Introducción
En un entorno empresarial cada vez más competitivo, las empresas buscan constantemente formas de optimizar sus procesos para mejorar la eficiencia, reducir costos y mantener un alto nivel de competitividad. En este contexto, Lean Manufacturing se ha consolidado como una metodología fundamental para alcanzar estos objetivos.
Lean no se trata solo de reducir costos, sino de crear más valor con menos recursos. Este enfoque, originado en la industria automotriz con la Toyota Production System (TPS), ha evolucionado hasta convertirse en una filosofía integral que aplica a empresas de todos los sectores. Lean Manufacturing es una forma de gestionar los procesos de producción con el objetivo de maximizar el valor y minimizar el desperdicio en cada fase de la cadena de producción.
Pero, ¿cuáles son las características clave de Lean Manufacturing? Si bien Lean tiene varias facetas, existen dos características considerables en las que se basa su éxito a largo plazo: la eliminación de desperdicios y la mejora continua. Estas dos características son fundamentales para que una organización pueda implementar Lean de manera efectiva, optimizando recursos, mejorando la calidad y reduciendo tiempos de ciclo, con el correspondiente incremento de la competitividad.
¿Qué es Lean Manufacturing?
Lean Manufacturing es una filosofía de gestión de la producción que busca optimizar los procesos al eliminar desperdicios y maximizar el valor entregado al cliente con la menor cantidad de recursos posibles. Su origen se encuentra en el sistema de producción de Toyota (TPS), pero hoy en día, su aplicabilidad se extiende más allá de la manufactura, abarcando diversos sectores industriales y comerciales.
El propósito de Lean es hacer más con menos: reducir costos, mejorar la eficiencia y aumentar la calidad, todo mientras se minimizan los desperdicios de tiempo, materiales y mano de obra. A lo largo de su evolución, Lean ha demostrado ser una metodología poderosa que permite a las empresas no solo mantenerse competitivas, sino también fomentar una cultura de mejora continua.
Principios fundamentales de Lean Manufacturing
Aunque Lean Manufacturing incluye diversas estrategias, herramientas y técnicas, todas se basan en los siguientes principios clave:
- Valor para el cliente: Lean comienza con una definición clara de lo que realmente importa para el cliente. Este principio se centra en identificar qué aspectos de un producto o servicio agregan valor al cliente final y qué actividades no lo hacen. Esto permite enfocar los esfuerzos en lo que realmente beneficia al cliente, eliminando todas las actividades que no agregan valor (es decir, los desperdicios).
- Eliminación de desperdicios: Un aspecto central es la eliminación de desperdicios. El desperdicio (o «Muda» en japonés) se refiere a cualquier actividad que consuma recursos (como tiempo, dinero o energía) sin agregar valor al cliente.
- Flujo continuo: Establecer un flujo de trabajo continuo, eliminando interrupciones y cuellos de botella. Esto implica gestionar los procesos de manera que los materiales, la información y las personas se muevan sin obstáculos, reduciendo tiempos de espera y aumentando la eficiencia.
- Producción Justo a Tiempo (JIT): Este principio implica producir y entregar productos solo cuando se necesitan, en la cantidad exacta y en el momento adecuado. La producción Justo a tiempo ayuda a reducir inventarios y a mejorar la eficiencia, asegurando que los recursos se utilicen de manera óptima y no se acumulen productos innecesarios.
- Mejora continua (Kaizen): La mejora continua, también conocida como Kaizen, es un principio fundamental de Lean. Kaizen enfatiza la necesidad de realizar mejoras pequeñas pero constantes en todos los aspectos del proceso productivo, involucrando a todo el personal en la identificación de problemas y la implementación de soluciones. A través de este ciclo de mejora constante, las empresas pueden adaptarse a los cambios del mercado y superar obstáculos operacionales de manera eficiente.
- Respeto por las personas: Aunque este principio puede no ser tan conocido como los anteriores, es significativo en la filosofía Lean. El respeto por las personas implica fomentar un ambiente donde se valore y se aproveche el conocimiento y las habilidades de todos los empleados. En lugar de imponer soluciones desde arriba, Lean promueve la participación activa de los trabajadores en la toma de decisiones y el diseño de procesos, lo que fortalece la cultura de mejora continua.
¿Por qué es importante Lean Manufacturing?
La implementación de Lean Manufacturing tiene múltiples beneficios para las empresas, entre los que se incluyen:
- Reducción de costos: Eliminando desperdicios y optimizar en los procesos, las empresas pueden reducir costos operativos.
- Mayor eficiencia: Mejorando los flujos de trabajo y eliminando ineficiencias, Lean aumenta la productividad.
- Mejora de la calidad: La constante mejora en los procesos y la reducción de defectos conduce a productos de mayor calidad.
- Satisfacción del cliente: Al ofrecer productos de calidad, a tiempo y a un costo competitivo, las empresas pueden mejorar la satisfacción y fidelidad del cliente.
- Mayor capacidad de respuesta al cambio: La mejora continua, la agilidad de las operaciones y la flexibilidad de Lean permiten a las empresas adaptarse rápidamente a cambios en la demanda o en el mercado.
Las dos características clave de Lean Manufacturing
Aunque Lean Manufacturing incluye una variedad de principios, enfoques y herramientas, en este artículo nos vamos a concentrar en dos características esenciales que son fundamentales para el éxito de Lean en cualquier empresa:
- Eliminación de desperdicios (Muda)
- Mejora continua (Kaizen)
Estas dos características son los pilares de la eficiencia operativa y la competitividad, y su implementación efectiva es lo que realmente transforma a una empresa en una organización Lean. A lo largo de este artículo, exploraremos cómo estas características se interrelacionan y cómo puedes implementarlas con éxito en tu empresa.
Impulsando la eficiencia a través de la eliminación de Desperdicios (Muda)
La eliminación de desperdicios, o Muda en japonés, es uno de los pilares fundamentales del Lean Manufacturing. Se refiere a la identificación y eliminación de todas las actividades que no agregan valor al producto o servicio final. La idea principal de Lean es que cada paso en el proceso de producción debe contribuir a la creación de valor para el cliente. Si un paso no lo hace, se considera un desperdicio y debe ser eliminado o minimizado.
¿Qué se entiende por desperdicio?
El desperdicio es cualquier actividad o recurso utilizado que no contribuye directamente al valor final que el cliente percibe. Esto puede incluir tanto recursos materiales como tiempo, esfuerzo humano, energía y espacio, entre otros. El principio básico de Lean es que todo desperdicio debe ser identificado y eliminado, no solo para mejorar la eficiencia, sino también para mejorar la calidad, reducir costos y agilizar los procesos.
Los 7 tipos de desperdicios en Lean Manufacturing
Lean Manufacturing identifica 7 tipos fundamentales de desperdicios que deben ser eliminados. Estos se conocen comúnmente como las 7 Mudas:
- Sobreproducción: Producir más de lo necesario o antes de que se necesite. La sobreproducción es uno de los peores tipos de desperdicio, ya que no solo consume recursos, sino que también genera inventarios innecesarios y reduce la flexibilidad de la empresa.
- Esperas: El tiempo de inactividad de los empleados, equipos o materiales mientras esperan la siguiente tarea o el siguiente proceso. Esto puede incluir esperar la llegada de materiales, esperar por información o esperar que un equipo esté disponible.
- Transporte innecesario: El movimiento innecesario de productos, materiales o información de un lugar a otro. Esto puede incluir el transporte de piezas de un área a otra sin agregar valor al producto.
- Sobreprocesamiento: Realizar más trabajo del necesario, como agregar características al producto que el cliente no requiere o realizar pasos adicionales que no agregan valor.
- Inventarios: Los inventarios son necesarios para mantener la producción, pero tener demasiado inventario genera varios problemas, como espacio de almacenamiento innecesario, mayores costos de mantenimiento y posibles obsolescencias.
- Movimientos innecesarios: Movimientos excesivos o ineficientes realizados por los trabajadores al realizar sus tareas. Estos pueden ser movimientos físicos, como caminar o ajustar herramientas, que no agregan valor al trabajo.
- Defectos: El tiempo y los recursos desperdiciados al producir productos defectuosos o con errores que deben ser corregidos o descartados. La calidad debe ser controlada en todas las etapas de producción para evitar estos defectos.
En este video, se presentan los 5 principios fundamentales del Lean manufacturing para optimizar los procesos. Esta guía ofrece una visión general clara para quienes buscan mejorar sus organizaciones. Cortesía de: TRADESAFE.
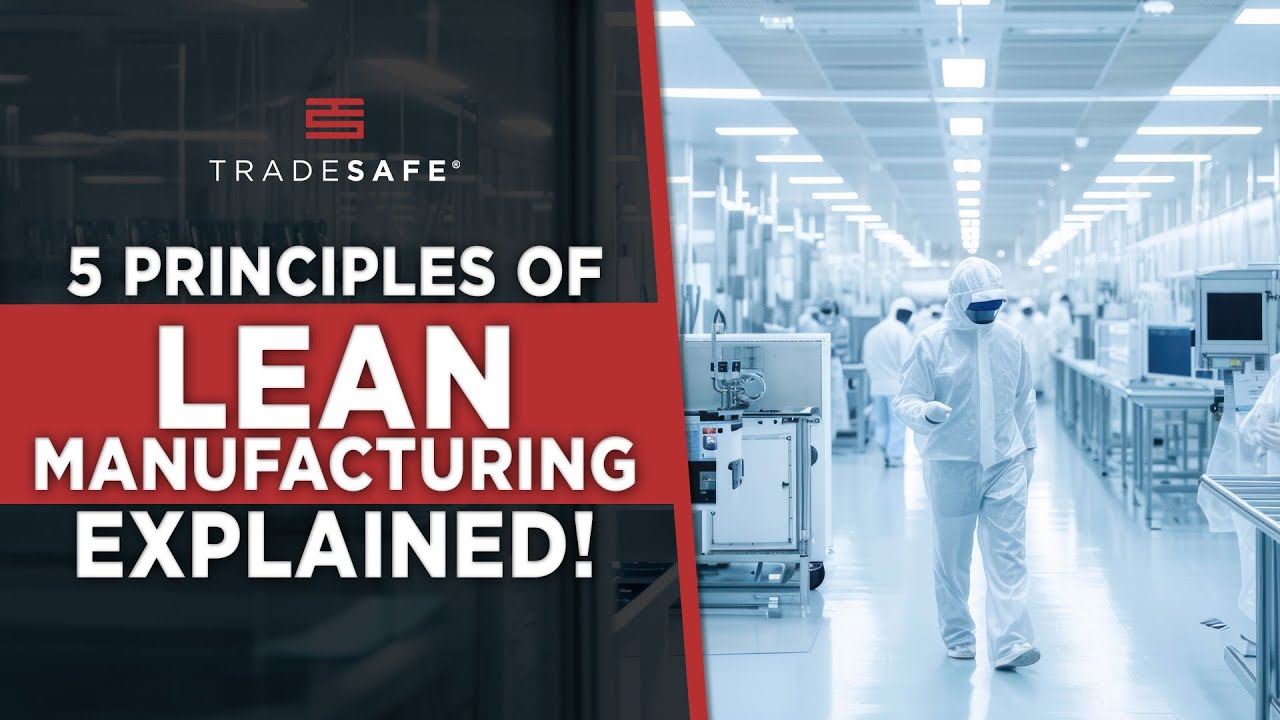
¿Qué es Lean Manufacturing? ¡5 principios explicados!
Impacto de la eliminación de desperdicios
La eliminación de desperdicios mejora la eficiencia, y reduce costos operativos, mejora la calidad y agiliza los tiempos de entrega, lo que resulta en una mayor satisfacción del cliente y una mayor competitividad en el mercado. Al reducir el tiempo que se tarda en producir un producto o prestar un servicio, las empresas pueden responder más rápidamente a las demandas del mercado, mejorar su flexibilidad y tener una mejor capacidad de adaptación.
La eliminación de desperdicios también contribuye a la creación de un entorno de trabajo más saludable y eficiente, donde los empleados pueden realizar sus tareas sin las interrupciones y obstáculos que a menudo surgen de la ineficiencia operativa.
Cómo implementar la eliminación de desperdicios en una organización
- Mapeo de procesos (Value Stream Mapping): Utilizar herramientas como el mapeo de flujo de valor para identificar todas las etapas del proceso y visualizar dónde ocurren los desperdicios.
- Establecer objetivos claros: Fijar metas específicas para la reducción de desperdicios en áreas clave y medir el progreso con indicadores de desempeño.
- Entrenamiento continuo: Capacitar a todo el personal en los principios Lean y fomentar la identificación proactiva de desperdicios en sus áreas de trabajo.
- Herramientas de Lean: Implementar herramientas como 5S (orden y limpieza), Kanban (gestión visual de inventarios) y Kaizen (mejora continua) para respaldar la eliminación de desperdicios.
La mejora continua (Kaizen), característica clave para la competitividad
El concepto de mejora continua, conocido como Kaizen en japonés, es una de las características más poderosas y esenciales del Lean Manufacturing. Se refiere a la práctica de realizar pequeñas mejoras constantes en todos los aspectos de un proceso, ya sea en la producción, en la gestión o en los servicios. La clave de Kaizen es que estas mejoras no necesitan ser grandes o revolucionarias, sino que se basan en un enfoque gradual y sostenible que genera resultados significativos a lo largo del tiempo.
¿Qué es Kaizen?
Kaizen proviene de las palabras japonesas “Kai” (cambio) y “Zen” (bueno), que juntas significan «cambio para mejorar» o «mejora continua». Es una filosofía de trabajo que busca la mejora constante en todos los niveles de la organización, involucrando a todos los empleados en el proceso. Kaizen no se limita a un solo área de la empresa, sino que debe ser aplicado de manera transversal, tocando todos los procesos, desde la línea de producción hasta la alta dirección.
A diferencia de enfoques que buscan cambios rápidos y drásticos, Kaizen enfatiza la evolución constante. Las mejoras son pequeñas, pero acumulativas, y cada acción tomada se enfoca en optimizar procesos y aumentar la eficiencia.
El ciclo de mejora continua: PHVA
Una herramienta central de Kaizen es el ciclo PHVA (Planificar, Hacer, Verificar, Actuar), un proceso iterativo que permite que las mejoras sean constantes y sostenibles:
- Planificar: Identificar el problema o área de mejora, establecer objetivos claros y diseñar una estrategia para implementarlos.
- Hacer: Implementar las soluciones de manera controlada, a menudo en un entorno de prueba o con un grupo pequeño antes de su expansión.
- Verificar: Medir los resultados de las acciones tomadas, compararlos con los objetivos y analizar los datos para verificar si se ha logrado la mejora.
- Actuar: Si los resultados son positivos, hacer los cambios permanentes; si no, ajustar y volver a probar. Este ciclo se repite de manera continua.
Este ciclo permite a las organizaciones adaptarse rápidamente y hacer ajustes según sea necesario, asegurando que los procesos siempre estén evolucionando hacia una mayor eficiencia.
Impacto de la mejora continua en Lean Manufacturing
El enfoque de mejora continua en Lean Manufacturing tiene un impacto significativo en varios aspectos de la operación de una empresa:
- Reducción de defectos: A través de la mejora constante, se identifican y corrigen fallas en el proceso antes de que se conviertan en defectos, lo que mejora la calidad del producto y reduce la necesidad de retrabajos.
- Mayor eficiencia: Kaizen ayuda a identificar áreas donde los procesos pueden ser más rápidos y menos costosos, lo que resulta en una mayor productividad.
- Mejor participación del personal: Al involucrar a todos los empleados en el proceso de mejora, se fomenta un ambiente de trabajo más colaborativo, donde cada miembro del equipo aporta ideas y soluciones.
- Adaptabilidad: La mejora continua permite a las empresas adaptarse rápidamente a los cambios en el mercado, la tecnología o los requisitos del cliente, lo que les da una ventaja competitiva.
Cómo implementar la mejora continua en tu organización
Implementar Kaizen requiere un compromiso continuo con la mejora y un enfoque estructurado. Aquí te presentamos algunos pasos clave para poner en práctica la mejora continua:
- Fomentar una cultura de Kaizen: Todos los niveles de la organización deben estar comprometidos con la mejora continua. Desde la alta dirección hasta los empleados de base, todos deben ser parte activa del proceso.
- Capacitación constante: El personal debe ser capacitado regularmente en las metodologías de Kaizen y en cómo identificar áreas de mejora dentro de sus roles y tareas.
- Involucrar a todos los empleados: Kaizen solo tiene éxito cuando todos los empleados están comprometidos con la mejora. Involucrar a cada miembro del equipo en la identificación de problemas y soluciones garantiza que las mejoras sean prácticas y efectivas.
- Establecer metas claras: Los objetivos de mejora deben ser específicos, medibles y alcanzables. Establecer metas claras para cada ciclo de mejora ayudará a mantener el enfoque y garantizará que los esfuerzos sean efectivos.
- Medir el progreso: El seguimiento de los resultados es crucial para evaluar si las mejoras han sido exitosas. Utiliza indicadores clave de rendimiento (KPIs) para monitorear los avances y asegurarte de que se están alcanzando los objetivos.
- Repetir el ciclo: La mejora continua es un proceso sin fin. Después de cada ciclo, es importante evaluar los resultados y seguir buscando nuevas áreas de mejora.
Cómo implementar Lean Manufacturing con éxito
Implementar Lean Manufacturing no es una tarea que se logre de la noche a la mañana. Es un proceso estructurado y gradual que requiere compromiso, planificación y participación activa de todos los niveles de la organización. A continuación, te detallo las fases clave para implementar Lean Manufacturing de manera exitosa:
Compromiso de la alta dirección: La implementación de Lean Manufacturing comienza con un compromiso absoluto de la alta dirección. Los líderes deben ser los primeros en impulsar el cambio hacia una cultura Lean y apoyar la transformación a nivel organizacional.
Acciones:
- Visión y estrategia: La alta dirección debe comunicar claramente la visión de Lean y cómo encaja dentro de los objetivos estratégicos de la empresa.
- Asignación de recursos: Se debe asignar el personal adecuado, tiempo y recursos para que Lean se implemente de manera efectiva.
- Compromiso con la mejora continua: Es fundamental que los líderes se comprometan a practicar los principios de mejora continua (Kaizen) y que muestren el ejemplo, involucrándose activamente en los proyectos de mejora.
Evaluación y diagnóstico inicial: Antes de comenzar con la implementación de Lean, es necesario realizar un diagnóstico detallado de los procesos actuales. Este paso consiste en evaluar el estado actual de las operaciones de la empresa para identificar áreas de mejora.
Acciones:
- Mapeo de flujo de valor (Value Stream Mapping): Esta herramienta permite visualizar el flujo de materiales e información en el proceso de producción, identificando las áreas donde se generan desperdicios.
- Identificación de desperdicios: Utilizando las 7 Mudas (sobreproducción, espera, transporte, sobreprocesamiento, inventarios, movimientos innecesarios y defectos), se analizan todos los procesos para identificar qué actividades no agregan valor.
- Análisis de indicadores clave: Se deben revisar los KPIs actuales, como el tiempo de ciclo, tasa de defectos, costos y productividad, para tener una referencia clara de cómo mejorar.
Capacitación y entrenamiento del personal: Para que Lean tenga éxito, es esencial que todos los empleados estén capacitados y alineados con la filosofía Lean. Esto incluye no solo al personal de producción, sino también a los supervisores y gerentes.
Acciones:
- Formación en herramientas Lean: Entrenar al personal en herramientas específicas de Lean, como 5S, Kanban, Justo a Tiempo (JIT) y Kaizen.
- Entrenamiento en resolución de problemas: Los empleados deben estar capacitados en técnicas de resolución de problemas, como el análisis de causa raíz y el uso del ciclo PDCA.
- Fomentar la participación activa: Asegurarse de que los empleados comprendan cómo pueden identificar desperdicios y proponer mejoras en sus áreas de trabajo.
Implementación progresiva y proyectos piloto: En lugar de implementar Lean en toda la empresa de inmediato, es recomendable comenzar con proyectos piloto en áreas específicas. Esto permite realizar ajustes antes de una implementación a gran escala.
Acciones:
- Seleccionar áreas piloto: Elegir áreas o procesos donde se puedan obtener resultados rápidos y tangibles con la implementación de Lean, como una línea de producción o un departamento de logística.
- Implementar mejoras específicas: En las áreas piloto, aplicar herramientas como Kanban para gestionar inventarios, 5S para mejorar el orden y la limpieza, y JIT para reducir los tiempos de espera.
- Medir los resultados: Evaluar los resultados del piloto mediante KPIs, como tiempos de ciclo, reducción de desperdicios y mejora en la calidad. Utilizar estos resultados para realizar ajustes antes de expandir Lean a otras áreas.
Medición de resultados y ajustes: La implementación de Lean es un proceso continuo. Es fundamental medir los resultados regularmente para asegurarse de que las iniciativas están logrando los objetivos deseados. Los ajustes deben hacerse de acuerdo con los resultados obtenidos.
Acciones:
- Establecer KPIs: Definir indicadores clave de rendimiento (KPIs) relacionados con la eliminación de desperdicios y mejora continua. Ejemplos de KPIs incluyen tiempos de ciclo, tasa de defectos, nivel de inventarios y costos operativos.
- Monitorear el progreso: Realizar evaluaciones periódicas para medir el impacto de Lean en los procesos y corregir áreas de oportunidad.
- Ajustes y optimización: Basado en los datos recogidos, hacer ajustes en los procesos Lean, ampliar las mejoras a otras áreas y seguir trabajando en la reducción de desperdicios.
Fomentar la cultura Lean: La verdadera transformación hacia Lean Manufacturing solo ocurre cuando Lean se convierte en parte de la cultura organizacional. Esto significa que todos los miembros de la organización deben estar comprometidos con la mejora continua y la eliminación de desperdicios.
Acciones clave:
- Involucrar a todos los niveles: Lean no debe ser solo responsabilidad de la dirección o del departamento de producción. Todos los empleados deben estar comprometidos con los principios de Lean.
- Reconocer logros: Reconocer y premiar a los empleados que contribuyan activamente a la mejora continua y la eliminación de desperdicios.
- Mantener la mejora continua: Asegurarse de que Lean no sea una iniciativa de corto plazo, sino una filosofía de trabajo que perdure en el tiempo.
A continuación se presenta un cuadro en el que se ilustran algunos puntos que relacionan las fases de la implementación de Lean Manufacturing con las dos características fundamentales estudiadas en este artículo.
Características claves del Lean Manufacturing.
Fase de implementación | Eliminación de desperdicios (Muda) | Mejora continua (Kaizen) |
---|---|---|
1. Compromiso de la alta dirección | Definir áreas clave para reducir desperdicios y establecer metas claras para su eliminación. | Impulsar una cultura organizacional basada en Kaizen, donde todos los niveles de la empresa se comprometan a mejorar constantemente. |
2. Evaluación y diagnóstico inicial | Realizar un mapeo de flujo de valor para identificar los tipos de desperdicios en los procesos. | Aplicar Kaizen para detectar oportunidades de mejora continua en los procesos actuales. |
3. Capacitación y entrenamiento del personal | Capacitar en la identificación y eliminación de desperdicios en el día a día, utilizando herramientas como 5S y Kanban. | Enseñar el ciclo PACV y la filosofía de Kaizen para implementar pequeñas mejoras constantes en los procesos. |
4. Implementación progresiva y proyectos piloto | Aplicar mejoras en áreas piloto enfocadas en la eliminación de desperdicios (por ejemplo, reducir tiempos de espera y sobreproducción). | Implementar el ciclo Kaizen en proyectos piloto, donde se hagan pequeñas mejoras de manera constante para optimizar el proceso. |
5. Medición de Resultados y Ajustes | Medir la reducción de desperdicios, como la disminución de defectos y tiempos de ciclo. | Medir los resultados de las mejoras continuas implementadas y realizar ajustes utilizando el ciclo PDCA. |
6. Fomentar la Cultura Lean | Promover la participación activa de todos los empleados para identificar y eliminar desperdicios a nivel individual y grupal. | Reforzar la práctica de Kaizen como parte del ADN de la empresa, asegurando que la mejora continua sea un compromiso diario de todos los empleados. |
Conclusiones
Lean Manufacturing es una metodología para mejorar la eficiencia operativa y reducir costos en las empresas, enfocandose en la eliminación de desperdicios y la mejora continua, de esta forma las organizaciones pueden optimizar los procesos, mejorar la calidad y maximizar el valor entregado al cliente. La eliminación de desperdicios, como sobreproducción, esperas y defectos, es fundamental para eliminar ineficiencias y reducir los costos operativos. Implementar herramientas como el mapeo de flujo de valor ayuda a identificar y eliminar estos desperdicios en todas las etapas de producción.
Por otro lado, la mejora continua fomenta una cultura de innovación constante mediante el ciclo PHVA, que permite realizar pequeñas mejoras continuas y medibles a lo largo del tiempo, contribuyendo al éxito sostenible de la organización. Esta filosofía debe ser adoptada por todos los niveles de la empresa, desde la alta dirección hasta los operativos, para generar un impacto significativo en la competitividad y productividad a largo plazo.
Implementar Lean de manera exitosa requiere un enfoque gradual, comenzando con un diagnóstico claro, capacitación del personal y proyectos piloto. Es un proceso que involucra tanto la reducción de desperdicios como la mejora continua, dos características que deben trabajarse de manera conjunta para lograr resultados eficientes y sostenibles. A través de la adopción de estas prácticas, las empresas reducen costos, y logran establecer una cultura de excelencia operativa que fomente el crecimiento y la innovación constante.
Referencias
- Womack, J. P., & Jones, D. T. (2008). Lean thinking: Banish waste and create wealth in your corporation. Free Press.
- Liker, J. K. (2014). The Toyota way: 14 management principles from the world’s greatest manufacturer. McGraw-Hill.
- Ohno, T. (2008). Toyota production system: Beyond large-scale production. Productivity Press.
- Rother, M., & Shook, J. (2021). Learning to see: Value stream mapping to add value and eliminate muda. Lean Enterprise Institute.
- Imai, M. (1986). Kaizen: The key to Japan’s competitive success. McGraw-Hill.
- Liker, J. K., & Meier, D. (2016). The Toyota way to continuous improvement: Linking strategy and operational excellence to achieve superior performance. McGraw-Hil