Tabla de Contenidos
Introducción
El mantenimiento centrado en la confiabilidad (RCM) es un proceso utilizado para determinar las políticas que se deben tomar para garantizar que un activo continúe desempeñando su función en el contexto operativo actual del activo y de la forma más costo-efectiva posible. Esto lo consigue mediante la identificación de la función del activo, su falla funcional y los modos de falla asociados, determinando políticas efectivas de mantenimiento preventivo que pueden implementarse de manera rentable y eficiente para reducir la probabilidad fallas.
Complementariamente, RCM encontró grandes limitaciones en la forma como interpretábamos la naturaleza de cómo se producían las fallas. En este artículo describiremos cómo ocurrió la transición entre las formas como pensábamos que ocurrían las fallas hasta la década de los 60 y las formas como RCM las desarrolló para mostrarnos los nuevos Patrones de Falla de RCM, la nueva lógica de ver al mantenimiento.
Primera generación de patrones de falla
Con la revolución industrial aparecieron las máquinas y con sus fallas aparecieron los primeros esfuerzos de “Mantenimiento”. Inicialmente todo el mantenimiento era correctivo. Se usaban las máquinas y con el paso del tiempo, el esfuerzo (cargas/ciclos, erosión, corrosión, fatiga, etc.) superaba la resistencia (diseños/robustez, materiales, etc.) y se generaban solturas, grietas, sobrecalentamientos, entre otros mecanismos de falla y los equipos fallaban.
Estas fallas podían ser de baja intensidad y en esos casos las reparaciones y retorno al servicio eran de corta duración y de bajo impacto económico. Pero en otras ocasiones las fallas eran mucho más severas y en ocasiones catastróficas. Por esta razón la gente de mantenimiento comenzó a darse cuenta de que ciertas fallas (modos de falla como se conocen en la actualidad) ocurrían con una “Frecuencia de fallas” más o menos conocida y, por lo tanto, se podría establecer algún tipo de intervención lo más cerca de la fecha en la cual se podría anticipar que ocurriría una falla, a la que llamaron “vida útil”.
A estas intervenciones cíclicas se les llamó “Mantenimiento Preventivo” y la representación gráfica de su comportamiento es lo que se conoce ahora como la “Primera generación del mantenimiento1”.
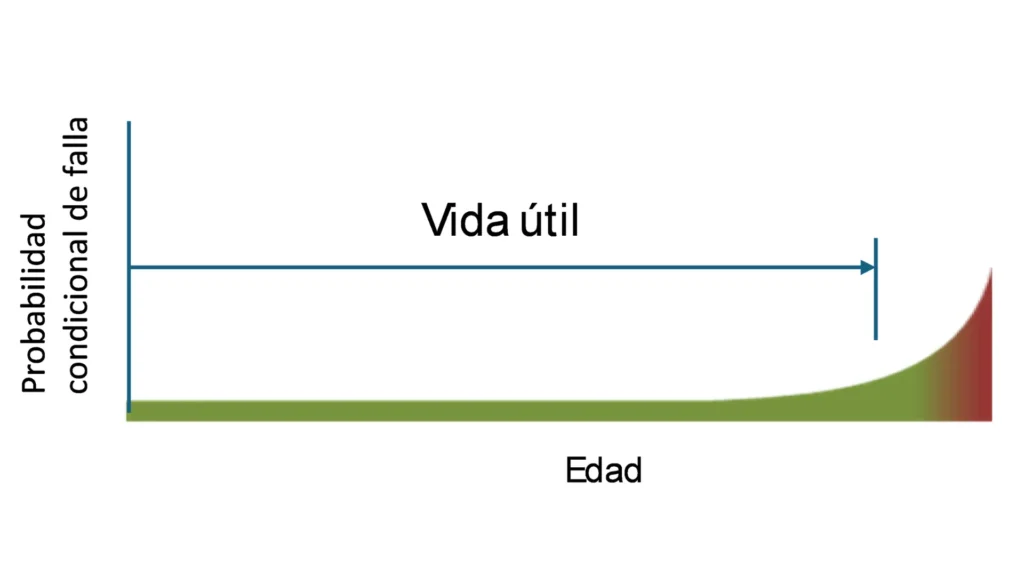
El eje X representa la “Edad”, que puede ser tiempo, km, ciclos, unidades producidas, etc. El eje Y horizontal representa la “Probabilidad condicional de falla”. Más adelante definiremos este término.
Como puede apreciarse, este Patrón de fallas, conocido también como “Enfoque tradicional” o “Desgaste”, muestra un período de baja probabilidad condicional de falla y al final de una vida útil relativamente conocida se presenta un súbito aumento de esta probabilidad de falla. Operar luego de este período sería muy riesgoso para la integridad física de los elementos que componen la maquinaria. Debido a esto, entonces, se programa un servicio o sustitución que restaure la condición de estos componentes de manera cíclica, con lo que se espera puedan operar en forma confiable en el próximo ciclo.
Debido a la sencillez y robustez de las primeras máquinas, este patrón lucía aceptable por todos porque solía permitir una operación más planificada y más económica al evitar en muchos casos las fallas y sus consecuencias.
Segunda generación de patrones de falla
Los ciclos que vendrían de instalación, operación, mantenimiento (preventivo o correctivo), operación y así sucesivamente, trajeron consigo lo que luego conoceríamos como “mortalidad infantil”. O sea, la falla justo al arranque de equipos cuyos componentes no fueron adecuadamente ensamblados inicialmente. Por mal ensamble nos referimos a: ajustes, holguras, aprietes, alineaciones inadecuados. O materiales de calidad/tipo inadecuados. Secuencias de armado inadecuadas. Los tiempos de duración de la mortalidad infantil son variables. Desde segundos en equipos eléctricos o electrónicos hasta unos pocos días en algunos equipos mecánicos robustos.
El factor común que arropa a los componentes con mortalidad infantil es la complejidad o cualquier otra situación donde se tenga alta probabilidad de que las cosas vayan mal durante su puesta en marcha. La siguiente gráfica muestra el patrón resultante de la vida útil conocida con la mortalidad infantil. A este Patrón de fallas, conocido como “Curva de la bañera” se le reconoce como la Segunda generación de Patrones de falla.
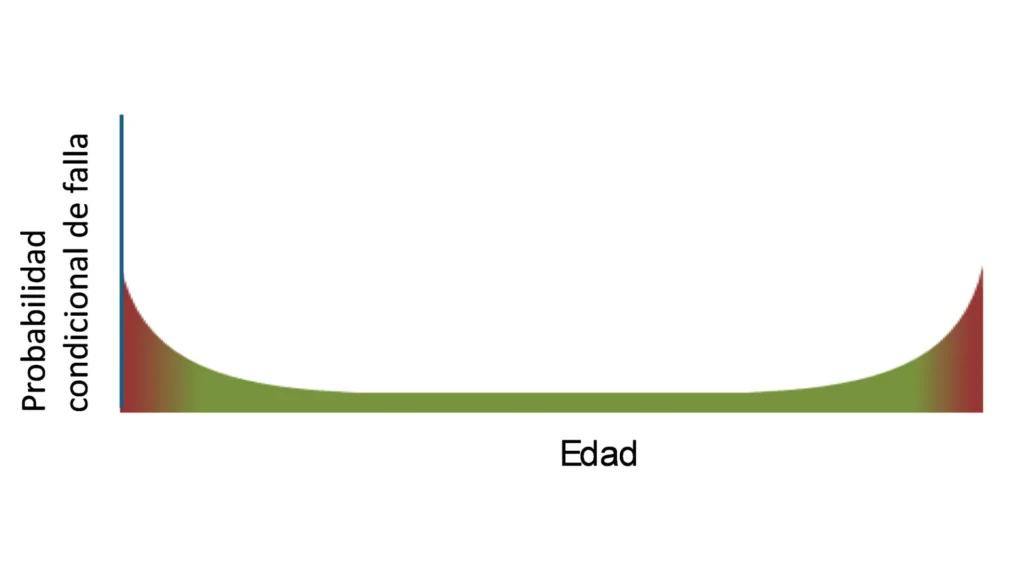
Limitaciones del análisis de patrones de fallas convencionales
Por muchos años se pensó que ya se tenía el tema del mantenimiento explicado con estos dos patrones de falla. Y hasta bien entrados los años 60, el pensamiento tradicional sugería que se podían utilizar registros extensos de fallas para determinar la vida útil de la mayoría de los componentes y se puede programar el mantenimiento preventivo poco antes de que el equipo falle.
Se creía que siempre existe una relación directa entre la confiabilidad y la edad operacional y que cuanto más frecuente se interviene un elemento, menor es su probabilidad de falla.
Estos paradigmas todavía se encuentran enraizados en muchas organizaciones actualmente. Pero esto cambia radicalmente cuando entendemos cada uno de los 6 Patrones de Falla (A al F) del estudio realizado Howard Heap y Stanley Nowlan de United Airlines (condensado en el Reporte “RELIABILITY-CENTERED MAINTENANCE” publicado en diciembre 1978).
Clasificación de los patrones de fallas de RCM
Si no se entiende la naturaleza (patrón) de un modo de falla la estrategia para evitarlo o mitigarlo tendrá el mismo resultado que tirar dardos con los ojos vendados. En este artículo deseamos clarificar algunos aspectos de estos patrones que no siempre son bien entendidos. Iniciemos mencionándolos y describiéndolos brevemente.
Nota: Cuando mencionamos probabilidad de falla nos referimos a la probabilidad condicional de fallas. En el contexto del mantenimiento centrado en confiabilidad, la probabilidad condicional de falla se define como la probabilidad de que un activo falle dentro de un intervalo de tiempo específico, dado que no ha fallado hasta ese momento.
- Patrón A “Curva de la bañera”: Muestra una alta probabilidad de fallas inicial, seguido de una fase continua de probabilidad de fallas aleatorias, finalizando en una zona de abrupto aumento de la probabilidad de falla. RCM asigna a este patrón 4% del total de las fallas.
- Patrón B llamado “Enfoque tradicional”, “Vida útil conocida” o “Patrón de Deterioro”: Comienza con fase continua de baja probabilidad de fallas aleatorias, culminando en una zona de abrupto aumento de la probabilidad de falla. RCM le asigna 2% a este patrón.
- Patrón C “Fatiga”: Incremento progresivo de la probabilidad de falla, pero sin una fase clara de incremento súbito. RCM le asigna 5% a este patrón.
Estos tres patrones, que suman 11% del total de fallas de una instalación, están relacionados con la edad de los componentes.
- Patrón D “Mejor nuevo”: Muestra muy baja probabilidad de falla al comienzo de operación y luego se monta en una fase continua de fallas aleatorias. RCM le asigna 7% a este patrón.
- Patrón E “Aleatorio”: Muestra probabilidad constante de fallas aleatorias durante toda la vida útil del componente. RCM le asigna 14% a este patrón.
- Patrón F “Mortalidad Infantil”: Muestra una alta probabilidad de fallas inicial, seguida de una fase de probabilidad aleatoria constante de fallas durante el resto de la vida útil del componente. RCM le asigna 68% a este patrón.
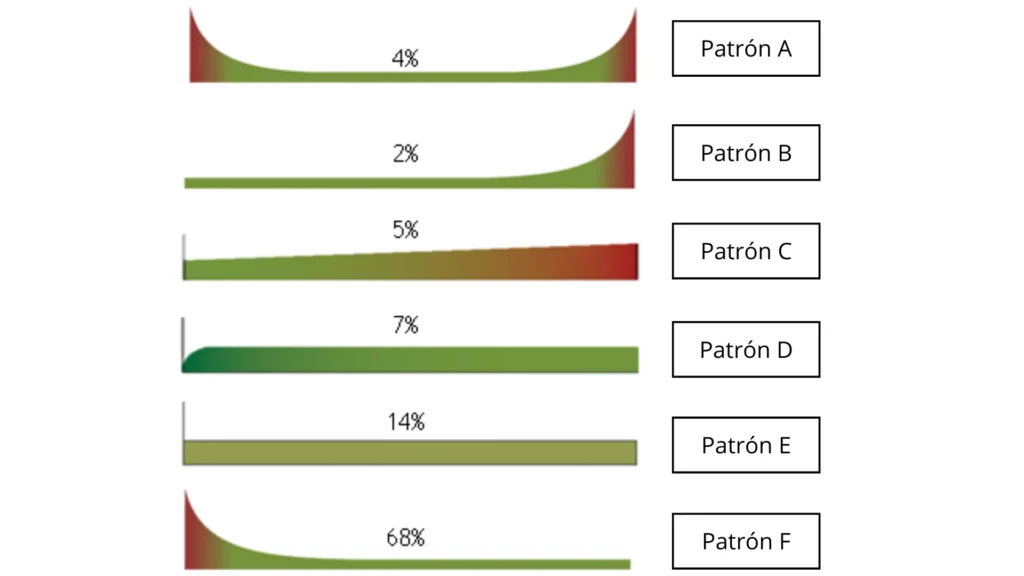
¿Qué nos enseñan los patrones de falla?
Hasta aquí podemos mencionar que interpretábamos en forma muy limitada la naturaleza (patrones) en que los componentes podrían fallar. Y que solo entendiendo esta naturaleza podremos diseñar las políticas adecuadas para manejar los modos de falla de cualquier activo.
Al observar los patrones, con excepción del patrón de fatiga C, notamos que hay tres regiones muy bien definidas. La primera fase, presente en los patrones A y F, muestra la mortalidad infantil. Luego la sigue una fase de probabilidad condicional de fallas constante y en los patrones A y B observamos que terminan con un aumento súbito de la probabilidad condicional de fallas.
Respecto a la mortalidad infantil, mucha gente confunde esta alta probabilidad condicional de fallas con fallas reales. Si fuera así, la industria aeronáutica, donde sus componentes presentan 70% de mortalidad infantil (suma de patrones A y F) no fuera el medio de transporte más seguro del mundo. La alta probabilidad condicional inicial de fallas se atribuye a componentes complejos con muchas conexiones, microcomponentes y/o requerimientos muy estrictos de secuencia de ensamblado, conexionado de equipos, alineación, torque, holguras, materiales resistentes, entre otros.
¿Entonces qué hace la industria aeronáutica y qué debemos hacer nosotros con nuestros equipos para evitar que la alta probabilidad de falla se convierta en fallas? Pues, maximizar los esfuerzos en identificar los modos de falla que cumplen con este patrón y evitar las fallas de mortalidad infantil por dos vías. Una, cumplir estrictamente con los procedimientos de ensamble y conexionado de equipos, alineación, torque, holguras, personal capacitado, materiales/repuestos de buena calidad y protocolos adecuados de pruebas y arranque.
Esto evitará el arranque de los equipos con los típicos resultados del equipo que, operando en forma estable, lo intervenimos el fin de semana y tardamos hasta el miércoles para estabilizarlo.
La segunda vía que nos evita los efectos de la mortalidad infantil será evitar las intervenciones innecesarias (sobre mantenimientos) que inducen a la misma alta probabilidad de falla inicial cada vez que intervenimos los equipos.
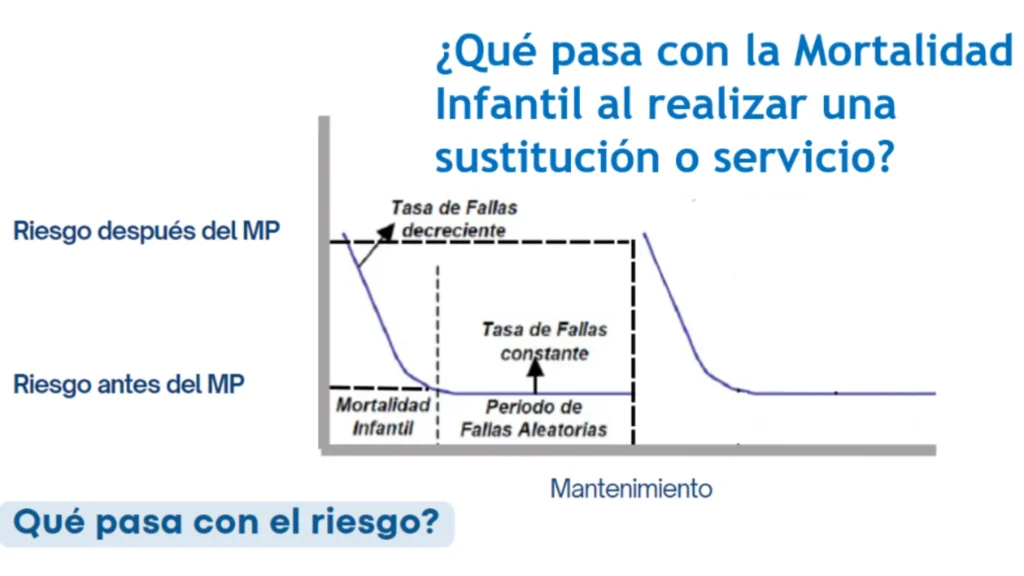
Igualmente debemos acotar que mientras más invasiva sea la intervención (se desarmen y sustituyan más componentes) mayor será la probabilidad de falla.
Donde se identifiquen patrones de falla cíclicos (A, B o C), tenderá a aplicarse una tarea de sustitución o servicio cíclico. Y donde se identifique un patrón aleatorio tenderá a aplicarse una tarea basada en condición. El árbol de decisión de RCM apoyará en seleccionar estas acciones u otras como búsqueda de fallas, operar hasta la falla o cambios.
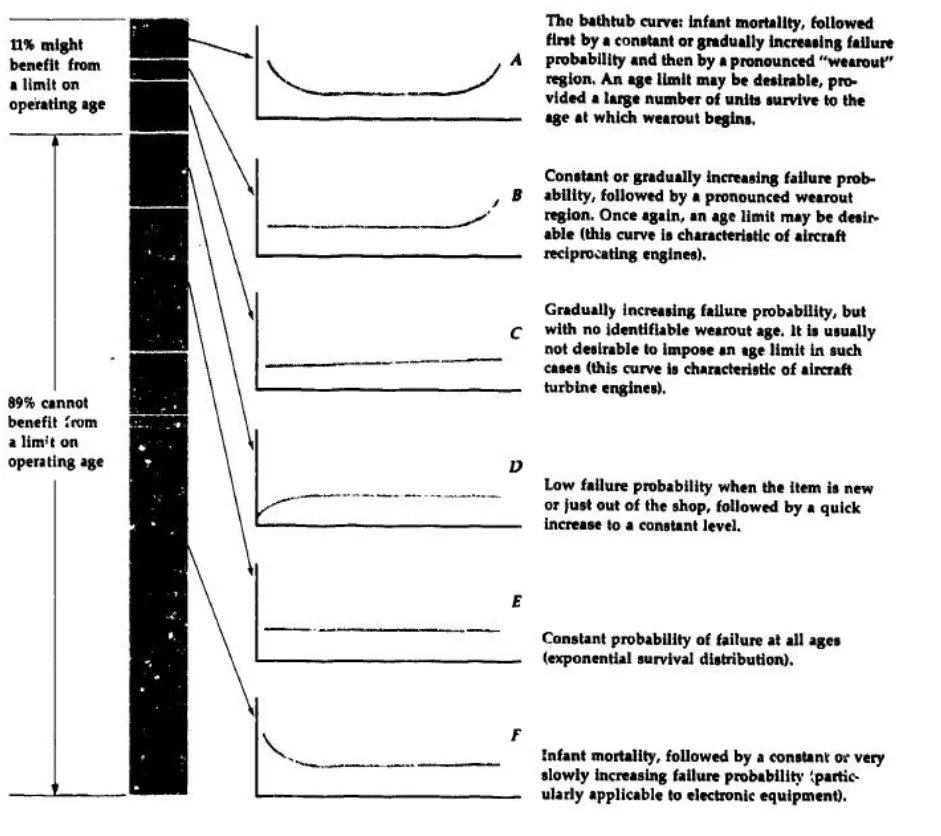
En los patrones aleatorios las tareas con frecuencias asociadas a la edad hacen muy poco para mejorar el desempeño costo-efectivo de un equipo.
Consideración especial con el patrón B
En la práctica el patrón B se identifica principalmente en elementos de activos que están en contacto directo con el producto, en los que existen fenómenos de fricción, corrosión, evaporación, abrasión y erosión, bajo esfuerzos uniformes y constantes. Las tareas de reemplazo o restauración periódicas pueden ser apropiadas.
Pero ¿qué pasa si un equipo tiene varios componentes con modos de falla que siguen el Patrón B? Seguramente la estimación de la vida útil tenderá a una variedad de edades (longevidad de los componentes) distintas que obligarán a conformar un cronograma de mantenimiento preventivo con paradas cada X cantidad de horas y donde se agrupen todas las actividades relativas a componentes cuyos ciclos de servicio y/o sustitución sean similares.
Por esta razón, luego de un análisis de RCM, aunque se espera que se reduzca la cantidad de actividades y que muchas tareas de sustitución cíclica pasen a sustitución por condición, seguramente se mantendrán frecuencias de mantenimiento, por ejemplo, cada 2000, 8000 y 16000 horas.
Conclusión
El conocimiento de los Patrones de Falla como la manera lógica de hacer mantenimiento. Nos quedó claro que para diseñar las políticas para el manejo de cualquier modo de falla debemos conocer su “naturaleza” (Patrón de Falla), de lo contrario estaríamos apostando al azar en la selección de estas políticas. Esto, por supuesto, resultará en una menor confiabilidad y altos costos de mantenimiento. Conocer los Patrones de Falla en profundidad ha sido uno de los mayores avances obtenidos por las organizaciones de mantenimiento a nivel global.
Referencias
- Amendola, L., «Confiabilidad Operacional». 2011.
- F. Stanley Nowlan y Howard F. Heap. “Reliability Centered Maintenance”. December 29, 1978, U.S. Department of Commerce, National Technical Information Service. Produced by Dolby Access Press.