Resumen
El proceso de encapsular un tramo de tubería; es el resultado de envolver una tubería metálico de diámetro (Ejemplo 4” de Ø) con otro tubo metálico de (6” de Ø); utilizando soldadura para la fijación y sellado de la envoltura o capsula según procedimiento y diseño de ingeniería.
Esta práctica generalmente es aplicada en plantas o unidades de proceso en servicios y cuando se detectan espesores bajos críticos; es recomendable su aplicación en tramos de tuberías, alcanzando algunas veces hasta circuitos completos. Esto con la finalidad de:
- Eliminar una condición de riesgo temporalmente; mientras se planifica su reparación permanente.
- Evitar un accidente de incendio que ocasionaría daños materiales y pérdidas humanas con grandes pérdidas de dinero.
- Extenderle la vida útil al activo.
- No realizar una parada no planificada.
- Seguir operando la refinería de forma segura y confiable
Desarrollo
La Sociedad Estadounidense de Ingenieros Mecánicos (ASME), desarrollo el estándar ASME PCC-2 (Reparación de equipos y tuberías a presión), que proporciona métodos para reparar equipos y tuberías dentro del alcance de los Códigos y Normas de Tecnología de Presión de ASME después de haberse colocado en servicio. Estos métodos de reparación incluyen prácticas relevantes de diseño, fabricación, examen y prueba y pueden ser temporales o permanentes, según las circunstancias.
Generalmente cuando se manejan sistemas de inspección en marcha para la industria de petróleo & gas (ver Figura.1); con la finalidad de prevenir potenciales fallas a tiempo, se utiliza este método de reparación temporal y es allí donde comienza el análisis metodológico del ingeniero de confiablidad o inspector de equipos y con su experiencia lograr un final exitoso del proyecto; Sin embargo, la aplicación de esta práctica es muy riesgosa y cada caso debe ser analizado en su totalidad como un proyecto. En este articulo se presenta una descripción sobre esta práctica, los riesgos y beneficios que implican su aplicación durante la reparación de equipos y tuberías a presión en servicio.
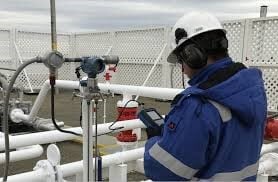
Figura 1. inspector de equipos midiendo el espesor de la tubería con la planta en servicio.
La detección de bajos espesores en una tubería que está en servicio por acción de cualquier desviación en el proceso (variables operacionales fuera de control) o por mecanismos de daños implícitos en el material, conllevan a la toma de acciones inmediatas tales como: inspección ampliada de mediciones de espesores al resto del circuito y otros similares en proceso y con los resultados obtenidos de dichas mediciones analizar los cálculos de tasas de corrosión, vida útil, espesor remanente y próxima fecha de inspección; los cuales, sirven al analista tomar la acción de:
- Continuar monitoreando el circuito de tubería.
- Continuar midiendo los puntos más críticos, bajo un régimen de mediciones especiales.
- Ampliar la inspección en el circuito controlado y en otros con características similares de proceso y materiales.
- Reemplazar el trecho de tubería sin parar la unidad de proceso.
- Encapsular el trecho de tubería con la planta en servicio (ver Figura. 2)
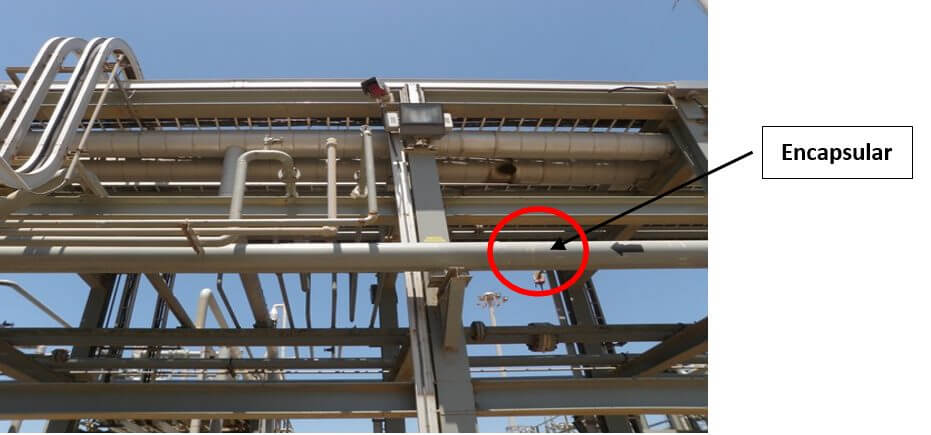
Riesgos y beneficios de encapsular un tramo de tubería
La decisión de encapsular un tramo de tubería con la planta en servicio, se deben considerar una serie de variables por el riesgo que esto representa y lo recomendable es guiarse por un procedimiento con firmas de responsabilidad, que garanticen la funcionabilidad del proceso. Algunas de estas variables son:
- Planta de proceso donde está ubicada el tramo de tubería. Esto por seguridad y estrategia de realizar la actividad. Es diferente encapsular en una planta donde se procesa nafta, que otra donde se procesa vapor.
- La longitud del tramo a encapsular la determina el inspector de equipos en base a los resultados obtenidos en la actividad de mediciones de espesores. Deberían definirse los extremos para las soldaduras circunferenciales de filete, realizando un barrido a la circunferencia del tubo a encapsular para evitar cualquier defecto a la hora de soldar. (información clave para el diseño de la capsula)
- El ingeniero de confiablidad diseña la capsula y le coloca las especificaciones técnicas para la fabricación y el procedimiento de soldadura adecuado para esa actividad. Así mismo, realiza un análisis de flexibilidad al circuito si el caso lo amerita, debido al nuevo peso del circuito.
- La fabricación de las secciones de la capsula debe realizarse en talleres, utilizando moldes de fabricación tomados del trecho de tubería a encapsular y garantizar que no existan desviaciones durante su instalación. (Ver Figura. 3).
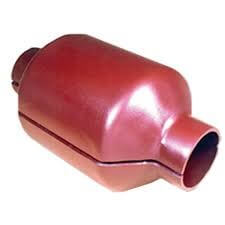
Figura. 3. Capsula de tuberia fabricada en el taller.
- Debe existir un protocolo de seguridad de acuerdo al caso, que debe incluir el uso de un camión de bomberos en sitio el día de la instalación de la capsula con sus operadores; como prevención de algún conato de incendio que pueda poner en riesgo vidas humanas y las instalaciones de la planta en cuestión.
- Debe quedar por escrito el formato de seguimiento de esta actividad con las diferentes firmas de responsabilidad por el rol cumplido y así garantizar el éxito de la actividad.
Una vez finalizado el proyecto de instalación de la capsula (ver Figura. 4), se debe realizar la recomendación para reemplazar el trecho de tubería encapsulado y eliminar esa condición temporal. A partir de la fecha de instalación de la capsula, el operador puede actuar más seguro dentro de su planta y estos son los beneficios obtenidos por la acción ejecutada:
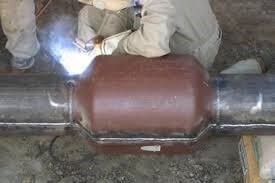
- Elimina una condición de riesgo
- Evita un accidente de incendio que ocasionaría daños materiales y pérdidas humanas con grandes pérdidas de dinero.
- Extiende la vida útil del activo.
- Evita una parada no planificada.
- Operación de la refinería de forma segura y confiable, para continuar produciendo sus refinados; los cuales generaran el beneficio del negocio de acuerdo a su plan de ganancias y cumpliendo con las metas de producción como empresa confiable en la entrega de productos.
Conclusión
La aplicación de esta práctica de reparación temporal en la industria de petróleo & gas ha proporcionado muchos beneficios a las empresas, ya que se ha podido mantener las unidades operativas y produciendo sus derivados de acuerdo a su plan de negocios. Aunque es una actividad que implica cierto riesgo, el disponer de personal calificado, herramientas adecuadas y con métodos y procedimientos seguros que sirvan de guía; esta actividad se convierte en una práctica usual.
Los operadores de estas grandes industrias tienen en esta práctica su gran aliada, como solución preventiva de mantener el indicador de disponibilidad de plantas en servicio en control con una confiabilidad operacional a nivel de los objetivos y metas de las grandes empresas.
Referencias
[1] ASME PCC2 Standard de reparación de equipos y tuberías a presión en servicio.
[1] API – 570 Código de inspección de tuberías: Inspección en servicio,
clasificación, reparación y alteración de los sistemas de tuberías.
[1] API RP-574 Practicas de Inspección para componentes del sistema de tuberías.
Para más artículos visita https://inspenet.com/articulos/
Sobre el autor. Ing. Mario J, Toyo. Asesor Técnico de Inspfalca, con más de 40 años de experiencia en Inspección de equipos para la Industrias de Petróleo y Gas
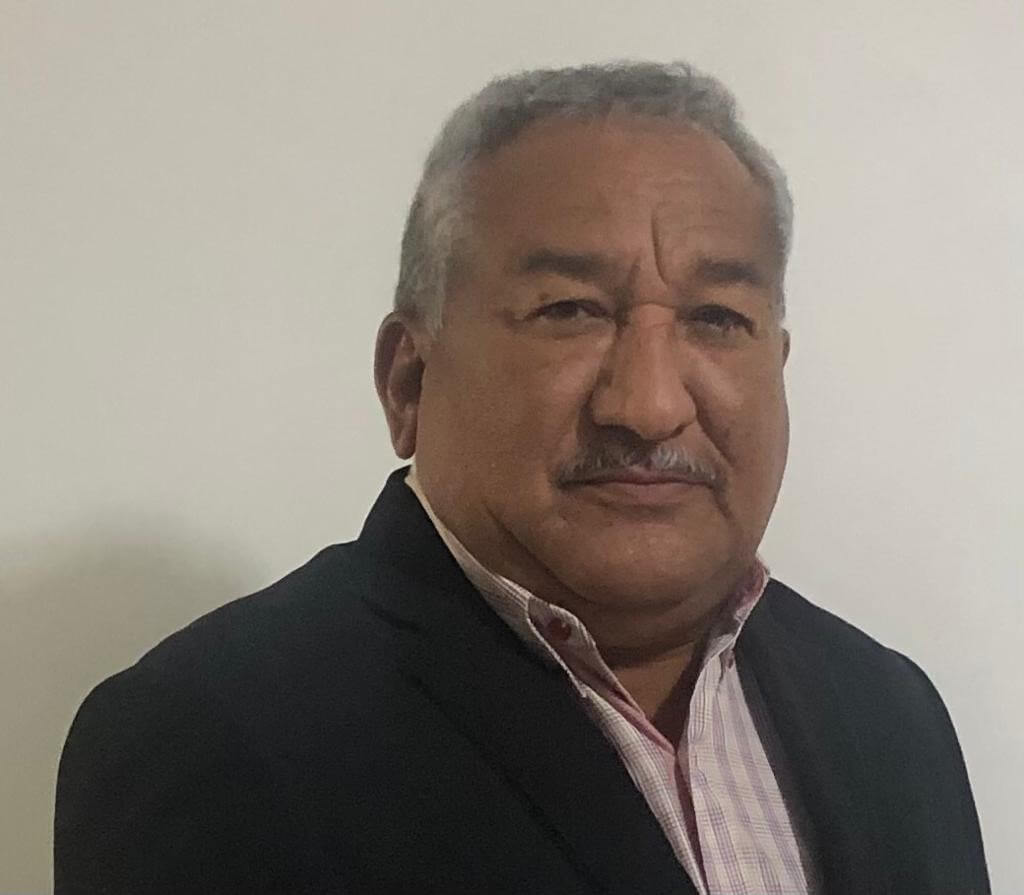