Tabla de Contenidos
- Introducción
- ¿Qué son los espacios confinados?
- Tipos de espacios confinados
- Riesgos asociados en los espacios confinados
- Trabajos en espacios confinados: Retos y medidas de seguridad
- Normas y regulaciones para espacios confinados
- EPP para Espacios confinados: Selección y uso correcto
- Inspección y mantenimiento de espacios confinados
- Conclusiones
- Referencias
Introducción
Los espacios confinados representan una amenaza oculta en múltiples industrias debido a las condiciones especiales que dificultan su acceso y ventilación. Estos lugares, aunque esenciales en operaciones como mantenimiento y construcción, plantean riesgos significativos para la seguridad en espacios confinados si no se gestionan adecuadamente.
Garantizar dicha seguridad implica no solo comprender los peligros inherentes, sino también conocer los tipos de espacios confinados, adoptar equipos adecuados, procedimientos rigurosos y cumplir con normativas específicas diseñadas para la prevención de accidentes y salvaguardar vidas. Entre estas medidas, el uso de equipo de protección personal adecuado se vuelve indispensable para mitigar riesgos.
A lo largo de este artículo, se han abordado los principales desafíos de trabajar en espacios confinados, las normativas aplicables, la importancia del EPP, y las medidas de inspección y mantenimiento preventivo. Estos aspectos son fundamentales para garantizar un entorno de trabajo seguro y eficiente.
¿Qué son los espacios confinados?
Un espacio confinado se define como un área cerrada o parcialmente cerrada que no está diseñada para la ocupación humana continua, pero que puede requerir el ingreso para tareas específicas. Las características principales incluyen accesos limitados, ventilación restringida y posibles riesgos atmosféricos o físicos.
El proceso de identificar y clasificar espacios confinados es fundamental para garantizar la seguridad laboral. OSHA establece un enfoque claro de dos pasos para esta evaluación: identificar todos los espacios confinados y determinar cuáles requieren permisos específicos. Este video, cortesía de OSHA Training Services, explica en detalle los criterios utilizados por OSHA para definir un espacio confinado, proporcionando ejemplos prácticos que facilitan su comprensión y aplicación en el lugar de trabajo:
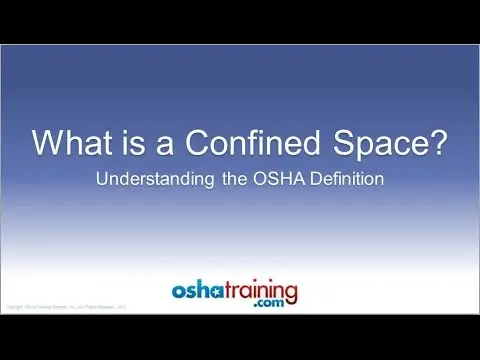
Identificación de espacios confinados.
Ejemplos comunes de estos espacios incluyen tanques de almacenamiento, silos, alcantarillas, túneles, reactores industriales y cámaras subterráneas. Estos ejemplos destacan cómo los tipos de espacios confinados se encuentran en industrias como la petroquímica, construcción, minería y agricultura.
Es crucial diferenciar entre un espacio confinado y un espacio restringido. Mientras que ambos tienen accesos limitados, el primero implica peligros adicionales que requieren medidas de control específicas. Por ejemplo, un sótano técnico puede ser un espacio restringido, pero si presenta riesgo de gases tóxicos, se clasifica como confinado.
En este contexto, comprender estos espacios y sus características es el primer paso para implementar estrategias efectivas de seguridad en espacios confinados y evitar accidents
Tipos de espacios confinados
Los tipos de espacios confinados se clasifican según los riesgos presentes:
- Riesgos atmosféricos
- Condiciones como insuficiencia de oxígeno, acumulación de gases tóxicos (ej., sulfuro de hidrógeno) o presencia de gases inflamables.
- Ejemplo: Tanques con residuos químicos donde la ventilación es mínima.
- Riesgos estructurales
- Peligros como derrumbes, atrapamientos o colapsos.
- Ejemplo: Túneles en construcción con soporte insuficiente.
- Riesgos de incendio o explosión
- Espacios donde materiales inflamables o atmósferas explosivas pueden causar accidentes graves.
- Ejemplo: Espacios donde se almacenan líquidos combustibles o polvos finos como harina o carbón.
Cada uno de estos tipos de espacios confinados requiere evaluaciones específicas para identificar riesgos y planificar intervenciones seguras. Identificarlos correctamente permite minimizar accidentes y maximizar la prevención de accidentes y maximizar la seguridad operativa.
Riesgos asociados en los espacios confinados
Los espacios confinados presentan una variedad de riesgos que deben abordarse cuidadosamente:
- Riesgos atmosféricos
- Falta de oxígeno: Puede causar asfixia en minutos.
- Presencia de gases tóxicos: Ej., monóxido de carbono o sulfuro de hidrógeno.
- Gases inflamables: Riesgo de explosiones si hay una fuente de ignición.
- Riesgos mecánicos
- Atrapamientos: Máquinas o componentes en movimiento pueden aprisionar al trabajador.
- Impacto de objetos: Caídas de herramientas o materiales en espacios reducidos.
- Caídas: Accesos complicados o superficies resbaladizas aumentan este peligro.
- Energía no controlada
- Contacto con líneas eléctricas o equipos energizados que no han sido desactivados adecuadamente.
- Riesgos psicológicos
- Claustrofobia y estrés por trabajar en un ambiente restringido.
- Fatiga mental, que puede llevar a errores humanos.
Mitigar estos riesgos es clave para garantizar la seguridad y la prevención de accidentes, utilizando procedimientos rigurosos, equipos adecuados y personal capacitado. En este contexto, el equipo de protección personal, como respiradores y detectores de gases, juega un papel crucial para proteger la vida de los trabajadores.
Caso de incidente en espacios confinados en una planta de tratamiento de aguas
En julio de 2019, en una planta de tratamiento de aguas residuales en Ohio, Estados Unidos, ocurrió un trágico accidente que dejó dos trabajadores fallecidos. El incidente se produjo cuando uno de los empleados ingresó a un tanque de almacenamiento para realizar tareas de mantenimiento sin verificar previamente la atmósfera del espacio confinado. El tanque contenía niveles peligrosos de sulfuro de hidrógeno (H₂S), un gas tóxico e incoloro que puede causar la pérdida de consciencia y la muerte en pocos minutos.
Tras no recibir respuesta del primer empleado, un compañero de trabajo ingresó al tanque para intentar rescatarlo, sin utilizar el equipo de protección personal necesario ni seguir los protocolos establecidos para espacios confinados. Ambos trabajadores sucumbieron a la intoxicación antes de que los equipos de emergencia pudieran intervenir.
Lecciones aprendidas
- Evaluación de riesgos: El tanque no había sido monitoreado previamente para detectar gases tóxicos ni niveles adecuados de oxígeno, violando normativas como la OSHA 1910.146.
- Uso de EPP: Ninguno de los trabajadores contaba con detectores de gases portátiles ni respiradores adecuados, elementos críticos del equipo de protección personal en espacios confinados.
- Capacitación insuficiente: La falta de entrenamiento adecuado sobre los riesgos de espacios confinados y los procedimientos de rescate contribuyó a la tragedia.
- Protocolos de entrada: No se implementaron permisos de entrada ni se estableció supervisión externa para monitorear las condiciones del espacio confinado.
Medidas Correctivas: Después del incidente, la planta implementó un programa riguroso de capacitación en seguridad, adquirió equipos avanzados de monitoreo de gases y reforzó la política de uso obligatorio de equipo de protección personal. Además, se establecieron simulacros periódicos para mejorar las respuestas de emergencia.
Impacto: Este caso destaca la importancia de seguir protocolos estrictos y utilizar el equipo adecuado para prevenir accidentes en espacios confinados. Refuerza el llamado a las empresas a invertir en seguridad y capacitación para proteger la vida de los trabajadores.
Trabajos en espacios confinados: Retos y medidas de seguridad
Los trabajos en los diferentes tipos de espacios confinados o áreas cerradas presentan múltiples desafíos para los trabajadores debido a la naturaleza de estos entornos. La limitación de espacio y movilidad dificulta el movimiento y la ejecución de tareas, mientras que la comunicación restringida puede complicar la coordinación de equipos y la respuesta ante emergencias. Estos factores aumentan el riesgo de accidentes y la exposición a condiciones peligrosas.
Para garantizar la seguridad en espacios confinados, es fundamental implementar procedimientos esenciales como los permisos de entrada y el control de acceso y la selección del equipo de protección personal adecuado. La ventilación adecuada y el monitoreo constante de la atmósfera son medidas clave para prevenir la acumulación de gases tóxicos o inflamables y garantizar niveles seguros de oxígeno. Además, es indispensable contar con supervisión continua de personal capacitado para detectar cualquier incidente y actuar rápidamente.
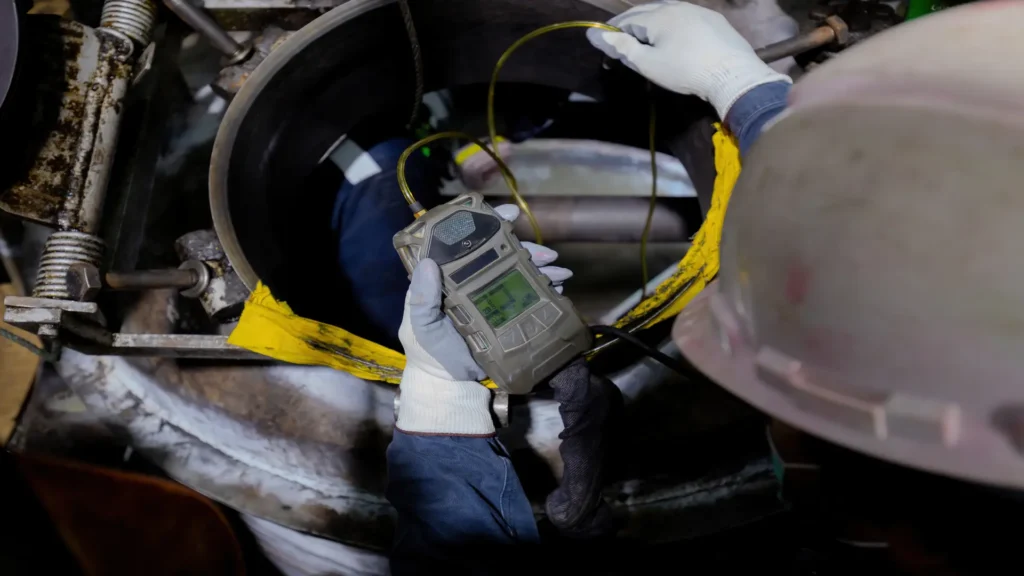
La tecnología también desempeña un papel crucial en la seguridad de espacios confinados para la mitigación de riesgos. Herramientas como sensores de gases portátiles y sistemas de monitoreo remoto permiten detectar condiciones peligrosas en tiempo real. Además, los drones y robots están ganando popularidad, ya que pueden realizar inspecciones iniciales sin poner en riesgo a los trabajadores.
Los trabajos en áreas cerradas requieren un enfoque integral de seguridad que combine medidas técnicas, administrativas y tecnológicas para proteger la vida de los operarios.
Normas y regulaciones para espacios confinados
La Administración de Seguridad y Salud Ocupacional (OSHA, por sus siglas en inglés) es una agencia del Departamento de Trabajo de los Estados Unidos fundada en 1970 bajo la Ley de Seguridad y Salud Ocupacional. Su objetivo principal es proteger la salud y seguridad de los trabajadores, reduciendo riesgos laborales mediante la creación y aplicación de normativas específicas. OSHA también ofrece capacitación, educación y asistencia técnica para fomentar entornos de trabajo seguros.
El cumplimiento de una norma de espacios confinados es esencial para reducir riesgos y garantizar la seguridad de los trabajadores. La OSHA 1910.146 establece requisitos específicos para la entrada a lugares confinados en industrias de alto riesgo, mientras que la ISO 45001 proporciona un marco global para la gestión de la seguridad y la salud ocupacional.
Entre los requisitos clave, destacan la identificación de los peligros asociados al espacio confinado, la implementación de procedimientos de entrada seguros y la capacitación del personal involucrado. Además, en algunas industrias como el petróleo y gas, se exige el uso de sistemas avanzados de monitoreo atmosférico y rescate.
La capacitación y el entrenamiento continuo son esenciales para garantizar que los trabajadores comprendan los riesgos y sepan responder adecuadamente. Un ejemplo práctico de implementación es la realización de simulacros periódicos para probar los procedimientos de rescate y evaluar la eficacia de las medidas de seguridad en un entorno controlado.
Cumplir con una norma de espacios confinados no solo protege a los empleados, sino que también asegura el cumplimiento legal, minimizando posibles sanciones y mejorando la productividad operativa.
EPP para Espacios confinados: Selección y uso correcto
El Equipo de Protección Personal (EPP) para éstos espacios es un elemento esencial para salvaguardar la seguridad de los trabajadores. Entre los elementos básicos se incluyen respiradores para proteger contra atmósferas contaminadas, detectores de gases portátiles para monitorear las condiciones del entorno, así como arneses y líneas de vida para prevenir caídas. Otros equipos importantes son los cascos de seguridad y guantes resistentes, diseñados para condiciones específicas.
La selección adecuada del EPP debe basarse en una evaluación del entorno, considerando factores como la presencia de gases tóxicos, riesgo de caída o confinamiento extremo. Además, es crucial cumplir con las normativas aplicables, como la OSHA 1910.146, que especifica los requisitos mínimos para los equipos utilizados en estos trabajos.
El mantenimiento y almacenamiento adecuado del EPP para áreas cerradas son igualmente importantes. Los respiradores deben limpiarse regularmente, y los detectores de gases deben ser calibrados periódicamente para garantizar su funcionamiento. Asimismo, los arneses y líneas de vida deben inspeccionarse antes de cada uso para detectar posibles daños.
Seleccionar y utilizar correctamente el EPP para espacios confinados es una medida fundamental para garantizar la seguridad y eficiencia en estas actividades de alto riesgo.
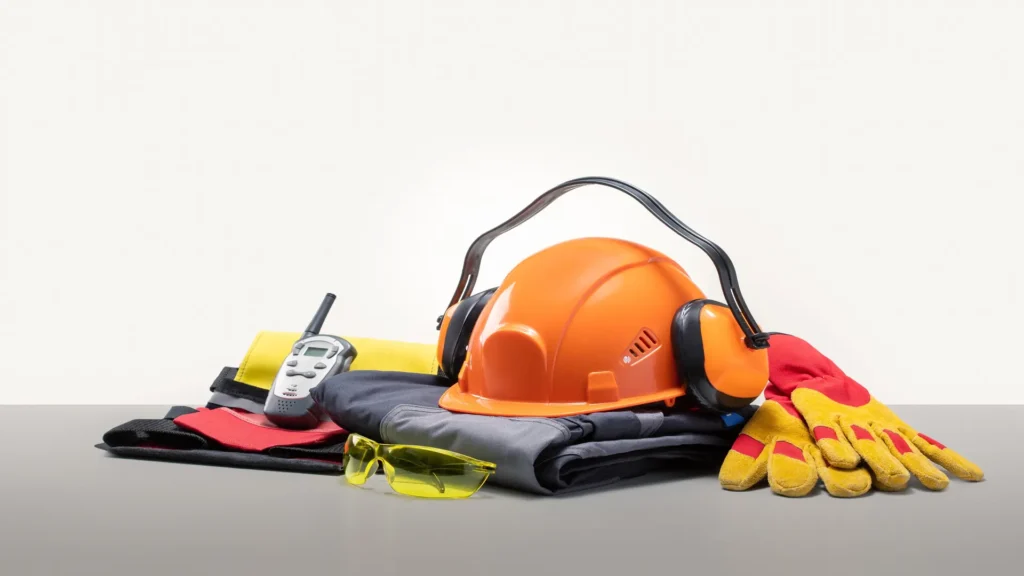
Inspección y mantenimiento de espacios confinados
La inspección y mantenimiento de espacios confinados son esenciales para garantizar la seguridad en espacios confinados y prevenir accidentes. Las inspecciones periódicas permiten identificar riesgos como la acumulación de gases peligrosos, estructuras deterioradas o fallos en los equipos, mitigando posibles incidentes antes de que ocurran.
Entre los métodos comunes de monitoreo atmosférico destacan los detectores portátiles de gases, que miden niveles de oxígeno, gases tóxicos e inflamables en tiempo real. Estos dispositivos son complementados por el análisis visual, donde se evalúan condiciones físicas del entorno, como integridad estructural, iluminación y accesibilidad.
El mantenimiento preventivo juega un papel crucial en la seguridad. Este incluye revisar y calibrar regularmente los equipos de monitoreo, realizar inspecciones detalladas de las estructuras para detectar corrosión o desgaste, y garantizar el correcto funcionamiento de sistemas de ventilación y rescate.
Implementar un programa robusto de inspección y mantenimiento reduce los riesgos asociados a las áreas cerradas, protege la vida de los trabajadores y asegura la continuidad operativa en cualquier industria. La prioridad siempre debe ser la prevención de accidentes, asegurando entornos más seguros y productivos.
Conclusiones
Es imperativo que las empresas adopten buenas prácticas de seguridad, capaciten constantemente a su personal y actualicen los procedimientos según las normativas vigentes. La inversión en tecnología, como detectores de gases avanzados o drones para inspección remota y medición de espesores, puede ser un cambio significativo para mitigar riesgos.
Mirando hacia el futuro, las innovaciones tecnológicas y los avances en materiales prometen nuevas soluciones para mejorar la seguridad en estos entornos. Con la implementación adecuada de estas medidas, es posible transformar las áreas cerradas en entornos más seguros para los trabajadores, reduciendo accidentes y mejorando la productividad.
La seguridad en espacios confinados; es un pilar fundamental para proteger vidas y garantizar la continuidad operativa. Cumplir con las normativas específicas minimiza riesgos, y se fomenta una cultura de prevención en las organizaciones. Al integrar prácticas seguras, equipos adecuados y una capacitación constante, es posible reducir significativamente los incidentes, fortaleciendo el bienestar de los trabajadores y el éxito de las operaciones industriales.
Profesionales y organizaciones, manténganse informados y comprometidos con el aprendizaje continuo para seguir avanzando.
Referencias
Fuente propia