. En cuanto al diseño mecánico, la API 660 proporciona directrices sobre dimensiones, tolerancias y métodos de construcción, asegurando que cada componente pueda soportar las condiciones operativas sin fallar. Esto incluye especificaciones para placas de tubo, carcasas, cabezales y otros componentes críticos, considerando factores como la expansión térmica y las vibraciones.
- Selección de materiales: La elección adecuada de materiales es crucial para garantizar la durabilidad y seguridad de los intercambiadores de calor. La API 660 ofrece una guía detallada sobre los materiales adecuados para diferentes entornos operativos, teniendo en cuenta factores como la resistencia a la corrosión, la capacidad para soportar altas temperaturas y presiones, y la compatibilidad con los fluidos procesados. Esto asegura que los materiales seleccionados no solo prolongarán la vida útil del intercambiador, sino que también mantendrán su integridad estructural bajo condiciones adversas.
- Inspección y pruebas: Para garantizar que los intercambiadores de calor cumplen con los estándares de calidad y seguridad, la API 660 establece protocolos rigurosos de inspección y pruebas. Esto incluye pruebas no destructivas para detectar defectos ocultos, pruebas hidrostáticas para verificar la resistencia bajo presión y pruebas de rendimiento para asegurar que el intercambiador cumple con los criterios de diseño. Estas inspecciones y pruebas son esenciales para identificar y corregir cualquier problema antes de que el equipo sea puesto en servicio, minimizando así el riesgo de fallas operativas y accidentes.
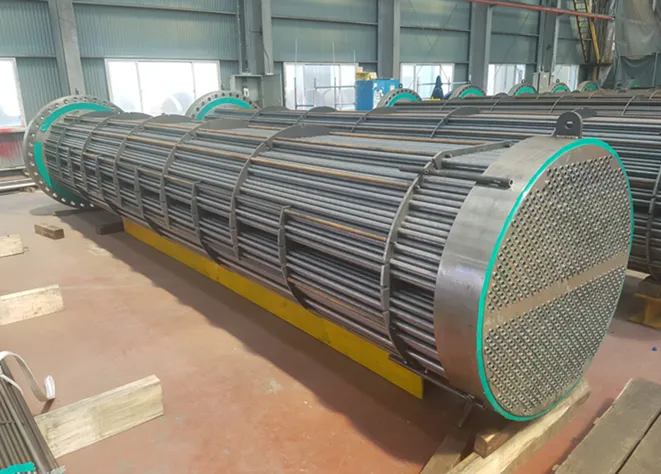
Tipos de inspección y pruebas
La norma API 660 establece una serie de inspecciones y pruebas rigurosas para garantizar la calidad, seguridad y rendimiento de los intercambiadores de calor de tubo y carcasa. Estas inspecciones y pruebas son cruciales para verificar que los intercambiadores cumplan con los estándares establecidos y funcionen de manera segura y eficiente en sus entornos operativos. A continuación, se detallan algunos de los tipos de inspección y pruebas más relevantes según la norma API 660:
Inspección visual y dimensional
- Visual: Se realiza una inspección visual detallada de todas las partes del intercambiador de calor para identificar cualquier defecto superficial, como grietas, corrosión o deformaciones.
- Dimensional: Se verifica que todas las dimensiones del intercambiador de calor cumplan con las especificaciones de diseño. Esto incluye la longitud, el diámetro, el espesor de las placas y tubos, y la alineación de los componentes.
Pruebas no destructivas (NDT)
- Radiografía o ultrasonido: Se utilizan para detectar defectos internos, como fisuras o inclusiones en soldaduras y materiales. Estas pruebas son esenciales para asegurar la integridad estructural del intercambiador.
- Prueba de partículas magnéticas: Se aplica a materiales ferromagnéticos para identificar discontinuidades superficiales y subsuperficiales.
- Prueba de líquidos penetrantes: Se utiliza para detectar fisuras y defectos en la superficie de los materiales no porosos.
- Pruebas de corrientes inducidas (ECT): Especialmente útil para inspeccionar tubos de intercambiadores de calor, esta prueba detecta fisuras, corrosión, y otros defectos superficiales y subsuperficiales en los materiales conductores. Funciona al inducir un campo magnético en el material y luego medir la respuesta, lo que permite identificar anomalías.
- Termografía infrarroja: Utiliza cámaras infrarrojas para detectar y medir la radiación térmica de una superficie. Las diferencias en la emisión de calor pueden indicar problemas como fugas, bloqueos o áreas de degradación.
- Ensayo por ultrasonido de fase (phased array): Una versión avanzada de la prueba de ultrasonido tradicional que utiliza múltiples elementos piezoeléctricos para controlar la dirección y el enfoque del haz de sonido. Esto permite una inspección más detallada y la capacidad de mapear y dimensionar defectos con alta precisión.
- Inspección visual remota (RVI): Utiliza dispositivos como endoscopios o cámaras en miniatura para inspeccionar visualmente áreas que son inaccesibles o difíciles de alcanzar. Es útil para verificar internamente tubos, soldaduras y componentes.
- Emisión acústica: Detecta las ondas de sonido de alta frecuencia emitidas por la estructura bajo estrés. Las emisiones acústicas pueden indicar la presencia de grietas o fracturas en desarrollo.
- Inspección por microondas: Utiliza ondas de radiofrecuencia para detectar cambios en las propiedades del material, como la presencia de corrosión, delaminaciones o agua atrapada.
- Ensayos de replicado metalográfico: Involucra la toma de impresiones de la microestructura del material en el sitio. Estas impresiones se analizan luego bajo un microscopio para evaluar la degradación, como la corrosión, la fatiga o los cambios microestructurales.
- Espectroscopía de emisión óptica: Analiza la luz emitida por una muestra cuando está excitada por una fuente de energía. Es útil para determinar la composición química y, por ende, la calidad y el tipo de material.
- El ultrasonido por I.R.I.S. (internal rotary inspection system): Es una técnica avanzada de ensayo no destructivo que utiliza un transductor ultrasónico rotativo para inspeccionar la integridad interna de tubos en intercambiadores de calor y calderas. Durante la inspección, los tubos se llenan de agua como medio para las ondas ultrasónicas, y el transductor, al girar y desplazarse a lo largo del tubo, emite ondas que penetran la pared del tubo y se reflejan de vuelta, permitiendo detectar y cuantificar defectos como corrosión, erosión, picaduras y grietas con alta precisión. Esta técnica ofrece una evaluación detallada y precisa, siendo capaz de identificar una amplia gama de deterioros y proporcionar registros visuales y cuantitativos para el seguimiento a lo largo del tiempo, aunque requiere tubos limpios y puede tener limitaciones en tubos con curvas pronunciadas o configuraciones complejas.

Pruebas hidrostáticas
- Prueba de presión de la carcasa y los tubos: Se realiza para verificar la resistencia y la ausencia de fugas en la carcasa y los tubos. Consiste en llenar el intercambiador con un líquido, generalmente agua, y presurizarlo a un valor superior al de operación para asegurar que no existen fugas ni deformaciones.
Pruebas de rendimiento
- Prueba de transferencia de calor: Se verifica que la tasa de transferencia de calor del intercambiador cumpla con las especificaciones de diseño.
- Prueba de caída de presión: Se asegura que la caída de presión a través del intercambiador no exceda los límites establecidos, lo que podría indicar obstrucciones o problemas de diseño.
Inspección de materiales
- Análisis químico y pruebas mecánicas: Se realizan para confirmar que los materiales utilizados en la construcción del intercambiador cumplan con las especificaciones de la norma en términos de composición química y propiedades mecánicas.
Pruebas de limpieza
- Inspección de limpieza: Se verifica que los intercambiadores estén libres de contaminantes, residuos de fabricación o corrosión antes de la puesta en servicio.
Cada una de estas pruebas e inspecciones es vital para asegurar que los intercambiadores de calor no solo cumplan con los estándares de diseño y fabricación, sino que también operen de manera segura y eficiente a lo largo de su vida útil. La norma API 660 proporciona directrices detalladas sobre cómo deben realizarse estas pruebas, los criterios de aceptación y las calificaciones que deben tener los inspectores y técnicos que las llevan a cabo.
Evolución y actualizaciones detalladas de la norma API 660
La API 660 ha experimentado transformaciones significativas, adaptándose a los avances tecnológicos y las necesidades cambiantes de la industria.
Mejoras en diseño
- Diseño térmico avanzado: Las revisiones han integrado métodos de diseño térmico avanzados, utilizando software de simulación para predecir el rendimiento y permitiendo diseños más eficientes y adaptados a necesidades específicas.
- Diseño mecánico innovador: La adopción de análisis por elementos finitos (FEA) ha mejorado la evaluación de la resistencia y durabilidad, optimizando la integridad estructural y extendiendo la vida útil del equipo.
Enfoque en la sostenibilidad
- Eficiencia energética: La norma ahora pone un énfasis especial en la eficiencia energética, promoviendo la optimización del intercambio térmico y la reducción de la pérdida de calor.
- Reducción de emisiones: Se han incorporado directrices para minimizar las emisiones nocivas, alineándose con regulaciones ambientales y promoviendo prácticas sostenibles.
Avances en materiales
- Nuevos materiales y aleaciones: La inclusión de materiales avanzados ha sido crucial, ofreciendo mayor resistencia a condiciones adversas y prolongando la vida útil de los intercambiadores.
- Vida útil prolongada: Estos materiales no solo mejoran la resistencia a la corrosión, sino que también reducen la necesidad de mantenimiento y reemplazos costosos.
Integración de tecnologías digitales
- Simulación y modelado: Herramientas de simulación y modelado computacional se han integrado para optimizar el diseño, permitiendo análisis detallados y mejoras en el rendimiento.
- Diseño asistido por computadora (CAD): El uso de software CAD facilita la creación de modelos detallados, agilizando el proceso de diseño y permitiendo ajustes eficientes.
Implicaciones de las últimas actualizaciones
Las últimas actualizaciones en la norma API 660 tienen implicaciones profundas y transformadoras para la industria del petróleo y gas, reflejando avances tecnológicos y un compromiso renovado con la eficiencia, la sostenibilidad y la seguridad.
Estas revisiones no solo incorporan métodos de diseño más sofisticados y materiales avanzados que mejoran la resistencia a condiciones extremas y prolongan la vida útil de los intercambiadores de calor, sino que también enfatizan la importancia de la eficiencia energética y la reducción de emisiones nocivas, alineándose con las regulaciones ambientales globales y las iniciativas de sostenibilidad.
La integración de tecnologías digitales como el modelado computacional y el diseño asistido por computadora (CAD) permite una precisión sin precedentes en el diseño y la fabricación, facilitando la detección temprana de posibles problemas y la personalización según las necesidades específicas de operación.
Estas actualizaciones no solo elevan el estándar de calidad y seguridad en los intercambiadores de calor, sino que también preparan a las empresas para enfrentar desafíos futuros, asegurando que sus productos y prácticas no solo cumplan con las exigencias actuales, sino que también estén a la vanguardia de la innovación y la responsabilidad ambiental.
Conclusión
La norma API 660 es un testimonio viviente de la evolución de la ingeniería y la tecnología en el sector industrial. Su continua actualización no solo asegura que los intercambiadores de calor cumplan con las exigencias actuales, sino que también estén preparados para los desafíos del futuro. Como profesionales en este campo, es nuestra responsabilidad mantenernos informados y adaptarnos a estas normativas, garantizando así la excelencia y seguridad en nuestros proyectos.
Referencias
Fuente propia