Tabla de Contenidos
- ¿Qué son los defectos de soldadura?
- Errores comunes que causan defectos superficiales
- Principales defectos superficiales en soldadura
- Métodos de inspección para detectar defectos superficiales
- Importancia de la inspección de soldaduras
- Norma que regula los defectos de soldadura permisibles
- Conclusiones
- Referencias
- Preguntas frecuentes sobre defectos superficiales en soldadura
La calidad de la soldadura es un factor preponderante de atención muy especial para la integridad estructural de cualquier proyecto industrial. Defectos como la soldadura socavada, la porosidad y las grietas superficiales pueden comprometer la resistencia de las uniones y provocar fallas prematuras.
Este artículo analiza los principales defectos superficiales en soldadura, sus causas, consecuencias y cómo los procesos de inspección de soldadura pueden ayudar a prevenirlos eficazmente.
¿Qué son los defectos de soldadura?
Los defectos de soldadura son irregularidades que comprometen la integridad, resistencia o estética de una unión metálica. Se clasifican en defectos internos y defectos superficiales, estos últimos más fáciles de detectar y evaluar mediante técnicas de inspección de soldadura, como el examen visual o los ensayos no destructivos.
Aunque superficiales, estos defectos de soldadura pueden ser el reflejo de problemas más profundos, como una mala técnica, materiales contaminados o parámetros inadecuados. Por lo tanto, su análisis es significativo para garantizar la fiabilidad de la unión.
Errores comunes que causan defectos superficiales
Detectar el origen de los defectos de soldadura permite establecer acciones correctivas. Entre las causas más comunes destacan:
- Parámetros de soldadura incorrectos (amperaje, voltaje, velocidad), que inducen soldadura socavada o exceso de refuerzo.
- Superficies contaminadas con óxido, humedad o grasa, que generan porosidad en soldadura.
- Técnica deficiente del soldador, que favorece cordones irregulares y grietas en soldadura.
- Electrodos húmedos o incompatibles que comprometen la calidad del proceso.
- Condiciones ambientales adversas, responsables de la porosidad en soldadura o grietas superficiales.
- Mala limpieza entre pasadas, origen común de inclusiones y defectos de soldadura superficiales.
Principales defectos superficiales en soldadura
A continuación, se describen los defectos de soldadura más comunes encontrados en la superficie de las uniones soldadas:
1. Grietas en soldaduras: Pequeñas fracturas visibles en la superficie del cordón que pueden ser:
- Longitudinales (a lo largo del eje del cordón).
- Transversales (perpendiculares al cordón).
- Marginales o en cráter (al final de la soldadura).
- Grietas en caliente: Se forman al enfriar el metal fundido.
- Grietas en frío: Aparecen luego de la solidificación, por tensiones residuales o presencia de hidrógeno.
Las grietas en soldadura son altamente peligrosas, ya que tienden a propagarse, comprometiendo la estructura. Su detección debe ser prioritaria durante la inspección de soldadura.
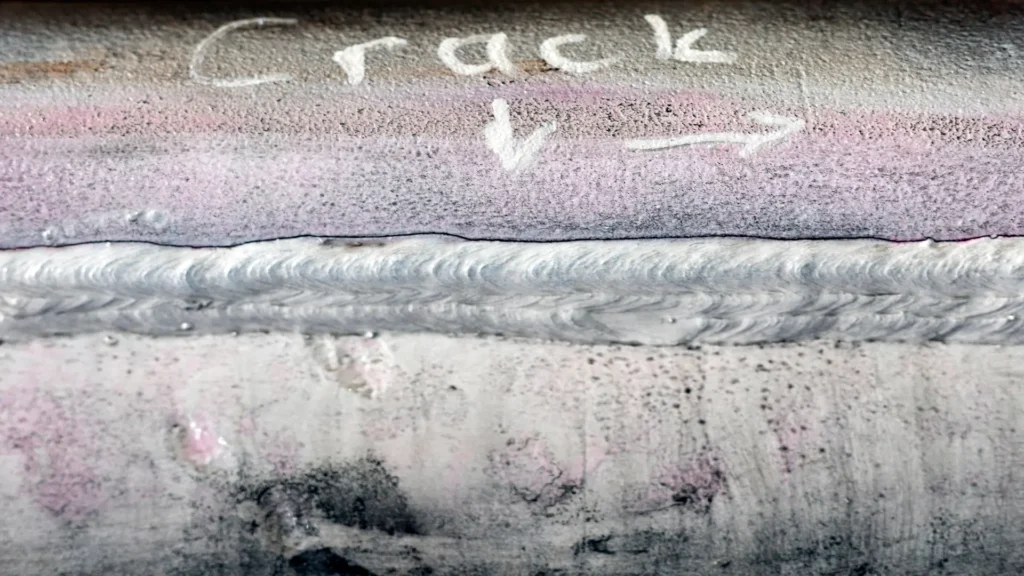
2. Porosidad en soldadura: La formación de cavidades gaseosas en la superficie, generadas por gases atrapados durante la solidificación. Puede presentarse como:
- Porosidad aislada.
- Porosidad agrupada o aglomerada.
- Micro porosidad superficial.
La porosidad en soldadura disminuye la densidad del material y es origen potencial de fisuras.
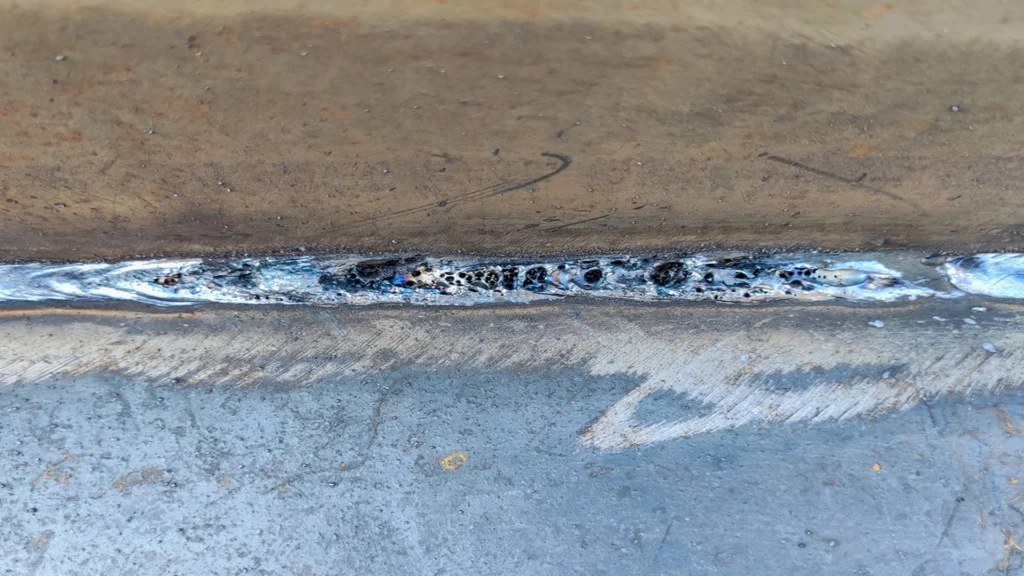
3. Inclusiones superficiales: Residuos visibles como escoria atrapada o partículas no metálicas que se solidifican en la superficie de la soldadura. Generalmente están asociadas a una mala técnica de limpieza entre pasadas o uso inadecuado de fundente.
4. Soldadura socavado (undercut): Surcos a lo largo del borde del cordón, causados por un exceso de calor o mala manipulación del electrodo. Este defecto reduce la resistencia a la fatiga de la soldadura.
Este defecto de soldadura consiste en un surco a lo largo del borde del cordón. Ocurre por exceso de calor o mala manipulación del electrodo. La soldadura socavada debilita la resistencia a la fatiga y puede ser detectada fácilmente mediante inspección de soldadura visual.
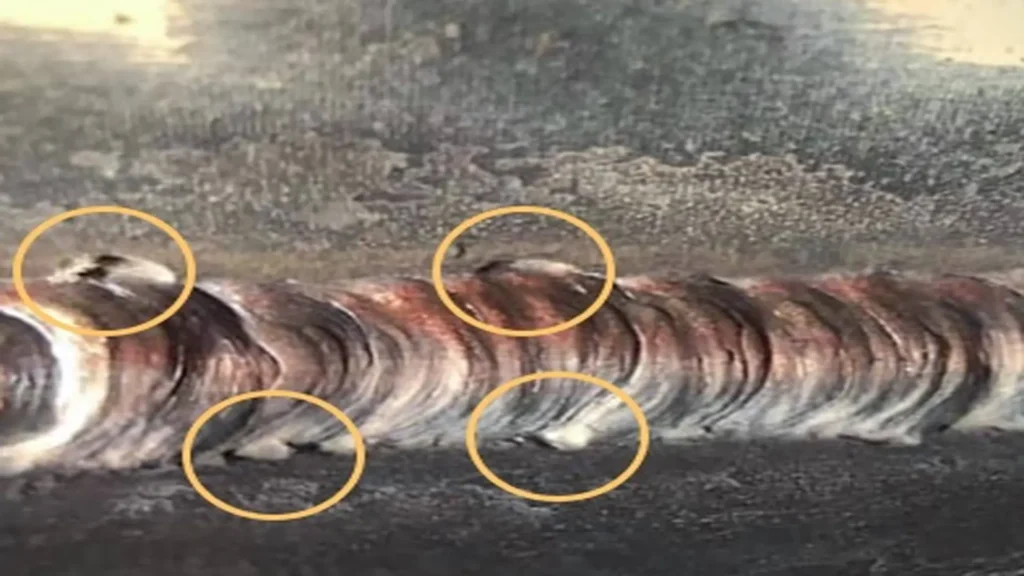
5. Exceso de refuerzo: Cuando el cordón sobresale demasiado por encima de la superficie base. Aunque visualmente puede parecer sólido, genera concentraciones de tensión no deseadas.
6. Perfil irregular del cordón: Un cordón con forma inestable, ondulación excesiva o desalineación, evidencia problemas de técnica, velocidad o amperaje. Aunque no es un defecto de soldadura crítico, un cordón con demasiado material genera tensiones no deseadas, afectando la homogeneidad estructural.
7. Falta de relleno: Presencia de depresiones visibles o ranuras entre pasadas, especialmente en soldaduras multipase. Esto se debe a aporte insuficiente de metal de soldadura.
8. Contaminación superficial: Manchas, óxidos, aceite o partículas metálicas visibles que alteran la adherencia del cordón y pueden provocar otros defectos de soldadura como grietas o porosidad.
9. Salpicaduras de soldadura (spatter): Pequeñas gotas de metal expulsadas del arco que se adhieren a la superficie. Aunque no siempre afectan la resistencia, perjudican el acabado superficial y requiere limpieza adicional.
10. Cráteres mal terminados: Son depresiones en el final del cordón, causadas por interrupciones bruscas del arco sin relleno adecuado que generan depresiones que favorecen las grietas en soldadura, sobre todo en zonas de esfuerzo.
11. Desalineación superficial: Mal empalme entre cordones adyacentes o entre los bordes de la junta. Es común en procesos manuales con mala guía del electrodo o incorrecto ajuste de la junta.
Para reducir la aparición de estos defectos de soldadura, se deben implementar buenas prácticas desde el inicio del proceso de soldadura. Entre las acciones más efectivas se encuentran:
- Capacitar adecuadamente a los soldadores en técnicas apropiadas y criterios de calidad.
- Controlar rigurosamente los parámetros de soldadura como voltaje, corriente, velocidad de avance y tipo de electrodo.
- Aplicar protocolos de inspección de soldadura visual y ensayos no destructivos conforme a los estándares del material y la estructura.
Tabla con las características de los defectos superficiales en soldadura
Defecto superficial | Descripción técnica | Causas comunes | Impacto en la calidad |
---|---|---|---|
Grietas en soldadura | Fracturas visibles longitudinales, transversales o en cráter. | Enfriamiento rápido, tensiones residuales o mala selección de parámetros. | Comprometen la resistencia e integridad estructural. |
Porosidad en soldadura | Cavidades generadas por gas atrapado. | Humedad, contaminación, corriente de aire en el arco de soldadura. | Disminuyen la densidad y pueden propagar fisuras. |
Inclusiones superficiales | Escoria o partículas no metálicas atrapadas en la superficie. | Mala limpieza entre pasadas, fundente deficiente. | Afectan la continuidad y resistencia del cordón. |
Soldadura Socavada (undercut) | Surco a lo largo del borde del cordón de soldadura. | Exceso de amperaje, mala técnica. | Disminuye resistencia a fatiga y carga cíclica. |
Exceso de refuerzo | Cordón sobresale excesivamente sobre la superficie. | Velocidad de avance baja, exceso de aporte. | Genera concentraciones de esfuerzo. |
Perfil irregular del cordón | Cordón con ondulaciones, inestabilidad o mal formado. | Técnica inadecuada, oscilación irregular. | Aspecto pobre, posible debilitamiento del cordón. |
Falta de relleno | Depresiones visibles entre pasadas. | Aporte de material insuficiente, mala cobertura. | Reducción del espesor efectivo de soldadura. |
Contaminación superficial | Presencia de óxidos, aceites o residuos. | Limpieza deficiente, preparación inadecuada. | Genera otros defectos y afecta adherencia. |
Salpicaduras (spatter) | Gotas de metal expulsadas del arco y adheridas a la superficie. | Exceso de amperaje, polaridad incorrecta. | Deterioro del acabado y necesidad de retrabajo. |
Cráteres mal terminados | Depresión al final del cordón por interrupción inadecuada. | Corte brusco del arco sin relleno del cráter. | Zona propensa a grietas y fisuras. |
Desalineación superficial | Desfase entre cordones o bordes mal posicionados. | Mala preparación de junta, guía incorrecta. | Debilita la unión y afecta el flujo de esfuerzos. |
Métodos de inspección para detectar defectos superficiales
Una inspección de soldadura adecuada permite detectar estos defectos antes de que la unión entre en servicio. A continuación, se presentan los métodos más comunes utilizados para identificar discontinuidades superficiales
1. Inspección visual (VT): Es el método más básico y ampliamente usado. Un inspector calificado puede identificar defectos como socavado, grietas visibles y porosidad con ayuda de lupas, luces LED o cámaras de alta resolución.
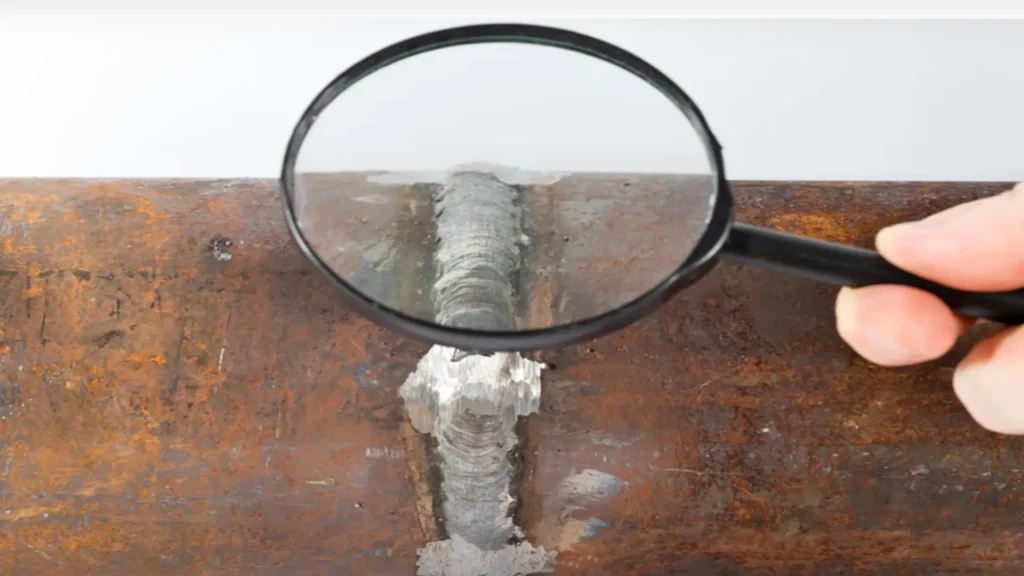
2. Ensayo de líquidos penetrantes (PT): Ideal para detectar discontinuidades abiertas a la superficie. Utiliza un líquido con alta capilaridad, seguido por un revelador, para hacer visible cualquier defecto bajo luz visible o ultravioleta.
3. Ensayo por partículas magnéticas (MT): Se aplica a materiales ferromagnéticos, para identificar grietas en soldaduras ubicadas en la superficie y sub-superficiales mediante la atracción de partículas magnéticas en zonas con alteración del campo.
4. Corrientes inducidas (ET): Utiliza campos electromagnéticos para reconocer variaciones en la conductividad del material. Eficaz para detectar porosidad en soldadura o fisuras en materiales conductores.
5. Inspección ultrasónica superficial (UT): La tecnología ultrasónica se usa para detectar cambios en la propagación de ondas reflejadas por discontinuidades. Métodos, como el haz angular, permiten la inspección de soldadura y un análisis superficial de alta precisión.
6. Emisión acústica (AET): Permite detectar defectos en tiempo real durante pruebas de carga. Aunque se usa más para defectos internos, también es útil en ciertas grietas en soldaduras que estén activas en la superficiales.
7. Termografía infrarroja: Se emplea para detectar defectos de soldaduras a través de variaciones de temperatura en la superficie, causadas por diferencias en la conductividad térmica debido a poros o grietas.
8. Métodos láser: Técnicas como la interferometría láser o el escaneo 3D detectan irregularidades topográficas con alta precisión. Son ideales para inspecciones automatizadas de soldaduras críticas.
9. Sistemas de inspección automatizados y robóticos: La robótica permite realizar inspecciones visuales y multiprotocolo de forma repetitiva, incluso en condiciones complejas o entornos peligrosos.
Importancia de la inspección de soldaduras
Una adecuada inspección de soldadura no solo mejora la calidad, sino que previene que defectos de soldadura pasen desapercibidos. Identificar condiciones como grietas en soldadura, porosidad en soldadura o soldadura socavada a tiempo evita fallas estructurales, costos de retrabajo y riesgos operacionales.
Estos defectos, aunque puedan parecer menores a simple vista, pueden comprometer seriamente la calidad de soldadura si no se identifican y corrigen oportunamente a través de métodos visuales y técnicas no destructivas.
Norma que regula los defectos de soldadura permisibles
La norma ISO 5817 y la AWS D1.1 son referentes para evaluar la calidad de las soldaduras según niveles de aceptación definidos.
Conclusiones
Los defectos ubicados en la superficiales como soldadura socavada, la porosidad en soldadura y las grietas en soldadura afectan directamente la resistencia y durabilidad de las uniones soldadas. Su detección oportuna mediante una inspección de soldadura adecuada garantiza la seguridad y el cumplimiento normativo en proyectos industriales.
Además, es esencial que los soldadores estén adecuadamente capacitados y que se utilicen los parámetros de soldadura correctos para minimizar la aparición de defectos. La calidad de una soldadura no solo depende del equipo y los materiales utilizados, sino también de la habilidad y conocimiento del soldador.
Referencias
- AWS D1.1 Structural Welding Code – Steel, American Welding Society
- ISO 5817:2014 – Fusion-welded joints in steel, nickel, titanium and their alloys — Quality levels for imperfections
- API 1104 – Welding of Pipelines and Related Facilities
- Handbook of Visual Inspection Techniques – ASNT
Preguntas frecuentes sobre defectos superficiales en soldadura
¿Cuál es el defecto superficial más crítico en una soldadura?
Las grietas superficiales son consideradas las más peligrosas. Estas discontinuidades pueden propagarse rápidamente, comprometiendo la integridad estructural y generando fallas catastróficas si no se detectan a tiempo.
¿Cómo afecta la zona afectada por el calor (ZAC) a los defectos superficiales?
En la ZAC pueden generarse microgrietas debido a tensiones térmicas o metalúrgicas. Estas son especialmente sensibles en materiales con alta dureza o tratamientos térmicos inadecuados.
¿Los defectos superficiales siempre se pueden reparar?
En muchos casos sí, pero si se trata de grietas profundas o localizadas en zonas críticas, puede requerirse la remoción completa del cordón y un nuevo procedimiento de soldadura calificado.
¿Qué relación hay entre el control de parámetros y la calidad de soldadura?
Un control deficiente puede generar falta de penetración, falta de fusión en la soldadura o aparición de grietas. Ajustar corriente, voltaje y velocidad es vital para evitar defectos y lograr una calidad de soldadura confiable.