Tabla de Contenidos
- ¿Qué son los puntos muertos en sistemas de tuberías?
- Impacto del punto muerto en la eficiencia del sistema
- Importancia de la evaluación de condiciones en los puntos muertos
- Inspección de puntos muertos en equipos industriales
- Materiales para control de corrosión en puntos muertos
- Estrategias para la gestión y control de puntos muertos
- Conclusiones
- Referencias
Introducción
En los sistemas de tuberías industriales, los “puntos muertos” representan un reto significativo para la integridad y el desempeño eficiente de las instalaciones. Se presentan en secciones de la tubería donde el flujo de fluidos es mínimo o inexistente, favorecen la acumulación de depósitos, productos de corrosión y otros contaminantes que comprometen la confiabilidad operativa del sistema.
La identificación y gestión adecuada de los puntos muertos es significativa en la prevención de fallas, con el fin de prolongar la vida útil de los equipos. En este contexto, el presente artículo aborda la definición, los riesgos asociados, las metodologías de inspección y las estrategias de gestión orientadas a preservar la integridad de los sistemas industriales.
¿Qué son los puntos muertos en sistemas de tuberías?
Un punto muerto es una sección de un sistema de tuberías donde el flujo de fluidos es esporádico o inexistente. Aunque estas áreas no participan activamente en el transporte de fluidos, siguen estando expuestas a los mismos factores que el resto del sistema, como la corrosión, el ataque químico y la acumulación de residuos. Estos tramos de tuberías se encuentran principalmente en ramas bloqueadas, líneas con válvulas cerradas o tuberías con extremos cegados.
Los puntos muertos se forman cuando un sistema de tuberías incluye secciones donde el flujo de fluidos no es continuo, pero estas áreas siguen expuestas a las condiciones operativas del proceso. Aunque no están en uso activo, son vulnerables a problemas como la corrosión localizada, la acumulación de sedimentos y la formación de depósitos de productos químicos. Esto ocurre porque los contaminantes en los fluidos se estancan y no son arrastrados por un flujo constante, lo que incrementa el riesgo de degradación del material y, en última instancia, de fallos estructurales.
Los puntos muertos se pueden encontrar en varias ubicaciones dentro de los sistemas de tuberías industriales. Ejemplos comunes incluyen:
- Ramas bloqueadas: Secciones de tuberías que no están conectadas a un flujo activo y que terminan en una obstrucción física.
- Líneas con válvulas de bloqueo cerradas: Secciones que quedan aisladas cuando se cierran las válvulas de paso de fluidos.
- Tuberías con extremos cegados: Zonas en las que no hay salida de flujo, como en derivaciones de válvulas de control o alrededor de equipos auxiliares.
Estos puntos muertos son comunes en industrias químicas, petroquímicas y de generación de energía, donde el diseño complejo de los sistemas puede dar lugar a estas áreas inadvertidas si no se consideran cuidadosamente durante la planificación. Los puntos muertos pueden parecer inofensivos, pero debido a la acumulación de productos corrosivos y al estancamiento, pueden desencadenar problemas graves si no se gestionan de manera adecuada.
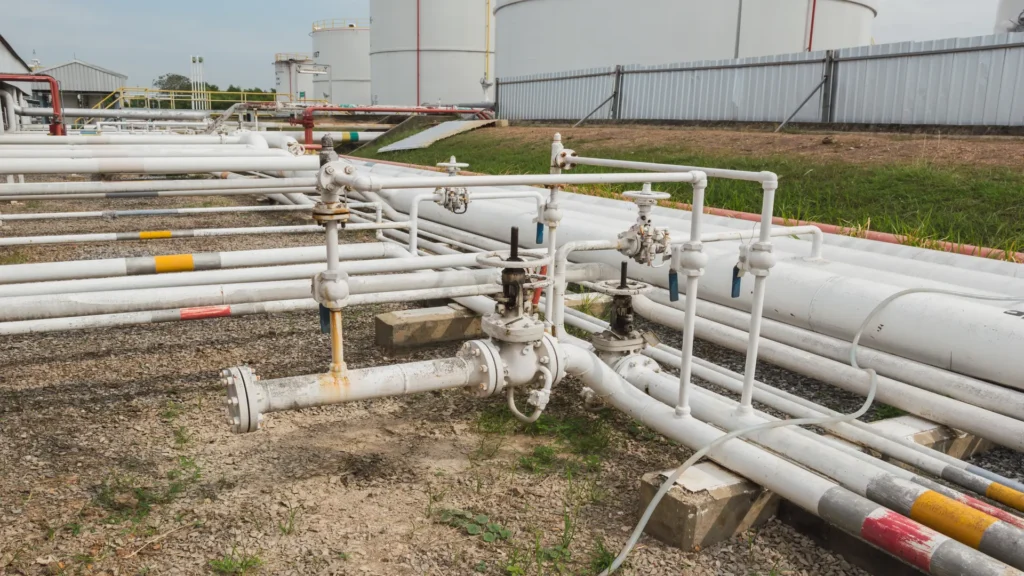
A continuación se presenta el siguiente video donde se muestra una breve introducción sobre tramos muertos en tuberías, consecuencias, selecciones de TML y métodos NDT. Cortesía de: Inspection Academy.

Puntos muertos en tuberías.
Impacto del punto muerto en la eficiencia del sistema
El punto muerto, además de ser un riesgo para la integridad estructural de los sistemas de tuberías industriales, tiene un impacto significativo en la eficiencia operativa. En los sistemas donde el flujo de los fluidos es intermitente o inexistente, las áreas estancadas tienden a acumular sedimentos, partículas y productos químicos. Esta acumulación genera una serie de problemas que afectan directamente el rendimiento del sistema, tales como:
- Pérdidas de presión en el sistema: Las obstrucciones en los puntos muertos pueden causar una caída de presión, lo que obliga a las bombas a trabajar más para mantener el flujo, incrementando el consumo energético.
- Reducción en la eficiencia del transporte de fluidos: Los depósitos en los puntos muertos pueden alterar la dinámica del fluido, reduciendo la eficiencia general del transporte de productos a través del sistema.
- Costos de operación más altos: Los sistemas de tuberías con puntos muertos requieren un monitoreo más frecuente y mantenimiento preventivo intensivo, lo que puede aumentar los costos operativos.
Estos problemas se pueden mitigar mediante la evaluación y monitoreo continuos del punto muerto, utilizando tecnologías avanzadas como sensores en tiempo real que detectan cambios en la presión y acumulación de sedimentos. En última instancia, la identificación temprana y el control proactivo de estos puntos críticos ayudarán a mantener la eficiencia del sistema, minimizar el tiempo de inactividad y reducir los costos de energía.
Importancia de la evaluación de condiciones en los puntos muertos
Riesgos asociados
Los puntos muertos son áreas de alto riesgo debido a su predisposición a la corrosión localizada, la acumulación de contaminantes y el crecimiento microbiológico. En sistemas donde se manejan fluidos corrosivos o con propiedades químicas agresivas, estos puntos vulnerables pueden extenderse a otras partes del sistema si no se detecta y trata a tiempo.
Además, la acumulación de depósitos y la proliferación de bacterias en los puntos muertos pueden contaminar los fluidos del proceso y afectar la calidad del producto, especialmente en industrias sensibles como la alimentaria o farmacéutica. A largo plazo, estas condiciones pueden llevar a fallos catastróficos, afectando tanto la seguridad operativa como la confiabilidad del equipo.
Formación microbiológica en los puntos muertos
Otro riesgo significativo asociado con los puntos muertos es la formación de microorganismos, especialmente en sistemas que transportan agua u otros fluidos orgánicos. La corrosión microbiológicamente influenciada (MIC) ocurre cuando ciertos tipos de bacterias proliferan en áreas estancadas, generando subproductos que aceleran la corrosión de los materiales metálicos. Este fenómeno es común en sistemas donde las condiciones estancadas y anaeróbicas favorecen el crecimiento de biofilms.
¿Por qué es preocupante la formación microbiológica?
- Aceleración de la corrosión: La actividad microbiológica genera ácidos y otros compuestos corrosivos que atacan directamente la estructura de las tuberías, lo que puede provocar la formación de agujeros o grietas en menos tiempo del esperado.
- Contaminación del producto: En industrias como la alimentaria, petroquímica y farmacéutica, la formación microbiológica en los puntos muertos puede llevar a la contaminación del producto final, arriesgando tanto la calidad del producto como la seguridad del consumidor.
Soluciones
- Implementar programas de limpieza y descontaminación periódica en áreas propensas a la formación de biofilms.
- Usar revestimientos antimicrobianos en los puntos muertos, que inhiban el crecimiento de bacterias y microorganismos.
- Monitorear la presencia de bacterias mediante técnicas de análisis de agua y biofilms, especialmente en zonas de difícil acceso.
Beneficios de la evaluación periódica
La inspección regular de los puntos muertos es crucial para mitigar los riesgos asociados con la corrosión y la acumulación de sedimentos. Mediante evaluaciones periódicas, es posible identificar problemas en etapas tempranas, lo que permite tomar medidas preventivas antes de que los problemas se agraven.
Un enfoque proactivo en la gestión de los puntos muertos también contribuye a extender la vida útil del equipo, minimizar los tiempos de inactividad no planificados y reducir los costos operativos. Además, la implementación de estrategias de monitoreo continuo puede garantizar que se detecten los cambios en las condiciones de los puntos muertos en tiempo real, permitiendo a los operadores realizar intervenciones oportunas y eficaces.
Inspección de puntos muertos en equipos industriales
Inspección visual y técnicas tradicionales
El primer paso en la evaluación de los puntos muertos es la inspección visual. Esta técnica, aunque básica, sigue siendo valiosa para identificar problemas evidentes, como daños superficiales, signos visibles de corrosión o acumulación de depósitos. Sin embargo, dado que los puntos muertos a menudo se encuentran en áreas de difícil acceso, las técnicas de inspección tradicionales son igualmente importantes.
Métodos como la radiografía industrial y la ultrasonografía permiten evaluar el estado interno de las tuberías sin necesidad de desmontar los sistemas. El uso de ultrasonido, por ejemplo, es especialmente útil para medir el grosor de las paredes de las tuberías y detectar cualquier indicio de corrosión interna. Estas técnicas permiten obtener datos cruciales sin interrumpir las operaciones normales del sistema.
Tecnologías avanzadas
Las nuevas tecnologías han transformado la manera en que se inspeccionan los puntos muertos. rones equipados con cámaras de alta resolución y sensores térmicos se utilizan cada vez más para inspecciones en áreas de difícil acceso o en zonas peligrosas. Los drones permiten realizar inspecciones remotas con mayor seguridad, proporcionando imágenes detalladas y datos precisos sin exponer al personal a riesgos innecesarios.
La termografía infrarroja es una herramienta avanzada utilizada para detectar cambios de temperatura en las tuberías, lo que puede indicar problemas de corrosión interna o obstrucciones. La tecnología de corrientes inducidas es otra técnica avanzada que se emplea para detectar defectos microscópicos y áreas con altos niveles de corrosión antes de que se conviertan en problemas críticos. Estas tecnologías permiten una evaluación más profunda y precisa, facilitando la toma de decisiones más informadas en relación con el mantenimiento y las reparaciones.
Materiales para control de corrosión en puntos muertos
Una solución fundamental para mitigar el riesgo en los puntos muertos es la elección de materiales resistentes a la corrosión. Debido a su exposición continua a productos químicos y condiciones estancadas, los puntos muertos son altamente susceptibles a la corrosión acelerada.
Para abordar este problema, es esencial seleccionar materiales que ofrezcan mayor durabilidad y resistencia en ambientes hostiles. Esto es especialmente relevante en situaciones donde la corrosión, como la que ocurre en tuberías enterradas o en zonas estancadas dentro del sistema de tuberías, puede acelerar la degradación del equipo.
Materiales recomendados
- Acero inoxidable: Un material altamente resistente a la corrosión, utilizado ampliamente en la industria química y petroquímica. Su capacidad para resistir la oxidación lo hace ideal para su uso en puntos muertos en sistemas que transportan fluidos corrosivos.
- Aleaciones de níquel: Estas aleaciones son extremadamente resistentes a la corrosión, especialmente en presencia de ácidos y ambientes altamente agresivos.
- Plásticos avanzados y compuestos: En ciertos sistemas, los plásticos reforzados con fibra o materiales compuestos no metálicos pueden ser una opción viable para prevenir la corrosión. Estos materiales no se ven afectados por la oxidación y pueden ser más económicos que las aleaciones metálicas.
- Revestimientos protectores: En sistemas donde la sustitución de materiales no es viable, se pueden aplicar revestimientos internos resistentes a la corrosión, como epóxicos o polímeros, para proteger los puntos muertos de los efectos corrosivos. Estos revestimientos deben ser inspeccionados regularmente para asegurar su efectividad a lo largo del tiempo.
Estrategias para la gestión y control de puntos muertos
1. Eliminación y reducción: La mejor estrategia para gestionar los puntos muertos es prevenir su formación desde la fase de diseño del sistema de tuberías. Además, cuando no es posible eliminarlos, se pueden implementar procedimientos de aislamiento o drenaje regular para minimizar los efectos adversos. Estas medidas preventivas mejoran no solo la integridad estructural del sistema, sino que también reducen los costos de mantenimiento preventivo a largo plazo.
En sistemas ya instalados, la modificación del diseño o la eliminación de tuberías innecesarias puede reducir significativamente el riesgo de corrosión y otros problemas. Cuando no es posible eliminar los puntos muertos, se pueden implementar procedimientos de aislamiento o drenaje regular para minimizar los efectos adversos. Estas medidas preventivas mejoran no solo la integridad estructural del sistema, sino que también reducen los costos de mantenimiento a largo plazo.
2. Monitoreo continuo: Sistemas de sensores avanzados pueden rastrear parámetros como la corrosión, la presión y la temperatura en tiempo real, proporcionando alertas tempranas cuando las condiciones cambian. Esto permite tomar decisiones más informadas sobre el mantenimiento preventivo del sistema y prevenir fallas, tal como se aplica en programas de Inspección Basada en Riesgo (IBR) para tanques atmosféricos. Al utilizar estos sistemas, los operadores pueden detectar problemas antes de que se conviertan en fallas importantes, lo que mejora la confiabilidad y eficiencia del sistema en general.
3. Cumplimiento de normas y estándares: La implementación de protocolos de mantenimiento preventivo específicos para los puntos muertos es esencial para garantizar la integridad del sistema a largo plazo. Estos protocolos deben incluir planes de inspección regular, limpieza y el reemplazo o reparación de tuberías según sea necesario. Estas normativas como las API 570 y API 1169 son fundamentales para garantizar la seguridad operativa y prevenir sanciones regulatorias.
Normas aplicables
- API 570 (American Petroleum Institute): Esta norma establece los requisitos para la inspección, reparación y mantenimiento de sistemas de tuberías en instalaciones de procesamiento de hidrocarburos. Los puntos muertos, como parte de estos sistemas, deben ser inspeccionadas siguiendo estos lineamientos.
- ASME B31.3 (American Society of Mechanical Engineers): Proporciona criterios para el diseño y construcción de sistemas de tuberías a presión. Los puntos muertos deben ser consideradas en el diseño para evitar la formación de puntos críticos de corrosión.
- NACE MR0175/ISO 15156: Define los criterios de selección de materiales resistentes a la corrosión para sistemas expuestos a ambientes con sulfuro de hidrógeno (H₂S). En puntos muertos, donde los depósitos pueden agravar los efectos de este gas corrosivo, el cumplimiento de esta norma es vital.
4. Cumplimiento regulatorio: Además de cumplir con los estándares de diseño y operación, las empresas deben implementar programas de inspección y monitoreo que cumplan con estas normativas. El incumplimiento puede resultar en sanciones, aumento de primas de seguro o, en el peor de los casos, fallas catastróficas que podrían haber sido evitadas.
5. Protocolos de mantenimiento: La implementación de protocolos de mantenimiento preventivo específicos para los puntos muertos es esencial para garantizar la integridad del sistema a largo plazo. Estos protocolos deben incluir planes de inspección regular, limpieza y el reemplazo o reparación de tuberías según sea necesario. También es importante personalizar los programas de mantenimiento en función de las características de cada sistema de tuberías, asegurando que todos los puntos muertos se gestionen adecuadamente.
Conclusiones
Los puntos muertos en los sistemas de tuberías industriales representan riesgos críticos para la seguridad y el rendimiento operativo, que, si se ignoran, pueden desencadenar fallos catastróficos. La acumulación de corrosión, sedimentos y contaminación en estas áreas, donde el flujo es mínimo o inexistente, puede comprometer tanto la integridad estructural como la eficiencia del sistema. Por lo tanto, es imperativo adoptar estrategias integrales que combinen la inspección avanzada, el monitoreo continuo con tecnologías como drones y sensores en tiempo real, y la implementación de materiales resistentes a la corrosión para mitigar estos riesgos.
Cumplir con normativas internacionales como API 570 y ASME B31.3 y desarrollar programas de mantenimiento preventivo personalizados es fundamental para garantizar la integridad a largo plazo de los sistemas de tuberías. Estas medidas permiten identificar problemas antes de que se conviertan en fallas mayores, mejorando la confiabilidad y reduciendo los costos operativos.
En un contexto donde la eficiencia y la seguridad son esenciales, el control proactivo de los puntos muertos no solo protege los activos industriales, sino que también asegura la sostenibilidad y rentabilidad operativa. Gestionar adecuadamente estas áreas es una prioridad estratégica que garantizará operaciones más seguras, eficientes y productivas en el futuro.
Referencias
- Amer, M. (2016, Noviembre–Diciembre). Dead‑Leg Integrity Management System. Inspectioneering Journal. Describe un enfoque sistemático para evaluar y prevenir la corrosión en puntos muertos, según estándares API 571 y API 574. onepetro.org+9store.ampp.org+9onepetro.org+9store.ampp.org+3inspectioneering.com+3twi-global.com+3
- Lee, C.‑M. (2019). Dead‑leg inspection for onshore and offshore facilities. TWI. Presenta una metodología basada en evaluación de riesgo y uso de técnicas END para la gestión de conectores sin flujo.