Los tanques de almacenamiento de acero al carbono, son estructuras o recipientes importantes para los procesos de operación y producción de las plantas en las áreas de petróleo, gas y petroquímica; en los cuales, se almacenan los productos que alimentan y procesan las plantas industriales como: agua potable, agua industrial, desechos, aditivos, productos terminados o semi-terminados, entre otros. los cuales, son básicos para los procesos de producción y operación, de allí la importancia de estos activos para el almacenamiento de estos productos.
Cuando se almacenan sustancias peligrosas en tanques de almacenamiento, reducir el riesgo de fugas, es crucial. La corrosión en tanques de almacenamiento puede causar fugas significativas de producto y por lo tanto contaminación del medio ambiente. Debido a este tipo de problemas, se necesita garantizar la seguridad y confiabilidad de estos activos.
Estos recipientes están conformados estructuralmente por el techo, pared y piso. De esas tres partes el piso es la sección más difícil para realizar la inspección, detectar y controlar la corrosión, eso se debe principalmente a la dificultad de acceder a esta parte.
Corrosión en pisos de tanques
La corrosión en los pisos de tanques ocurre en tres ambientes diferentes. En la parte interna donde está en contacto con el producto almacenado (gasolina, nafta, fuel oil, petróleo, agua potable, aceite, etc.), en la parte externa en contacto con el suelo y en la pestaña de la placa o plancha anular donde está expuesto a la atmosfera y el suelo (figura 1).
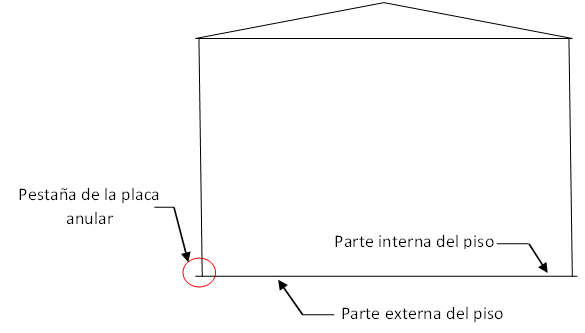
A continuación, se realiza un análisis de estos tres ambientes.
Parte interna: Para evaluar la corrosividad en la parte interna de los pisos de tanques, es importante determinar el tipo o características del producto almacenado, temperatura, agresividad química, pH, contenido sulfuros, cantidad de agua salada y arrastres de lodos, entre otros.
Después de evaluar que tan corrosivo puede ser el producto sobre el material de fabricación del piso, se define si se requiere o no protección contra la corrosión. En caso de necesitar protección, el método más usado y muy efectivo es evitar el contacto del producto y el sustrato; para lo cual, se aplican las pinturas o recubrimientos industriales más adecuados para cada caso.
Algunos productos, como los aceites, no son corrosivos; por lo tanto, no es necesario la aplicación de recubrimiento en el piso, pero se debe considerar en la evaluación, si existe la posibilidad de arrastres sólidos corrosivos en el fluido.
Como actividad preventiva de corrosión, los tanques que contengan agua salada en el producto (Ej. los crudos), deben ser drenados frecuentemente para retirar el agua que se decanta en el fondo.
Para detectar corrosión o fallas en la parte interna del piso; primeramente, se debe realizar inspección visual (VT) minuciosa a todas las planchas, soldaduras, colectores, refuerzos y recubrimientos. El resultado de esta evaluación determinará si es necesario utilizar otro método de Ensayos No Destructivos (END); como, Tintes Penetraste (PT) o Partículas Magnéticas (MT), para revelar grietas superficiales o sub-superficiales en las soldaduras, también se puede usar pruebas de fuga con caja de vacío para descartar o detectar grietas pasantes en soldaduras (figura 2), [1]. Obviamente todas las inspecciones o END mencionados anteriormente, requieren que el tanque esté fuera de servicio, limpio y desgasificado.
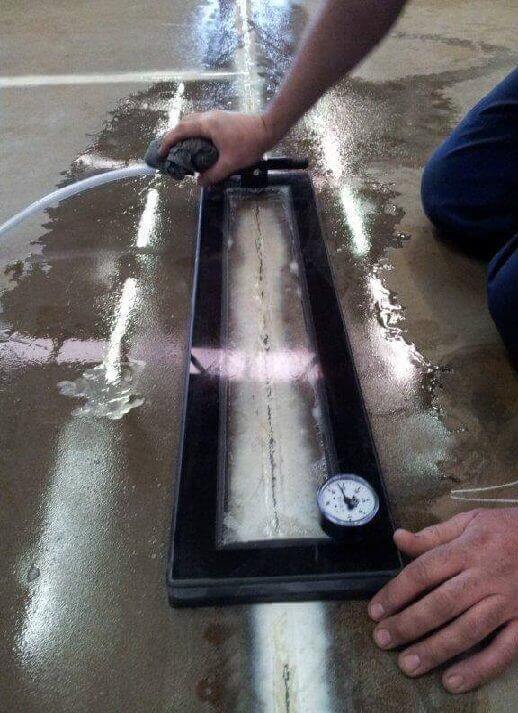
Figura 2. Representación fotográfica de una caja de vacío [1].
Parte externa: La parte externa del piso es el área que está en contacto con el suelo y para determinar la corrosividad de este ambiente hay que hacer un análisis completo del suelo, con el propósito de definir el tipo de suelo, pH, humedad, temperatura, composición química y resistividad del suelo, entre otros. Estos análisis deben realizarse con personal experto en corrosión que determinará la resistividad del suelo, la acides, el potencial rédox, si el contenido de agua favorece la corrosión electroquímica, la presencia de sulfuros, sulfatos, cloruros y elementos orgánicos, entre otros, para establecerlos controles de corrosión más adecuados.
Medidas de prevención contra la corrosión.
Después de evaluar todos estos factores y definir los mecanismos de corrosión que puedan generarse, se toman la siguiente medida de prevención contra la corrosión:
- Diseñar y construir la fundación o cimentación con materiales adecuado y libre de humedad. La selección de materiales a instalar debe ser de baja corrosividad y colocarlos en un arreglo por capas de la manera siguiente: Excavar y retirar la tierra natural del suelo, reemplazarla por una primera capa de arena dulce cernida compactada y sobre ella una capa asfáltica también compactada. Debajo de esas dos capas se debe colocar una malla geotextil impermeable no biodegradable, que impida la entrada de agua de las lluvias o del nivel freático.
- Otro tipo de cimentación a instalar pueda ser de concreto; el cual, debe ser fabricado usando arena dulce cernida
- Los diseños de las cimentaciones deben hacerse con pendientes que mantenga la cementación de forma cóncava. Para evitar la entrada de lluvia debajo del piso.
- Para aquellos casos donde la resistividad del suelo es muy baja (< 10 Ωm) donde el grado de agresividad es severo o cuando la resistividad está entre 10 Ωm – 100 Ωm, cuya agresividad es moderada, se debe instalar protección catódica, preferiblemente por corriente impresa [2].
Técnicas de monitoreo.
Para detectar corrosión o fallas en la parte externa del piso, y considerando que esa zona no es accesible, se utilizan métodos de END que permitan realizar la evaluación de condiciones desde la parte interna.
Fuga de Flujo Magnético (MFL): La técnica más utilizada y confiables para este caso, es la Fuga de Flujo Magnético (MFL, o Magnetic Flux Leakage). Con estas técnicas para materiales ferromagnéticos, se detectan las pérdidas volumétricas en las planchas, magnetizando temporalmente el componente a ser ensayado, para luego localizar las distorsiones en el flujo magnético que se producen en zonas corroídas interna y/o externamente. Los equipos utilizados para el ensayo, puede escanear más del 90 % de la superficie del fondo del tanque (figura 3)[3], y los resultados de la evaluación se presentan mediante un software, en un mapa con una variación de colores que definen las zonas críticas, (figura 4) [4].
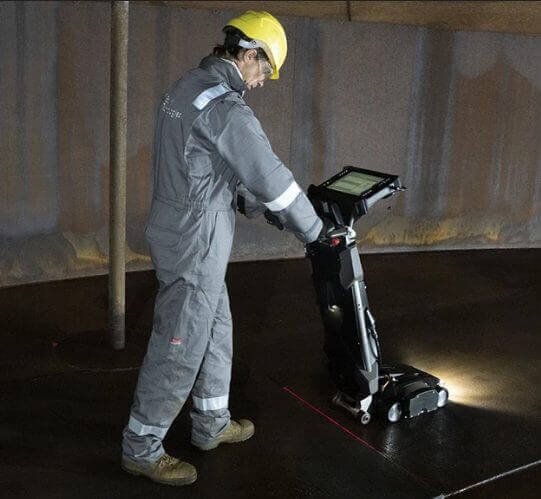
Esta técnica de Inspección se complementa con el método de inspección END de ultrasonido, con el cual se determina el espesor remanente; esta técnica MFL, detecta pérdidas volumétricas no espesores. Igualmente se emplea el equipo de ultrasonido para evaluar zonas donde no se puede acceder con los equipos MFL, como los potes colectores.
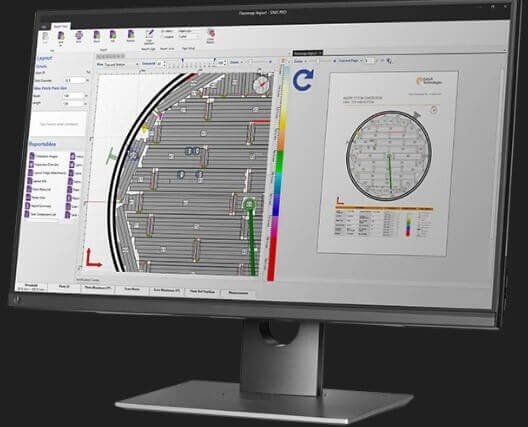
La pestaña de la placa o plancha anular: Esta zona considerada como la zona critica de los tanques de almacenamiento, la conforma una junta soldada, una sección de la pancha anular y la parte inferior de la pared (Ver figura 5) es de gran importancia y de especial atención por su configuración y ubicación, es donde se ejercen las mayores presiones y tensiones en el tanque de almacenamiento y en donde se pueden producir fallas con consecuencias catastróficas. Esta zona está expuesta a dos ambientes siguientes.
- La parte inferior que está en contacto con el suelo: Esta zona se evalúa y controla la corrosión de igual manera que la parte externa del piso.
- La parte superior que está expuesta a la atmosfera: Para determinar la corrosividad en esta zona se debe evaluar varios factores, la humedad, considerando que el valor crítico está por encima de 70 %, las aguas de lluvia, el ambiente salino y los elementos o componente generados por instalaciones industriales cercanas.
Finalmente, los factores que intervienen en la corrosión del acero en esta zona son el aire y la humedad, agravada con la presencia de ácidos diluidos y soluciones salinas.
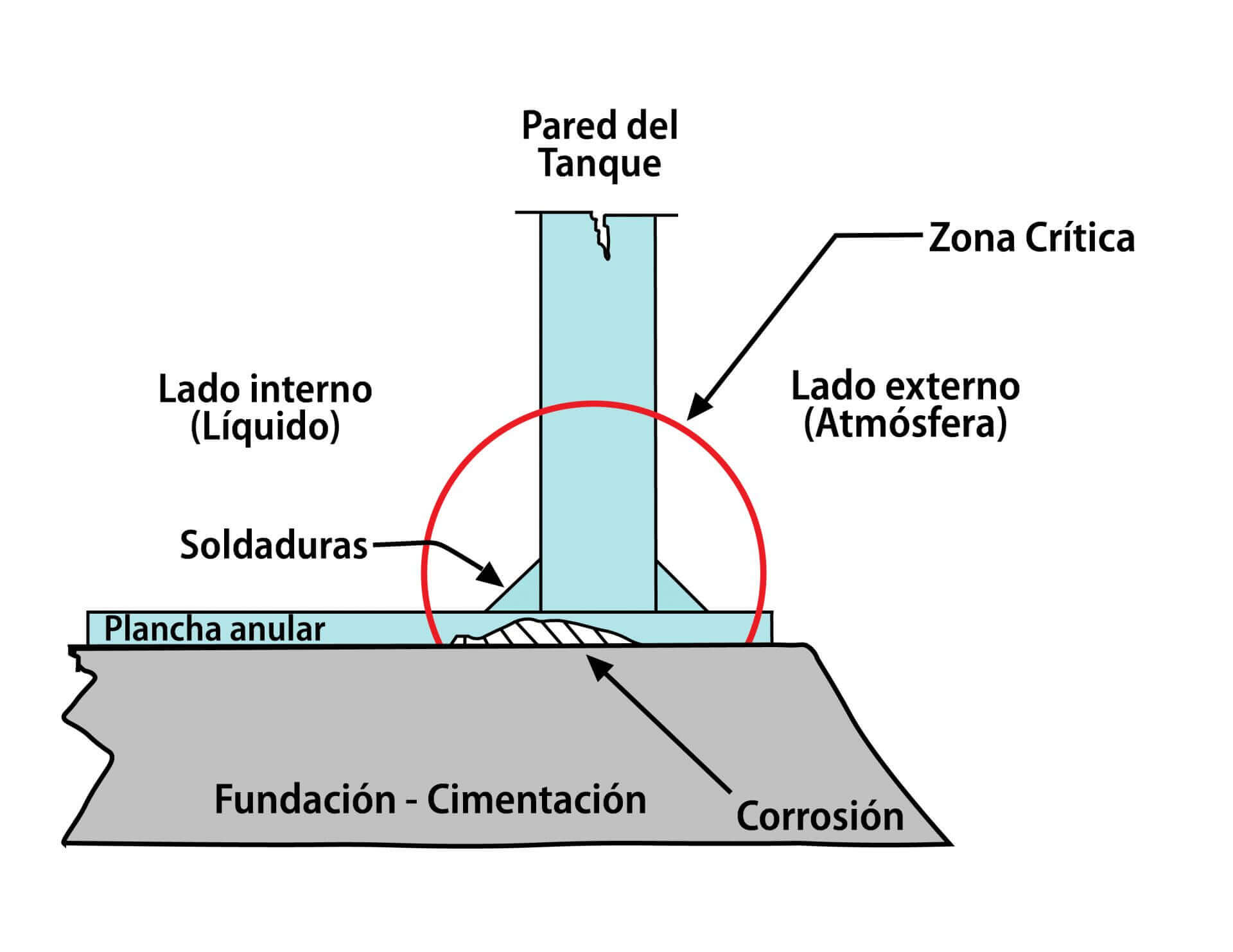
Como esta zona es de fácil acceso se evalúa con los tanques en operación, principalmente mediante la técnica de END de Inspección Visual directa (VT), para ubicar fallas en el recubrimiento y corrosión en la pestaña del lado externo del tanque
Ondas Guiadas: Para inspeccionar la zona crítica en contacto con el suelo, se han desarrollado equipos como el mostrado en la figuras 6 [5]. que utilizan el ensayo de ultrasonido mediante la técnica cualitativa de Ondas Guiadas para ubicar daños en la zona crítica. La técnica mencionada se basa en el concepto de impulsos de ondas laminares guiadas que se propagan desde el transductor hacia la plancha anular y cuando hay corrosión, la ondas ultrasónicas retorna al transductor, convirtiendo la señal e indicando la discontinuidad. Ver figuras 7
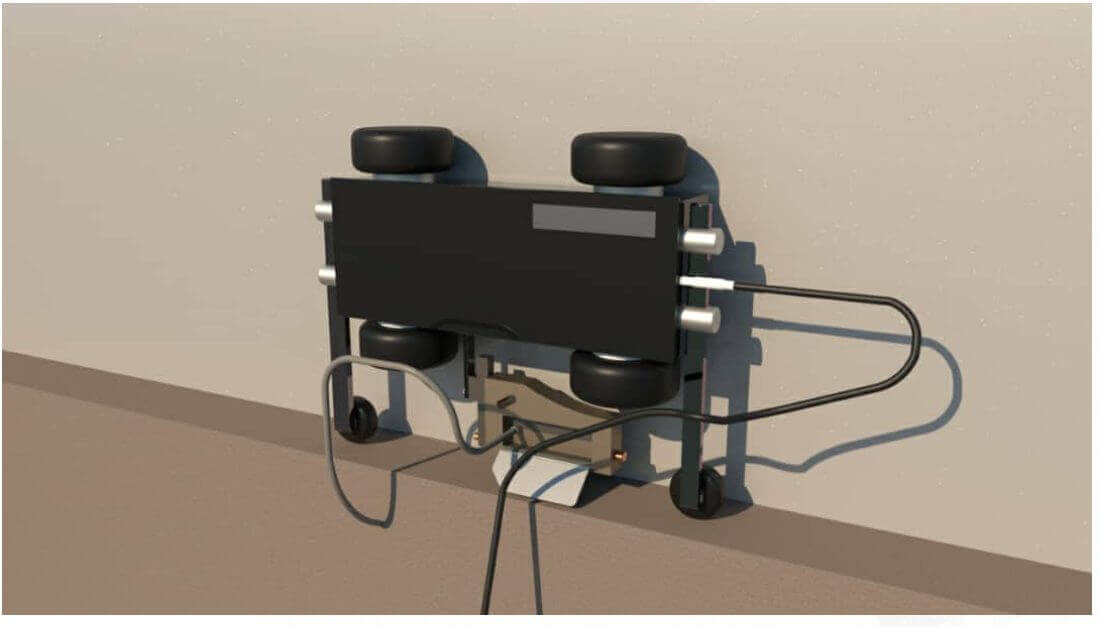
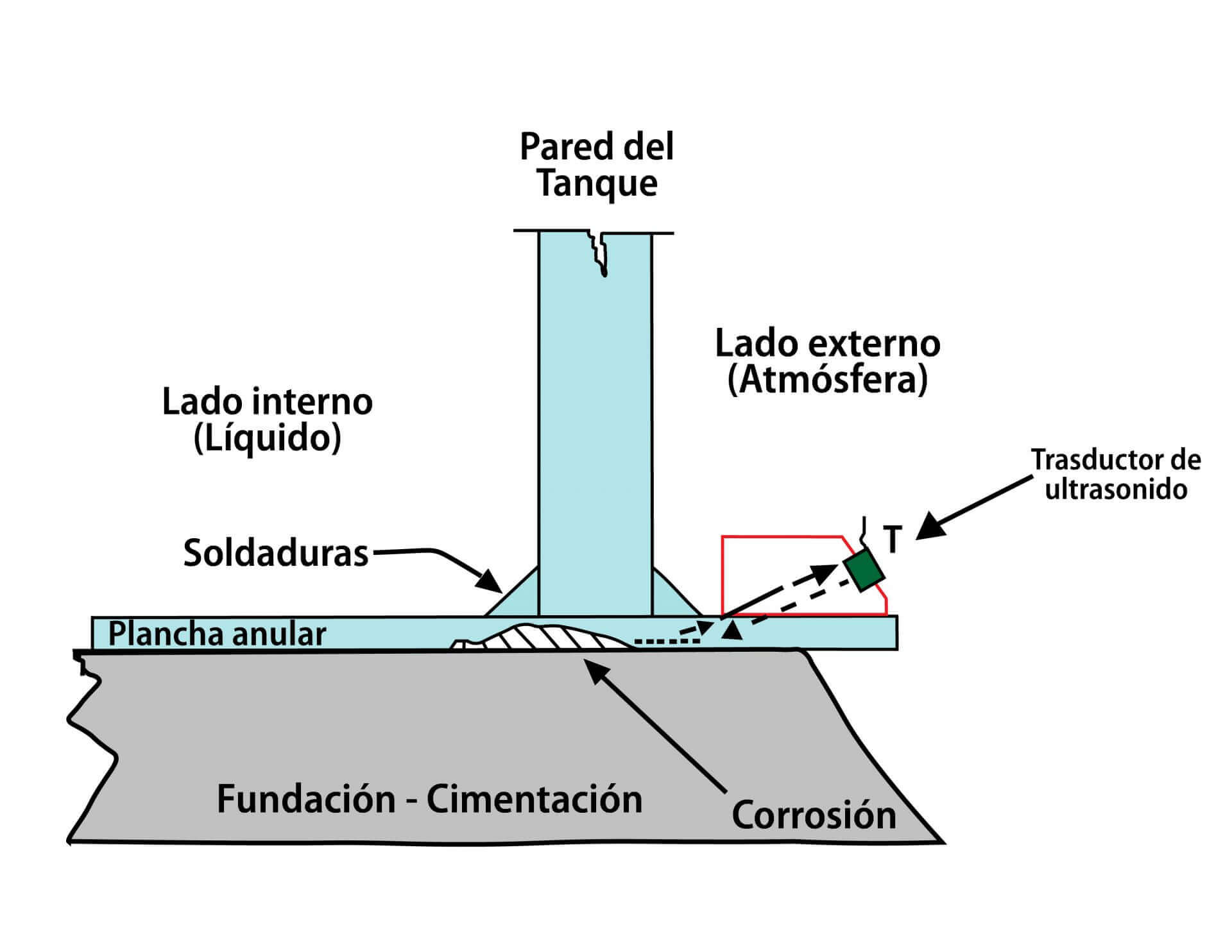
Líquidos penetrantes: Cuando se especifique el examen de líquido penetrante, este deberá estar de acuerdo con la sección V, Artículo 6 del Código ASME. El método de examen con líquidos penetrantes es un medio eficaz para detectar discontinuidades que están abiertas a la superficie de metales no porosos y otros materiales. Las discontinuidades típicas detectables por este método son grietas, uniones, vueltas, cierres fríos, laminaciones y porosidad.
Emisión Acustaica (EA). Para finalizar, mencionaremos la técnica de END de Emisión Acústica (EA), la cual se emplea para realizar la evaluación integral de los tanques de almacenamiento. Esta técnica se puede definir de una manera simple como un ensayo de sonido audible que detecta el sonido que emite los materiales cuando son sometidos a esfuerzo o presión.
El principio básico de las técnicas EA, se fundamenta en el hecho de que los materiales emiten sonido en sus puntos más débiles (Grietas, poros, perdida de espesores, entre otros), cuando son sometidos a cargas. En general, no mide el tamaño de los defectos, pero localiza los puntos con potencial daño, los cuales deben ser evaluados con otras técnicas de END (Generalmente ultrasonido) para cuantificarla.
La principal importancia de esta técnica es que se realiza con los tanques en servicio, prueba de una vez toda la estructura del tanque, detecta fuga en el fondo que afectaría el nivel freático, es relativamente económico y es un gran apoyo para la ampliación de la metodología de inspección basada en riesgo (RBI).
Referencias Bibliográficas:
[1] Industrial Testing & Inspetion Services (ITIS); itis-nl.com.
[2] Publicaciones de estudiantes; aiu.edu
[3] Eddyfi Technologies ; https://www.eddyfi.com/en/product/floormapx-mfl-tank-bottom-inspection.
[4] Eddyfi Technologies Sistema FloormapX; https://www.eddyfi.com/en/product/floormapx-mfl-tank-bottom-inspection.
[5] Tomado de Grupo de Empresas ESCON http://www.escon-dt.com/assetmanagement.php.
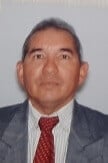
Sobre el autor.
Ingeniero. Euclides Quiñonez. Inspector senior, analista de integridad mecánica de equipos y de confiabilidad de activos, gerente técnico de parada de plantas, evaluador de viabilidad de proyectos de inversión con 40 años de experiencia en las industrias petrolera, petroquímica y gas.