Tabla de Contenidos
- Introducción
- ¿Qué es una soldadura a tope? Definición y fundamentos
- Aplicaciones industriales de la soldadura a tope
- Innovaciones en soldadura a tope: Soldadura orbital
- Soldadura a tope vs. soldadura de filete: Comparación práctica
- ¿Cuándo elegir la junta que aplica?
- Ensayos No Destructivos (NDT) para la inspección de soldaduras a tope
- Normativas y códigos aplicables
- Conclusión
- Referencias
Introducción
La soldadura a tope es una de las uniones más utilizadas en la industria, garantizando seguridad, durabilidad y eficiencia operativa en diversas aplicaciones. Su resistencia y adaptabilidad en la técnica, ha evolucionado significativamente con la introducción de nuevas tecnologías. Sectores como el energético, petroquímico, farmacéutico y manufacturero se benefician enormemente de sus aplicaciones, especialmente cuando se requiere una unión robusta, precisa y confiable entre componentes metálicos.
En este artículo, expondremos el concepto del significado de la soldadura a tope, los avances más recientes en su aplicación, factores como el tipo de bisel, el papel de la soldadura orbital y la efectividad de los ensayos no destructivos (NDT) para garantizar la integridad de las uniones. Además, compararemos soldadura a tope vs soldadura de filete, destacando su aplicabilidad según los estándares de la American Welding Society.
¿Qué es una soldadura a tope? Definición y fundamentos
La soldadura de junta a tope es una técnica de unión en la que dos piezas se colocan en el mismo plano, extremo con extremo, lo que permite una eficiente transferencia de cargas. Este tipo de unión es ideal para estructuras que requieren una integridad mecánica superior, y se aplica principalmente en tuberías, recipientes a presión, estructuras metálicas y componentes industriales críticos.
A diferencia de otras uniones, la soldadura a tope requiere una preparación precisa de los bordes (biselado) y un control riguroso del proceso para evitar defectos internos.
Tipos de bisel y su impacto en la calidad de la soldadura a tope
Una de las decisiones en la ingeniería de una soldadura a tope es la selección del tipo de bisel. Este afecta directamente la penetración del cordón, la eficiencia del proceso y la calidad de la unión. Los tipos más comunes incluyen:
- Bisel en V simple o doble
- Bisel en J o U (usados para reducir volumen de soldadura)
- Sin bisel (para chapas delgadas)
Factores que influyen en la elección del bisel
- Espesor del material: A mayor espesor, se requieren biseles más amplios para permitir una adecuada penetración.
- Tipo de material: Aceros inoxidables o aleaciones exóticas pueden necesitar diseños de bisel especiales para controlar la dilución y evitar fallas metalúrgicas.
- Accesibilidad: En espacios reducidos o soldaduras orbitales, se prefieren biseles que minimicen el volumen de material a depositar.
- Técnica de soldadura utilizada: Los Procesos de soldadura MIG, TIG, o FCAW requieren distintos ángulos y preparaciones.
Impacto en la calidad de la soldadura
Una correcta selección del bisel mejora la calidad de la unión, optimiza el tiempo y los costos, y prolonga la vida útil de la estructura soldada. A continuación, algunos de los impactos más importantes:
- Penetración del cordón y calidad de fusión: La geometría del bisel define la facilidad con la que el calor y el material de aporte alcanzan la raíz de la junta. Una mala selección puede causar:
- Falta de fusión en la raíz o los flancos.
- Inclusiones de escoria en zonas de difícil acceso.
- Exceso de refuerzo, que afecta la fatiga de la unión.
Por ejemplo, un bisel en V simple es suficiente para espesores moderados, pero si se trata de espesores altos, es probable que no se alcance una fusión completa sin múltiples pasadas, aumentando el riesgo de defectos internos.
- Eficiencia del proceso de soldadura: Los biseles afectan directamente el volumen de soldadura requerido, lo que a su vez impacta en:
- Tiempo de ejecución.
- Consumo de material de aporte.
- Costos de energía y mano de obra.
Biseles en J o U, aunque más complejos de preparar, permiten una reducción sustancial en el volumen a rellenar, lo cual mejora la eficiencia, especialmente en aplicaciones automatizadas o de alto volumen.
- Control metalúrgico y prevención de fallas: En materiales como aceros inoxidables, dúplex o aleaciones de níquel, el diseño del bisel ayuda a:
- Minimizar la dilución con el metal base.
- Evitar zonas afectadas por el calor excesivo (ZAC) que podrían volverse frágiles.
- Controlar la geometría de solidificación para evitar microfisuras.
Una inadecuada elección compromete la integridad metalúrgica, e incluso si la unión parece aceptable visualmente.
- Adaptabilidad a la técnica de soldadura: Cada proceso de soldadura tiene requisitos distintos:
- TIG (GTAW) necesita biseles limpios y estrechos, ideales para precisión.
- MIG/MAG (GMAW) requiere accesos más amplios para buena cobertura.
- FCAW permite biseles más cerrados debido a su alta tasa de deposición.
- En soldadura orbital, el diseño debe optimizar la accesibilidad automática.
El tipo de bisel debe complementar las capacidades y limitaciones del proceso seleccionado. En resumen, una selección adecuada del bisel:
- Mejora la calidad de la unión.
- Reduce el riesgo de defectos.
- Optimiza tiempo y costos.
- Prolonga la vida útil de la estructura soldada.
Mientras que una selección inadecuada conlleva:
- Mayores retrabajos.
- Posibles fallas en el servicio.
- Pérdida de eficiencia y sobrecostos.
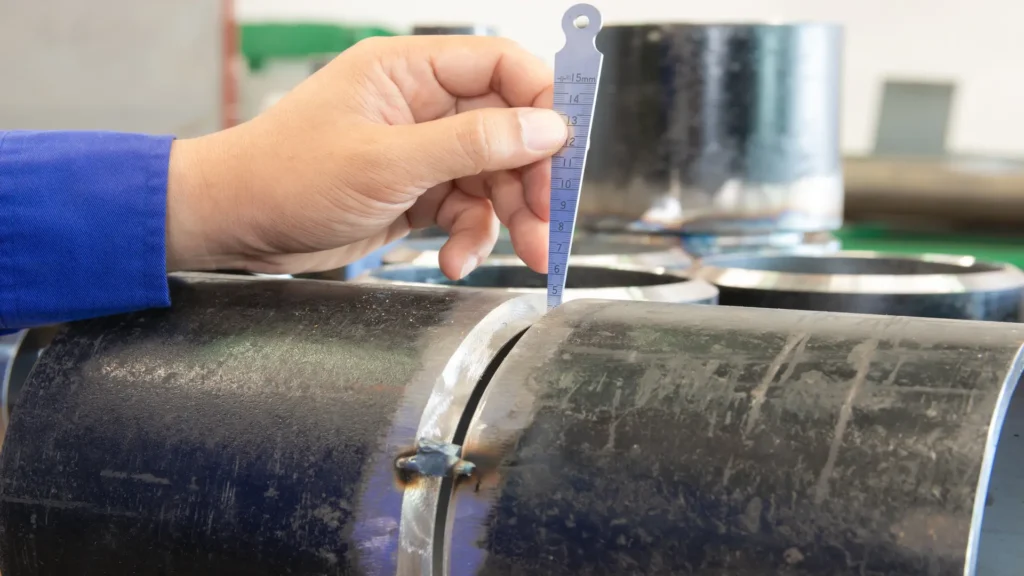
Aplicaciones industriales de la soldadura a tope
La soldadura de junta a tope es fundamental en sectores que requieren alta resistencia estructural, automatización y facilidad de inspección. Algunas de las aplicaciones más destacadas incluyen:
1.Energía, gas y petróleo
- Soldadura de tuberías de alta presión, líneas de transporte de hidrocarburos y recipientes sometidos a esfuerzos térmicos y mecánicos.
- Se aplican códigos como ASME Sección IX, API 1104 y AWS D1.1.
2. Industria nuclear
- Uniones de alta integridad en circuitos primarios y secundarios, donde la resistencia a la fatiga térmica y la fiabilidad son esenciales.
- Requiere trazabilidad completa bajo normativas como ASME III.
3. Alimentos, bebidas y farmacéutica
- Soldadura orbital en tuberías sanitarias de acero inoxidable para evitar zonas de acumulación bacteriana.
- Cumplimiento de estándares como ASME BPE y regulaciones sanitarias.
4. Naval y aeronáutica
- Aplicaciones en estructuras sometidas a vibración, fatiga y ambientes agresivos.
- La soldadura de junta a tope permite reducir peso sin comprometer la integridad.
5. Construcción metálica y estructuras civiles
- Uniones críticas en vigas, columnas y nudos estructurales en edificaciones, puentes y plataformas offshore.
Innovaciones en soldadura a tope: Soldadura orbital
La soldadura orbital ha transformado el proceso de unión a tope, especialmente en tuberías de pequeño y mediano diámetro. Este proceso automatizado mejora la precisión, uniformidad y trazabilidad de las soldaduras, convirtiéndose en un estándar en industrias con altas exigencias.
Soldadura orbital: Definición y fundamentos
La soldadura orbital es un proceso automatizado de soldadura TIG (Gas Tungsten Arc Welding) en el que el arco de soldadura gira alrededor de una pieza estática, generalmente un tubo o tubería. Este método asegura soldaduras consistentes, de alta calidad y repetibilidad, lo que lo hace ideal para aplicaciones que requieren precisión y alta integridad. La soldadura orbital es especialmente útil en industrias que exigen alta fiabilidad, como la aeroespacial, alimentaria, farmacéutica, energética y otras que requieren una soldadura limpia, segura y trazable.
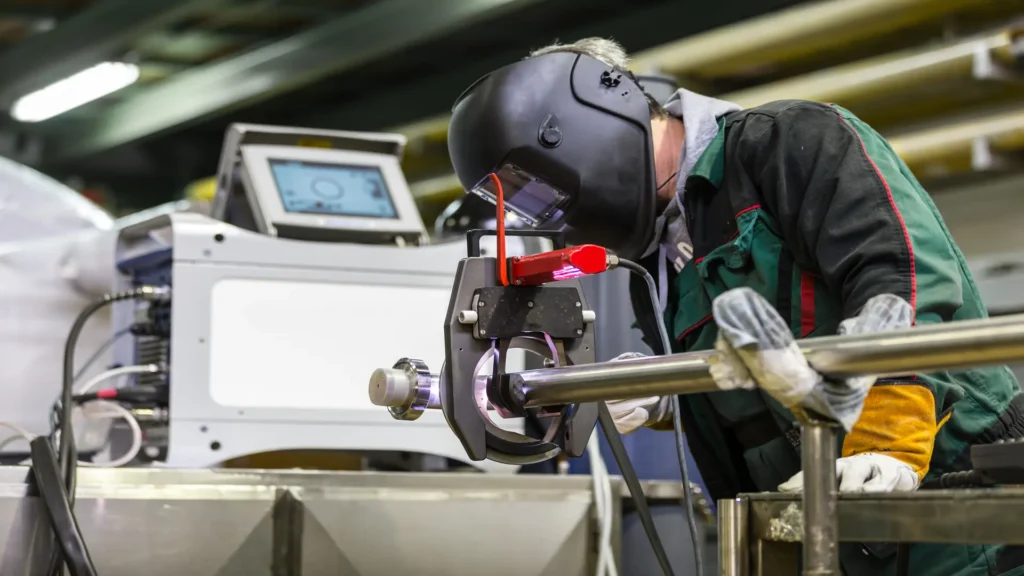
¿Por qué es una innovación para la industria?
- Soldadura automatizada con control automático de parámetros críticos: Regulación constante de voltaje, corriente, velocidad y flujo de gas elimina la variabilidad del operador, garantizando resultados consistentes incluso en ambientes adversos.
- Reducción drástica de defectos: Menor riesgo de porosidad, falta de fusión o penetración incompleta. Esto se traduce en menores rechazos y retrabajos, vital en líneas de producción con altos estándares.
- Productividad sin interrupciones: Al eliminar tiempos muertos entre pasadas y ajustes manuales, se logra una alta tasa de deposición y velocidad de avance, lo que incrementa la eficiencia operativa.
- Trazabilidad total de cada unión: Ideal para auditorías, sistemas de calidad y cumplimiento normativo. Cada soldadura puede ser documentada, rastreada y validada, cumpliendo con estándares como ASME o ISO.
¿Qué la hace especialmente atractiva para el sector energético?
En aplicaciones como líneas de conducción de gas, instalaciones nucleares, refinerías y plantas químicas, donde el fallo de una soldadura puede tener consecuencias catastróficas, la soldadura orbital ofrece:
- Confiabilidad operativa en zonas de difícil acceso o con altas exigencias de integridad estructural.
- Compatibilidad con materiales críticos, como aceros inoxidables, dúplex y aleaciones de níquel.
- Reducción del riesgo humano, clave en proyectos de larga duración y alta presión.
¿Quieres ver cómo funciona una soldadura orbital en acción? Te invito a ver este video y conoce sus ventajas operativas en industrias críticas. Cortesía de: KEPUNIWORLDWIDE.
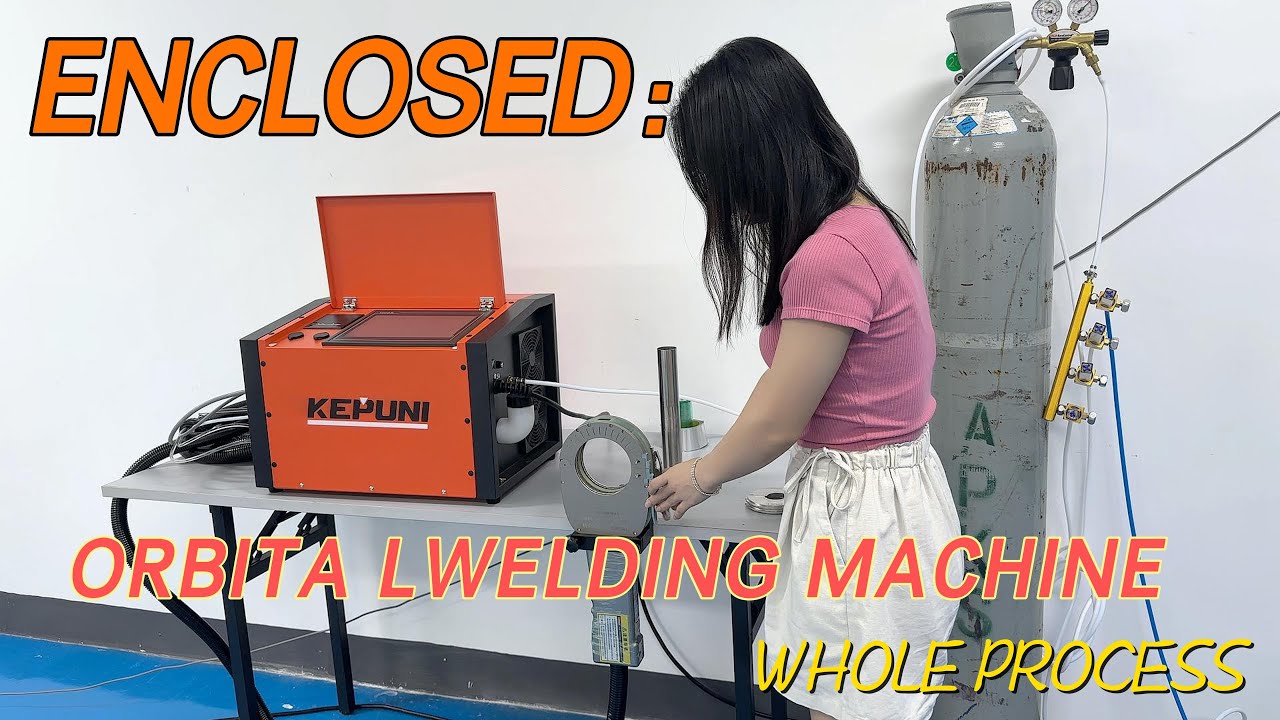
Máquina de Soldar Orbital.
Este recurso visual es ideal para entender su aplicación real en campo, especialmente en industrias como la farmacéutica, alimentaria, energética y nuclear, donde la integridad y limpieza de la unión son críticas.
Soldadura a tope vs. soldadura de filete: Comparación práctica
Tanto la soldadura de junta a tope como la soldadura de filete son fundamentales en la fabricación y montaje de estructuras metálicas. Sin embargo, su elección no es arbitraria: depende del tipo de esfuerzo mecánico, la configuración de las piezas y las exigencias operativas del sistema.
A continuación, una comparación práctica de Soldadura de junta a tope vs soldadura de filete, para facilitar la toma de decisiones en proyectos industriales y energéticos:
Característica | Soldadura a Tope | Soldadura de Filete |
---|---|---|
Tipo de unión | Extremo con extremo | Ángulo entre dos superficies (T, L o esquina) |
Resistencia estructural | Alta – Ideal para cargas axiales o de tracción | Media – Adecuada para cargas de menor magnitud |
Costo y preparación | Mayor – Requiere preparación de bisel y mayor control de alineación | Menor – No necesita biselado, más fácil de ejecutar |
Control de calidad | Más exigente – Inspección rigurosa (NDT, alineación, penetración) | Menos exigente, pero propensa a defectos en cordones mal ejecutados |
Aplicaciones típicas | Tuberías de presión, recipientes, estructuras críticas (nuclear, gas, petróleo) | Refuerzos, soportes, marcos, carrocerías, estructuras secundarias |
En la comparación de soldadura a tope vs. soldadura a filete, la soldadura de junta a tope se prefiere cuando se requiere una alta resistencia estructural y la integridad de la unión es esencial, mientras que la soldadura de filete es más económica y adecuada para aplicaciones con cargas menores o cuando se busca facilidad en la preparación de las piezas.
¿Cuándo elegir la junta que aplica?
Soldadura de junta a tope
Se prefiere cuando se requiere una continuidad estructural total, alta resistencia a la presión interna o una exigente resistencia mecánica. Es esencial en:
- Plantas de energía
- Oleoductos y gasoductos
- Tanques de almacenamiento (API 650/653)
- Estructuras críticas con certificación
Soldadura de filete
Es más económica y flexible, utilizada donde las tensiones son menores o están bien distribuidas. Ideal para:
- Fabricación de estructuras livianas
- Montaje de soportes
- Estructuras auxiliares o temporales
Ensayos No Destructivos (NDT) para la inspección de soldaduras a tope
Los Ensayos No Destructivos (NDT) son herramientas fundamentales para garantizar la calidad, confiabilidad y seguridad de las uniones soldadas sin comprometer su integridad estructural. La implementación de estos ensayos en soldaduras a tope permite detectar defectos ocultos o superficiales que, si no se corrigen, podrían evolucionar en fallas catastróficos, especialmente en aplicaciones críticas como ductos, recipientes a presión o sistemas en plantas petroquímicas y nucleares.
Métodos más eficaces para inspeccionar soldaduras a tope
- Radiografía industrial (RT): Permite visualizar el volumen completo de la soldadura, ideal para detectar: Porosidades internas, Grietas longitudinales, y falta de fusión o penetración. Uso común en soldaduras de tuberías, calderas y equipos presurizados.
- Ultrasonido (UT): Emite ondas acústicas de alta frecuencia para identificar defectos volumétricos y planos con alta precisión, incluso en zonas inaccesibles o de gran espesor. Detecta inclusiones de escoria, grietas y desalineaciones internas.
- Partículas magnéticas (MT): Para materiales ferromagnéticos, revela fisuras y discontinuidades superficiales o sub-superficiales mediante la aplicación de un campo magnético y partículas finas.
- Liquidos penetrantes (PT): Las prueba con líquidos penetrantes es un método de alta sensibilidad para superficies metálicas no ferrosas, donde se busca detectar: Grietas por fatiga, Porosidad superficial, y Discontinuidades de fabricación o durante reparaciones
Normativas y códigos aplicables
Para garantizar uniformidad en los criterios de inspección y aceptación, estos ensayos se rigen por estándares reconocidos a nivel mundial:
- ASME Sección V: Requisitos generales para NDT en sistemas de presión.
- AWS D1.1 (American Welding Society): Norma estructural aplicable a acero estructural, define procedimientos y criterios de aceptación.
- API 1104: Aplicada en soldaduras de tuberías para transporte de hidrocarburos, muy usada en la industria energética.
- ISO 17635 y EN 9712: Normas europeas que definen requisitos de aplicación y calificación del personal de ensayo.
Recomendaciones según la American Welding Society (AWS)
La American Welding Society establece lineamientos técnicos que aseguran la calidad y consistencia de las juntas de soldaduras en distintas aplicaciones.
Algunos aspectos claves recomendados por AWS:
- Preparación adecuada de superficies.
- Control de parámetros de soldadura.
- Calificación de soldadores y procedimientos.
- Aplicación obligatoria de NDT en uniones críticas.
- Documentación de trazabilidad para auditorías.
Cumplir con estas directrices no solo garantiza soldaduras confiables, sino que también permite cumplir con estándares internacionales y normas de certificación ISO y ASME.
Conclusión
La soldadura a tope sigue siendo una técnica fundamental para garantizar la resistencia, durabilidad y seguridad en la industria. Desde la correcta elección del bisel hasta el uso de innovaciones como la soldadura orbital y técnicas avanzadas de inspección, los avances tecnológicos continúan mejorando la eficiencia y calidad de las uniones. Gracias a los estándares promovidos por organizaciones como la American Welding Society, las empresas ahora cuentan con las herramientas necesarias para garantizar uniones seguras, trazables y de larga vida útil.
¡Optimiza tus uniones críticas con tecnología en soldadura a tope!
Referencias
- Soldadura orbital: Una guía completa – Codinter (https://www.codinter.com)
- ASME Sección V: Requisitos generales para NDT en sistemas de presión.
- AWS D1.1 (American Welding Society): Norma estructural aplicable a acero estructural.