Tabla de Contenidos
- Propiedades de los metales ferrosos y no ferrosos
- Corrosión en metales ferrosos
- Corrosión en metales no ferrosos
- Ejemplos de los metales ferrosos y no ferrosos
- Diferencias de corrosión: metales ferrosos vs no ferrosos
- ¿Cuál es más resistente a ambientes salinos?
- Conclusiones
- (FAQs) sobre la corrosión en metales ferrosos y no ferrosos
- Referencias
La corrosión, aunque muchas veces subestimada, sigue siendo uno de los enemigos silenciosos más críticos para la integridad operativa en sectores industriales estratégicos. Cada punto de óxido representa una amenaza potencial a la confiabilidad de activos multimillonarios, desde refinerías hasta plataformas offshore.
Desde fallas estructurales en plataformas offshore hasta pérdidas económicas en refinerías y terminales marítimos, el deterioro progresivo de materiales metálicos compromete la seguridad, confiabilidad y eficiencia de los activos. Comprender la naturaleza de esta degradación no es solo una cuestión técnica, sino una necesidad estratégica para la gestión de activos industriales.
En este contexto, diferenciar entre aleaciones ferrosas y no ferrosas cobra especial relevancia. En contraposición, ambos grupos presentan comportamientos distintos frente a ambientes corrosivos y, particularmente, en ambientes marinos, diferenciar entre metales ferrosos y no ferrosos cobra especial relevancia. Ambos grupos presentan comportamientos distintos frente a ambientes corrosivos y, en particular, a ambientes marinos, lo cual influye directamente en decisiones de diseño, mantenimiento y selección de materiales.
Para profesionales en Oil & Gas, energía eólica, petroquímica o producción offshore, conocer estas diferencias permite anticipar riesgos, optimizar ciclos de vida y mejorar la sostenibilidad operativa. Este artículo ofrece un análisis comparativo riguroso con base técnica, normativa y aplicada.
Propiedades de los metales ferrosos y no ferrosos
Las propiedades fundamentales de los metales ferrosos y no ferrosos determinan no solo su desempeño mecánico, sino también su comportamiento frente a entornos corrosivos. En términos estructurales, las aleaciones ferrosas, como el acero al carbono o el hierro fundido, contienen una cantidad significativa de hierro, lo que los hace magnéticos y más densos. Suelen presentar una microestructura que, si no es adecuadamente tratada o protegida, favorece la formación de óxidos en presencia de humedad y oxígeno.
Por otro lado, las aleaciones sin contenido férrico, como el aluminio, el cobre o el titanio, no contienen hierro en cantidades relevantes. Esto no solo las hace no magnéticas, sino que además les confiere una densidad generalmente menor y una mejor relación resistencia-peso, especialmente valiosa en aplicaciones aeroespaciales y offshore.
Curiosamente, estos materiales reaccionan de manera muy distinta cuando se enfrentan a ambientes agresivos, como sucede frecuentemente en contextos marinos o industriales. Mientras que los compuestos metálicos con base ferrosa son propensos a oxidarse rápidamente, los no ferrosos suelen formar una capa pasiva de óxido (como la alúmina o la pátina de cobre) que actúa como barrera natural contra la corrosión. Esta capacidad de autoprotección, especialmente en aleaciones como el aluminio anodizado, ofrece ventajas clave en términos de durabilidad y mantenimiento.
Comparación de metales ferrosos y no ferrosos
Seleccionar entre metales ferrosos y no ferrosos implica evaluar múltiples variables técnicas y económicas, especialmente en industrias donde la corrosión representa una amenaza constante para la confiabilidad operativa.
A continuación, se presenta una comparación general:
Parámetro | Metales ferrosos | Metales no ferrosos |
Costo | Generalmente más económicos | Más costosos, especialmente en aleaciones nobles |
Resistencia a la corrosión | Baja sin tratamiento superficial | Alta en muchos casos, incluso sin recubrimientos |
Peso | Mayor densidad | Menor peso, ideal en diseños estructurales |
Mantenimiento | Requiere protección y monitoreo continuo | Mantenimiento más espaciado y predictivo |
Conductividad | Baja (excepto en algunos aceros inox.) | Alta (especialmente cobre y sus aleaciones) |
Aplicaciones | Tuberías, estructuras, recipientes a presión | Aeroespacial, intercambiadores, plantas |
En el contexto energético, por ejemplo, este tipo de materiales con base férrica sigue siendo ampliamente usado en ductos terrestres, debido a su bajo costo y alta resistencia mecánica. Sin embargo, en ambientes marinos, ácidos o de alta salinidad, los metales no ferrosos como el titanio o el aluminio anodizado ofrecen una vida útil considerablemente superior, reduciendo costos de intervención y mejorando la continuidad operativa.
Este breve video del canal Patriot Coin Rings explica de forma rápida y clara la diferencia entre metales ferrosos y no ferrosos, repasando su composición, propiedades y aplicaciones industriales:

Corrosión en metales ferrosos
La corrosión en metales ferrosos es un fenómeno ampliamente documentado y, sin embargo, sigue siendo una de las principales causas de fallos en estructuras e instalaciones industriales. Sus mecanismos más comunes incluyen la oxidación directa, la corrosión por picaduras en presencia de cloruros, y fenómenos de corrosión galvánica cuando entran en contacto con metales más nobles.
La salinidad, la temperatura y la humedad relativa son factores ambientales que aceleran estos procesos, particularmente en zonas costeras, ambientes marinos, o instalaciones offshore. La alta concentración de sales disueltas en entornos marinos, combinada con ciclos térmicos y condensación, particularmente crea un entorno altamente agresivo para aceros al carbono y otras familias metálicas de base ferrosa.
Los materiales férreos sufren oxidación acelerada sin pasivación natural, lo que significa que no desarrollan una capa protectora estable por sí mismos. Por eso, requieren tratamientos anticorrosivos como recubrimientos, inhibidores o protección catódica para prolongar su vida útil. Si deseas conocer tecnologías emergentes que están revolucionando este campo, te invitamos a leer el artículo de Inspenet: “Innovación en recubrimientos anticorrosivos inteligentes”.
Casos frecuentes de este tipo de corrosión se observan en tanques de almacenamiento, estructuras portuarias y sistemas de tuberías en terminales marítimos. La norma ISO 9223:2012 proporciona criterios claros para evaluar la corrosividad de ambientes y anticipar el deterioro de estos materiales.
Corrosión en metales no ferrosos
Los metales no ferrosos presentan comportamientos diferentes frente a la corrosión, gracias a su capacidad de generar óxidos protectores de forma natural. Ahora bien, aunque estos materiales ofrecen ventajas, no caigamos en el error de pensar que son invulnerables. Todo depende del entorno y la aplicación. Tipos de corrosión como la intergranular, la por picadura y la corrosión bajo tensión pueden presentarse dependiendo del material, su microestructura y el entorno operativo.
En aleaciones de aluminio, por ejemplo, el óxido superficial (alúmina) actúa como barrera, pero puede perforarse en presencia de cloruros, como los que abundan en entornos marinos. El cobre y sus aleaciones forman una pátina que lo protege de manera efectiva, aunque pueden sufrir corrosión selectiva en presencia de amoníaco o ácidos débiles. El titanio, por su parte, es un verdadero aliado en entornos hostiles. Su resistencia sobresaliente a medios oxidantes o incluso a soluciones de ácido clorhídrico lo convierte en la opción preferida en plantas químicas donde otros materiales simplemente no duran.
Los metales no ferrosos pueden resistir mejor entornos marinos o ácidos, en especial cuando se seleccionan correctamente según la aplicación y se controlan los parámetros de operación.
Aplicaciones típicas incluyen estructuras offshore en aluminio, tuberías HVAC en cobre, y reactores o intercambiadores en titanio. Para una comprensión más profunda, el Journal of Corrosion Science and Engineering de la American Chemical Society (ACS) ofrece investigaciones actualizadas sobre estos mecanismos.
Ejemplos de los metales ferrosos y no ferrosos
En el contexto de la ingeniería y las aplicaciones industriales, conocer los metales ferrosos y no ferrosos más comunes es fundamental para seleccionar materiales que cumplan con los requerimientos de desempeño y durabilidad.
Entre los metales ferrosos, el acero al carbono sigue siendo el más utilizado debido a su resistencia mecánica y bajo costo, especialmente en tuberías, tanques y estructuras. El hierro fundido, por su parte, se emplea en bases de maquinaria y cuerpos de válvulas por su capacidad para absorber vibraciones. Los aceros inoxidables martensíticos ofrecen una resistencia moderada a la corrosión y se encuentran en componentes de turbinas o aplicaciones de alto desgaste.
En cuanto a los metales no ferrosos, el aluminio es ampliamente usado en sectores offshore y aeroespaciales por su ligereza y buena resistencia a la corrosión. El cobre es esencial en sistemas eléctricos y tuberías HVAC gracias a su alta conductividad. El titanio, con su excepcional resistencia química, se aplica en intercambiadores de calor y recipientes a presión. Las aleaciones de níquel se utilizan en turbinas de gas y reactores químicos por su desempeño en altas temperaturas.
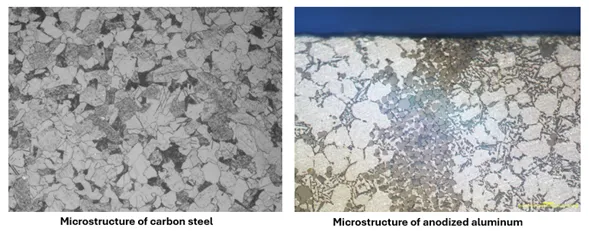
Diferencias de corrosión: metales ferrosos vs no ferrosos
La principal diferencia en el comportamiento frente a la corrosión entre los metales ferrosos y no ferrosos radica en su respuesta electroquímica y su capacidad de formar barreras protectoras.
Las aleaciones con contenido férrico, al contener hierro, son especialmente vulnerables a la oxidación en presencia de humedad y oxígeno. Sin protección adecuada, su degradación puede ser rápida, evidenciada por la formación de óxido (herrumbre) y picaduras. Su vida útil en ambientes agresivos se ve comprometida si no se aplican recubrimientos, protección catódica o estrategias de aleación específicas.
Por el contrario, lo que muchos ingenieros valoran en los metales no ferrosos es su capacidad para autoprotección: una fina película de óxido que actúa como escudo natural frente a la corrosión. Una ventaja que marca la diferencia en ambientes marinos exigentes. El aluminio, por ejemplo, forma alúmina; el cobre, una pátina estable. Estas capas aumentan su durabilidad en ambientes marinos o condiciones ácidas.
Sin embargo, ningún grupo está exento. El diseño adecuado, el uso de recubrimientos protectores específicos y la gestión predictiva del mantenimiento siguen siendo esenciales para extender la vida útil de los activos industriales.
¿Cuál es más resistente a ambientes salinos?
Cuando se trata de resistencia a la corrosión en entornos offshore o marinos, no todos los metales se comportan de la misma manera. La salinidad, combinada con alta humedad y variaciones térmicas constantes, genera uno de los escenarios más agresivos de corrosión en la operación industrial.
Los metales no ferrosos —especialmente el titanio, el aluminio y las aleaciones a base de níquel— están mucho mejor adaptados a estas condiciones que los metales ferrosos sin tratamiento. Su capacidad para formar capas de óxido estables en la superficie actúa como una barrera natural, reduciendo la necesidad de mantenimiento continuo. Por ejemplo, el titanio es prácticamente inmune a la corrosión inducida por cloruros, lo que lo hace ideal para plataformas offshore y plantas de desalinización.
Por el contrario, los compuestos metálicos con contenido de hierro, como el acero al carbono, se oxidan rápidamente si no cuentan con protección externa, como recubrimientos o sistemas de protección catódica. Para mejorar su desempeño en ambientes salinos, son necesarios elementos de aleación (como el cromo en aceros inoxidables), tratamientos metalúrgicos y revestimientos protectores.
Para una guía técnica detallada, las normas NACE MR0175 y DNVGL-CG-0288 ofrecen especificaciones sobre selección de materiales y control de corrosión en ambientes con presencia de cloruros o sulfuro de hidrógeno.
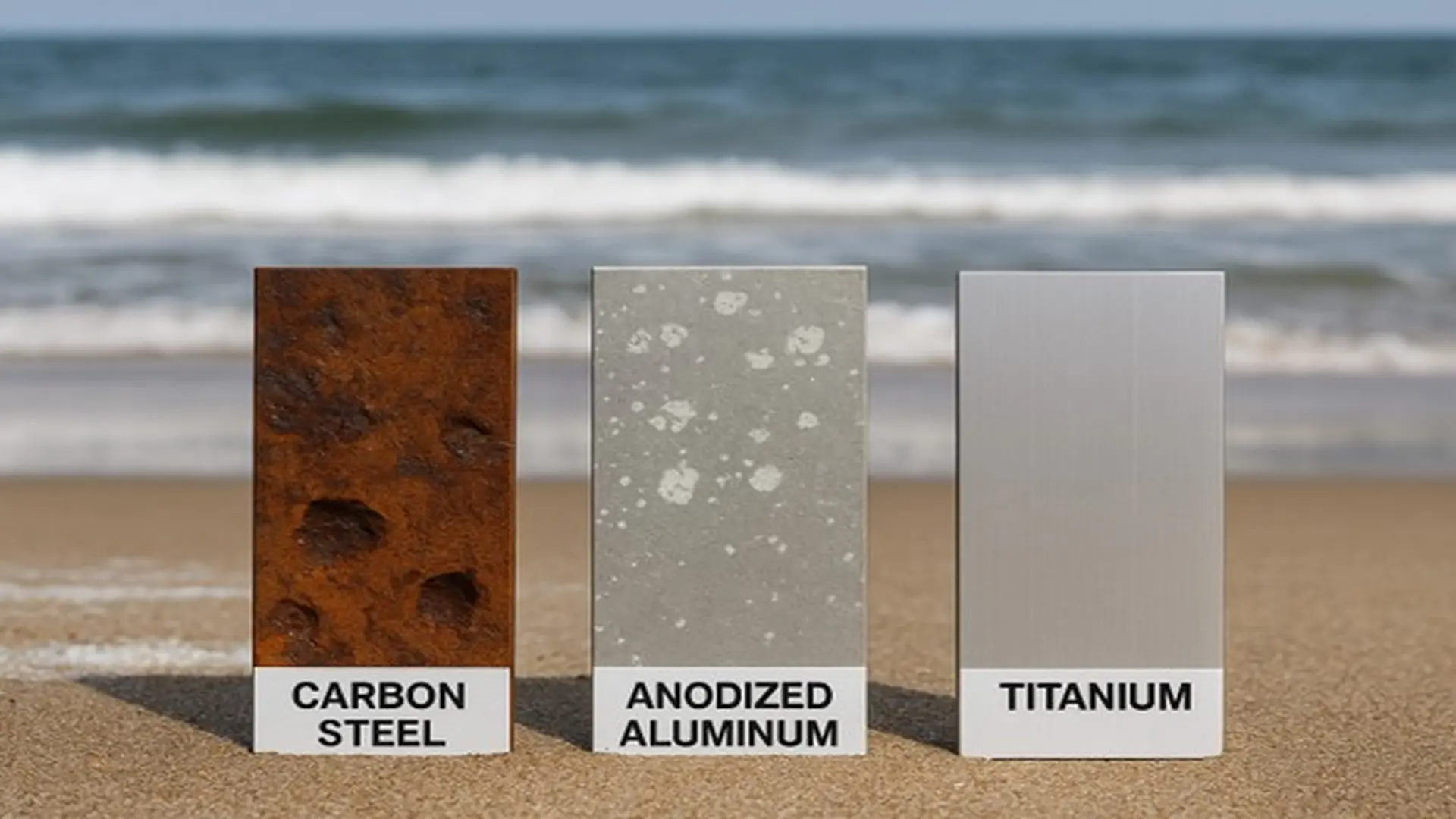
Conclusiones
El comportamiento corrosivo de las aleaciones ferrosas y no ferrosas no es una variable menor en el diseño industrial: es un factor clave que debe considerarse en cualquier proceso de ingeniería, mantenimiento o gestión de activos.
Seleccionar el material adecuado para cada entorno operativo puede marcar la diferencia entre la continuidad exitosa o el fracaso prematuro de una operación. Comprender los mecanismos de corrosión, el papel de la pasivación y la influencia del entorno permite a ingenieros y responsables de activos tomar decisiones más inteligentes y estratégicas.
En sectores críticos como Oil & Gas, energía offshore, ambientes marinos, y petroquímica, este conocimiento se traduce directamente en ahorro de costos, mayor seguridad y vida útil prolongada de los equipos.
No podemos erradicar la corrosión por completo. Pero sí podemos anticiparla, comprenderla y controlarla con inteligencia. Esa es la diferencia entre operar con incertidumbre o con visión estratégica. La selección adecuada de aleaciones, el mantenimiento predictivo, los recubrimientos protectores y el monitoreo ambiental deben formar parte de una estrategia estándar.
Para profundizar en estrategias eficaces de control, monitoreo y selección de materiales frente a distintos tipos de corrosión, te invitamos a leer el artículo de Inspenet: “Retos en la protección de materiales por corrosión”, donde exploramos soluciones aplicadas en sectores como Oil & Gas, petroquímica y ambientes offshore.
(FAQs) sobre la corrosión en metales ferrosos y no ferrosos
¿Qué diferencia la corrosión en metales ferrosos y no ferrosos?
Los metales ferrosos contienen hierro, lo que los hace más propensos a la oxidación, especialmente en ambientes húmedos o salinos. En cambio, los metales no ferrosos, como el aluminio o el cobre, desarrollan capas de óxido que inhiben la corrosión.
¿Qué metales son más resistentes al agua salada?
Metales no ferrosos como el titanio, el aluminio y ciertas aleaciones de cobre superan con creces a los metales ferrosos sin tratar en entornos marinos y ácidos, ofreciendo mayor durabilidad y menores necesidades de mantenimiento.
¿Es posible prevenir completamente la corrosión?
No de forma absoluta, pero sí se puede controlar mediante una combinación de selección adecuada de materiales, recubrimientos protectores, protección catódica y mantenimiento predictivo.
¿Qué normas rigen el control de corrosión industrial?
¿Cuál norma seguir cuando hay tantas opciones? En general, la ISO 9223, la ASTM G1 y las directrices de NACE, hoy AMPP, son el punto de partida más confiable y son ampliamente adoptadas en industrias energéticas, petroquímicas y offshore.
Referencias
- ISO 9223:2012 – Corrosion of metals and alloys — Corrosivity of atmospheres.
- https://www.sciencedirect.com/science/article/pii/S0010938X24000252
- https://pubs.acs.org/doi/10.1021/acscatal.3c00000
- American Welding Society (AWS D3.6M:2017) – Underwater Welding.
- NACE International – Corrosion Basics: An Introduction.
- IUPAC – Standard definitions for metal classification.
- Norma ASTM G1 – Standard Practice for Preparing, Cleaning, and Evaluating Corrosion Test Specimens.