Autor: Ing, José Martínez. 21 noviembre 2022.
Introducción
La Identificación Positiva de Materiales (PMI) es un método rápido y no destructivo para verificar la composición química de metales y aleaciones. El PMI portátil y rentable se puede realizar en laboratorios o en el sitio. Los END incluyen técnicas no solamente que permiten evaluar la condición de integridad mecánica, sino también la identificación de materiales para su segregación. Entre las más conocidas se destacan la Fluorescencia de Rayos X o XRF.
En todas las industrias o disciplinas existen ciertas áreas grises; en el caso de la identificación de materiales, no es incorrecto definirla como un END a pesar de su propósito, que es la diferenciación e identificación de materiales metálicos. También se le conoce más comúnmente como PMI por sus siglas en inglés: Positive Identification of Materials. Dependiendo de las necesidades, se usa la Fluorescencia de Rayos X, conocida como XFR, la Espectroscopía de Emisión Óptica u OES, y la Espectroscopía de Ruptura Inducida por Láser o LIBS.
La Identificación Positiva de Materiales es un método rentable para verificar tipos de materiales comunes. Aunque no es tan completo como otros métodos de análisis químico, PMI es una excelente opción para revisar la aleación o el tipo de grandes lotes de materiales, probar componentes terminados, materiales de recertificación y evaluar materiales que no pueden destruirse o enviarse a un laboratorio.
Como ya sabemos, esta diferenciación de aleaciones permitirá la segregación de dichos materiales para su posterior uso. El campo del análisis de materiales ha cambiado enormemente en las últimas décadas. Actualmente, es más fácil que nunca para las compañías encontrar un equipo que se ajuste a sus necesidades.
Esta poderosa herramienta se ha hecho indispensable en infinidad de industrias. Como verificación del control de calidad, principalmente. Estos equipos se han ido haciendo más económicos y sofisticados, como ha ocurrido con la mayoría de nuestras herramientas tecnológicas en esta maravillosa rama de la ingeniería en la que nos desempeñamos.
Y puesto que necesitamos ahora cuidar el ambiente más que nunca, la identificación de materiales que pudieran contener elementos potencialmente dañinos para los ecosistemas se ha ido incrementalmente tomando más en serio. La amplia difusión de equipos electrónicos en el mundo ha hecho necesaria la implementación de normativas como la RoHS, que se refiere a la Directiva 2011/65/UE de Restricción de Sustancias Peligrosas en aparatos eléctricos y electrónicos.
Gracias a una discriminación eficiente de residuos se puede evitar que, por ejemplo, fuentes de agua subterránea sean fatalmente contaminadas con componentes tóxicos presentes en cierto tipo de “basura electrónica”.
Dicho esto, podemos elaborar un poco en la historia de estas técnicas antes de describir someramente sus principios de funcionamiento. Durante mucho tiempo la selección de materiales se hizo con personal experimentado, y con métodos relativamente convencionales: análisis de laboratorio, por ejemplo. Estos métodos consumían tiempo y no se ajustaban a los estándares de productividad de una empresa cuyo negocio medular era, por ejemplo, el de reciclaje de chatarra.
Por lo tanto, se buscó una solución tecnológica, y los resultados fueron positivos. Los aparatos modernos incluso tienen conectividad y conectarse en línea a fin de ajustar los parámetros de lo que va a ingresar a una fundición, por ejemplo. O generar una alerta inmediata al departamento de compras de que un lote de materiales no cumple con las especificaciones del certificado, por ejemplo. De más está decir que esto es una manera de asegurar las propiedades como resistencia al calor, a la corrosión, la soldabilidad, entre otras.
¿Por qué es importante?
Los ensayos de PMI aseguran que cada componente que entra a una planta fue fabricado conforme a las especificaciones. De esta forma, partes críticas que van a ser usadas como reemplazo serán de la aleación y grado adecuados; todos los materiales son exactamente los que deben ser. Y esto puede ser la diferencia entre una operación ininterrumpida, o catastróficas, fallas que pueden llegar a ser fatales.
Este ensayo coloca en manos de los operadores un control de calidad rápido y altamente confiable. Y su amplia aceptación se debe a que es justamente lo que las exigencias del día a día de cualquier planta moderna demandan: una visión periférica de todo el arreglo mecánico, de todos los parámetros críticos, las variables esenciales que pudieran afectar las operaciones, pero con métodos que no las interrumpan.
Vamos a limitarnos a los equipos portátiles que son empleados en campo; la variedad de equipos de laboratorio es vasta, y como inspectores, seguramente estamos (o estaremos) mucho más familiarizados con los equipos que se usan en el campo. El objetivo es claro: confirmar o determinar el grado de una aleación.
Los equipos actuales poseen un altísimo grado de precisión respecto a la diferenciación de aleaciones, y una extensa base de datos que es actualizada constantemente, con lo que la asertividad del ensayo ha crecido mucho. Es de interés destacar que por sus capacidades de detección son de gran utilidad para la verificación de la composición química en cordones de soldadura.
Principios de Fluorescencia de Rayos X
Mediante esta técnica se pueden estudiar la composición no solamente de materiales metálicos, sino que se incluyen muestras incluso de petróleo y minerales.
De nuestras lecciones de física básica, sabemos que los rayos X forman parte del espectro electromagnético. Estos rayos se encuentran en el lado de los rayos de alta energía del ultravioleta; y se expresan en términos de energía en kEv o longitudes de onda en nanómetros. El rango de elementos que puede ser analizado es amplio, desde el sodio hasta el uranio, pudiendo detectar concentraciones desde partes por millón (ppm) hasta altos porcentajes en diferentes morfologías de material, como sólidos, líquidos y material pulverizado.
Todos los instrumentos de XRF se diseñan alrededor de dos componentes: una fuente de rayos X (comúnmente un tubo) y un detector. Los rayos X primarios se generan por la fuente y son dirigidos a la superficie de la muestra, usualmente pasando a través de un filtro para modificar el haz de Rayos X. cuando este haz golpea los átomos de dicha muestra, los mismos reaccionan produciendo una emisión secundaria de rayos X de ciertas características ( ver imagen).
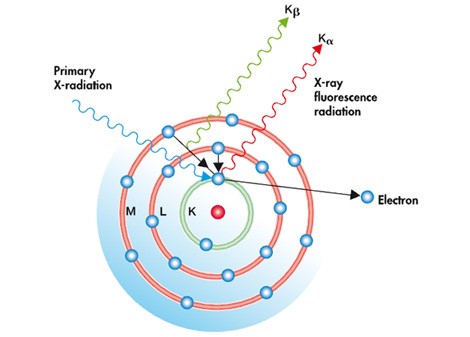
Esta emisión secundaria se produce según lo siguiente: un átomo estable se compone, recordando nuestras lecciones de química básica, de un núcleo y electrones orbitando alrededor de él. Estos electrones están dispuestos en niveles de energía, también llamados lóbulos. Diferentes niveles de energía pueden tener un número diferente de electrones.
Cuando el haz primario de Rayos X de alta energía incide sobre un átomo, altera su equilibrio generando la eyección de electrones de los niveles más bajos de energía, desestabilizando el átomo. A fin de restaurar este equilibrio, un electrón de un nivel más alto de energía cae dentro de esta vacancia. El exceso de energía liberada al generarse este movimiento entre ambos niveles es emitido entonces como rayos X secundarios, los cuales son entonces captados y procesadas por un detector.
Esta energía liberada en el proceso resulta ser característica para cada elemento. Por lo tanto, el XRF es un ensayo de medición cualitativa, que nos indica qué elementos se encuentran presentes y en qué proporción. Información que, convenientemente procesada, es ubicada en una base de datos y el resultado presentado en forma de composición química de los elementos más importantes, y el código con que se denota la aleación en sí.
En los próximos artículos, continuaremos con la descripción de los métodos mencionados. Visita https://inspenet.com/
¡Éxitos!
Sobre el autor.
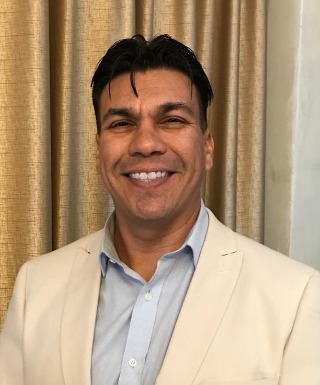
Ing. José Martínez de Munck. 15 años de experiencia en Inspección de equipos para las Industrias de Petróleo y Gas