Tabla de Contenidos
- Introducción
- ¿Qué es la soldadura orbital y cómo funciona?
- Características del proceso
- Principios de funcionamiento
- Inicio del proceso de soldadura: Activar el sistema para iniciar la soldadura orbital automatizada
- Aplicaciones comunes de la soldadura orbital en diferentes industrias
- Avances recientes en tecnología de soldadura orbital
- Mantenimiento preventivo de las máquinas de soldadura orbital
- Normativas y estándares que regulan la soldadura orbital
- Ventajas
- Limitaciones
- Conclusión
- Referencias
Introducción
La soldadura orbital es una técnica automatizada de alta precisión que se utiliza para ejecutar servicios críticos en diversos sectores industriales gracias a su capacidad para producir uniones consistentes y de calidad superior. Este artículo aborda este proceso de soldadura, sus aplicaciones, avances tecnológicos recientes y las normativas que aplican para su buen desempeño, destacando su relevancia en entornos críticos como las industrias aeroespacial, farmacéutica, de alimentación y energética.
¿Qué es la soldadura orbital y cómo funciona?
Es un proceso de soldadura automatizada automatizada que utiliza los mismos principios de la soldadura TIG (Tungsten Inert Gas) y está diseñada específicamente para realizar uniones de alta precisión en tubos, tuberías y componentes de forma circular. Este método utiliza un equipo especializado que mueve el electrodo (tungsteno) junto con el alambre consumible y el gas de protección, alrededor del objeto a soldar en un trayecto circular, logrando una unión uniforme y consistente
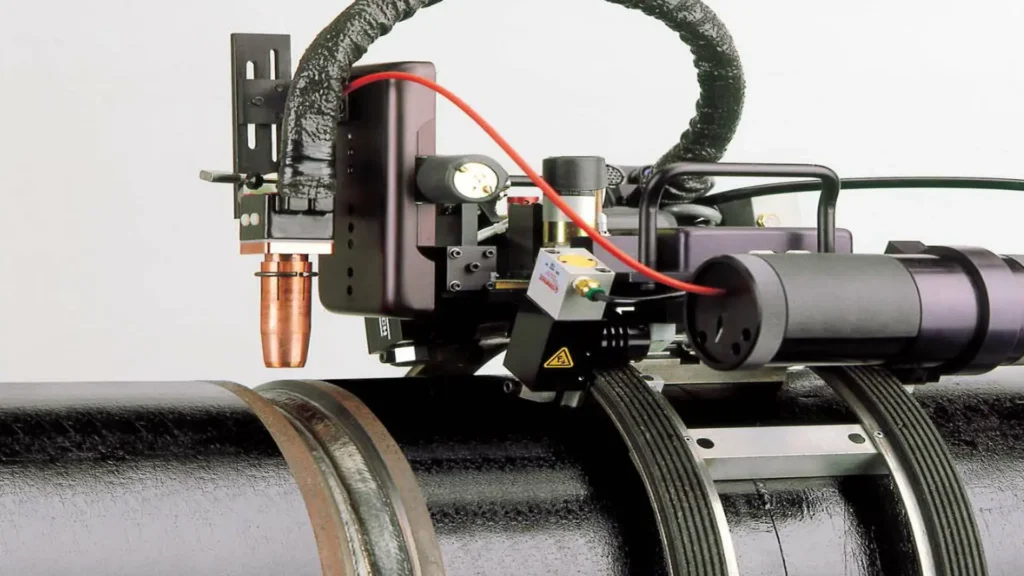
Características del proceso
- Automatización total: Al ser completamente automatizado, se reduce al mínimo la intervención manual, lo que disminuye significativamente los errores humanos.
- Control preciso: Los parámetros clave de soldadura, como velocidad, corriente y tensión, son gestionados automáticamente, asegurando una uniformidad constante en los resultados.
- Alta repetibilidad: Perfecto para proyectos que demandan un gran volumen de soldaduras consistentes y de alta calidad.
- Aplicación libre de defectos: Su precisión garantiza la minimización de defectos comunes como porosidad, grietas o falta de penetración.
Principios de funcionamiento
El proceso de soldadura orbital automatiza el movimiento del electrodo para realizar soldaduras de alta calidad y precisión. Se utiliza principalmente en aplicaciones donde los estándares de calidad son críticos, como la industria farmacéutica, alimentaria, aeroespacial, y energética. A continuación, se detalla el proceso.
- Limpieza: Limpiar las superficies a soldar para eliminar óxido, grasa, pintura o cualquier otro contaminante.
- Corte y preparación del tubo: Asegurar de que los extremos del tubo tengan cortes precisos y biselados (si aplica) para un ajuste perfecto.
- Alineación: Alinear los tubos de manera que no haya desniveles o espacios entre las piezas.
- Cabezal orbital: Elegir el cabezal orbital compatible con el diámetro del tubo.
- Gas de protección: Seleccionar un gas de protección adecuado (como argón de alta pureza) para evitar contaminación del baño de soldadura.
Configuración y control de los parámetros de soldadura
La soldadura orbital requiere una configuración precisa de parámetros para garantizar una soldadura uniforme y de alta calidad. A continuación, se describen los principales parámetros que deben configurarse:
- Corriente de soldadura (amperaje): Se ajusta según el grosor del material base y el diámetro del electrodo. Un amperaje alto produce mayor penetración, pero puede causar defectos como quemaduras en materiales delgados.
- Tensión de arco (voltaje): Influye en la longitud del arco eléctrico. Un voltaje adecuado asegura un baño de fusión estable.
- Tipo de corriente: La corriente continua (DC) es común en materiales como acero inoxidable y aleaciones de níquel y la corriente alterna (AC) es usada para soldar como el aluminio.
- Frecuencia del pulso: Controla el ciclo de calor, reduciendo deformaciones y mejorando la penetración en materiales delicados.
- Velocidad de rotación del cabezal: La velocidad orbital determina el tiempo que el electrodo permanece sobre cada punto de la unión. Debe ajustarse según el diámetro de la tubería y el espesor del material.
- Gas protector: El gas, normalmente de argón o mezcla de argón/helio, protege el arco de contaminantes durante la soldadura.
- Flujo de gas: Generalmente medido en litros por minuto (L/min). Los flujos bajos pueden causar contaminación, mientras que los flujos altos generan turbulencias.
- Alimentación del material de aporte: Se configura la velocidad de alimentación del alambre, sincronizada con la velocidad de rotación del cabezal y la corriente.
- Programación del ciclo de soldadura: En este ciclo se programa el número de pasadas determinadas por el espesor de las juntas.
- Montaje del cabezal orbital: Instala el cabezal orbital alrededor del tubo asegurando que quede firme y alineado. Conectar el cabezal al sistema de control para automatizar el movimiento de rotación.
- Pruebas preliminares: Realizar las pruebas iniciales siguientes:
- Simulación sin arco: Ejecutar una prueba sin producir arco para verificar la alineación y el funcionamiento del cabezal.
- Ajuste fino: Corregir cualquier desalineación y ajustar los parámetros de soldadura si es necesario.
Inicio del proceso de soldadura: Activar el sistema para iniciar la soldadura orbital automatizada
Control y monitoreo: Se deben llevar los controles a continuación
- Supervisar en tiempo real la soldadura a través del sistema de control, verificando que no haya interrupciones en la alimentación de corriente o en el movimiento del cabezal.
- Asegurando que el gas de protección fluya antes, durante y después de la soldadura para evitar oxidación.
- Finalización y enfriamiento: Una vez completada la soldadura, permite que el material se enfríe de forma controlada.
- Inspección de calidad: Realizar inspección visual a la soldadura acabada para identificar defectos superficiales y posteriormente aplicar metodologías o técnicas de ensayo no destructivos (END) como radiografías, ultrasonidos o inspección con líquidos penetrantes para garantizar la integridad de la soldadura.
- Limpieza final: Eliminar cualquier residuo que pueda haber quedado en la superficie de la soldadura.
Aplicaciones comunes de la soldadura orbital en diferentes industrias
- Industria aeroespacial: En el sector aeroespacial, donde la precisión es crítica, la soldadura orbital se utiliza para unir materiales como titanio y aleaciones ligeras. Estos materiales son comunes en estructuras aeronáuticas y sistemas hidráulicos debido a su resistencia y bajo peso.
- Industria farmacéutica, alimentación y bebidas: El sector farmacéutico exige uniones sanitarias y libres de contaminación en sus sistemas de tuberías. La tecnología de soldadura orbital es ideal para lograr este objetivo, garantizando superficies internas lisas y evitando acumulaciones de bacterias que podrían comprometer la esterilidad, lo cual cumple con los criterios de aceptación de ASME BPE.
- Sector de energía y petróleo: En el ámbito de la energía, esta técnica se emplea en sistemas de alta presión y conducción de fluidos. La calidad de las uniones realizadas con soldadoras orbitales da una garantía extra para soportar condiciones extremas, incluyendo altas temperaturas y presión.
- Industria metalmecánica: En esta área de la construcción es muy utilizada en las soldaduras de tuberías y sus accesorios y muy especialmente para soldadura de placas con tubos para la fabricación de intercambiadores de calor y calderas.
En el siguiente video se aprecia cómo realizar una soldadura orbital para uniones de tubo a tubo. Fuente: Orbitalum Tools GmbH2.

Proceso de soldadura orbital de placas de tubos.
Avances recientes en tecnología de soldadura orbital
- Automatización y control de precisión: Los últimos avances han llevado a un nivel superior de automatización en la tecnología de soldadura orbital, con sistemas capaces de ajustar parámetros en tiempo real. Esto garantiza resultados consistentes incluso en aplicaciones complejas.
- Integración de sensores y monitoreo en tiempo real: La incorporación de sensores avanzados permite detectar defectos durante el proceso y realizar ajustes automáticamente, reduciendo el riesgo de fallas y mejorando la eficiencia operativa.
- Innovaciones en equipos multiproceso: Los equipos más recientes ofrecen la posibilidad de alternar entre procesos como TIG, MIG y plasma en una misma máquina, optimizando tanto el tiempo como los costos del proyecto.
Mantenimiento preventivo de las máquinas de soldadura orbital
El mantenimiento preventivo es esencial para garantizar su desempeño óptimo, prolongar su vida útil y prevenir fallos durante operaciones críticas. Este tipo de mantenimiento incluye inspecciones, ajustes y limpieza periódica de los componentes clave. A continuación, se describen las principales acciones a realizar:
- Cabezal de soldadura: Limpiar regularmente las guías de los electrodos y las superficies de contacto para evitar la acumulación de residuos metálicos o salpicaduras.
- Cables y conectores: Verificar y limpiar los cables eléctricos y de señal para garantizar un flujo de corriente estable y evitar interrupciones.
- Sistemas de refrigeración: Limpieza de los conductos de agua y los enfriadores para prevenir obstrucciones que puedan causar sobrecalentamiento.
- Fuente de energía: Revisar el estado de los circuitos internos, paneles de control y sistemas de alimentación para detectar posibles conexiones, flojas o componentes dañados.
- Sensores y sistemas de control: Compruebe que los sensores de temperatura, corriente y velocidad funcionen correctamente, ya que son fundamentales para la precisión del proceso.
- Pantallas y controles: Se debe verificar el funcionamiento de las interfaces de usuario y ajustar las configuraciones necesarias.
- Guías y rodamientos: Lubricar y comprobar el estado de las piezas móviles para evitar desgastes que puedan afectar la precisión del cabezal orbital.
- Brazos y soportes: Inspeccionar las fijaciones y mecanismos de ajuste para garantizar una sujeción segura durante el proceso.
- Electrodos y antorchas: Evaluar el estado de los consumibles y cambiarlos si están desgastados o dañados.
- Revisión del sistema de enfriamiento: Comprobar los niveles de líquidos refrigerantes y la limpieza de los conductos. Identifique posibles fugas o bloqueos en el sistema.
- Calibración periódica: Realizar calibraciones regulares para asegurar que los parámetros de soldadura, como corriente, voltaje y velocidad de rotación, cumplen con las especificaciones del fabricante y las necesidades del proyecto.
- Frecuencia recomendada: La frecuencia del mantenimiento preventivo puede variar según la intensidad de uso y el entorno operativo. Sin embargo, se recomienda realizarlo al menos cada 500 horas de operación.
Normativas y estándares que regulan la soldadura orbital
El proceso de soldadura orbital se soporta en un conjunto de normas internacionales que garantizan calidad, precisión y seguridad en su aplicación. Entre las más destacadas se encuentra la ISO 14732, que establece los requisitos para la calificación de operadores y ajustadores de equipos de soldadura automatizada, asegurando que el personal encargado posea las habilidades necesarias para manejar este tipo de tecnología avanzada, igualmente por tratarse de un proceso de soldadura, se aplican todas las normas que regulen la calidad, procedimientos, todas las normas y procedimientos de soldadura que garanticen la calidad, seguridad y eficiencia de las uniones soldadas como la ASME Section IX y API 1104.
Por otro lado, las normas ISO 9606 e ISO 15614 complementan este proceso al establecer los lineamientos para la cualificación de soldadores y los procedimientos específicos para materiales metálicos. Estas normas garantizan que las soldaduras realizadas cumplan con los estándares de calidad exigidos en industrias altamente reguladas como la farmacéutica, aeroespacial y alimentaria, donde la soldadura orbital es ampliamente utilizada.
Ventajas
- Consistencia: Las soldaduras son repetibles y uniformes, reduciendo defectos.
- Alta precisión: Ideal para diámetros pequeños y juntas críticas.
- Mayor velocidad y eficiencia del proceso.
- La automatización minimiza la intervención humana, mejorando la seguridad.
- Reducción de desperdicios por el uso eficiente del material y menor necesidad de rectificaciones.
- Versatilidad para aplicaciones únicas, como una pieza que no se puede girar, que tiene poca visibilidad o está en un área de difícil acceso.
Limitaciones
- Costo inicial elevado: Los equipos de soldadura orbital son costosos.
- Preparación estricta: Requiere alineación y limpieza meticulosa.
- No adecuado para todas las geometrías: Diseñado principalmente para objetos cilíndricos.
Conclusión
La soldadura orbital representa una solución innovadora y eficiente para diversas aplicaciones industriales que requieren un alto nivel de precisión y consistencia. Los avances tecnológicos en automatización y monitoreo han ampliado aún más su alcance, mientras que las normativas internacionales como la ISO 14732 garantizan la calidad y seguridad del proceso. Esta técnica, impulsada por su capacidad para realizar uniones fiables en entornos críticos, continúa siendo un pilar fundamental en industrias de alta exigencia como la aeroespacial, farmacéutica y energética.
Referencias
- https://www.demaquinasyherramientas.com/soldadura/soldadura-orbital-que-es
- https://www.youtube.com/watch?v=l4zCL8uU51s