Tabla de Contenidos
- Introducción
- Importancia de la eficiencia energética en calderas industriales
- ¿Cómo se determina la eficiencia de una caldera?
- Análisis de la eficiencia en calderas industriales
- Factores que afectan el rendimiento de una caldera
- ¿Cómo mejorar el rendimiento y la eficiencia energética en calderas industriales?
- Conclusiones
- Referencias
Introducción
En la actualidad, las industrias enfrentan el problema de optimizar el uso de la energía mientras minimizan su impacto ambiental. En el centro de este objetivo se encuentra la eficiencia energética en calderas industriales, equipos diseñados para convertir agua en vapor mediante la combustión de combustibles como: fósiles, biomasa o fuentes renovables.
Este vapor, generado a presiones específicas, es utilizado en diferentes procesos industriales, incluyendo la generación de energía eléctrica, la refinación, la manufactura y la calefacción. Optimizar la eficiencia energética en calderas industriales asegura la continuidad de las operaciones, reduce los costos operativos y minimiza el impacto ambiental. Operar caldera a niveles óptimos y con la carga correcta, reduce el consumo de combustible y de las emisiones de gases de efecto invernadero, factores fundamentales para los sectores industriales.
El propósito del artículo es abordar la importancia de la eficiencia energética en calderas industriales, exponer los factores que afectan su rendimiento y ofrecer recomendaciones para mejorar el rendimiento y eficiencia energética, así como explorar las aplicaciones de nuevas tecnologías en este campo específico.
Importancia de la eficiencia energética en calderas industriales
Básicamente es definida como la eficiencia del equipo durante el proceso de conversión de la energía que contiene el combustible necesario para producir vapor. Por este motivo, los sistemas de generación de vapor exigen el mejor uso posible del combustible utilizado, con el propósito de minimizar los residuos térmicos con el consecuente aumento de la eficiencia energética.
Desde una perspectiva económica, la importancia de mantener la eficiencia de estos equipos, se fundamenta en reducir costos operativos mediante el consumo de energía; debido a que la energía que consumen representa una gran parte de los gastos de los procesos productivos. En términos ambientales, la eficiencia energética se relaciona con mejorar el perfil de las emisiones de gases de efecto invernadero, al reducir la demanda de combustibles fósiles para la generación de energía. Además, cuando las calderas operan de forma eficiente y realizan el proceso de combustión completo, se minimiza el consumo de energía y, por ende, las emisiones contaminantes.
En las calderas acuotubulares, un horno calienta el gas que circula por los tubos que contienen agua. El calor se transfiere a través de las paredes de los tubos, calentando el agua dentro de los tubos hasta que se produce vapor (figura1). Las calderas acuotubulares están diseñadas para generar considerablemente más presión que las calderas pirotubulares.
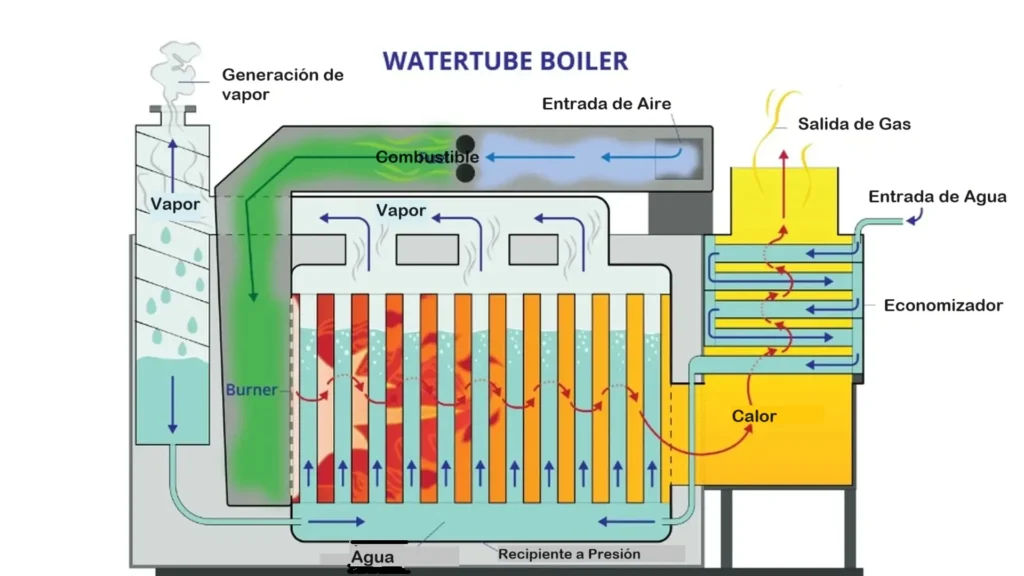
¿Cómo se determina la eficiencia de una caldera?
Para conocer la eficiencia real de una caldera, se inicia con una medición precisa de los gases de combustión emitidos por el quemador. Este sería el primer paso a ejecutar para detectar los factores que influyen en la eficiencia operativa de las calderas.
Los principales gases emitidos durante la combustión incluyen CO2 (dióxido de carbono), O2 (oxígeno) y CO (monóxido de carbono), los cuales son indicativos de la eficiencia operativa de las calderas; las altas concentraciones de CO señalan una combustión incompleta, mientras que las proporciones adecuadas de CO2 y O2 indican una combustión eficiente y completa. Por medio del monitoreo correcto de estos gases se detecta la calidad de la combustión, se conoce si el calor se está utilizando de manera eficiente y si la cantidad de aire suministrada es la ideal para el proceso.
El análisis de los gases emitidos determina la eficiencia real energética de la caldera. Es importante conocer el modelo de la caldera, combustible utilizado y procesos realizados, para facilitar la propuesta de mejoras y ajustes requeridos en caso de encontrar desviaciones durante las mediciones.
Análisis de la eficiencia en calderas industriales
La eficiencia de una caldera se mide por su capacidad para convertir la energía contenida en el combustible en calor útil durante un periodo determinado. La eficiencia térmica, es una medida común en este contexto, refleja la relación entre la cantidad de calor útil generado y la energía total consumida, expresada generalmente en porcentaje y puede variar desde un 50% hasta un 98%.
Para profundizar en el análisis de la eficiencia en calderas, se recurre al método indirecto, también conocido como método de pérdida de calor. El cual se centra en identificar y cuantificar las diversas pérdidas de calor dentro del sistema de la caldera, tales como las pérdidas por los gases de escape, pérdidas por purga, pérdidas por radiación, entre otras. Este análisis detallado identifica específicamente dónde y cómo se pierde calor, siendo un estudio requerido para conocer el análisis de la eficiencia en calderas y formular estrategias de mejora.
El siguiente video muestra cómo calcular el rendimiento de una caldera por el método indirecto y directo, especificando todos los parámetros necesarios, cortesía de Electrical Hub.
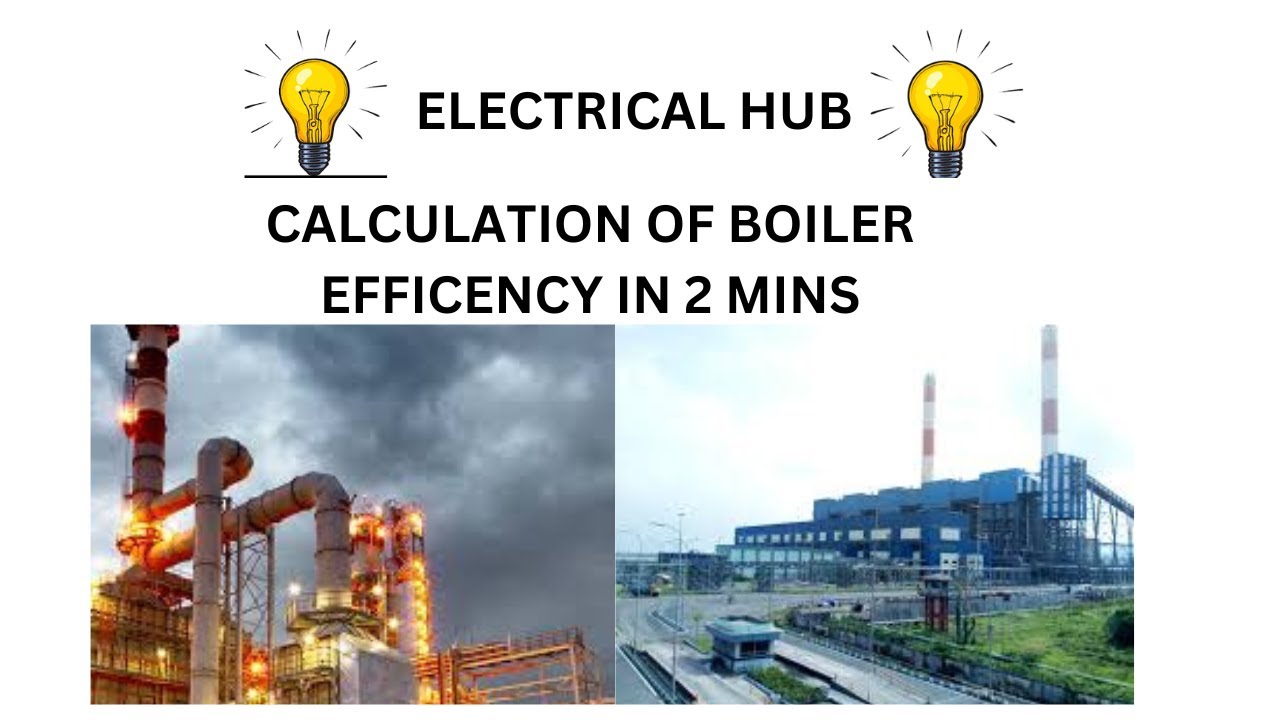
Cálculo de la eficiencia de la caldera.
Factores que afectan el rendimiento de una caldera
El rendimiento de una cadera es representado por la eficiencia con la que convierte la energía del combustible en calor útil para un proceso específico.
Este rendimiento generalmente es afectado por factores como: calidad del combustible suministrado, el cual puede contener humedad, azufre y residuos minerales; el tratamiento y la calidad del agua, así mismo influye la disposición de la atomización, que es afectada por el fraccionamiento y distribución de las gotas, la viscosidad y factores de explotación y temperatura del vapor de atomización. Otro factor es la carga térmica del horno y el tiempo de permanencia de los gases en el mismo; por otra parte, el exceso e infiltraciones de aire y los depósitos e incrustaciones sobre la superficie de transferencia de calor disminuyen la eficiencia operativa de las calderas2.
Así mismo, existen factores como la capacidad de diseño, la respuesta a las variaciones de carga, la estabilidad operativa, y la eficacia con que la caldera resisten los cambios en los parámetros de operación sin comprometer la salida del producto; del mismo modo, las fallas mecánicas, la integridad estructural y la corrosión en los componentes son factores que afectan el rendimiento.
¿Cómo mejorar el rendimiento y la eficiencia energética en calderas industriales?
El diseño y desarrollo técnico de las calderas afronta la inevitable ineficiencia energética durante los procesos, instando que incluso las más avanzadas tecnológicamente no alcanzan una eficiencia del 100% debido a pérdidas de energía. Para controlar estas pérdidas y mejorar la eficiencia, existen varias estrategias:
- Control del combustible y combustión: Un adecuado control de la combustión y emisiones mediante el uso quemadores de alta eficiencia y ajuste en la relación aire-combustible proporcionan un mejor rendimiento y controlan el desperdicio de energía. Los sistemas de control avanzados monitorean y ajustan el suministro de combustible.
- Recuperación de calor residual: Esta técnica implica la utilización de economizadores y precalentadores para capturar y reutilizar el calor de los gases de escape. Al hacerlo, se reduce la cantidad de energía térmica desperdiciada, disminuyendo las cargas térmicas y aumentando la eficiencia del proceso.
- Optimizar el sistema de distribución: Asegurar que el sistema de distribución de vapor o agua caliente esté correctamente dimensionado y aislado, minimiza las pérdidas de calor de las calderas.
- Mantenimiento e inspecciones regulares: Los mantenimientos preventivos evitan la acumulación de incrustaciones y hollín, que disminuyen la transferencia de calor y la eficiencia operativa de las calderas, en conjunto con inspecciones programadas para verificar la integridad del sistema. Por ejemplo, las inspecciones o reemplazos de trampas y bombas de retorno de condensado, evitan desperdicios de agua, maximizando la eficiencia operativa.
- Tratamiento del agua: Un adecuado control de la calidad del agua, de la concentración de sólidos en suspensión en el interior de la caldera y buenas prácticas de purgado son medidas efectivas para aumentar la eficiencia operativa de las calderas.
- Automatización de controles: Implementar controles automatizados como los sistemas de monitoreo de energía, ajustan los parámetros operativos según las necesidades de la demanda de vapor, mejorando la respuesta y eficiencia del sistema.
- Aislamiento térmico: El aislamiento reduce la pérdida de calor por convección y radiación. Es decir, aislar correctamente el exterior de la caldera, así como los accesorios y tuberías que transporten agua caliente o vapor, con el objetivo de aprovechar al máximo el calor generado.
- Gestión y recuperación del calor en los procesos de purga: La recuperación del calor en agua de purgas por medio de intercambiadores o tanques flash para reutilizar la energía y también regular la tasa de purga minimiza las pérdidas de calor y evita las impurezas y sólidos disueltos; esta acción reduce los riesgos de fallas por incrustaciones y eleva la eficiencia operativa de las calderas.
- Actualización de los sistemas de la caldera: Si la caldera tiene más de una década en servicio, es recomendable evaluar la inversión en sistemas modernos y más eficientes. Si bien, la inversión inicial será alta, los beneficios a largo plazo en términos de ahorro de energía y reducción de costos operativos compensarán la inversión.
Al implementarse estas estrategias incrementa la eficiencia operativa de las calderas y optimiza la rentabilidad, y sostenibilidad de las operaciones.
Aplicaciones de nuevas tecnologías en calderas industriales
Hoy en día, las calderas son complejas unidades integradas con la más avanzada tecnología. Los fabricantes de calderas diseñan continuamente tecnologías innovadoras que constituyen un avance en la confiabilidad y eficiencia operativa de las calderas, factores exigidos por la industria moderna para un mejor rendimiento energético. Entre las nuevas tecnologías en calderas industriales se destacan:
- Calderas de bajo consumo: Conocidas como calderas de alta eficiencia energética, se distinguen por su capacidad para aprovechar al máximo la energía del combustible, minimizando las pérdidas y convirtiendo una mayor proporción en calor útil. Alcanzan eficiencias térmicas superiores al 90%, lo que significa que más del 90% de la energía del combustible se convierte en calor útil.
- Tecnología de condensación: Las calderas de condensación recuperan el calor residual de los gases de combustión que se pierde a través de la chimenea en las calderas tradicionales. Al condensar el vapor de agua en los gases de escape, las calderas recuperan calor latente, aumentando su eficiencia energética.
- Quemadores de baja emisión (Low-NOx): Están diseñados para reducir la producción de óxidos de nitrógeno, un contaminante nocivo para el ambiente. Utilizan técnicas como la recirculación de gases de escape y la tecnología de combustión escalonada para lograr una combustión más eficiente y limpia.
- Sistemas de recuperación de calor de residuos: Están diseñados para capturar el calor de los procesos que de otra manera se perdería y lo utilizan para precalentar el agua de alimentación o para otros procesos térmicos dentro de la planta, mejorando así la eficiencia operativa de las calderas.
- Integración de energías renovables: Utilizar fuentes de energía renovable, como la biomasa, la solar o el calor geotérmico, en los sistemas de calderas reduce la dependencia de combustibles fósiles y disminuyen las emisiones de carbono.
El siguiente video muestra cómo funciona una caldera de biomasa, cortesía de HoSt Group – Bioenergy Systems.

¿Cómo funciona una central de calderas de biomasa?
- Automatización y sistemas de control inteligente: Disponer de sistemas con integración de algoritmos y sensores de última generación basados en Inteligencia Artificial, Internet de las cosas (IoT), Big Data y Aprendizaje Automático para el control inteligente de los procesos, regula las operaciones, optimizando el consumo de energía y mejorando la respuesta a las cargas cambiantes de la planta3.
- Calderas híbridas: La combinación de tecnologías de combustión con sistemas de bomba de calor ofrecen una eficiencia alta, especialmente en climas donde las condiciones cambiantes afectan el rendimiento de los sistemas tradicionales.
- Software para optimizar calderas: Existen software para evaluar los circuitos cerrados de combustible y aire en tiempo real, y todas las cargas operativas. Estos sistemas controlan las relaciones aire-combustible y la transferencia de calor entre gases de combustión y vapor, con el propósito de mejorar la productividad de la caldera, las temperaturas del vapor y las emisiones3.
- Avance en calderas electrificadas: La empresa AtmosZero ha desarrollado una de las nuevas tecnologías en calderas, que es la innovadora caldera electrificada conocida como Boiler 2.0; el cual es un sistema de bomba de calor totalmente eléctrico que produce vapor para procesos industriales a temperaturas de entre 100 y 200 °C. Utiliza un sistema en cascada que combina circuitos de baja y alta temperatura, obteniendo una eficiencia doble en comparación con otras calderas eléctricas y representa una alternativa verde para las calderas tradicionales que queman combustibles fósiles4.
Conclusiones
La eficiencia energética en calderas industriales, es una necesidad operativa, que responde a exigencias ambientales y económicas de los sectores industriales. A través del análisis de las condiciones operativas y uso de nuevas tecnologías y estrategias de gestión energética, las industrias reducen los gastos operativos y las emisiones contaminantes.
Avanzadas tecnologías como las calderas de bajo consumo, las calderas de condensación y los nuevos sistemas de recuperación de calor, junto con la integración de fuentes de energía renovable y la automatización avanzada, optimizan el rendimiento de las calderas y establecen nuevos estándares en la producción industrial sostenible. Estas innovaciones prometen maquinarias más eficientes e inteligentes que impulsan la innovación industrial y apoyan los objetivos climáticos globales, destacándose en un mercado cada vez más enfocado en el desempeño ecológico.
Referencias
- https://miuraboiler.com/steam-boilers-101/. Consultado el 27 de mayo 2024
- https://slideplayer.es/slide/2269282/. Consultado el 22 de mayo 2024
- https://www.ge.com/digital/applications/operations-performance-management-opm/boiler-plant-optimization-steam-plant-efficiency. Consultado el 21 de mayo 2024
- https://ecoinventos.com/startup-desarrolla-nueva-bomba-de-calor-alimentada-por-aire-que-genera-vapor-para-uso-industrial/#AtmosZero_innovacion_en_calderas_electrificadas. Consultado el 23 de mayo 2024.