Tabla de Contenidos
- Cavitación y su mecanismo
- Detección y diagnóstico
- Tipos de cavitación en sistemas de bombeo
- Fundamentos termodinámicos y fluidodinamicos
- Equipos susceptibles a cavitación
- Estrategias de predicción, diseño y operaciones
- Dinámica de formación de vapor y comportamiento del fluido: claves para prevenir la cavitación
- Estrategias efectivas para prevenir la cavitación y maximizar la vida útil de las bombas
- Conclusiones
- Referencias
La cavitación es un fenómeno hidrodinámico caracterizado por la formación, crecimiento y colapso implosivo de burbujas de vapor en un fluido. En sistemas de bombeo, este fenómeno se produce cuando la presión local del fluido desciende por debajo de su presión de vapor a la temperatura de operación, induciendo un cambio de fase del líquido a vapor, generando microcavidades que, al ser transportadas a zonas de mayor presión, colapsan súbitamente.
El colapso de estas burbujas produce ondas de choque localizadas con presiones transitorias extremadamente altas (hasta 10,000 bar) y microchorros de alta velocidad que impactan contra las superficies metálicas, causando erosión, vibraciones y ruido característico. El conocimiento profundo de la cavitación, sus causas y efectos, permite a los ingenieros implementar medidas preventivas adecuadas, como mantener presiones de entrada óptimas y realizar modificaciones en los diseños de las bombas.
El control del NPSH es clave para evitar la cavitación y maximizar la vida útil de una bomba centrífuga. Una selección y diseño adecuados de la bomba, junto con una correcta instalación y mantenimiento, permitirán operar dentro de rangos seguros, minimizando el riesgo de fallas y mejorando la eficiencia global del sistema de bombeo. Este fenómeno representa uno de los mecanismos de fallo más destructivos en sistemas de bombeo industrial.
Cavitación y su mecanismo
La cavitación es un fenómeno complejo y perjudicial que afecta el rendimiento y la integridad mecánica de las bombas centrífugas. Se trata de un proceso bifásico que ocurre cuando hay una caída significativa en la presión del líquido en zonas específicas del sistema hidráulico, especialmente al paso por el impulsor.
El mecanismo de cavitación comienza cuando la presión del fluido desciende por debajo de su presión de vapor, lo que provoca la formación de burbujas de vapor en la entrada del impulsor. Esta etapa inicial tiene lugar típicamente en el ojo del impulsor, donde el líquido es sometido a una aceleración súbita y, como consecuencia, a una reducción de presión.
A medida que el impulsor gira, las burbujas se desplazan hacia regiones de mayor presión a lo largo de los álabes. En ese punto, las burbujas colapsan violentamente en un proceso conocido como implosión. Estas implosiones generan ondas de choque de alta energía capaces de superar el límite elástico de los materiales que conforman la bomba, en particular del impulsor.
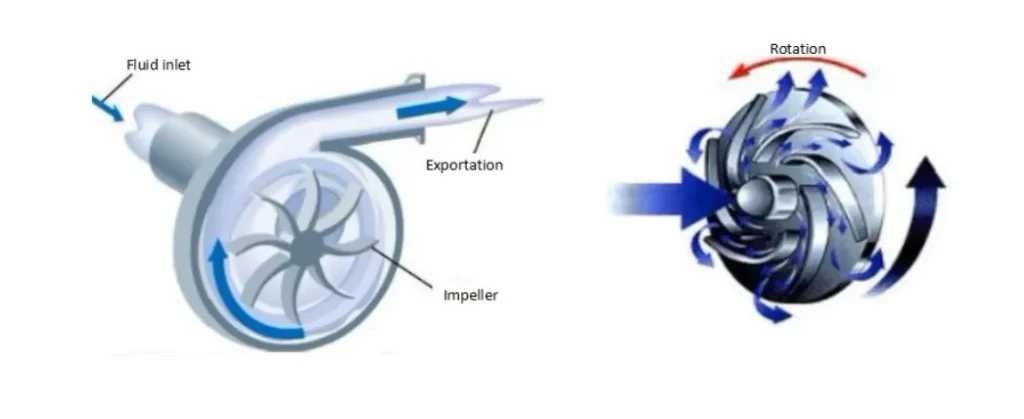
El resultado de este fenómeno son daños localizados en forma de picaduras o cavidades en la superficie metálica, especialmente en los bordes de ataque de los álabes. Con el tiempo, este deterioro se intensifica si la cavitación no se controla, afectando no solo al impulsor sino también, en casos extremos, a la carcasa de la bomba.
Además del daño físico, la cavitación va acompañada de síntomas operativos característicos: ruidos similares a golpes de grava, altos niveles de vibración y una disminución notable en la altura manométrica generada por la bomba. A medida que el fenómeno se agrava, estos efectos se intensifican, provocando pérdida de eficiencia, aumento en los costos de mantenimiento e incluso fallas catastróficas en la maquinaria.
Detección y diagnóstico
La presencia de cavitación puede identificarse mediante los siguientes indicadores:
- Indicadores acústicos: Ruido característico de alta frecuencia (>1 kHz), similar a la circulación de grava.(rocas).
- Indicadores mecánicos: Vibraciones irregulares de alta frecuencia, medibles mediante análisis espectral.
- Indicadores hidráulicos: Degradación de la curva H-Q con caída pronunciada de rendimiento, fluctuaciones de presión y caudal.
- Indicadores térmicos: Incremento localizado de temperatura debido a la energía liberada durante el colapso de las burbujas.
- Manifestaciones físicas: Erosión característica en zonas de baja presión (típicamente cara de succión de álabes), con patrón de «panal de abeja» o superficie esponjosa.
Tipos de cavitación en sistemas de bombeo
- Cavitación de succión: Ocurre en la entrada del impulsor debido a NPSH insuficiente.
- Cavitación de descarga: Se produce en la cara posterior de los álabes, generalmente en condiciones de operación muy alejadas del punto óptimo.
- Cavitación de recirculación: Asociada a flujos secundarios en condiciones de carga parcial o sobrecarga.
- Cavitación de vórtice: Generada por vórtices en la succión que pueden arrastrar aire.
- Cavitación por separación de flujo: Ocurre cuando el fluido no puede seguir los contornos del impulsor debido a geometrías inadecuadas o regímenes transitorios.
Fundamentos termodinámicos y fluidodinamicos
La cavitación está gobernada por la relación entre dos parámetros fundamentales:
1. NPSH disponible (NPSHd): Representa la energía disponible en el sistema para evitar la vaporización del fluido, expresada como:
NPSHd = P₁/γ + v₁²/2g – Pᵥ/γ
Donde:
P₁ = Presión absoluta en la entrada de la bomba. γ = Peso específico del fluido. v₁ = Velocidad del fluido en la succión. g = Aceleración de la gravedad. Pᵥ = Presión de vapor del fluido a temperatura de operación
2. NPSH requerido (NPSHr): Valor mínimo de NPSH necesario para prevenir la cavitación, determinado experimentalmente por el fabricante como la condición donde se observa una caída del 3% en la altura manométrica.
La condición operativa segura exige que: NPSHd > NPSHr + Margen de seguridad (típicamente 0.5-1.0 m).
Como complemento a esta informacion en este video cortesia de «The Ingenieering Mindset», se abordan los principios fundamentales de la presión neta positiva de succión (NPSH) en bombas, para facilitar la comprensión del fenómeno.
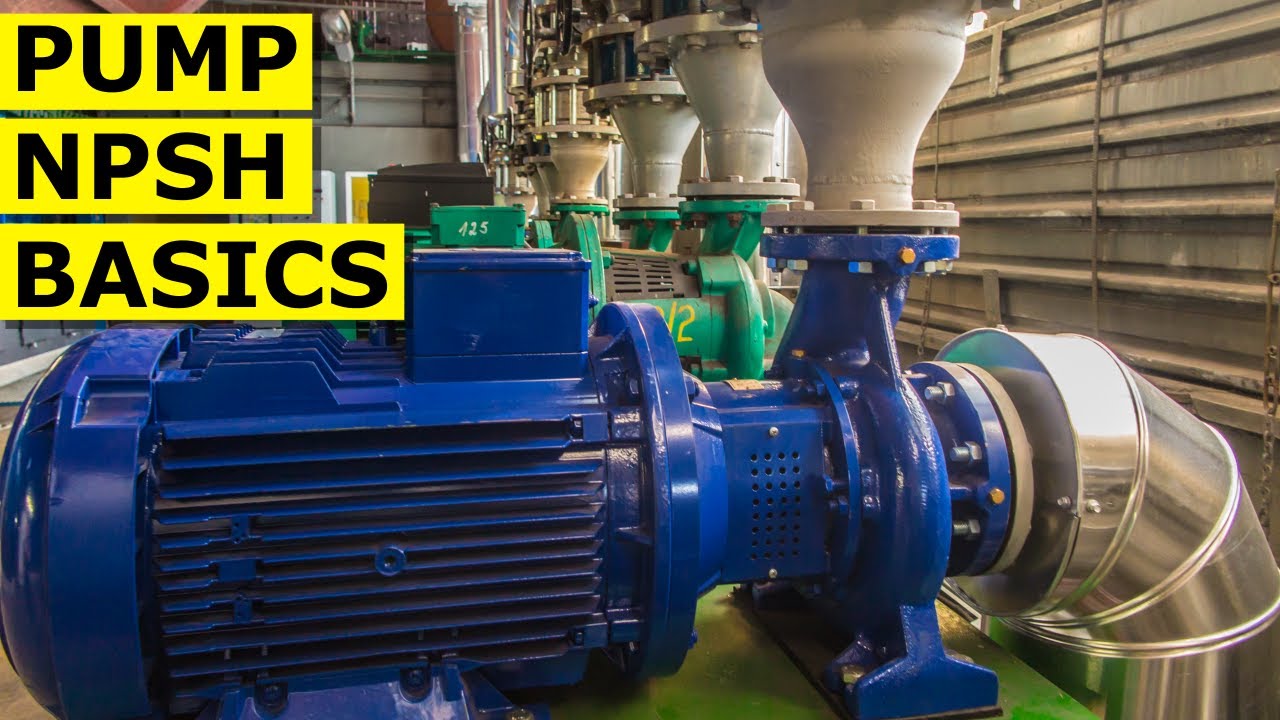
Presión neta positiva de succión (NPSH) en bombas.
Equipos susceptibles a cavitación
La susceptibilidad a la cavitación varía según la tipología de bomba:
- Bombas centrífugas: Particularmente vulnerables debido a las altas velocidades periféricas y gradientes de presión pronunciados. La incidencia es mayor en diseños de alta velocidad específica (Ns>40) y cuando operan fuera de su BEP (Best Efficiency Point).
- Bombas de flujo axial: Extremadamente sensibles a condiciones de NPSH marginales debido a sus altas velocidades específicas (Ns>80). La cavitación típicamente se inicia en las puntas de los álabes donde las velocidades relativas son máximas.
- Bombas de desplazamiento positivo:
- Bombas de engranajes: Susceptibles a cavitación en los puntos de engranaje y en la transición entre cámaras.
- Bombas de tornillo: La cavitación puede ocurrir en los espacios entre los rotores y la carcasa.
- Bombas de pistón/diafragma: La cavitación suele presentarse durante la fase de aspiración, especialmente a altas velocidades.
Estrategias de predicción, diseño y operaciones
Análisis de curvas características de bombas
El análisis de las curvas características de una bomba centrífuga es una herramienta fundamental para prevenir fenómenos como la cavitación y optimizar la operación del sistema. Estas curvas —que relacionan el caudal con la altura manométrica, la potencia absorbida y la eficiencia— permiten evaluar el comportamiento hidráulico del equipo bajo diferentes condiciones de operación.
Una correcta interpretación de la curva H-Q (altura vs caudal) permite identificar el punto de mejor eficiencia (BEP, Best Efficiency Point) y verificar si el sistema opera en condiciones alejadas de este punto, lo cual puede inducir inestabilidades hidráulicas y facilitar la aparición de cavitación. Asimismo, la superposición de la curva de NPSH requerido (Net Positive Suction Head Required) con la curva de NPSH disponible del sistema es clave para asegurar que no se alcance la presión de vapor del líquido.
Las estrategias de mitigación incluyen:
- Ajuste del punto de operación: mediante el rediseño del sistema hidráulico o cambios en la velocidad de rotación.
- Selección adecuada de bombas: considerando condiciones reales de operación y márgenes de NPSH.
- Monitoreo continuo de parámetros críticos: caudal, presión de succión, vibraciones y ruido.
- Uso de variadores de frecuencia (VFD): para mantener el funcionamiento dentro de la zona estable y alejada del régimen de cavitación.
El análisis de la curva carcateristica de una bomba permite predecir condiciones de cavitación, para tomar decisiones informadas con el fin de aumentar la confiabilidad y eficiencia del sistema de bombeo industrial. Para mayor informacion se recomienda ver el siguiente video cortesia de: Central States Industrial Equipment (CSI).
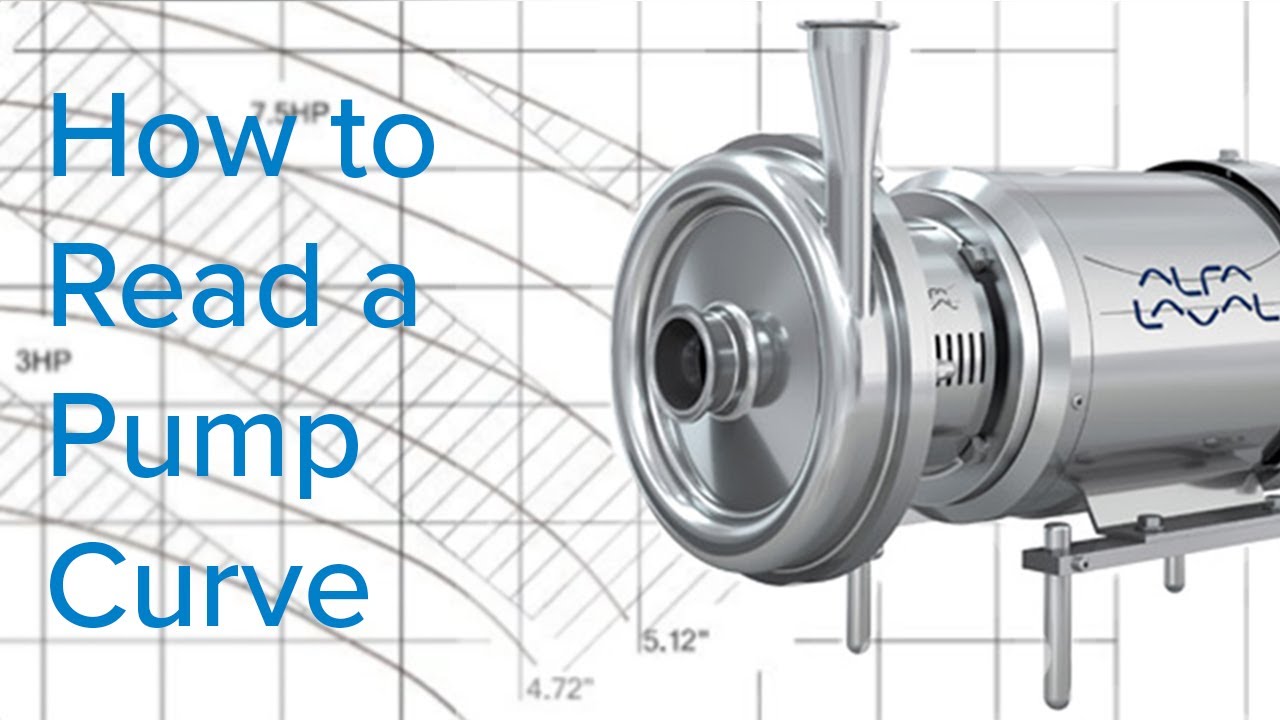
¿Cómo leer la curva característica de una bomba centrífuga?
Diseño y selección
- Sobredimensionamiento selectivo:
- Calcular NPSHd considerando condiciones críticas (temperatura máxima, nivel mínimo, pérdidas máximas).
- Aplicar factor de seguridad: NPSHd ≥ 1.3 × NPSHr para aplicaciones críticas.
- Considerar efectos de la viscosidad y contenido de gases en fluidos no ideales.
- Modificaciones geométricas:
- Implementación de inductores en la succión (reducen NPSHr hasta en un 50%).
- Optimización del ángulo de entrada de los álabes.
- Diseño de impulsores de doble succión para equilibrar cargas axiales.
- Tratamientos superficiales resistentes a la erosión (recubrimientos de estelite, carburo de tungsteno).
- Configuraciones del sistema:
- Sumergencia mínima recomendada en tanques de succión: S ≥ 4D + 0.1v²/2g.
- Instalación de supresores de vórtices o placas deflectoras.
- Minimización de accesorios en la línea de succión (codos, válvulas, reducciones).
- Tubería de succión sobredimensionada (velocidad recomendada < 1.5 m/s).
Condiciones operativas
- Modificación de parámetros operativos:
- Reducción de la velocidad de operación (el NPSHr varía con el cuadrado de la velocidad).
- Incremento de la presión en la succión mediante:
- Elevación del nivel del tanque de succión.
- Reducción de pérdidas en la línea de aspiración.
- Instalación de bombas booster.
- Control de temperatura del fluido (cada 10°C de reducción disminuye significativamente la Pv).
- Control activo:
- Sistemas de detección temprana mediante monitoreo acústico o vibracional.
- Algoritmos de control que eviten operación en zonas críticas.
- Regulación de caudal mediante variadores de frecuencia en lugar de estrangulamiento.
Dinámica de formación de vapor y comportamiento del fluido: claves para prevenir la cavitación
La prevención de la cavitación en bombas centrífugas parte de un principio esencial: evitar la formación de vapor dentro del cuerpo de la bomba. Este fenómeno ocurre cuando la presión local del fluido desciende por debajo de su presión de vapor, lo que induce la formación de cavidades llenas de vapor que, al ser transportadas hacia zonas de mayor presión, colapsan violentamente. El colapso de estas burbujas genera ondas de choque localizadas que impactan directamente sobre las superficies metálicas, provocando erosión, vibraciones y, en casos severos, fallas estructurales.
Influencia de las leyes de afinidad en el riesgo de cavitación
Cuando se realizan modificaciones operativas en una bomba centrífuga, como aumentar la velocidad de rotación o cambiar el diámetro del impulsor, se aplican las leyes de afinidad. Estas leyes permiten estimar cómo varían el caudal, la altura de impulsión y la potencia consumida. Sin embargo, un aumento en la velocidad o el diámetro también incrementa el NPSH requerido, debido a que el líquido se acelera más rápidamente y la presión en la entrada del impulsor puede caer por debajo del umbral de cavitación.
Si el sistema no está diseñado para suministrar un NPSH disponible suficiente, estos cambios pueden inducir condiciones cavitantes. Por ello, antes de aplicar ajustes mediante las leyes de afinidad, es esencial evaluar cuidadosamente su impacto sobre la hidráulica de succión.
La susceptibilidad de un sistema a desarrollar cavitación depende de múltiples factores. Desde el punto de vista del fluido, aquellos con baja gravedad específica o alta presión de vapor presentan una mayor tendencia a vaporizar ante caídas de presión. Por otro lado, las condiciones operativas también juegan un rol determinante: el funcionamiento frecuente a caudales bajos aleja a la bomba de su punto de mayor eficiencia hidráulica, lo cual incrementa las pérdidas de carga y reduce la presión en la entrada del impulsor. Además, en bombas con holguras excesivas en los anillos de desgaste, puede ocurrir recirculación interna de fluido caliente hacia la zona de succión, lo que promueve un entorno térmico desfavorable y facilita el cambio de fase.
El tipo de fluido y su comportamiento frente a la vaporización también influyen directamente en la severidad del daño causado por la cavitación. Los líquidos monocomponentes, como el agua pura, suelen generar burbujas más estables y cargadas de energía. Al colapsar, estas burbujas liberan microimpactos de alta intensidad que erosionan aceleradamente los álabes del impulsor. En contraste, las mezclas de hidrocarburos presentan un comportamiento menos agresivo: su mayor viscosidad y menor tendencia a la vaporización generan burbujas menos energéticas, lo que reduce la magnitud del daño mecánico.
Comprender la interacción entre las condiciones hidráulicas, las propiedades del fluido y el diseño del sistema es esencial para establecer medidas de mitigación efectivas. Estas incluyen la selección adecuada de materiales, el control riguroso del NPSH disponible, el dimensionamiento correcto de los componentes y la operación dentro de los rangos óptimos de caudal y presión. Solo mediante un enfoque integrado es posible minimizar el riesgo de cavitación y prolongar la vida útil de los equipos rotodinámicos.
Factores que promueven la cavitación
La presión dentro de una bomba disminuye desde la brida de succión hasta el borde delantero de los álabes del impulsor, para luego aumentar rápidamente una vez que el líquido está dentro de los álabes. Esta reducción de presión se debe a:
- Pérdidas por fricción en el paso de flujo.
- Aceleración del líquido.
- Pérdidas por impacto de entrada en las puntas de los álabes.
Adicionalmente, la operación a caudales bajos reduce significativamente la eficiencia del impulsor, lo que aumenta la temperatura del líquido y, consecuentemente, su presión de vapor.
La prevención de la cavitación en bombas centrífugas parte de un principio esencial: evitar, en todo momento, la formación de vapor dentro del cuerpo de la bomba. Este fenómeno se produce cuando la presión local del fluido cae por debajo de su presión de vapor, generando burbujas que colapsan violentamente y dañan los componentes internos.
Existen ciertos factores que incrementan el riesgo de cavitación. Los líquidos con baja gravedad específica o alta presión de vapor son especialmente propensos a sufrir este fenómeno, al igual que aquellos sistemas que operan con frecuencia a caudales bajos, donde el impulsor no trabaja en su punto óptimo de eficiencia. Asimismo, las holguras excesivas en los anillos de desgaste pueden favorecer la recirculación de fluido caliente hacia la zona de succión, mezclándose con líquido más frío e intensificando la formación de vapor en el interior.
El impacto destructivo de la cavitación también depende del tipo de fluido y de la cantidad de vaporización que ocurre. En general, los líquidos monocomponentes, como el agua pura, liberan mayor cantidad de energía durante el colapso de las burbujas, provocando microimpactos intensos que aceleran la erosión de las superficies metálicas.
Por otro lado, las mezclas de hidrocarburos, debido a su mayor viscosidad y comportamiento termodinámico, tienden a vaporizar en menor medida y a generar colapsos menos energéticos, por lo que el daño mecánico es generalmente menos severo. Comprender estos factores es fundamental para implementar estrategias eficaces de diseño, selección de materiales y operación, con el objetivo de minimizar el riesgo de cavitación y prolongar la vida útil del sistema de bombeo.
Estrategias efectivas para prevenir la cavitación y maximizar la vida útil de las bombas
La cavitación sigue siendo uno de los principales retos operativos en los sistemas de bombeo, ya que puede provocar daños irreversibles a las bombas centrífugas, reduciendo su eficiencia y vida útil. Para prevenir este fenómeno, es crucial entender los principios fundamentales que lo originan, como las condiciones de presión, la naturaleza del fluido y los parámetros de operación.
El control adecuado de factores como la presión de succión, la correcta selección del NPSH disponible y requerido, y la evaluación detallada de las propiedades del fluido son esenciales para evitar la formación de vapor dentro de la bomba. La aplicación cuidadosa de las leyes de afinidad al realizar ajustes operativos, como cambios en la velocidad de rotación o el diámetro del impulsor, debe ir acompañada de un análisis exhaustivo de sus efectos en el rendimiento hidráulico. Asimismo, el mantenimiento preventivo, que incluya el control de las holguras de los anillos de desgaste y la revisión de los componentes clave, desempeña un papel crucial en la prolongación de la vida útil del sistema.
A través de una correcta planificación operativa, el diseño adecuado de las bombas y un mantenimiento riguroso, se puede maximizar la eficiencia de las bombas centrífugas, minimizando el riesgo de cavitación y garantizando una operación confiable y rentable a largo plazo. Implementar estas estrategias no solo reduce el riesgo de fallas catastróficas, sino que también optimiza el rendimiento general de los sistemas de bombeo industriales.
Conclusiones
La cavitación en bombas es un fenómeno de preocupacion en la ingeniería de fluidos, con implicaciones directas en el diseño, operación y mantenimiento de equipos rotodinámicos. Su manifestación en bombas centrífugas y turbomáquinas puede generar daño localizado por implosión de burbujas, afectando la integridad de componentes como impulsores y carcasa, además de reducir la eficiencia hidráulica del sistema. No obstante, bajo condiciones controladas, la cavitación también puede utilizarse de forma funcional, como ocurre en ciertos procesos de limpieza ultrasónica, donde la acción de las microburbujas facilita la remoción de contaminantes sin necesidad de abrasivos.
Desde un enfoque operativo, la detección de este problema mediante monitoreo de vibraciones, análisis acústico y control de parámetros hidráulicos es clave para mitigar sus efectos y evitar fallas prematuras. La implementación de estrategias de diseño que eleven el NPSH disponible y optimicen la geometría de succión también son fundamentales para prevenir su aparición. Comprender los mecanismos que originan la cavitación permite proteger los activos industriales, y explorar su aprovechamiento en aplicaciones específicas. Su estudio sigue siendo un área crítica dentro de la hidráulica aplicada y el mantenimiento predictivo en entornos industriales exigentes.
Referencias
- Forsthoffer, W. E. (2005). Forsthoffer’s rotating equipment handbooks, Vol. 1: Fundamentals of rotating equipment. Elsevier.
- www.lawrencepumps.com/documents/news_vol1_i5_oct.pdf
- www.pumpfundamentals.com/pump_glossary.htm
- https://evodrop.com/
- Karassik, I. J. P., Messina, J. P., Cooper, P., & Heald, C. C. (2008). Pump handbook (4th ed.). McGraw-Hill.