Tabla de Contenidos
- Diseño e ingeniería integral
- Selección y certificación de materiales
- Procesos de fabricación especializados
- Inspección y ensayos rigurosos
- Documentación de control de calidad
- Estampa ASME
- Mejora continua y capacitación
- Implementación de principios de manufactura esbelta
- Colaboración con partes interesadas
- Conclusiones
- Referencias
El aseguramiento de la calidad en la fabricación de recipientes a presión es un proceso importante para garantizar la seguridad, la confiabilidad y el cumplimiento de las normas industriales. Los recipientes a presión, que se utilizan para almacenar gases o líquidos a alta presión, están sujetos a regulaciones estrictas debido a los riesgos potenciales asociados con su falla.
Este artículo expone diversas estrategias para garantizar la calidad en el proceso de fabricación de recipientes a presión, cubriendo aspectos desde el diseño y la selección de materiales hasta la inspección y las pruebas.
Diseño e ingeniería integral
Cumplimiento de normas y códigos: ¿Por qué ASME es tan importante para la fabricación de recipientes a presión?
El primer paso en el aseguramiento de la calidad es garantizar que el diseño del recipiente a presión cumpla con las normas y códigos reconocidos. Organizaciones como la Sociedad Americana de Ingenieros Mecánicos (ASME) proporcionan directrices que dictan el diseño, los materiales, la construcción y las pruebas de los recipientes a presión. El cumplimiento de estas normas garantiza que el recipiente pueda soportar las presiones para las que está diseñado y reduce el riesgo de falla.
Específicamente, la Sección VIII, describe las pautas rigurosas que cubren los procesos de diseño, fabricación, inspección y prueba a los que deben someterse los recipientes a presión antes de que se consideren seguros1.
Análisis de ingeniería
Un análisis de ingeniería exhaustivo es esencial para identificar puntos de falla potenciales y optimizar el diseño. Esto incluye el Análisis de Elementos Finitos para simular tensiones y deformaciones en condiciones operativas. Al comprender el comportamiento mecánico del recipiente, los ingenieros pueden tomar decisiones informadas para mejorar su resistencia y durabilidad.
Selección y certificación de materiales
La selección y certificación, del material adecuado en la fabricación de productos; así como, la correcta elección de materiales mejoran el rendimiento, durabilidad y sostenibilidad de un producto. Ofreciendo propiedades específicas ideales para ciertas aplicaciones. Por otro lado, elegir materiales incorrectos puede llevar a problemas de rendimiento, fallos prematuros y efectos ambientales negativos.
Elección de los materiales adecuados
La selección de materiales es significativa en la integridad de los recipientes a presión, para que puedan soportar altas presiones, temperaturas y ambientes corrosivos. Los materiales comunes incluyen acero al carbono, acero inoxidable y varias aleaciones.
La elección depende de la aplicación específica y las condiciones operativas. La selección de materiales en la fabricación de recipientes a presión es un factor crítico que influye directamente en su durabilidad, rendimiento e idoneidad para aplicaciones específicas1.
Certificación de materiales
Para asegurar la calidad de los materiales, los fabricantes deben obtener materiales de proveedores certificados y requerir informes de prueba de materiales. Estos informes proporcionan información detallada sobre la composición química y las propiedades mecánicas de los materiales, asegurando que cumplan con las especificaciones requeridas.
Procesos de fabricación especializados
Procedimientos de soldadura
La soldadura es el proceso utilizado en la fabricación de recipientes a presión, mediante el cual se aseguran soldaduras de alta calidad, haciendo uso de procedimientos de soldadura calificados y utilizando soldadores certificados.
Las soldaduras de recipientes a presión deben cumplir con los requisitos del código e inspecciones específicas, y estas deben estar libres de defectos. Cuantos más pases de soldadura se requieran, más difícil será hacer que cada pase parezca perfecto. También hay una mayor posibilidad de que existan defectos que requieran retrabajo.
El retrabajo y el tiempo de inactividad asociado cuestan tiempo y dinero, y la realización de excesivas soldaduras fallidas podría hacer que un taller de fabricación pierda su certificación ASME U.
Este sello certifica que el taller produce recipientes a presión que cumplen con los lineamientos de la ASME2.
Mecanizado y ensamblaje de precisión
La precisión en el mecanizado y ensamblaje es necesario para lograr las tolerancias requeridas y el ajuste de los componentes. Se deben implementar técnicas de mecanizado avanzadas y medidas de control de calidad para evitar desviaciones que puedan comprometer la integridad del recipiente.
Inspección y ensayos rigurosos
Ensayos No Destructivos (END)
Los métodos END se emplean para inspeccionar la integridad de los recipientes a presión sin causar daños. Los END comunes incluyen:
- Ensayo de Radiografía (RT): Utilizan rayos X o gamma para detectar defectos internos.
- Ensayo de Ultrasonido (UT): Emplean ondas sonoras de alta frecuencia para identificar fallas.
- Ensayo de Partículas Magnéticas (MT): Detectan defectos superficiales y cercanos a la superficie en materiales ferromagnéticos mediante la aplicación de un campo magnético y partículas magnéticas ferrosas.
- Ensayo de Líquidos Penetrantes (PT): Revelan grietas superficiales y porosidad en materiales no porosos mediante la aplicación de líquidos de alta capilaridad provistos de tintes para una mejor detección.
Pruebas hidrostáticas y neumáticas
Los recipientes a presión se someten a pruebas hidrostáticas y neumáticas para verificar su resistencia y hermeticidad. Este tipo de prueba consiste en llenar con agua presurizada a un nivel superior al de su presión operativa. Las pruebas neumáticas utilizan aire o gases inertes y se realizan a presiones más bajas debido a los posibles peligros, esto debido a la enorme energía que sé puede acumular en el sistema, donde una falla repentina puede producir una enorme explosión.
En el siguiente video se aprecia la realización de pruebas hidrostáticas, procedimiento diseñado para probar la resistencia y las fugas en sistemas de tuberías, calderas, cilindros de gas y recipientes a presión, etc., para confirmar que funcionarán correctamente, incluso en condiciones extremas. . También se requieren pruebas después de reparaciones y paradas para validar si los equipos/tuberías pueden volver a funcionar con éxito. Fuente: PIPING MANTRA Platform.
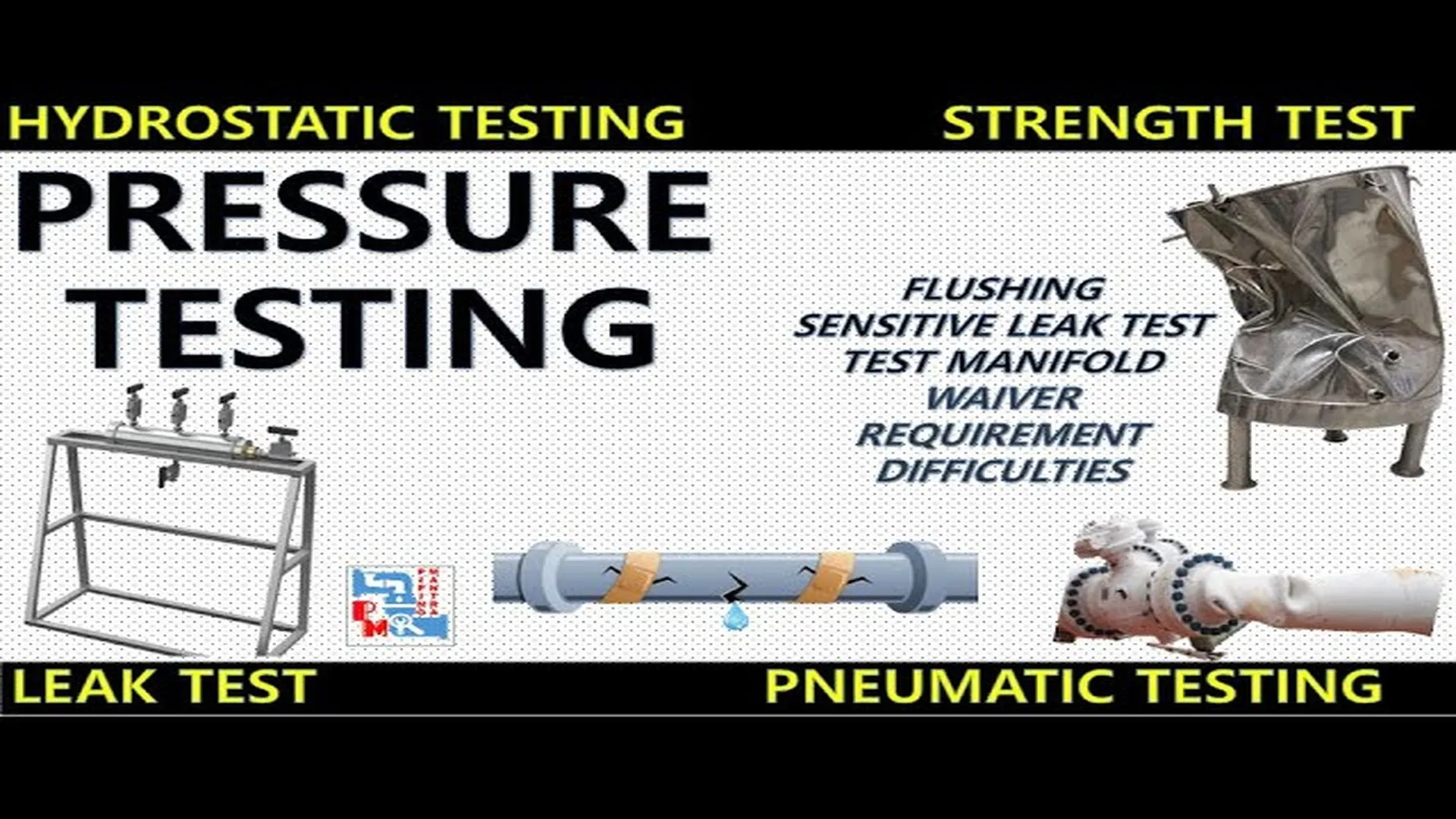
Procedimiento para probar la resistencia y las fugas en sistemas de recipientes a presión.
Documentación de control de calidad
Plan de aseguramiento de la calidad (PAC)
Un PAC describe los procedimientos y responsabilidades para garantizar la calidad a lo largo del proceso de fabricación. Incluye detalles sobre la verificación del diseño, la inspección de materiales, los métodos de fabricación y los protocolos de prueba. Adherirse al PAC asegura un enfoque sistemático para el aseguramiento de la calidad.
Trazabilidad y registro de datos
Mantener registros detallados y la trazabilidad de los materiales, procesos e inspecciones es esencial. Esta documentación ayuda a identificar las causas raíz de cualquier problema y facilita el cumplimiento de los requisitos regulatorios. También proporciona una base para la mejora continua.
Estampa ASME
Seguir las reglas y normas establecidas por el Código ASME, asegura la máxima calidad, integridad y confiabilidad de los recipientes a presión bajo este código, lo que da a los clientes la tranquilidad al adquirir un producto confiable y seguro, garantizado por escrito.
Al cumplir con éxito todos los requisitos, los recipientes a presión reciben una estampa ASME, que sirve como un claro indicador del cumplimiento de ASME BPVC. El tipo específico de sello, como U-Stamp o R-Stamp, depende de la aplicación prevista y el uso del recipiente3.
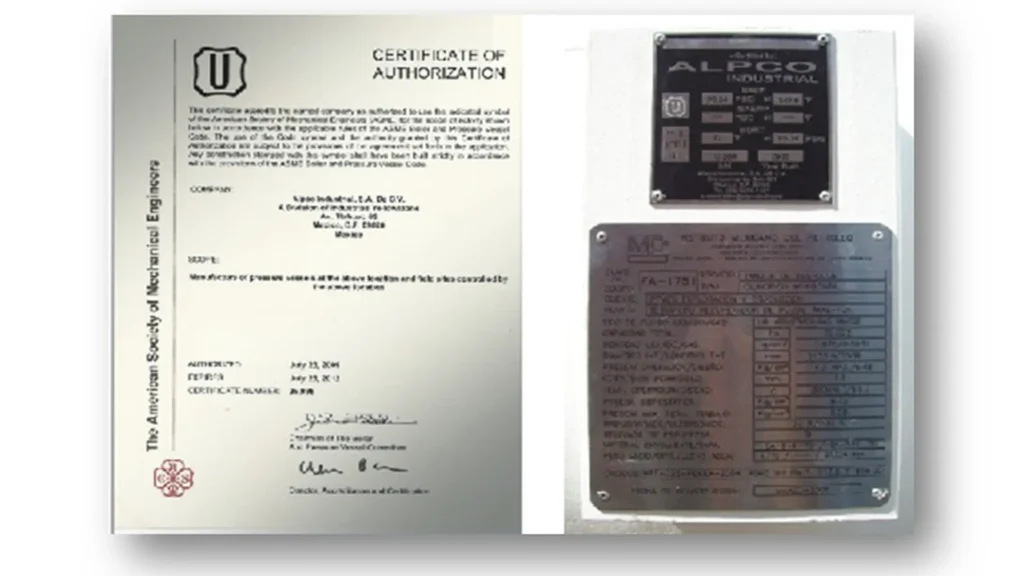
Al cumplir exitosamente con todos los requisitos, los recipientes a presión reciben una estampa ASME; la cual, indica claramente el cumplimiento del Código ASME para calderas y recipientes a presión Código ASME para calderas y recipientes a presión (BPVC). El tipo específico de sello de la marca, como el U-Stamp o el R-Stamp, depende de la aplicación prevista y el uso del recipiente.
Mejora continua y capacitación
Capacitación y certificación de empleados
La capacitación y certificación continua de los empleados involucrados en el proceso de fabricación son cruciales. Esto asegura que estén actualizados con las últimas normas, técnicas y prácticas de seguridad. El personal capacitado y conocedor está mejor equipado para mantener altos estándares de calidad.
Los procesos de calificación y certificación del personal incluyen al personal que realiza las labores de soldadura, Ensayos No Destructivos, inspección de soldaduras y seguimiento del proceso de ensamblaje, entre otros.
Implementación de principios de manufactura esbelta
Los principios de manufactura esbelta se enfocan en reducir desperdicios, mejorar la eficiencia y mejorar la calidad del producto. Al adoptar prácticas esbeltas, los fabricantes pueden optimizar procesos, minimizar defectos y entregar recipientes a presión de alta calidad.
Colaboración con partes interesadas
Gestión de calidad del proveedor
Establecer relaciones sólidas con los proveedores y garantizar que cumplan con los estándares de calidad es vital. Las auditorías regulares y las evaluaciones de desempeño ayudan a mantener la calidad de los materiales y componentes suministrados.
Retroalimentación del cliente y cumplimiento
Involucrarse con los clientes para comprender sus requisitos y retroalimentación es importante para la mejora continua. Asegurar el cumplimiento de las especificaciones del cliente y las normas regulatorias genera confianza y mejora la reputación del fabricante.
Conclusiones
El aseguramiento de la calidad en la fabricación de recipientes a presión es un proceso multifacético que requiere una atención meticulosa al detalle en cada etapa. Desde el diseño y la selección de materiales hasta la fabricación y las pruebas, cada paso juega un papel crucial en garantizar la seguridad y la confiabilidad del producto final.
La implementación de estrategias de aseguramiento de la calidad integrales, los fabricantes pueden cumplir con las normas regulatorias, satisfacer los requisitos del cliente y mitigar los riesgos asociados con las fallas de los recipientes a presión. La mejora continua, la capacitación de los empleados y la colaboración con las partes interesadas son componentes esenciales de un programa robusto de aseguramiento de la calidad que asegura la producción de recipientes a presión de alta calidad.
Referencias
- BAKER INDUSTRIES. Pressure Vessel Fabrication Process: Compliance Standards and Design Best Practices; Consultado en fecha 11 de junio de 2024.
- DAVID JESCOVITCH, JOHN LIMBERIS. La soldadura de pases múltiples en recipientes a presión requiere una preparación y limpieza adecuadas; Consultado en fecha 12 de junio de 2024. https://mexico.weilerabrasives.com/La-soldadura-de-pases-multiples-en-recipientes-a-presion-requiere-una-preparacion-y-limpieza-adecuadas
- ACCRE SURVEYING SOLUTIONS. Inspección de tuberías con el detector de gas para dron Sniffer4D; Consultado en fecha 12 de junio de 2024. https://grupoacre.es/inspeccion-de-tuberias-con-el-detector-de-gas-para-dron-sniffer4d/