Tabla de Contenidos
- Propósito de la soldadura por explosión
- ¿Cómo funciona la soldadura por explosión?
- ¿Cómo se aplica la energía explosiva en la soldadura?
- Explosivos más utilizados en soldadura por explosión
- Propiedades de cladding metálico por soldadura explosiva
- Metales disímiles más comunes en soldadura por explosión
- Aplicaciones industriales del revestimiento metálico mediante soldadura por explosión
- Consideraciones en el diseño de la soldadura por explosión
- Controles de calidad en la soldadura por explosión
- Conclusiones
- Referencias
En industrias que enfrentan ambientes agresivos, altas presiones y temperaturas elevadas, proteger los materiales estructurales frente a la corrosión y la erosión es un desafío prioritario. Una de las soluciones más efectivas y confiables es la soldadura por explosión, una técnica de unión en estado sólido utilizada ampliamente en procesos de cladding o revestimiento metálico. Mediante este método se combinan metales disímiles, manteniendo la integridad estructural y las propiedades térmicas originales de los materiales involucrados.
Propósito de la soldadura por explosión
El propósito principal es lograr una unión metalúrgica firme entre metales diferentes mediante el uso controlado de energía explosiva, aplicando un revestimiento metálico resistente sin fundir los materiales, reduciendo defectos térmicos y conservando sus propiedades originales, protegiendo contra la corrosión, erosión, el ataque químico, y además representa una solución económica al evitar el uso completo de metales nobles, al aplicar solo una capa delgada sobre una base estructural más económica.
¿Cómo funciona la soldadura por explosión?
Es un proceso de unión en estado sólido que emplea la energía de una carga explosiva para impulsar dos metales diferentes a un contacto forzado a velocidades extremadamente altas. A diferencia de los métodos de soldadura por fusión, este procedimiento no funde los materiales, lo que elimina la formación de zonas afectadas por el calor (ZAC) y reduce significativamente la aparición de defectos térmicos típicos.
El principio fundamental consiste en posicionar dos placas metálicas, una placa base, generalmente de mayor espesor y menor costo (como acero al carbono), y una placa de revestimiento, más delgada y fabricada con un metal resistente a la corrosión y a la erosión (como acero inoxidable, titanio, cobre o una aleación de níquel).
Sobre la placa de revestimiento se coloca una carga explosiva cuidadosamente distribuida. Al detonar, la explosión genera una onda de choque que impulsa la placa de revestimiento contra la placa base con una velocidad angular óptima, generando una unión metalúrgica firme sin que ocurra fusión. Como resultado, se forma una interfaz ondulada característica del proceso, la cual evidencia la naturaleza sólida de la unión y contribuye al anclaje mecánico entre ambos materiales.
Para mayor información sobre el tema te invito a ver el siguiente video. Fuente: ReP Facts Operational Facts.
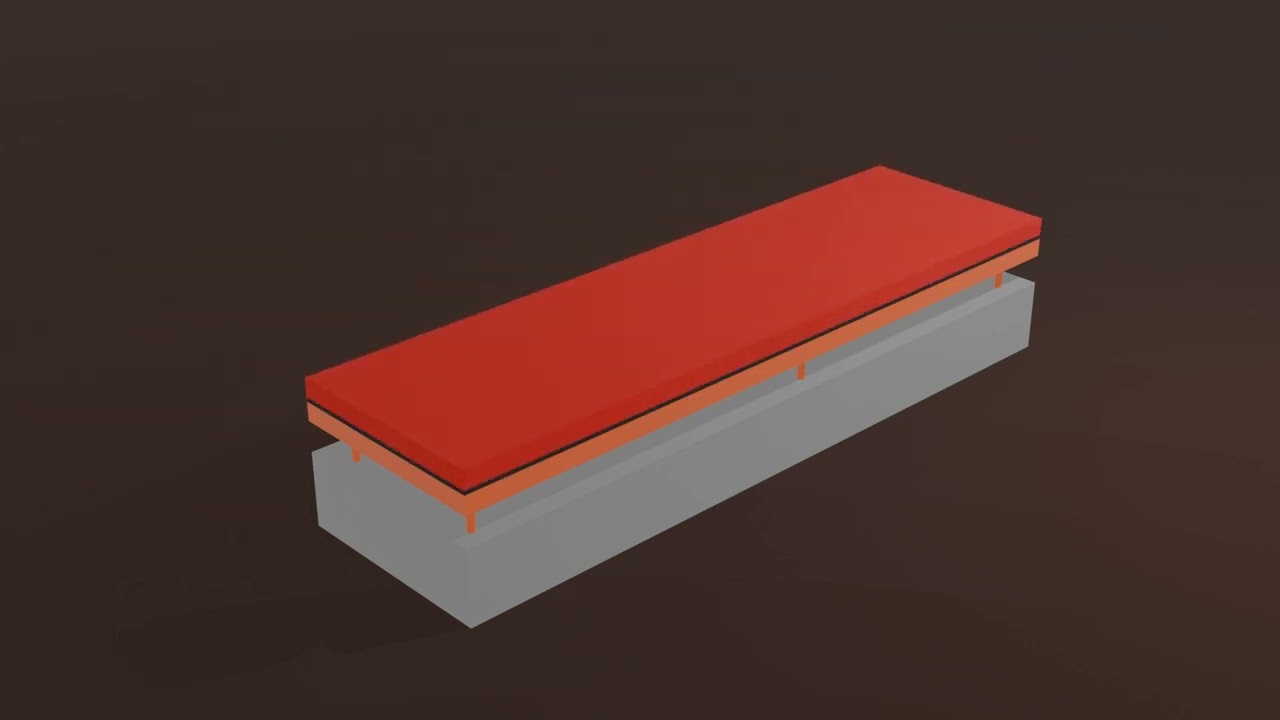
Soldadura explosiva.
Importancia de la interfaz ondulada
La característica zona ondulada de interfaz, generada por la soldadura por explosión, actúa como amortiguador mecánico, ya que:
- Mejora la distribución de las tensiones inducidas por la diferencia de expansión.
- Incrementa la superficie de contacto, aumentando la adherencia.
- Absorbe parte del movimiento diferencial, retrasando la falla por separación.
¿Cómo se aplica la energía explosiva en la soldadura?
La aplicación de la energía explosiva es una etapa crítica del proceso. No se trata de una simple detonación, sino de una técnica cuidadosamente calculada para lograr la unión deseada sin dañar las propiedades de los metales involucrados.
El diseño del proceso considera factores como:
- Tipo y espesor de los metales: Determinan la energía necesaria para lograr la deformación y unión adecuadas sin dañar los materiales.
- Tipo de explosivo y su velocidad de detonación: Afectan directamente la velocidad de colisión y la presión generada, lo cual debe ajustarse al tipo de metales usados.
- Ángulo de impacto entre la placa de revestimiento y la base: Influye en la formación de la zona ondulada y en la eficiencia de la unión metalúrgica.
- Distancia entre las placas al momento de la detonación: Permite controlar la aceleración de la placa de revestimiento antes del impacto, asegurando una unión uniforme y limpia.
El detonador inicia una reacción controlada que genera una presión transitoria de varios gigapascales durante microsegundos. Esta presión impulsa la placa de revestimiento (Cladding) contra la placa de metal base, generando una colisión angular que remueve las impurezas superficiales y propicia una unión metalúrgica efectiva, logrando una unión sólida sin alterar la microestructura de los metales. El resultado es un revestimiento metálico industrial de alta calidad, sin zonas fundidas ni alteración térmica del material base.
Explosivos más utilizados en soldadura por explosión
Los explosivos deben seleccionarse cuidadosamente en función de su potencia, seguridad y adecuación a los materiales involucrados. Entre los más comunes se encuentran:
- RDX (Ciclotrimetilentrinitramina): Es uno de los explosivos más efectivos, con alta velocidad de detonación (~8,750 m/s). Su precisión y potencia lo hacen ideal para obtener uniones limpias con zona ondulada definida. Muy usado en placas bimetálicas de alta calidad.
- ANFO (Nitrato de amonio con fuel oil): Es económico y fácil de manejar. Su velocidad de detonación es moderada (~3,200–4,500 m/s), por lo que se utiliza en aplicaciones de gran escala donde no se requiere una presión explosiva extrema.
- PETN (Pentaeritritol tetranitrato): Muy energético, buena sensibilidad, de uso limitado en mezclas. Velocidad de detonación de ~8,400 m/s. Excelente para capas de revestimiento delgadas.
- C4 (Basado en RDX con plastificantes): Moldeable, resistente al agua, estable bajo manipulación. Velocidad de detonación ~8,040 m/s. Puede adaptarse a geometrías irregulares.
Propiedades de cladding metálico por soldadura explosiva
Las uniones metálicas logradas mediante soldadura por explosión presentan buenas propiedades , entre las que destacan:
- Alta resistencia a la separación: La energía de unión supera ampliamente a la de la soldadura convencional.
- Ausencia de zona fundida: Lo que evita fragilización por solidificación y mantiene la estructura original del grano metálico.
- Interfaz metalúrgica ondulada: Mejora el anclaje mecánico y minimiza el riesgo de despegue.
- Compatibilidad con diferentes sistemas de materiales: Permite unir hasta combinaciones tradicionalmente difíciles, como titanio-acero, cobre-acero o acero inoxidable-aluminio.
El diseño de revestimientos metálicos industriales altamente funcionales y adaptados a entornos exigente, depende de las propiedades antes mencionadas.
Metales disímiles más comunes en soldadura por explosión
La soldadura por explosión combina metales con propiedades físicas y químicas muy distintas. Entre las combinaciones más utilizadas en la industria destacan:
Metal base | Metal de revestimiento (Cladding) |
Acero al carbono | Acero inoxidable |
Acero al carbono | Titanio |
Acero al carbono | Cobre o latón |
Acero al carbono | Níquel o aleaciones de níquel |
Acero inoxidable | Aluminio |
Aplicaciones industriales del revestimiento metálico mediante soldadura por explosión
Es una tecnología estratégica para los sectores industriales que requieren uniones de alto desempeño entre metales disímiles. Algunas aplicaciones incluyen:
- Recipientes a presión: Conforme a ASME VIII Div 1, se emplean placas bimetálicas explosivamente soldadas para revestimientos internos resistentes a la corrosión, mientras que el cuerpo del recipiente mantiene su resistencia estructural.
- Intercambiadores de calor: Donde la alta conductividad térmica y la resistencia a medios agresivos son esenciales.
- Placas bimetálicas: Para columnas de destilación, reactores y equipos de proceso.
- Componentes navales y aeroespaciales: donde el ahorro de peso combinado con resistencia a ambientes agresivos es prioritario.
Consideraciones en el diseño de la soldadura por explosión
El diseño adecuado de una unión mediante soldadura por explosión exige una cuidadosa evaluación de un gran número de variables. Las más relevantes incluyen:
- Compatibilidad metalúrgica: Se deben evitar combinaciones que generen fases frágiles o reactivas entre metales disímiles y que la diferencia en el coeficiente de expansión térmica no sea excesiva (idealmente menor a 5–7 x 10⁻⁶ K⁻¹). Si la diferencia es significativa, se pueden utilizar capas intermedias (por ejemplo, usar níquel entre acero y cobre).
- Energía del explosivo: Debe ajustarse la velocidad de detonación y cantidad de carga para lograr una unión sin dañar las placas.
- Geometría de unión: La distancia inicial entre placas, el ángulo de colisión y el espesor influyen en la calidad de la zona ondulada de interfaz.
- Preparación de superficie: Las placas deben estar limpias y planas para favorecer el contacto y eliminar impurezas.
- El análisis mediante simulación FEM (Finite Element Method): Se emplea para predecir tensiones térmicas, deformaciones y validar parámetros antes de la detonación.
- Normativas: El diseño debe cumplir con estándares como ASTM B898 y ASME VIII.
Controles de calidad en la soldadura por explosión
Para garantizar la confiabilidad de la unión mediante soldadura por explosión, es fundamental establecer controles rigurosos en tres etapas del proceso:
Antes del proceso
- Verificación de materiales: Confirmar especificaciones, certificados y compatibilidad metalúrgica.
- Preparación de superficies: Inspección visual, limpieza mecánica o química para eliminar óxidos y contaminantes.
- Configuración geométrica: Medición de separación entre placas, alineación y control del ángulo de impacto.
Durante el proceso
- Monitoreo del entorno: Condiciones climáticas, seguridad perimetral y estado de confinamiento de la carga.
- Control del explosivo: Tipo, masa, velocidad de detonación y uniformidad de distribución.
- Registro del disparo: Cronología, presión generada y comportamiento del material.
Después del proceso
- Inspección visual y dimensional: Revisión de la continuidad y planitud de la unión.
- Ensayos no destructivos (END): Ultrasonido Arreglo de Fase (PAUT) para verificar adherencia y ausencia de defectos.
- Pruebas mecánicas: Cizalladura, tracción y dureza para validar la resistencia de la unión.
- Ensayar cupones mediante adherencia en caliente (Hot Shear).
Conclusiones
La soldadura por explosión aplicada al cladding de metales disímiles es una técnica avanzada que proporciona uniones confiables, resistentes y eficientes. Su capacidad para preservar la conductividad térmica, evitar zonas afectadas por el calor y resistir condiciones extremas la convierte en una tecnología eficaz para la fabricación de revestimientos metálicos industriales.
Desde placas bimetálicas hasta equipos regulados por ASME VIII, esta técnica continúa expandiendo sus aplicaciones, apoyada por herramientas como la simulación FEM y estándares como ASTM B898. Así, la ingeniería moderna garantiza un equilibrio entre rendimiento, durabilidad y economía en el diseño de componentes críticos.
Referencias
- Zhou, Q., Lu, H., Lan, X., Guo, Y., Liu, K., Huang, G., Jia, B., & Chen, P. (2023). Anisotropy in microstructure and shear properties of TA2/Q235 explosive welding interfaces. Journal of Materials Research and Technology, 25, 6472–6491. https://doi.org/10.1016/j.jmrt.2023.06.129
- https://thetech.com.vn/en/what-is-explosion-welding-advantages-disadvantages-and-applications/
- Inspenet. (2025). Detaclad: Soldadura por explosión – AMPP 2025 [Video]. Inspenet. https://inspenet.com/video-tv/detaclad-soldadura-por-explosion-ampp-2025/
- Inspenet. (s.f.). Finite element analysis applications. Inspenet. https://inspenet.com/en/articulo/finite-element-analysis-applications/