En la compleja industria energética y petroquímica, la construcción y operaciones de oleoductos se destacan como pilares fundamentales para el transporte de hidrocarburos. Estos sistemas críticos no solo conectan puntos de producción con centros de consumo, sino que también representan desafíos únicos en términos de seguridad, medio ambiente y eficiencia operativa.
La gestión de estos retos empieza con un profundo análisis de riesgos en oleoductos. Este enfoque no es solo una medida preventiva, sino una estrategia fundamental que sustenta la integridad y fiabilidad de infraestructuras críticas que transportan diariamente millones de barriles de hidrocarburos a nivel mundial.
Según datos de la Asociación Internacional de Oleoductos, el transporte seguro y eficiente a través de estos sistemas es responsable del movimiento del 60% del petróleo y gas consumido globalmente. Sin un análisis de riesgo meticuloso, las consecuencias de un fallo pueden ser devastadoras, no solo en términos económicos, con pérdidas que pueden superar los miles de millones, sino también en impactos ambientales irreparables y riesgos significativos para la salud pública
Este artículo se sumerge en las prácticas y normativas que rigen el análisis de riesgo, ofreciendo una guía para empresarios, directivos y profesionales del sector energético, industrial y conexo, interesados en optimizar la seguridad y eficiencia de estas infraestructuras vitales.
Importancia del análisis de riesgo en creación de oleoductos
Se denomina oleoducto a la tubería e instalaciones conexas utilizadas para el transporte de petróleo, sus derivados y biobutanol, a grandes distancias. La construcción de oleoductos es compleja y requiere de estudios de ingeniería mecánica para su diseño, así como estudios de impacto ambiental en las áreas donde serán tendidos.
La construcción y operación de oleoductos involucran múltiples fases, cada una con sus riesgos inherentes. Desde el diseño hasta la operación y el mantenimiento, el análisis de riesgos en oleoductos proporciona una base para identificar, evaluar y mitigar potenciales amenazas. Esta práctica no solo es crucial para prevenir derrames o fugas, sino que también garantiza la seguridad de las operaciones, protege el medio ambiente y asegura la continuidad del negocio.
A continuación se presenta el siguiente video para complementar el contenido de este tema “el proceso de construcción de un oleoducto”. Cortesía de X-Machines.
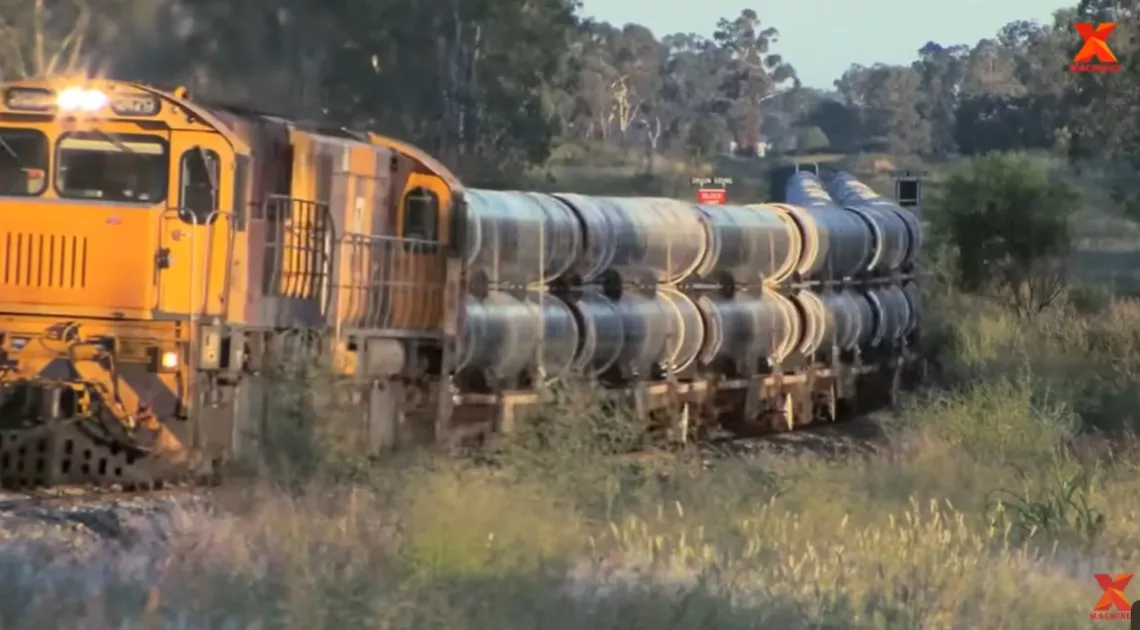
Proceso de construcción de uno de los oleoductos y gasoductos más grandes del mundo.
En términos cuantitativos, se estima que la implementación de programas de gestión de integridad y análisis de riesgos puede reducir los incidentes en los oleoductos en hasta un 40%.
Identificación de riesgos
Todo análisis comienza con la identificación de riesgos. En el contexto de los oleoductos, esto incluye desde fallas técnicas, como la corrosión y fallas mecánicas, hasta desafíos externos, como impactos ambientales y desastres naturales. La metodología para esta fase es diversa, abarcando desde el Análisis Preliminar de Peligros (PHA) hasta el Análisis de Modos de Falla y Efectos (FMEA), subrayando la importancia de un enfoque exhaustivo.
Una identificación de riesgos efectiva es el cimiento sobre el cual se construyen todas las demás fases del análisis de riesgos. Al comprender y anticipar los desafíos únicos que enfrentan los oleoductos, desde su construcción hasta su operación y mantenimiento, la industria puede avanzar hacia una gestión más segura y sostenible de esta infraestructura vital.
Evaluación y análisis de riesgos
Una vez identificados los riesgos, el siguiente paso es evaluarlos cuantitativamente. Utilizando el Análisis Cuantitativo de Riesgos (QRA), los ingenieros pueden determinar la probabilidad y las posibles consecuencias de cada riesgo identificado.
Este proceso se apoya en normas para la construcción de un oleoducto como la API 1160, orientado a la gestión de la integridad de sistemas de tuberías que transportan líquidos peligrosos, y ASME B31.4 (American Society of Mechanical Engineers), proporcionando las directrices para el diseño, construcción, inspección, ensayos y mantenimiento de sistemas de tuberías para hidrocarburos líquidos, derivados del petróleo, gas natural líquido (GNL), dióxido de carbono, y líquidos criogénicos.
Estrategias de mitigación
Con un análisis de riesgos completo, se desarrollan estrategias de mitigación personalizadas. Desde el diseño resistente a condiciones adversas hasta la selección de materiales avanzados y la implementación de sistemas de protección catódica, cada medida se elige cuidadosamente para minimizar los riesgos identificados.
La adherencia a las normas para la construcción de un oleoducto se vuelve indispensable para garantizar la integridad a largo plazo de estas infraestructuras. El American Petroleum Institute es la institución más influyente a nivel mundial, en lo que respecta a normas de ingeniería para la construcción de oleoductos, siendo la especificación API 5L (Especificaciones para Tubería de Línea) la aplicable para la construcción de tuberías para transporte de petróleo crudo, gas, así como derivados de hidrocarburos. La última versión del API 5L fue divulgada en octubre de 2007 en su edición 44ta.
Los oleoductos de tubería de acero son construidos uniendo en el sitio (campo) las series de tubos del diámetro requerido que han sido llevados al lugar del tendido, la unión es generalmente mediante soldadura. Los tubos, por su parte, pueden tener diámetros desde 1/2″ (12,7 mm) hasta 144″ (aproximadamente 360 cm) y vienen de fábricas de tuberías que pueden utilizar diversos métodos para su fabricación; de acuerdo a la norma API 5L, los métodos más usados son:
- Seamless (Sin costura, un tipo de tubería que no es soldada).
- ERW (Electrical Resistance Welding o soldadura por resistencia eléctrica hoy día conocida como High Frequency Welding o HFW).
- SAW (Submerged Arc Welding o Soldadura por Arco Sumergido). De este tipo existe la SAWL (Con costura longitudinal) y la SAWH (Con costura Helicoidal o en Espiral).
Monitoreo y gestión continua
El análisis de riesgo no termina una vez que el oleoducto está en operación. La gestión de riesgos es un ciclo continuo que incluye la inspección regular y el monitoreo de la integridad. Se realizan inspecciones regulares, monitoreo de la integridad del oleoducto mediante técnicas como la inspección por pigging (inspección interna con dispositivos especiales) y el monitoreo de la corrosión. Un ejemplo de inspección remota, es la utilizada por Morken Group utilizada en este contenido para ilustrar a los lectores del tema en cuestión.
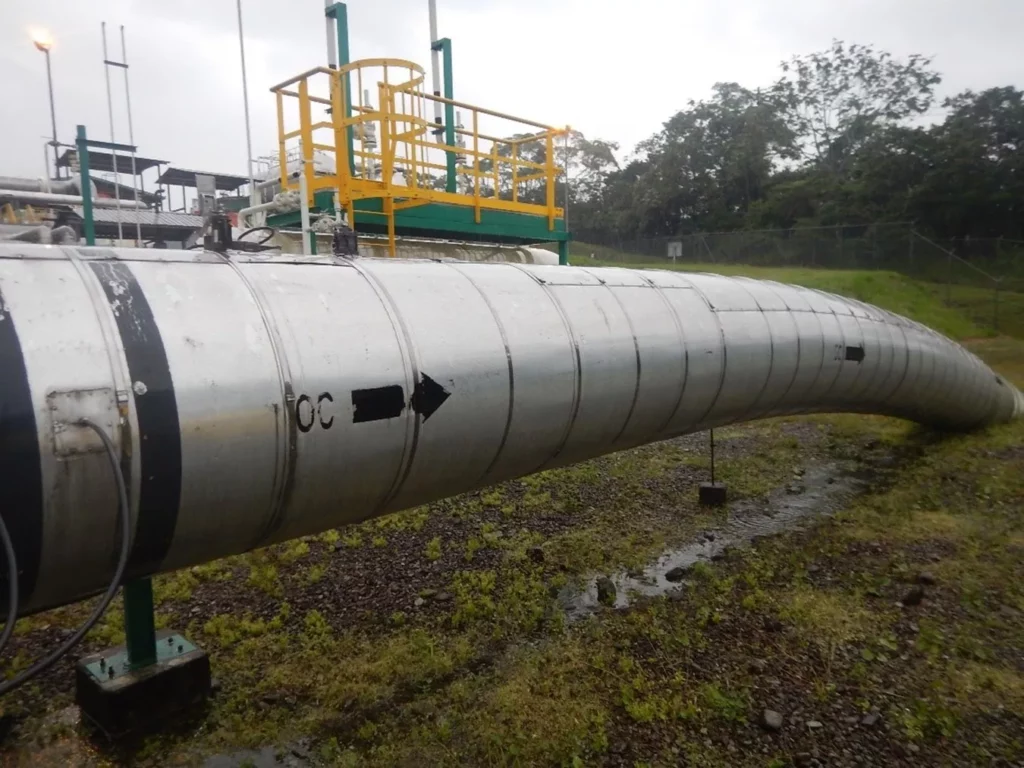
Las normas API (American Petroleum Institute), tiene una serie de estándares clave para oleoductos, incluyendo:
- API 5L: Especifica los requisitos para la fabricación de dos niveles de especificación de tubería de acero para oleoductos.
- API 1104: Establece las prácticas de soldadura para oleoductos y instalaciones relacionadas.
- API 1160: Orientado a la gestión de la integridad de sistemas de tuberías que transportan líquidos peligrosos.
Estas normas ofrecen directrices para el monitoreo continuo y la reevaluación de riesgos, asegurando que cualquier cambio en las condiciones operativas o descubrimientos de nuevas vulnerabilidades se manejen de manera efectiva.
Preparación y respuesta a emergencias
Los oleoductos pueden ser el blanco de vandalismo, sabotaje o hasta de ataques terroristas. En la guerra, los oleoductos suelen ser el blanco de tácticas militares, ya que la destrucción de oleoductos puede romper seriamente la logística enemiga.
Parte integral del análisis de riesgos es la planificación de emergencias. Este componente asegura que, en caso de incidente, se puedan implementar acciones rápidas y efectivas para minimizar los impactos. La realización de simulacros de y la coordinación con autoridades locales son prácticas estándar en esta fase, enfatizando la importancia de una preparación exhaustiva para prevenir derrames o fugas.
Un ejemplo práctico, pero lamentable de este punto, es el accidente del 18 de enero de 2019, donde explota un oleoducto de PEMEX en el estado de Hidalgo, debido a la perforación y mal uso de este, dejando un saldo preliminar de 66 muertos y 79 heridos. Este caso conmovió al mundo y es donde el punto 6 de esta práctica hace énfasis en un buen plan para estar preparado para cualquier emergencia.
Conclusiones
El análisis de riesgo en la construcción y operaciones de oleoductos es un pilar fundamental para asegurar la eficiencia, seguridad y sostenibilidad del transporte de hidrocarburos. A través de una metodología rigurosa que abarca la identificación, evaluación, mitigación y monitoreo continuo de riesgos, así como la preparación ante emergencias, las organizaciones pueden enfrentar los desafíos inherentes a estos sistemas críticos.
La adhesión de estándares por parte de los propietarios, normas para la construcción de un oleoducto y la implementación de mejores prácticas en el análisis de riesgos no solo cumplen con obligaciones regulatorias, sino que también refuerzan la reputación corporativa, fortalecen la confianza de los stakeholders y aseguran una operación responsable ante la sociedad y el medio ambiente.
La construcción y operaciones de oleoductos seguras y eficientes son un objetivo común que beneficia a todos, y mediante el compromiso con el análisis de riesgos en oleoductos, podemos avanzar hacia un futuro energético más seguro y sostenible.
«Protege tu futuro energético: Actúa ahora.»
Referencias
- American Petroleum Institute (API)
- API 5L: «Specification for Line Pipe»
- API 1104: «Welding of Pipelines and Related Facilities»
- API 1160: «Managing System Integrity for Hazardous Liquid Pipelines»
- American Society of Mechanical Engineers (ASME)
- ASME B31.4: «Pipeline Transportation Systems for Liquids and Slurries»