Tabla de Contenidos
- Introducción
- Diagnóstico rápido para sistemas de energía industriales
- Soluciones de energía de respaldo de última generación
- Equipos de conmutación automatizados de vanguardia para el mantenimiento eléctrico
- Tipos de rutina de mantenimiento eléctrico preventivo
- Resiliencia a través del diseño
- Medidas de seguridad ampliadas
- Mitigando el riesgo de accidentes aplicando el mantenimiento preventivo eléctrico (EPM)
- Conclusión
- Referencias
Introducción
Los sistemas eléctricos son responsables del 24% de los incendios en entornos industriales, según la NFPA, subrayando la importancia de los programas de mantenimiento eléctrico. Estos programas integran tecnologías avanzadas como sistemas SCADA y análisis predictivo impulsado por IA para detectar y manejar fallas eléctricas de manera eficiente.
Además, la implementación de soluciones de energía de respaldo y equipos de conmutación automatizados minimiza el tiempo de inactividad durante interrupciones, asegurando operaciones continuas y seguras en industrias donde cada instante cuenta. Este artículo explorará cómo estas tecnologías y estrategias están redefinen la seguridad y eficiencia industrial.
Diagnóstico rápido para sistemas de energía industriales
Los sistemas industriales actuales requieren mecanismos de respuesta rápidos y precisos para detectar y reducir fallas eléctricas. Los sistemas SCADA, junto con el análisis predictivo impulsado por IA, brindan capacidades avanzadas de monitoreo y predicción. La integración de sensores inteligentes dentro de la infraestructura de energía permite la detección de fallas en tiempo real, lo que señala instantáneamente anomalías como caídas de voltaje, desequilibrios de frecuencia o desgaste del equipo.
Además, los diagnósticos de IA pueden predecir el estado de los componentes clave como transformadores y tableros de distribución, lo que permite un mantenimiento preventivo antes de que los problemas se agraven. Esta fusión de monitoreo, predicción y retroalimentación inmediata es la columna vertebral de una estrategia de respuesta a emergencias ágil.
Soluciones de energía de respaldo de última generación
En las industrias donde el tiempo de inactividad genera pérdidas significativas, las soluciones de energía de respaldo son fundamentales. Los sistemas híbridos que combinan generadores tradicionales con fuentes de energía renovable (solar, eólica) proporcionan una fuente de energía sostenible pero confiable.
Las tecnologías de celdas de combustible, como las celdas de óxido sólido, son cada vez más viables para duraciones de respaldo prolongadas, lo que ofrece un tiempo operativo más extenso y más limpio durante las interrupciones del suministro eléctrico.
Los sistemas de almacenamiento de energía, incluidas las baterías de flujo avanzadas o el almacenamiento de energía de aire comprimido (CAES), brindan otra capa de redundancia, manteniendo la energía para operaciones críticas y evitando las emisiones y los costos de combustible asociados con los generadores convencionales.
Equipos de conmutación automatizados de vanguardia para el mantenimiento eléctrico
Los interruptores de transferencia estática (STS) de alta velocidad permiten transiciones inmediatas entre fuentes de energía, lo que garantiza un tiempo de inactividad mínimo durante las interrupciones del suministro eléctrico.
Al combinar estas tecnologías, las instalaciones pueden garantizar operaciones ininterrumpidas y optimizar las respuestas de emergencia, aprovechando la automatización para superar las respuestas manuales tradicionales.
Tipos de rutina de mantenimiento eléctrico preventivo
El mantenimiento eléctrico preventivo abarca diversas actividades que garantizan la operación continua y segura de los sistemas. Estas rutinas se dividen en tres categorías principales: inspección, prueba y servicio, y deben implementarse de manera sistemática para abordar diferentes aspectos operativos de cada equipo.
A continuación, se detallan los elementos clave y otros tópicos críticos para un programa eficiente:
1. Inventario y clasificación de riesgo: Es esencial llevar un inventario detallado de todos los equipos eléctricos dentro de las instalaciones. Este inventario no solo debe catalogar los activos, sino también clasificarlos en función del nivel de daño potencial si fallan.
El criterio de clasificación puede basarse en la criticidad operativa, los costos asociados al tiempo de inactividad y los riesgos de seguridad. Para facilitar las inspecciones y pruebas, se debe generar una lista de verificación detallada que aborde cada equipo, priorizando aquellos cuya falla tendría mayores consecuencias.
2. Inspección periódica: Cada equipo en el inventario debe tener un ciclo de inspección predeterminado según su criticidad, año de fabricación y las condiciones operativas a las que está sometido. Los equipos que trabajan bajo cargas variables, entornos severos o altas temperaturas deben ser inspeccionados con mayor frecuencia. Las inspecciones deben incluir una revisión visual completa, buscando señales de desgaste, sobrecalentamiento, corrosión, y otros indicadores de deterioro.
3. Pruebas diagnósticas y funcionales: Además de las observaciones visuales y auditivas, se deben realizar pruebas exhaustivas. Estas incluyen mediciones de resistencia de aislamiento, pruebas de corriente de fuga, análisis de factor de potencia, y termografía infrarroja para detectar puntos calientes. También es recomendable realizar análisis de calidad de energía (armónicos, desequilibrios de fase) para detectar problemas que puedan reducir la vida útil de los equipos y elevar los costos de operación. Las pruebas funcionales deben verificar la capacidad operativa bajo cargas simuladas.
4. Monitoreo en línea y mantenimiento eléctrico predictivo: Un enfoque moderno incluye el uso de tecnologías de monitoreo en línea para la supervisión continua de parámetros críticos como temperatura, vibración y tensión de operación. Estos sistemas permiten un enfoque predictivo, identificando fallas inminentes antes de que se produzcan. Los sistemas de monitoreo basados en IoT pueden alertar automáticamente a los equipos de mantenimiento eléctrico sobre desviaciones que requieran intervención inmediata, reduciendo la necesidad de inspecciones manuales frecuentes.
5. Un minucioso registro de datos: Mantener registros meticulosos de cada acción es fundamental para la trazabilidad y la mejora continua del mantenimiento eléctrico. Se deben registrar no solo las fallas y correcciones, sino también mediciones críticas de las pruebas realizadas, condiciones operativas, e incluso información sobre los mantenimientos preventivos realizados.
Un sistema de gestión de mantenimiento computarizado (CMMS) puede facilitar este proceso, permitiendo un seguimiento en tiempo real y la generación de reportes para análisis de tendencias y optimización de ciclos de mantenimiento eléctrico.
6. Reparación, ajuste y reemplazo programado: El mantenimiento eléctrico preventivo no se limita a inspeccionar y diagnosticar; también implica llevar a cabo reparaciones correctivas y ajustes a medida que se identifican los problemas. Los componentes defectuosos o de bajo rendimiento deben ser reparados o sustituidos de inmediato para evitar fallos mayores.
Adicionalmente, debe existir un plan de reemplazo para piezas con ciclos de vida determinados, basado en los datos recopilados y en las recomendaciones del fabricante. Este paso incluye la planificación de la disponibilidad de repuestos críticos.
7. Cumplimiento normativo y auditoría: Las instalaciones deben cumplir con las normativas y estándares aplicables a la seguridad eléctrica, tales como el Código Eléctrico Nacional (NEC) o las normativas OSHA. Además, es recomendable realizar auditorías periódicas para asegurar que las rutinas de mantenimiento eléctrico cumplen con las mejores prácticas industriales y con los requisitos legales. La falta de cumplimiento puede derivar en sanciones o en riesgos de seguridad graves.
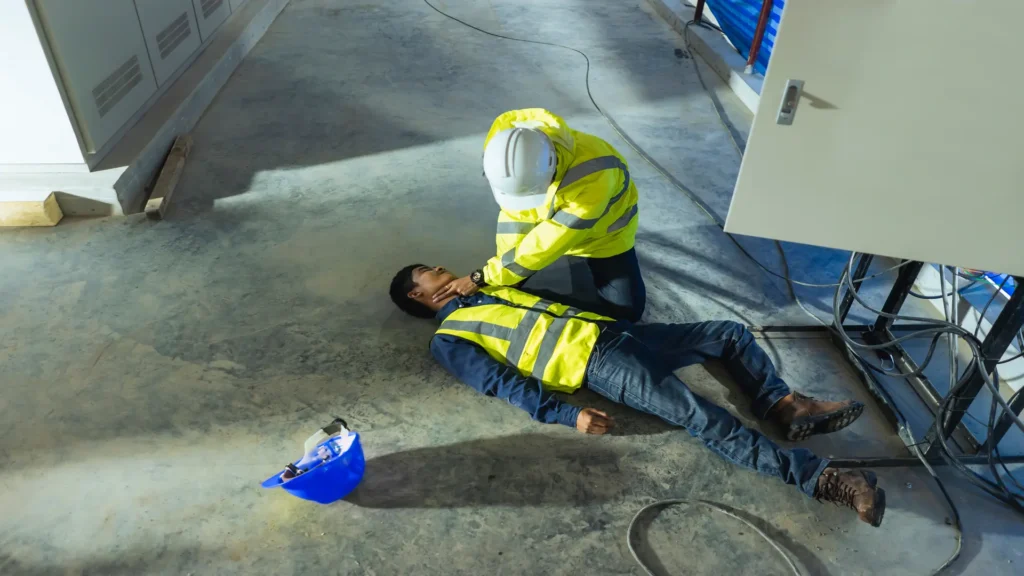
Resiliencia a través del diseño
Para preparar las instalaciones industriales para el futuro se necesitan redes autorreparables, que puedan aislar y reparar fallas de manera autónoma. Los sistemas de distribución de energía modulares también ofrecen flexibilidad, lo que permite aislar secciones de la red durante fallas mientras se mantienen las operaciones en áreas no afectadas.
Los materiales avanzados, como los superconductores de alta temperatura, pueden mejorar aún más la resiliencia de los equipos eléctricos, mejorando la durabilidad y el funcionamiento.
El término resiliencia no solo se aplica al comportamiento humano; en el ámbito de la ingeniería y los sistemas industriales, también se utiliza para describir la capacidad de un sistema, equipo o activo de adaptarse y recuperarse frente a perturbaciones o condiciones adversas, como fallos mecánicos, fluctuaciones en la demanda o condiciones ambientales extremas.
En el diseño de activos industriales, la resiliencia se refiere a crear equipos y sistemas que sean robustos y adaptables, capaces de resistir fallos o recuperarse rápidamente para minimizar el tiempo de inactividad.
Esto implica integrar características como:
- Redundancia: Tener componentes duplicados o sistemas paralelos que tomen el relevo en caso de fallo.
- Modularidad: Facilitar el mantenimiento eléctrico o reemplazo de partes del equipo sin interrumpir toda la operación.
- Tolerancia a fallos: Diseñar sistemas que puedan operar de manera segura, aunque algunos componentes fallen.
- Monitoreo y diagnóstico: Implementar sensores y algoritmos de mantenimiento predictivo para anticipar problemas antes de que afecten el funcionamiento.
Así, la resiliencia en el diseño industrial asegura que los activos puedan enfrentar desafíos imprevistos sin comprometer la operación general, mejorando tanto la fiabilidad como la eficiencia del sistema.
Medidas de seguridad ampliadas
La identificación rápida de peligros permite la implementación inmediata de protocolos de seguridad, lo que reduce el riesgo para el personal y los activos. Los dispositivos portátiles pueden monitorear la condición física de los equipos de respuesta a emergencias. En este contexto, la «condición física» se refiere al estado estructural y operativo del equipo, es decir, a su integridad mecánica y eléctrica, lo que garantiza su seguridad durante las operaciones.
Despliegue eficiente de recursos: Estos diagnósticos ayudan a determinar la ubicación exacta y la naturaleza de una emergencia, lo que permite un despliegue más específico y eficiente de los activos y equipos de respuesta. Los sistemas de información geográfica (SIG) integrados con los datos de diagnóstico pueden proporcionar un contexto espacial para una mejor asignación de recursos.
Comunicación y coordinación sin interrupciones: Los diagnósticos rápidos y precisos facilitan una mejor comunicación entre los diferentes equipos y las partes interesadas involucradas en la respuesta a la emergencia. Los sistemas de comunicación integrados pueden difundir rápidamente la información de diagnóstico a todas las partes relevantes.
Monitoreo y adaptación continuos: Los datos de diagnóstico continuos permiten el ajuste en tiempo real de las estrategias de respuesta a medida que evoluciona la situación. Este enfoque adaptativo garantiza que la respuesta siga siendo efectiva durante toda la duración de la emergencia.
Mitigando el riesgo de accidentes aplicando el mantenimiento preventivo eléctrico (EPM)
El mantenimiento eléctrico preventivo (EPM) es una estrategia esencial para garantizar la confiabilidad y el rendimiento continuo de los sistemas eléctricos en instalaciones industriales. A través de inspecciones y evaluaciones regulares, este enfoque permite detectar y corregir problemas antes de que se conviertan en fallas críticas.
Al identificar fallos potenciales de forma anticipada, se asegura un tiempo de funcionamiento constante, evitando interrupciones no planificadas que puedan afectar tanto a la operación como a la productividad de una planta.
Otro aspecto crucial del EPM es su impacto directo en la seguridad. Los programas de mantenimiento incluyen pruebas detalladas que permiten identificar riesgos eléctricos como posibles arcos eléctricos o fallos de aislamiento, mitigando así el riesgo de accidentes que pueden poner en peligro tanto al personal como a la infraestructura de la instalación.
El mantenimiento preventivo también prolonga la vida útil de los equipos eléctricos, al asegurarse de que operen dentro de sus especificaciones de diseño. Los componentes eléctricos que reciben un mantenimiento adecuado sufren menos desgaste, lo que retrasa la necesidad de reemplazos y permite un mejor aprovechamiento de las inversiones en equipos.
Conclusión
Desde un punto de vista normativo, el EPM es una herramienta que asegura el cumplimiento con los códigos y estándares eléctricos aplicables en la industria. Muchas regulaciones exigen inspecciones periódicas para garantizar que los sistemas operen de manera segura y eficiente, y no cumplir con estos requisitos puede resultar en sanciones o penalizaciones. Un programa de mantenimiento preventivo garantiza que las instalaciones se mantengan dentro de los parámetros regulatorios, evitando así consecuencias legales o financieras.
Además, este enfoque permite mejorar la eficiencia energética de los sistemas eléctricos. Problemas como un bajo factor de potencia o desequilibrios en las cargas pueden ser identificados y corregidos, reduciendo el desperdicio de energía y optimizando el consumo. Esto no solo implica una reducción en los costos de los servicios públicos, sino también un menor impacto ambiental, lo que es cada vez más relevante en sectores industriales donde la sostenibilidad es una prioridad.
Referencias
- https://www.hanover.com/businesses/business-customer-resources/hanover-risk-solutions/electrical-preventive-maintenance-epm
- https://www.kazarselectric.com/how-a-transfer-switch-protects-your-home-during-power-outages/
- https://www.emersonautomationexperts.com/2019/control-safety-systems/controlling-surge-centrifugal-compressors/
- https://www.lembergelectric.com/blog/3-ways-electrical-preventative-maintenance-can-improve-your-operatives/