La corrosión es uno de los principales factores de deterioro de las infraestructuras metálicas enterradas o sumergidas, representando pérdidas económicas significativas en sectores como el petróleo y gas, la industria química y el suministro de agua. Para mitigar este problema, se implementan sistemas de protección catódica (PC), los cuales requieren un monitoreo continuo para garantizar su efectividad y prevenir fallas estructurales, bajo este contexto las estaciones de pruebas juegan un papel importante en la confiabilidad de los sistemas de protección catódica.
Desde el punto de vista económico, la implementación de estaciones de prueba eficaces minimiza gastos en reparaciones imprevistas y extiende la vida útil de activos críticos, favoreciendo la rentabilidad a largo plazo. Adicionalmente, en un contexto de regulación estricta en materia de seguridad industrial y medioambiental, estas estaciones permiten cumplir con normativas internacionales como NACE SP0169 e ISO 15589-1, evitando sanciones y garantizando la conformidad con estándares de calidad.
El propósito de este artículo es analizar en profundidad el diseño, instalación y mantenimiento de las estaciones de prueba de protección catódica, destacando su rol en la evaluación y control de los sistemas de PC. Asimismo, se abordarán innovaciones tecnológicas que optimizan su desempeño y contribuyen a una gestión más eficiente de la corrosión en infraestructuras críticas.
¿Qué es una estación de prueba y para qué se utiliza?
Una estación de prueba de protección catódica (PC) es un punto de monitoreo estratégico diseñado para la medición y evaluación de parámetros eléctricos en sistemas de protección catódica. Estas estaciones se instalan a lo largo de la estructura protegida (oleoductos, gasoductos, tanques, estructuras marinas, entre otras) y permiten acceder a información significativa para la validación y ajuste del sistema de PC. En la siguiente imagen se puede apreciar el poste de medición integrado al sistema de protección catódica de una tubería, (Figura 1).
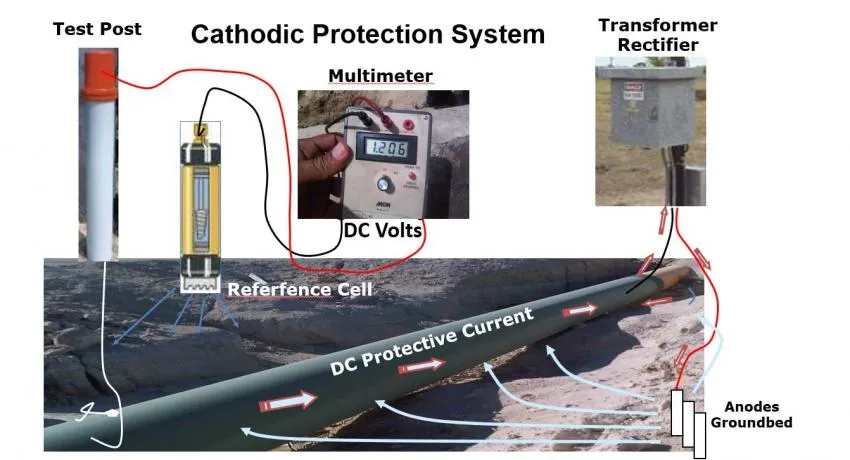
Estos dispositivos facilitan la verificación del potencial de protección, la medición de corriente, la evaluación del aislamiento y la detección de interferencias de corriente alterna (CA) y corriente continua (CC), desempeñan un papel fundamental en la gestión de la integridad de las estructuras, asegurando que el sistema de PC funcione dentro de los parámetros de diseño y cumpla con normativas como NACE SP0169 e ISO 15589-1.
Funciones principales
Las estaciones de prueba de protección catódica son dispositivos fundamentales en la gestión del buen funcionamiento de los sistemas de protección catódica, permitiendo la medición y evaluación de parámetros como el potencial de protección, la corriente de protección y la integridad del aislamiento ( figura 2). Su correcta instalación y mantenimiento aseguran la vida útil de las estructuras protegidas, y reducen costos operativos al disminuir intervenciones correctivas y evitar pérdidas por fugas, rupturas o fallas en la infraestructura.
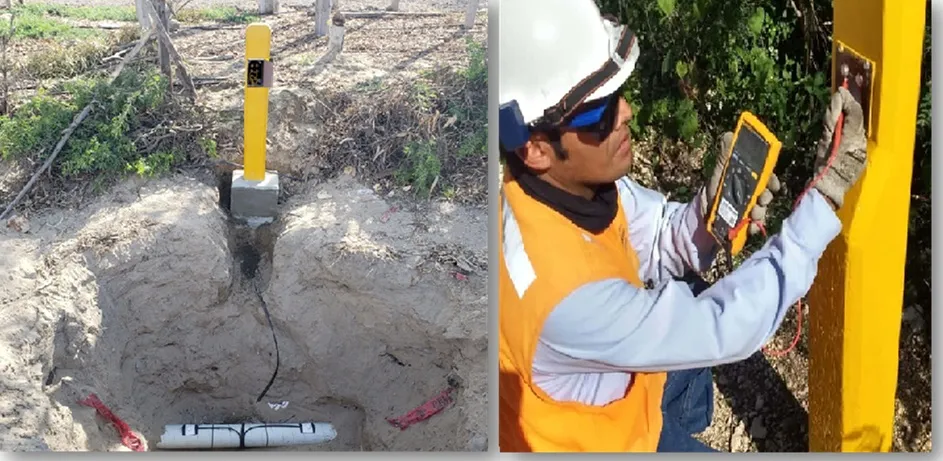
Las estaciones de prueba cumplen con funciones específicas para el control y mantenimiento de los sistemas de PC:
- Medición del potencial electroquímico: Permiten evaluar el nivel de protección alcanzado en la estructura metálica en comparación con un electrodo de referencia, asegurando que se encuentra dentro del rango de protección adecuado según normativas como NACE SP0169 e ISO 15589-1.
- Monitoreo de la corriente de protección: En sistemas de corriente impresa, facilitan la medición de la corriente suministrada por el rectificador y su distribución a lo largo de la estructura.
- Verificación del rendimiento de ánodos de sacrificio: Permiten evaluar el estado y la eficiencia de ánodos galvánicos, midiendo la diferencia de potencial entre estos y la estructura protegida.
- Evaluación de la continuidad eléctrica: Ayudan a comprobar la continuidad metálica entre diferentes secciones de la estructura, evitando pérdidas de protección por desconexiones no intencionadas.
- Detección de interferencias eléctricas: Permiten identificar y cuantificar interferencias de corriente alterna (CA) y corriente continua (CC) inducidas por líneas eléctricas, ferrocarriles electrificados o sistemas de PC adyacentes.
- Inspección de recubrimientos: Mediante pruebas de detección de fugas (DCVG) o gradiente de voltaje en corriente alterna (ACVG), se puede evaluar la integridad del recubrimiento de la estructura y localizar fallas que puedan exponer el metal a la corrosión.
Componentes de una estación de prueba
Una estación de prueba típica está compuesta por los siguientes elementos:
- Caja de conexiones (borne terminal): Fabricada en materiales resistentes a la intemperie (fenólicos, polímeros reforzados o metales tratados), protege las conexiones eléctricas y permite la instalación de diferentes circuitos de prueba.
- Electrodos de referencia: Se utilizan para medir el potencial de protección de la estructura con relación a una referencia estable (ej. electrodo de cobre/sulfato de cobre en suelos o plata/cloruro de plata en ambientes marinos).
- Cables de conexión: Generalmente fabricados con conductores de cobre con aislamiento de alta resistencia, conectan la estructura protegida con la estación de prueba.
- Conectores y resistencias de medición: Permiten configurar circuitos de prueba específicos, como la medición de la caída de voltaje a través de resistencias conocidas para determinar la corriente de protección.
- Sondas de polarización (en estaciones inteligentes): Dispositivos que permiten evaluar la efectividad real de la protección catódica minimizando los errores por interferencias de corriente.
Clasificación de las estaciones de prueba
Las estaciones de prueba pueden clasificarse según diferentes criterios:
El material de construcción
- Pilas de prueba de acero: Fabricadas en acero al carbono o acero inoxidable, ofrecen alta resistencia mecánica y durabilidad.
- Pilas de prueba de cemento: Proporcionan estabilidad estructural en terrenos de alta agresividad química.
- Pilas de prueba de plástico: Generalmente fabricadas en polímeros de alta resistencia, brindan una opción ligera y resistente a la corrosión.
Según la función
- Estación de prueba de potencial: Diseñada para la medición del potencial electroquímico de la estructura protegida.
- Estación de prueba de ánodos de sacrificio: Permite la conexión y monitoreo del desempeño de ánodos galvánicos.
- Estación de prueba de corriente: Empleada para la medición de corriente en el sistema de PC.
- Estación de prueba de efecto de protección: Evalúa la continuidad de la protección a lo largo de la estructura.
- Estación de prueba inteligente: Integrada con sensores y dispositivos de adquisición de datos para monitoreo remoto y análisis en tiempo real.
Diseño e instalación de estaciones de prueba
El proceso de diseño e instalación de estaciones de prueba se inicia con un análisis detallado de los requisitos técnicos y operativos del sistema a evaluar. Para ello, se considera la capacidad de carga de las estaciones, la precisión de las mediciones requeridas y las condiciones específicas de los entornos de prueba. Posteriormente, se procede a la selección y adquisición de los equipos adecuados, como dispositivos de medición, sistemas de control y software especializado, con el objetivo de asegurar la efectividad y fiabilidad de las pruebas.
La instalación de las estaciones de prueba se lleva a cabo bajo estrictos estándares de calidad, garantizando que todos los componentes estén correctamente integrados y que los sistemas funcionen de manera óptima. Además, se incluyen pruebas preliminares para verificar que el conjunto de equipos y la infraestructura instalada cumplan con los parámetros establecidos en el diseño. Para finalizar, se realiza un proceso de capacitación del personal encargado de operar las estaciones, asegurando que puedan realizar las pruebas de manera eficiente y con el conocimiento necesario para resolver cualquier eventualidad
Procedimiento de instalación
La instalación debe garantizar una base firme y estable para evitar inclinaciones o desplazamientos. Se recomienda la utilización de postes o cajas de protección en áreas expuestas, en general en campo se utilizan los siguientes elementos una base de hormigón o concreto en la cual va inserto un tubo de 1.5 m galvanizado o cincado; en la parte superior del tubo se coloca una pequeña caja de modelos distintos donde se conectan los cables de las estructuras enterradas. En la figura 3, se ilustra una representación esquemática del proceso de instalación.
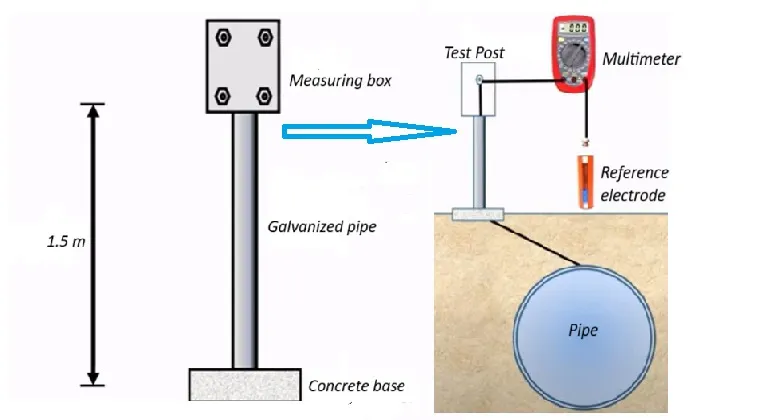
La instalación debe garantizar una base firme y estable para evitar inclinaciones o desplazamientos. Se recomienda el uso de postes o cajas de protección en las zonas expuestas. El procedimiento general incluye:
- Selección del emplazamiento: Se elige un punto representativo donde la medición refleje con precisión el comportamiento del sistema de PC.
- Preparación del terreno: Se acondiciona el área para asegurar una base estable, evitando zonas propensas a deslizamientos o acumulación de agua.
- Instalación de la pila de prueba: Dependiendo del material seleccionado, se entierra o fija sobre una base de hormigón para garantizar estabilidad.
- Conexión de cables: Se conectan los conductores de medición a la estructura protegida, asegurando continuidad y evitando falsos contactos.
- Montaje de caja de bornes: Se instala una caja resistente a la intemperie con terminales accesibles para facilitar la toma de mediciones.
- Pruebas iniciales: Se realizan mediciones de referencia para verificar el correcto funcionamiento de la estación de prueba antes de su puesta en operación.
Mantenimiento y verificación de estaciones de prueba
El mantenimiento adecuado de las estaciones de prueba es esencial para asegurar el funcionamiento continuo y efectivo del sistema de protección catódica. Un mantenimiento preventivo y verificaciones periódicas garantizan que las estaciones de prueba sigan proporcionando datos precisos y fiables, lo cual es clave para la protección de infraestructuras metálicas expuestas a la corrosión. Este proceso incluye una serie de actividades tanto de inspección como de medición, que deben realizarse de acuerdo con los estándares establecidos.
Primero, es fundamental realizar inspecciones visuales periódicas de la estación de prueba para comprobar la integridad de sus componentes. Esto incluye verificar que no haya daños estructurales en la caja de bornes, los cables de conexión y la pila de prueba. Las condiciones ambientales, como la humedad, la corrosión o el desgaste por exposición al clima, pueden afectar el estado físico de la estación, por lo que cualquier anomalía detectada debe corregirse de inmediato.
Un aspecto crucial del mantenimiento es la verificación de las conexiones eléctricas. Los bornes y cables de medición deben ser limpiados regularmente para evitar la acumulación de suciedad o corrosión que podría interferir con las mediciones. Es importante asegurarse de que todas las conexiones estén bien apretadas y libres de corrosión, ya que cualquier pérdida de contacto o resistencia adicional puede alterar la precisión de los datos obtenidos.
En cuanto a las mediciones, es esencial realizar mediciones de potencial de protección en puntos específicos de la estructura para comprobar que se mantiene dentro de los valores esperados. Estas mediciones deben compararse con los registros previos para detectar posibles desviaciones, lo que puede ser indicativo de un mal funcionamiento del sistema de protección. Además, es necesario verificar la resistencia de los contactos y la continuidad de los circuitos de medición, lo cual garantiza que las lecturas sean representativas del estado real de la estructura protegida.
Por último, el mantenimiento de las estaciones de prueba también debe incluir la recalibración periódica de los equipos de medición, así como la actualización de los sistemas de monitoreo si se utilizan estaciones inteligentes. Este tipo de estaciones, que incorporan dispositivos avanzados como sensores de polarización, módulos de adquisición de datos y conectividad remota, requieren un mantenimiento más detallado para asegurar que los datos se transmiten de manera correcta y oportuna.
Innovaciones tecnológicas en estaciones de prueba
En los últimos, debido a los grandes avances tecnológicos, a las estaciones de prueba de protección catódica se les han realizado cambios significativos en el diseño. Las innovaciones más recientes han mejorado la eficiencia de las mediciones y la precisión de los datos, facilitado el monitoreo remoto y la integración de sistemas de análisis en tiempo real; optimizando la gestión de la corrosión y garantizando el mantenimiento proactivo de infraestructuras críticas, reduciendo costos y mejorando la seguridad operativa.
Una de las innovaciones más destacadas es la incorporación de estaciones de prueba inteligentes, que se caracterizan por su capacidad para recopilar, procesar y transmitir datos de forma automática y remota. A diferencia de los dispositivos tradicionales, que requieren intervenciones manuales frecuentes para la medición y el análisis de los parámetros de protección catódica, las estaciones inteligentes permiten realizar monitoreos continuos sin la necesidad de personal en el sitio. Esta tecnología utiliza sensores avanzados, como sondas de polarización y electrodos de referencia, que permiten medir el potencial de protección, la corriente de protección y otros parámetros en tiempo real.
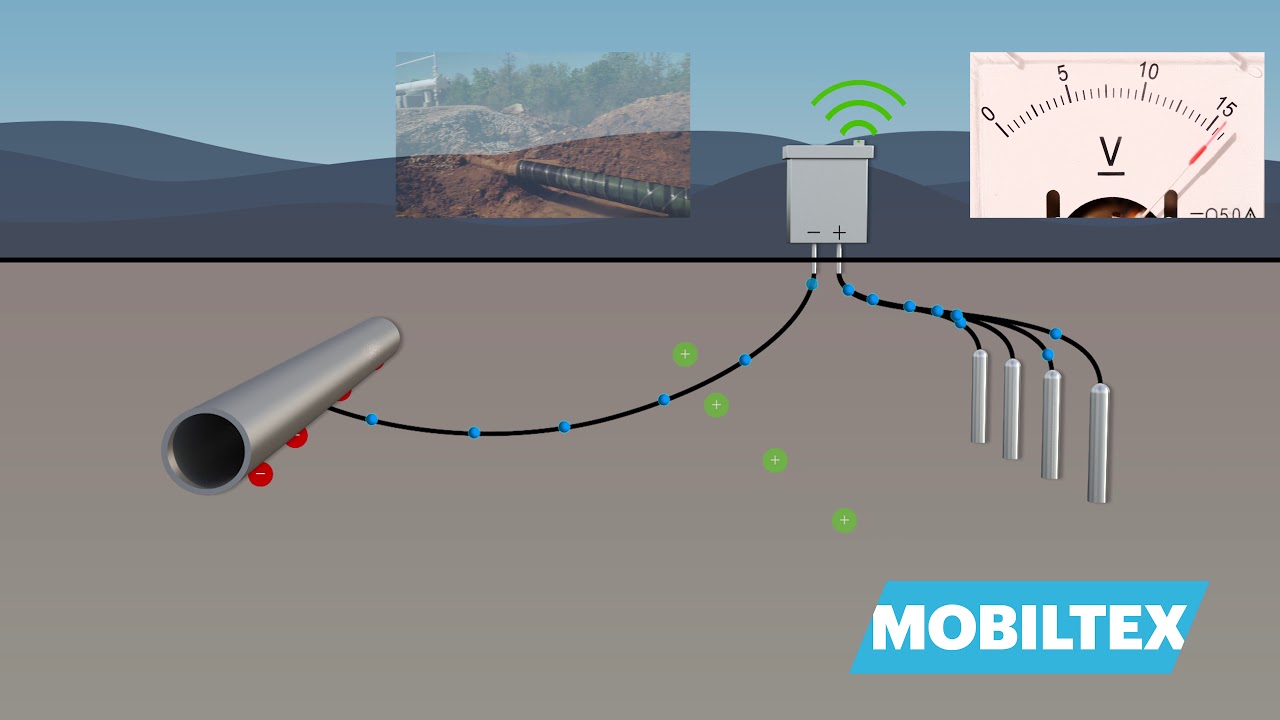
La principal ventaja de estas estaciones inteligentes es la conectividad, que se logra mediante el uso de tecnologías como GPRS, IoT y redes celulares. Esto permite que los datos de las estaciones de prueba sean accesibles desde cualquier lugar, facilitando el monitoreo remoto y la toma de decisiones informadas en tiempo real. Esta capacidad de transmitir información en tiempo real no solo mejora la eficiencia operativa, sino que también permite la detección temprana de posibles fallos o anomalías, lo que reduce la necesidad de intervenciones correctivas y permite programar mantenimientos preventivos.
Además, estas estaciones inteligentes suelen integrar módulos de adquisición de datos y sistemas de almacenamiento que procesan y almacenan la información recopilada durante el monitoreo. Esto facilita la trazabilidad de los datos a lo largo del tiempo y la generación de informes detallados, lo que optimiza la gestión y el análisis del rendimiento de los sistemas de protección catódica. Al contar con sistemas de sincronización GPS, es posible realizar un seguimiento preciso de la ubicación de cada estación, lo que resulta especialmente útil en oleoductos y gasoductos de gran longitud y en áreas de difícil acceso.
Otra innovación importante es la integración de algoritmos avanzados para el análisis predictivo. Estos algoritmos pueden evaluar los datos históricos de las estaciones de prueba y prever posibles fallos o degradaciones en el sistema de protección catódica, lo que permite implementar acciones correctivas antes de que ocurra un daño significativo. Esta capacidad predictiva representa un avance respecto a los métodos tradicionales de monitoreo, que se basan principalmente en mediciones puntuales y no cuentan con la capacidad de anticipar problemas antes de que se presenten.
Las estaciones de prueba tradicionales, aunque eficaces en su función básica de medición, requieren de una intervención manual regular para realizar lecturas y realizar las correcciones necesarias. Además, su capacidad de diagnóstico es limitada, ya que se basan principalmente en mediciones de potencial y corriente que deben ser interpretadas por personal especializado. A pesar de su fiabilidad, estas estaciones son más propensas a errores humanos, requieren más tiempo de mantenimiento y son menos eficientes en cuanto a la recopilación de datos a largo plazo.
Las estaciones de prueba inteligentes, en cambio, no solo mejoran la precisión de las mediciones, sino que también aumentan la eficiencia operativa al permitir la automatización del proceso de monitoreo. Gracias a su capacidad para realizar mediciones continuas, transmitir datos en tiempo real y analizar el rendimiento de los sistemas, estas estaciones contribuyen a una reducción significativa en los costos operativos y de mantenimiento, además de minimizar los tiempos de inactividad de las infraestructuras protegidas.
Conclusiones
La implementación de estaciones de prueba en un sistema de PC es fundamental para garantizar el monitoreo continuo del sistema y la integridad de la estructura protegida. Un diseño adecuado y un mantenimiento periódico optimizan su desempeño, asegurando el cumplimiento de los criterios de protección y prolongando la vida útil de los activos industriales.
El mantenimiento y la verificación continuos son vitales para el funcionamiento efectivo de las estaciones de prueba de protección catódica. Estas acciones no solo previenen fallos operativos, sino que también optimizan la longevidad de las infraestructuras protegidas y garantizan la conformidad con las normativas de seguridad y medioambientales.
Las innovaciones tecnológicas en las estaciones de prueba de protección catódica han marcado un antes y un después en la forma en que se gestionan y mantienen los sistemas de protección contra la corrosión. Las estaciones inteligentes, con su capacidad de monitoreo remoto, análisis predictivo y recopilación de datos en tiempo real, ofrecen ventajas clave sobre los dispositivos tradicionales, optimizando la eficiencia, reduciendo costos y mejorando la seguridad y fiabilidad de las infraestructuras críticas.
Referencias
- Barton, M. (2015). Cathodic Protection: Theory and Practice. CRC Press.
- Payer, J. H. (2015). Handbook of Cathodic Corrosion Protection (4th ed.). NACE International.
- NACE International (2018). SP0169-2018: Control of External Corrosion on Underground or Submerged Metallic Piping Systems. NACE International.