Tabla de Contenidos
- ¿Qué es un análisis de riesgos?
- Modelo de matriz de riesgos para equipos rotativos
- Priorización de riesgos cuantitativos
- Sistema dinámico de apoyo a las decisiones
- Personalización de la matriz de riesgos adaptativa
- Enfoque integrado de sistemas críticos para la seguridad
- Optimización costo-beneficio
- Motor de cumplimiento y estandarización
- Integración del mantenimiento predictivo y prescriptivo
- Causas de fallas en rodamientos y cómo identificarlas
- ¿Cuándo se debe reemplazar un rodamiento?
- Análisis costo-beneficio del reemplazo de rodamientos
- Conclusiones
- Referencias
Los rodamientos son componentes fundamentales de la maquinaria y están especialmente diseñados para reducir la fricción y proporcionar una superficie de apoyo, permitiendo que los componentes de los equipos rotativos giren o se desplacen sin esfuerzo. Al minimizar la fricción y el desgaste, los rodamientos aseguran que la energía hidráulica se convierta en movimientos precisos y fluidos, mejorando el rendimiento general de los equipos.
Con el tiempo, los rodamientos se desgastan y requieren reemplazo o reacondicionamiento para mantener la eficiencia y reducir el tiempo de inactividad. Este artículo tiene como objetivo proporcionar información sobre cuándo reemplazar los rodamientos en equipos rotativos mediante la evaluación de riesgos, garantizando la eficiencia operativa y minimizando el tiempo de inactividad. Además, se evalúa la rentabilidad del reacondicionamiento de rodamientos en comparación con su reemplazo total, destacando los beneficios económicos.
¿Qué es un análisis de riesgos?
El análisis de riesgo es un proceso sistemático utilizado para identificar, evaluar y gestionar los riesgos potenciales que pueden afectar a una instalación existente o a un proyecto en desarrollo. Consiste en estudiar detenidamente los posibles peligros, tanto internos como externos, y sus posibles consecuencias. Este proceso permite establecer medidas de prevención y protección adecuadas para mitigar o eliminar estos riesgos1.
Es importante tener en cuenta la diferencia entre peligros y riesgos. Un peligro es cualquier evento que pueda causar daño, incluidos accidentes laborales, situaciones de emergencia, productos químicos tóxicos, conflictos entre empleados, estrés y más. Un riesgo consiste en la posibilidad de que un peligro cause daño. Como parte de un plan de evaluación de riesgos, primero se deben identificar los peligros potenciales y luego calcular el riesgo o la probabilidad de que ocurran esos peligros.
Esta técnica no se enfoca directamente en determinar cuándo reemplazar un rodamiento en equipos rotativos específicamente, sino más bien en evaluar los peligros potenciales asociados con la operación continua de rodamientos desgastados o defectuosos.
La evaluación de riesgos en el contexto de los rodamientos en equipos rotativos ayuda a identificar los posibles riesgos derivados de un mal funcionamiento de los rodamientos. Esto incluye riesgos como fallos inesperados que podrían resultar en paradas no planificadas, daños en el equipo, o incluso riesgos para la seguridad de los trabajadores si un rodamiento falla durante la operación. La evaluación de estos riesgos, permite tomar decisiones informadas sobre cuándo es necesario reemplazar los rodamientos.
Por ejemplo, la evaluación de riesgos puede considerar factores como la frecuencia y severidad de las fallas pasadas de rodamientos, la criticidad del equipo en el proceso productivo, y los posibles impactos económicos y de seguridad asociados con una falla de rodamiento. Estos análisis ayudan a establecer criterios para determinar cuándo programar el reemplazo preventivo de rodamientos antes de que ocurran fallas críticas.
La evaluación de riesgos no proporciona directamente la fecha exacta de reemplazo de un rodamiento, sí proporciona información importante para gestionar los riesgos asociados con su operación continua y establecer estrategias de mantenimiento preventivo adecuadas para minimizar estos riesgos. Desde el punto de vista de un analista de mantenimiento predictivo, el enfoque se centraría más en utilizar técnicas y herramientas específicas para monitorear el estado de los rodamientos y predecir cuándo es necesario su reemplazo antes de que ocurra una falla. A continuacion se detallan laas caracteristicas de estos dos procedimientos:
Evaluación de riesgos
- Alcance: Este enfoque evalúa los riesgos asociados con el mal funcionamiento de los rodamientos, pero no proporciona una metodología detallada para determinar el momento exacto de reemplazo. Se concentra en identificar los posibles impactos de una falla y establecer criterios generales para la gestión de riesgos.
- Utilidad: Es útil para comprender las implicaciones de seguridad y operativas de mantener rodamientos desgastados, pero no proporciona datos específicos sobre la condición que presenta el rodamiento ni recomendaciones detalladas sobre el momento óptimo para el reemplazo.
Análisis predictivo
- Alcance: Este tipo de analisis predictivo utiliza técnicas como el monitoreo de vibraciones, análisis de aceite, termografía, entre otras, para evaluar el estado actual de los rodamientos y predecir su vida útil restante.
- Utilidad: Proporciona datos concretos y específicos sobre la condición actual del rodamiento y su deterioro gradual. Permite identificar patrones de falla temprana y planificar el reemplazo de manera más precisa y eficiente, minimizando el riesgo de paradas no planificadas y optimizando los costos de mantenimiento.
Modelo de matriz de riesgos para equipos rotativos
Priorización de riesgos cuantitativos
- Implementar un sistema de puntuación de riesgo multifactorial.
- Utilizar simulaciones de Monte Carlo para tener en cuenta las incertidumbres en los factores de riesgo. Las simulaciones de Monte Carlo son una técnica matemática que predice los posibles resultados de un evento incierto. Los programas informáticos utilizan este método para analizar datos pasados y predecir una serie de resultados futuros en función de una elección de acción. Una simulación de Monte Carlo es un modelo probabilístico que puede incluir un elemento de incertidumbre o aleatoriedad en su predicción. Cuando se utiliza un modelo probabilístico para simular una salida, se obtienen resultados diferentes cada vez.
R = C * P * D
Dónde:
R = Puntuación de riesgo
C = Gravedad de las consecuencias (escala 1-10)
P = Probabilidad de fallo (escala 0-1)
D = Factor de detectabilidad (escala 1-5)
Sistema dinámico de apoyo a las decisiones
- Desarrollar un panel de riesgos en tiempo real integrando:
- Datos de sensores en vivo del equipo.
- Datos históricos de fallos.
- Registros de mantenimiento.
- Implementar algoritmos de aprendizaje automático para el análisis predictivo de riesgos:
- Bosque aleatorio para clasificación de modos de falla.
- Redes neuronales LSTM para la predicción de series temporales de degradación de equipos.
Personalización de la matriz de riesgos adaptativa
- Emplear matrices de riesgo jerárquicas:
- Nivel 1: Categoría de equipamiento general.
- Nivel 2: Tipo de equipo específico.
- Nivel 3: Componente individual.
- Implementar la recalibración automatizada de la matriz basada en los datos recopilados y las tendencias identificadas.
Enfoque integrado de sistemas críticos para la seguridad
- Incorporar el Análisis de Árbol de Fallas (FTA) y el Análisis de Árbol de Eventos (ETA) en el proceso de evaluación de riesgos.
- Implementar Análisis de Capas de Protección (LOPA) para escenarios de alto riesgo.
- Utilice diagramas de pajarita para una visualización integral de riesgos y un análisis de barreras.
Optimización costo-beneficio
- Desarrollar un modelo de costos dinámico integrando:
- Costes directos de mantenimiento.
- Costos indirectos (por ejemplo, tiempo de inactividad, pérdida de producción).
- Costos de mitigación de riesgos.
- Implementar Algoritmos Genéticos para optimización multi objetivo de cronogramas de mantenimiento y asignación de recursos.
Motor de cumplimiento y estandarización
- Crear un motor basado en reglas para garantizar la alineación con estándares como:
- ISO 31000 (Gestión de Riesgos).
- IEC 60812 (FMEA): IEC 60812: 2018 explica cómo se planifica, realiza, documenta y mantiene el análisis de modos y efectos de falla (FMEA), incluida la variante de análisis de modos, efectos y criticidad de falla (FMEA). El propósito del análisis de modos y efectos de falla (FMEA) es establecer cómo los elementos o procesos pueden fallar en el desempeño de su función para que se pueda identificar cualquier tratamiento requerido.
- API 581 (Inspección basada en riesgos).
- Implementar informes de cumplimiento automatizados y análisis de brechas.
Integración del mantenimiento predictivo y prescriptivo
- Desarrollar un modelo híbrido combinando:
- Modelos basados en la física (por ejemplo, análisis de elementos finitos para la predicción del estrés).
- Modelos basados en datos (por ejemplo, aumento de gradiente para la estimación de la vida útil restante).
- Implementar tecnología Digital Twin para monitoreo del estado del equipo y análisis de escenarios en tiempo real.
Causas de fallas en rodamientos y cómo identificarlas
Los rodamientos, pueden fallar por diversas razones. Identificar la causa de la falla es importante para implementar medidas correctivas efectivas y prevenir recurrencias. A continuación, se detallan las principales causas de fallas en rodamientos y cómo identificarlas2.
- Falta de lubricación: La mayoría de las fallas prematuras de rodamientos son causadas por una lubricación deficiente. Factores como lubricantes inadecuados, cantidades excesivas o insuficientes, y la degradación de los lubricantes contribuyen a este problema. La falta de lubricación se manifiesta como desgaste abrasivo, adhesivo y fatiga de los caminos de rodadura, con indicios como ralladuras y decoloración. Para prevenir esta falla, es esencial utilizar el lubricante correcto en la cantidad y frecuencia adecuadas.
- Contaminación: La contaminación por sustancias extrañas en el lubricante o durante el proceso operativo puede causar fallas en los rodamientos. Los signos incluyen indentaciones en los caminos de rodadura y elementos rodantes, formación de microcráteres y huellas en forma de abanico. La prevención implica procedimientos rigurosos de almacenamiento, filtrado y limpieza, así como mejoras en los sistemas de sellado.
- Corrosión por rozamiento: La corrosión por rozamiento ocurre debido a maquinado inadecuado de las superficies de contacto, especialmente cuando uno de los aros no permite la dilatación axial. Esta falla se presenta como oxidación y micro movimientos que causan pérdida de material. La prevención requiere la medición precisa del eje y alojamiento durante el recambio de rodamientos.
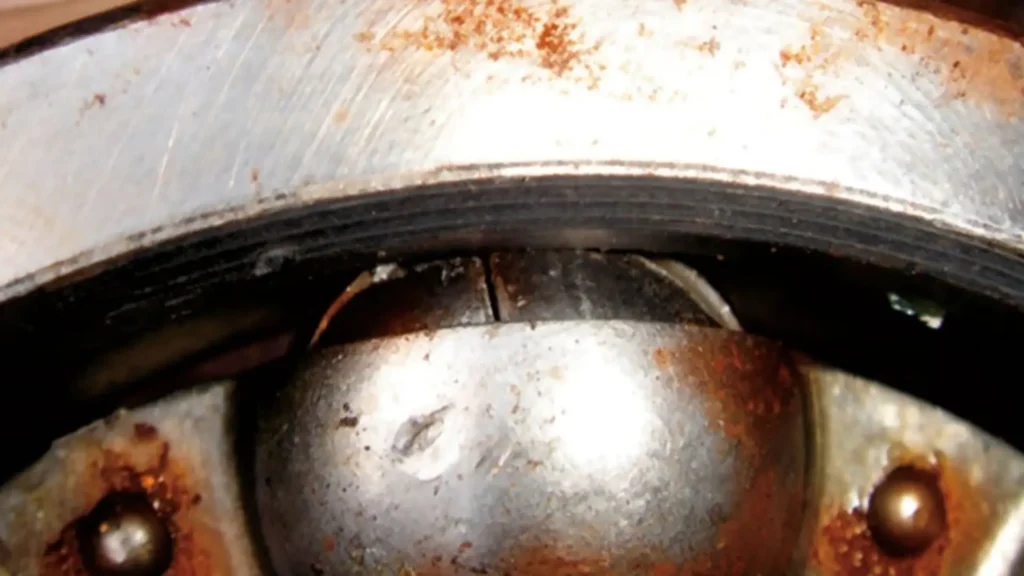
- Sobrecarga o montaje fnadecuado: El montaje incorrecto de rodamientos, utilizando métodos no adecuados, provoca sobrecarga y daños en los caminos de rodadura. Para prevenir esta falla, se recomienda aplicar la fuerza de montaje correctamente, siguiendo las instrucciones específicas.
- Sobrecalentamiento: El sobrecalentamiento de rodamientos, a temperaturas superiores a 125°C, afecta la estabilidad dimensional y las propiedades metalúrgicas, causando deformaciones y fracturas. Para prevenirlo, se deben utilizar calentadores de inducción y capacitar al personal en el uso correcto de herramientas.
- Corrosión por humedad: La corrosión por humedad ocurre durante el almacenamiento prolongado o por fallas en el sellado, causando oxidación y daños en los rodamientos. La prevención requiere tareas de mantenimiento regular, el uso de lubricantes adecuados y mejoras en los sistemas de sellado.
- Desalineación: La desalineación, debido a la pérdida de colinealidad entre equipos, causa sobrecarga y desgaste prematuro. Se identifica por el desgaste desigual en los caminos de rodadura. La prevención implica mejorar los procesos de maquinado, implementar procedimientos adecuados de montaje y capacitar al personal en la alineación de ejes y poleas.
- Almacenamiento y manipulación: El almacenamiento incorrecto de rodamientos, expuestos a vibraciones externas, humedad y contaminantes, causa desgaste abrasivo y daños. La prevención incluye la capacitación del personal de almacén, el control de las condiciones ambientales y la protección adecuada de los rodamientos.
¿Cuándo se debe reemplazar un rodamiento?
Monitoreo de la condición del rodamiento
El tiempo entre el daño inicial de un rodamiento y su falla total puede variar considerablemente. En condiciones de alta velocidad, este período puede ser de solo unos segundos, mientras que en equipos grandes con rotación lenta, puede extenderse durante meses. La clave para determinar el momento adecuado para reemplazar un rodamiento es el monitoreo continuo de su condición.
Importancia del diagnóstico temprano
El monitoreo de la condición del rodamiento es esencial para detectar daños antes de que se produzca una falla catastrófica. Si el daño no se diagnostica a tiempo y el rodamiento no se reemplaza oportunamente, se corre el riesgo de causar daños secundarios al equipo y a sus componentes. Las fallas catastróficas pueden resultar en paradas prolongadas y costosas, además de dificultar o incluso imposibilitar la identificación de la causa raíz del problema.
Técnicas de monitoreo
Existen diversas técnicas de monitoreo de la condición del rodamiento, entre las cuales destacan:
- Análisis de vibraciones: Permite detectar irregularidades en el funcionamiento del rodamiento, identificando patrones anómalos que indican desgaste o daño.
- Análisis de aceite: Evalúa la presencia de partículas metálicas y contaminantes en el lubricante, lo que puede señalar desgaste del rodamiento.
- Termografía: Utiliza imágenes térmicas para identificar áreas de calor excesivo, indicativo de fricción anormal o fallos inminentes.
Criterios de reemplazo
La decisión de reemplazar un rodamiento debe basarse en criterios técnicos precisos, considerando factores como:
- Grado de desgaste: Medido mediante inspección visual y análisis de superficie.
- Niveles de vibración: Comparados con estándares establecidos para determinar la severidad del daño.
- Condición del lubricante: Evaluada para detectar signos de degradación o contaminación.
Consecuencias de no reemplazar a tiempo
No reemplazar un rodamiento dañado a tiempo puede tener consecuencias graves, incluyendo:
- Daño secundario: A otros componentes del equipo, lo que puede incrementar los costos de reparación y mantenimiento.
- Fallas catastróficas: Que pueden resultar en paradas no planificadas, pérdida de producción y mayores riesgos operativos.
- Dificultades en el diagnóstico: Posterior de la causa raíz del fallo, complicando las acciones correctivas y preventivas.
Análisis costo-beneficio del reemplazo de rodamientos
Es importante reconocer que, si bien el reacondicionamiento de rodamientos puede ofrecer beneficios económicos y ambientales significativos, también conlleva riesgos potenciales para la integridad mecánica del equipo. La decisión de reacondicionar o reemplazar un rodamiento debe basarse en una evaluación detallada de factores como la criticidad del equipo, las condiciones de operación y los estándares de seguridad.
Implementar procedimientos rigurosos de control de calidad es esencial para mitigar los riesgos asociados con el reacondicionamiento. En algunos casos, especialmente en equipos críticos o de alta carga, el reemplazo debe ser preferible para garantizar la fiabilidad a largo plazo y minimizar el riesgo de fallas catastróficas.
Basándome en la experiencia y en observaciones presentes, el reacondicionamiento de rodamientos no siempre es la opción más económica ni la más segura. La decisión de reacondicionar o reemplazar debe basarse en un análisis detallado de costos, riesgos y beneficios. En muchos casos, reemplazar el rodamiento puede ser una opción más segura y económicamente viable, asegurando la integridad mecánica del equipo y minimizando el tiempo de inactividad.
Conclusiones
El reemplazo oportuno de rodamientos en equipos rotativos es crucial para mantener la eficiencia operativa y minimizar el tiempo de inactividad. El monitoreo de la condición del rodamiento es la mejor herramienta para determinar el momento adecuado para el reemplazo, evitando daños secundarios y fallas catastróficas. Implementar un programa de mantenimiento basado en la condición y el uso de técnicas avanzadas de monitoreo garantizará la longevidad y el rendimiento óptimo de los equipos.
Identificar y comprender las causas de las fallas en rodamientos es fundamental para la implementación de medidas preventivas y correctivas. El monitoreo de la condición del rodamiento y la adherencia a prácticas de mantenimiento adecuadas son esenciales para prolongar la vida útil de los rodamientos y garantizar la eficiencia operativa de los equipos
Referencias
- Diego Santos; «Qué es y cómo hacer un análisis de riesgos (con ejemplos)»
- https://brr.mx/10-fallas-en-los-rodamientos-y-sus-causas/
- Daño de rodamientos y análisis de fallas.