La Internet de las cosas (IoT) se basa en la interconexión de dispositivos equipados con sensores, software y tecnologías que permiten la comunicación y el intercambio de datos. En el ámbito de la instrumentacion industrial inteligente, el IoT Industrial (IIoT) está transformando la supervisión y el control de procesos mediante redes de sensores avanzadas, análisis en tiempo real y automatización inteligente.
Esta transformación, a menudo denominada «inteligencia de procesos industriales», abarca una amplia gama de tecnologías que mejoran la visibilidad operativa, el mantenimiento predictivo y la eficiencia general del sistema. Una gestión de calidad eficaz implica el control de una amplia gama de parámetros de procesos y máquinas que influyen en la calidad del producto.
En el pasado, el control de calidad en la fabricación era un proceso manual que a menudo era propenso a errores. Con la llegada del IoT, los fabricantes ahora pueden realizar un seguimiento de parámetros de calidad como la humedad, la temperatura, la presión y las partículas con mayor precisión.
Los sensores del IoT ayudan a recopilar datos que pueden determinar qué productos cumplen los estándares de calidad y deben inspeccionarse más de cerca. Esto es especialmente importante para los fabricantes de instrumentacion industrial que cumplen con estándares de calidad como ISO y GMP.
Instrumentación industrial en el control de procesos industriales
La instrumentación industrial es fundamental en la automatización y el control de procesos en sectores como la manufactura, la energía y la petroquímica. Consiste en un conjunto de dispositivos, como sensores, transmisores y controladores, que permiten monitorear y ajustar variables críticas como presión, temperatura, nivel y flujo.
Un sistema de instrumentación está compuesto por un conjunto de instrumentos interconectados que trabajan en conjunto para garantizar mediciones precisas y consistentes. Estos sistemas incluyen sensores, transductores, conexiones físicas y software de automatización que aseguran la repetibilidad y fiabilidad de las mediciones.

En las plantas industriales, el control y la medición de variables son fundamentales para garantizar la eficiencia, seguridad y calidad de los procesos. Entre las principales variables físicas que se monitorean están el caudal (másico y volumétrico), la presión, la temperatura, el nivel (de líquidos y sólidos), la velocidad, el peso, la humedad y el punto de rocío.
En cuanto a las variables químicas, destacan el pH, la conductividad eléctrica y el potencial redox, esenciales para mantener el equilibrio químico y evitar problemas como la corrosión o la contaminación. La instrumentación precisa de estas variables permite un control efectivo, optimizando recursos y asegurando operaciones confiables.
La eficiencia en los procesos productivos, depende de estos instrumentos porque abarca el uso de elementos diseñados para medir, convertir, transmitir y controlar variables clave, además aseguran la calidad y la seguridad en la operación, y optimizan los recursos empleados, reduciendo costos y mejorando la sostenibilidad.
El sensor es el componente esencial de este sistema, encargado de captar una variable física, como temperatura o presión, y transformarla en una señal interpretable. Los transductores, a su vez, convierten estas señales en formas útiles para el registro o el control, como señales eléctricas o mecánicas.
La medición, que consiste en asignar un valor específico a una variable física, es la base para tomar decisiones fundamentadas en tiempo real. Los sistemas de instrumentación industrial permiten realizar estas mediciones con alta precisión, mejorando así la regulación, supervisión y seguridad de los procesos productivos.
Factores clave de la instrumentación industrial inteligente
La instrumentación inteligente en la Industria 4.0 aprovecha la analítica avanzada de datos y la conectividad para transformar el control y la supervisión de procesos. Este cambio de paradigma, abarca cinco factores clave:
Los instrumentos inteligentes trascienden las funciones de medición tradicionales al generar datos auxiliares, incluida la información de diagnóstico.
Estos dispositivos utilizan protocolos de comunicación avanzados como Ethernet/IP u OPC-UA, lo que permite la integración directa en las redes del sitio, evitando los intermediarios del sistema de control convencional.
Esta arquitectura permite que los sistemas de control se centren en las funciones principales, mientras que los datos de mantenimiento, calibración y puesta en servicio son accesibles en niveles jerárquicos superiores como SCADA.
Capacidades de diagnóstico avanzadas
Los dispositivos inteligentes modernos, como los caudalímetros, emplean diagnósticos sofisticados tanto en sensores como en transmisores para detectar anomalías físicas o desviaciones de calibración. Los sensores analíticos, incluidas las sondas de pH y conductividad, han evolucionado a salidas principalmente digitales con soporte de protocolo avanzado.
Estos sensores digitales proporcionan métricas críticas, como ciclos operativos, desviación de calibración y estado general del sensor, lo que facilita la toma de decisiones basadas en datos para la calibración y el reemplazo de componentes.
Ventajas de protocolo mejorado
Los instrumentos conectados a Ethernet ofrecen un rendimiento de datos superior en comparación con las señales tradicionales de 4-20 mA, con una complejidad de cableado reducida.
Por ejemplo, un caudalímetro magnético ahora puede transmitir datos de temperatura, conductividad y caudal a través de una única conexión Ethernet, lo que elimina la necesidad de múltiples salidas analógicas y reduce potencialmente tanto los costos como los requisitos espaciales.
Acceso a los datos en instalaciones conectadas
En una instalación de la Industria 4.0 completamente conectada, los datos de instrumentación son fácilmente accesibles a través de interfaces móviles, lo que permite la supervisión de procesos a pedido y la localización de equipos.
La conexión directa de instrumentos a sistemas SCADA o historicos a través de protocolos abiertos facilita la programación proactiva del mantenimiento y la generación de órdenes de trabajo, lo que mitiga el tiempo de inactividad no planificado y deja obsoletas las alarmas de calibración tradicionales basadas en PLC.
Utilización y análisis de datos
Los voluminosos datos generados por los instrumentos inteligentes requieren estrategias de gestión de datos sofisticadas. Los paneles personalizados para la limpieza, organización y visualización de datos proporcionan información valiosa para los procesos de toma de decisiones.
Al aprovechar estos datos, los fabricantes pueden implementar algoritmos de mantenimiento predictivo, optimizar los procesos de producción y mejorar la eficiencia operativa general.
Una buena planificación de la integración de sistemas de control
La integración de sistemas de control no es una capa funcional que se encuentra sobre el diseño de una instalación; es el diseño de la instalación, o un componente de este. Su equipo de integración de sistemas de control debe trabajar junto con los ingenieros de procesos e instalaciones para alinear las decisiones de diseño iniciales con la filosofía general de controles de la planta.
El aporte de las personas que representan a los equipos de operaciones, mantenimiento, calidad y otros en toda la planta es clave. Incorporar esta perspectiva multidisciplinaria en las actividades iniciales de diseño y planificación de procesos sentará las bases para una estrategia de integración de sistemas de control resiliente y significativa.
¿Qué es la IoT industrial (IoT)?
Las tecnologías de IoT existen a nuestro alrededor: todos esos dispositivos interconectados que usamos, como las tecnologías portátiles y los asistentes virtuales, son posibles gracias a la IoT.
La IoT industrial, entonces, está tomando la interconectividad digital de la que hemos llegado a depender y aplicándola a operaciones de fabricación masivas, donde los riesgos son mayores, pero la recompensa es mayor. A medida que la industria manufacturera pasa de las funciones automatizadas y los sistemas conectados de la Industria 4.0 a la personalización mejorada y la computación cognitiva de la Industria 5.0, se puede pensar en la IIoT como un enfoque de la fabricación más centrado en el ser humano.
Sensores IoT y redes Inalámbricas conectividad y datos en tiempo real
Las Redes Inalámbricas de Sensores (WSNs, por sus siglas en inglés) desempeñan un papel esencial en el ecosistema del Internet de las Cosas (IoT). Estas redes permiten la conectividad sin interrupciones y la recolección de datos en tiempo real desde sensores distribuidos en diferentes ubicaciones. Al aprovechar las ventajas de las WSNs, la tecnología IoT está logrando avances significativos en eficiencia, monitoreo y automatización.
Una red inalámbrica de sensores es un sistema compuesto por pequeños nodos sensores de bajo costo y consumo energético que se comunican entre sí de forma inalámbrica a corta distancia. Cada nodo está equipado con transductores, microcomputadoras, transceptores y una fuente de energía, lo que les permite medir variables físicas o químicas del entorno y transmitir estos datos a una estación base o gateway.
Este enfoque no solo mejora la capacidad de monitoreo en tiempo real, sino que también facilita el análisis avanzado de los datos, abriendo nuevas posibilidades en sectores como la industria, la agricultura, las ciudades inteligentes y la salud. En un mundo cada vez más conectado, las WSNs son el pilar que permite que los sensores IoT transformen la forma en que interactuamos con nuestro entorno.
A continuación, se muestra un tutorial, cortesía de Sentec®, donde se presentan los distintos tipos de sensores de IoT, de temperatura, presión y sensores de nivel. En este video comprenderás las capacidades y funcionalidades de los diferentes sensores de IoT.
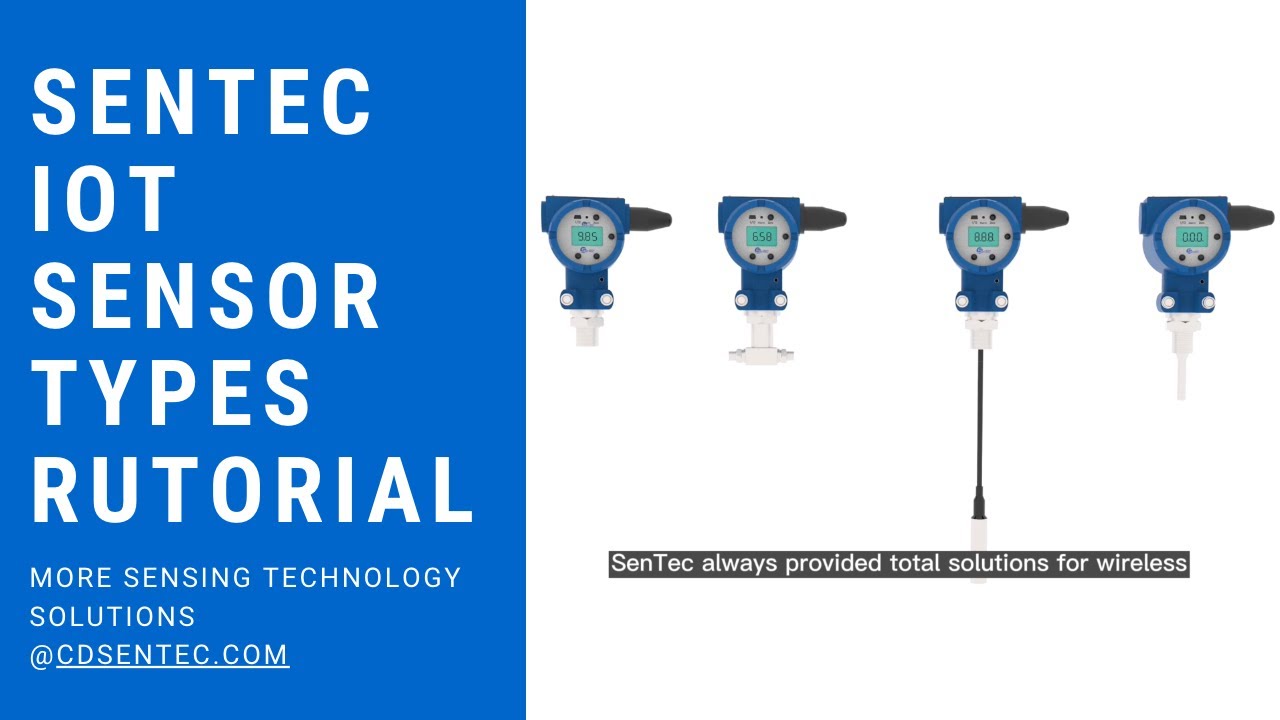
Tipos y aplicaciones de los sensores IoT.
La transformación digital en fabricación, denominada Fabricación inteligente, permite a los operadores optimizar la toma de decisiones mediante el análisis de datos masivos generados por la Industrial Internet of Things (IIoT). Esta estrategia requiere una inversión integral en la digitalización operativa, fundamentada en cuatro componentes tecnológicos críticos:
- Infraestructura de sensórica inteligente: Dispositivos y máquinas habilitados con sistemas de monitoreo digital que capturan, registran y transmiten datos operacionales en tiempo real. La sensórica inteligente se refiere a los sensores que cuentan con microprocesadores incorporados para procesar los datos que obtienen.
- Arquitectura de computación en la nube: Plataformas informáticas escalables con capacidad de almacenamiento y procesamiento distribuido que garantizan la integridad y disponibilidad de los datos industriales.
- Sistemas de inteligencia analítica: Herramientas avanzadas de procesamiento de datos que transforman la información cruda en perspectivas estratégicas, permitiendo la optimización predictiva de procesos manufactureros.
- Capital humano especializado: Recurso técnico cualificado, entrenado en la interpretación y aplicación de análisis de datos, capaz de implementar mejoras operativas y mantener la eficiencia del ecosistema tecnológico.
Adopción de IoT en la fabricación
Se entiende que el IoT industrial integrado es una parte esencial del futuro de la fabricación, impulsando estrategias de generación de ingresos como la monetización de datos y nuevos modelos comerciales tanto como equipo como servicio.
Mantenimiento predictivo en la fabricación
Nada afecta más negativamente a una operación de fabricación que el tiempo de inactividad de las máquinas. Los expertos estiman que el fabricante promedio experimenta 800 horas de inactividad de los equipos al año, lo que suma un costo de $50 mil millones al año en gastos no planificados para toda la industria.
Cuando el mantenimiento en el mundo de la fabricación es reactivo en lugar de proactivo, los fabricantes se quedan atascados tratando de identificar cuál es el problema, cómo se puede reparar y cuánto costará. Con el mantenimiento predictivo impulsado por soluciones de IoT industrial, todos esos problemas se alivian.
Dimensiones del impacto del IIoT
1. En torno de producción:
- Monitoreo predictivo en tiempo real de condiciones de fabricación.
- Habilitación de toma de decisiones basado en datos para mantenimiento preventivo.
- Seguimiento de seguridad ocupacional mediante sistemas de geolocalización y telemetría.
- Análisis de capacidad productiva con modelado de escenarios dinámicos.
2. Operaciones de campo:
- Telemetría de flota para evaluación de rendimiento integral.
- Implementación de mantenimiento predictivo mediante análisis de patrones de desgaste.
- Supervisión virtual de equipos con geolocalización y diagnóstico remoto.
- Reducción de tiempos de respuesta mediante gestión proactiva de servicios.
3. Gestión de cadena de suministro:
- Monitoreo integral de flujos logísticos con sensórica distribuida.
- Control de condiciones ambientales durante transporte y almacenamiento.
- Detección temprana de potenciales disrupciones mediante análisis predictivo.
- Trazabilidad de extremo a extremo de los movimientos de inventario.
4. Coordinación de operaciones distribuidas:
- Plataforma centralizada de gestión de procesos tercerizados.
- Auditoría digital de cumplimiento de estándares.
- Estandarización de protocolos de calidad y rendimiento.
La implementación de IIoT representa una transformación sistémica que trasciende la mera digitalización, constituyéndose como una estrategia de optimización organizacional fundamentada en inteligencia de datos.
Componentes de IoT
Una arquitectura de solución de IoT comprende varios componentes críticos:
Dispositivos conectados
Estos abarcan una variedad de elementos interconectados, que incluyen:
- Sensores y actuadores para adquisición y control de datos.
- Sistemas integrados y microcontroladores (MCU) para procesamiento local.
- Módulos de comunicación para transmisión de datos.
Las consideraciones clave incluyen:
- Tipos y especificaciones de sensores (p. ej., temperatura, presión, flujo).
- Parámetros de recopilación de datos y tasas de muestreo.
- Capacidades de computación de borde para ejecución local de algoritmos de IA/ML.
Infraestructura de conectividad
La transmisión de datos se facilita a través de:
- Protocolos cableados (p. ej., Ethernet, RS-485).
- Tecnologías inalámbricas (p. ej., Wi-Fi, Bluetooth, LPWAN, 5G).
Factores críticos:
- Topología y arquitectura de red.
- Parámetros de calidad de servicio (QoS).
- Capacidades de transmisión de datos en tiempo real.
- Protocolos de seguridad (p. ej., TLS, DTLS).
Plataforma de procesamiento y análisis de datos
Infraestructura de software escalable para la gestión de datos y análisis:
- Plataformas de computación en la nube o de borde.
- Soluciones de almacenamiento de Big Data (por ejemplo, lagos de datos, bases de datos de series temporales).
- Motores de análisis para obtener información descriptiva, predictiva y prescriptiva.
- Canalizaciones de aprendizaje automático para el entrenamiento y la implementación de modelos.
Esta arquitectura garantiza un ecosistema de IoT sólido, escalable e inteligente capaz de brindar información procesable e impulsar eficiencias operativas.
Para garantizar la aceptación en toda la empresa, debe haber una comprensión del valor que proporciona la IoT industrial. Con demasiada frecuencia, las empresas se estancan en la solución de los problemas técnicos y se centran exclusivamente en la inversión en hardware (sensores, puertas de enlace, etc.), conectividad, almacenamiento en la nube, mano de obra administrativa, soporte técnico y más.
Conclusiones
La instrumentación inteligente, impulsada por el Internet Industrial de las Cosas (IIoT), ha transformado la manera en que las industrias gestionan sus operaciones. Gracias a sensores avanzados y análisis de datos en tiempo real, es posible lograr una optimización continua de los procesos. Además, el mantenimiento predictivo reduce significativamente los tiempos de inactividad al anticipar fallos y permitir una planificación más eficiente de las intervenciones.
La integración de tecnologías como sensores avanzados, análisis en la nube y computación de borde permite la creación de fábricas inteligentes. Estas fábricas no solo automatizan tareas repetitivas, sino que también utilizan sistemas autónomos para mejorar procesos de forma continua y adaptarse dinámicamente a las demandas cambiantes del mercado. Esto da lugar a un ecosistema industrial más ágil, resiliente y eficiente, alineado con los retos de la manufactura moderna.
La adopción de la instrumentación industrial inteligente está revolucionando el control y monitoreo de los procesos productivos, convirtiéndolos en disciplinas altamente sofisticadas y basadas en datos. Con la integración de tecnologías como la computación en la nube y análisis predictivo, las industrias logran niveles inéditos de inteligencia operativa, mejorando la toma de decisiones, incrementando la productividad y garantizando un control más preciso de la calidad en sus operaciones.
la instrumentación industrial es una herramienta vital para la transformación eficiente de datos físicos en información procesable, asegurando la estabilidad y competitividad de las operaciones industriales. En un entorno competitivo y orientado hacia la sostenibilidad, la instrumentación industrial no solo mejora el control, sino que también impulsa la innovación y la adaptación a tecnologías emergentes, consolidándose como un recurso esencial para el futuro de los procesos industriales.
Referencias
- https://netilion.endress.com/blog/6-examples-industrial-iot-monitoring-solutions/
- https://www.globalxetfs.com/connectivity-internet-of-things-digital-infrastructure/
- https://1nce.com/en-us/resources/news/blog/iot-hardware-and-ecosystem
- https://www.techtarget.com/iotagenda/tip/A-comprehensive-view-of-the-4-IoT-architecture-layers