Tabla de Contenidos
- Introducción
- Generalidades del agrietamiento cáustico e impacto en la industria
- Factores y condiciones que producen agrietamiento cáustico
- Prevención y mitigación
- Selección de materiales
- Reducción del estrés residual
- Inhibidores de corrosión
- Control de la temperatura y la concentración
- Norma Nace SP0403: Control de la corrosión por fragilidad cáustica
- Retos y desafíos en la prevención del agrietamiento cáustico
- Variabilidad de las condiciones operativas
- Evolución tecnológica de los procesos industriales
- Necesidad de equilibrar la eficiencia de costos con la integridad de los materiales
- Avances tecnológicos y limitaciones
- Avances tecnológicos en materiales
- Avances en inhibidores de corrosión
- Integración de nuevas tecnologías
- Conclusiones
- Referencias
Introducción
El agrietamiento por fragilidad cáustica representa uno de los desafíos más significativos en la vida útil de los activos industriales, que abarcan desde la refinación de petróleo hasta la producción de energía nuclear. Este fenómeno afecta principalmente a los aceros al carbono y de baja aleación, comprometiendo seriamente la integridad estructural de los equipos.
A través de este artículo, exploraremos qué es el agrietamiento cáustico, sus causas, cómo prevenirlo y mitigarlo; brindando una visión integral de los retos y desafíos de la industria en el manejo de la prevención del agrietamiento cáustico.
Generalidades del agrietamiento cáustico e impacto en la industria
El agrietamiento cáustico, también conocido como corrosión bajo tensión cáustica, es un tipo de deterioro que afecta a metales y aleaciones cuando están expuestos a soluciones alcalinas en presencia de tensiones de tracción. Este fenómeno no solo compromete la integridad estructural de los equipos, sino que también representa un riesgo significativo para la seguridad operacional y la eficiencia económica en varias industrias clave.
Este tipo de corrosión ocurre cuando los aceros al carbono y de baja aleación entran en contacto con soluciones alcalinas de alta concentración, especialmente en condiciones de alta temperatura y bajo tensiones de tracción, ocasionando la formación de grietas intergranulares o transgranulares que debilitan el metal.
Las implicaciones del agrietamiento cáustico se reducen en costos asociados con inspecciones, mantenimientos, y reparaciones de equipos dañados, los cuales pueden ascender a millones de dólares anualmente para una sola planta de operación.
Además, las fallas de equipos pueden resultar en paradas no planificadas, pérdida de producción y, en el peor de los casos, accidentes que comprometan la seguridad humana y el medio ambiente.
Factores y condiciones que producen agrietamiento cáustico
Para desarrollar estrategias efectivas de prevención y mitigación, es crucial entender los factores que contribuyen al agrietamiento cáustico. Estos incluyen la concentración de la solución alcalina, la temperatura de operación y el nivel de tensión de tracción presente en el material.
En términos generales, la aparición de agrietamiento cáustico alcalino de acero al carbono y acero de baja aleación requiere tres condiciones:
- Concentración de soda cáustica: El riesgo de agrietamiento aumenta significativamente cuando la concentración de NaOH supera el 5% en aceros al carbono y de baja aleación.
- Temperatura: La temperatura crítica para el agrietamiento cáustico se encuentra alrededor de los 50 °C, aumentando dramáticamente cerca del punto de ebullición de la solución.
- Tensión de tracción: Según la teoría, el mecanismo de Stress Corrosion Cracking (SCC) de acero con bajo carbono en solución alcalina con concentrado en caliente pertenece a la disolución anódica intercristalina, y el potencial de SCC reside en el rango de transformación de activación-pasivación. Cuando el NaOH local es superior al 10%, la película protectora de óxido del metal se disolverá y reaccionará aún más con la base.
La susceptibilidad del material a la corrosión cáustica y al CSCC depende en gran medida de la concentración de soda cáustica , la temperatura del proceso y el tipo de aleación metálica. El acero al carbono es el material más común utilizado para ambientes cáusticos y es susceptible al CSCC y a la corrosión general o picaduras a temperaturas superiores a 50-60 °C y concentraciones de NaOH inferiores al 20 % en peso %. El acero inoxidable proporciona más protección, pero corre el riesgo de sufrir CSCC y corrosión agresiva por encima de los 120 °C. Tal cual como se aprecia en la siguiente imagen.
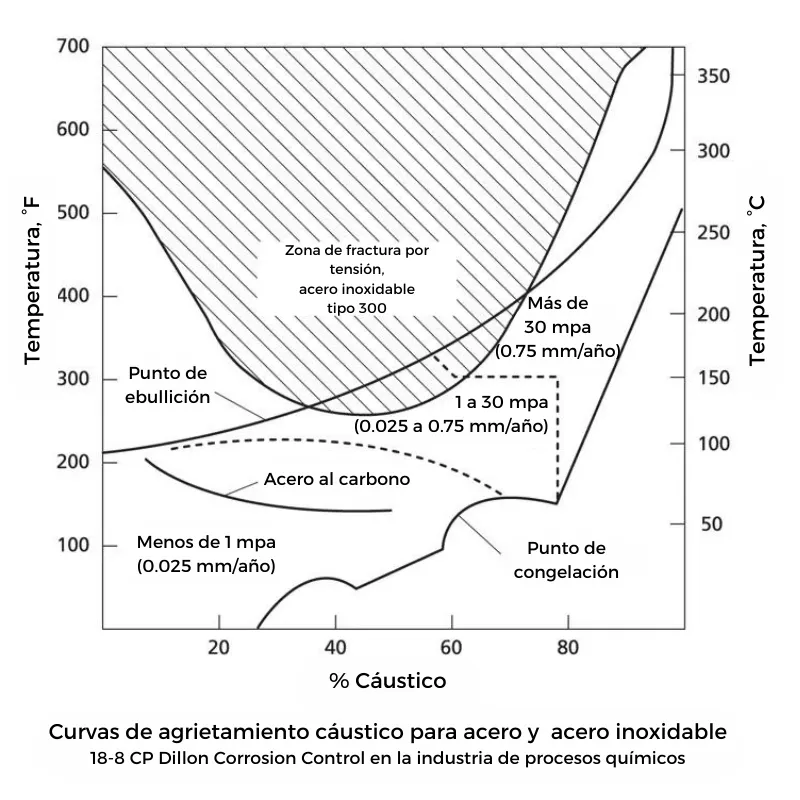
(Fuente: ASSDA)
Prevención y mitigación
La prevención y mitigación del agrietamiento cáustico involucran una combinación de selección adecuada de materiales, manejo de estrés, uso de inhibidores de corrosión, y control de las condiciones operativas. Estas estrategias no solo ayudan a prolongar la vida útil de los equipos, sino que también mejoran la seguridad y la eficiencia operativa.
Selección de materiales
La selección del material adecuado es fundamental para evitar el agrietamiento cáustico. Los aceros al carbono y de baja aleación pueden ser adecuados para ciertas condiciones, pero su susceptibilidad aumenta con la concentración de NaOH y la temperatura.
El uso de aceros inoxidables austeníticos, aunque más costoso, puede ofrecer una alta resistencia a la corrosión en medios acuosos alcalinos. La adición de elementos como el titanio y el niobio ha demostrado mejorar la resistencia al agrietamiento cáustico en ciertos aceros.
Reducción del estrés residual
El manejo adecuado de tensión residual mediante técnicas de fabricación y soldadura es crucial. La implementación de un adecuado precalentamiento y postcalentamiento durante la soldadura, junto con el control de la secuencia de soldadura, puede minimizar las tensiones residuales que contribuyen al agrietamiento.
Además, el tratamiento térmico post-soldadura (PWHT) puede ser efectivo para reducir el estrés y mejorar la estructura microscópica del material.
Inhibidores de corrosión
El uso de inhibidores de corrosión es una estrategia efectiva para reducir el riesgo de agrietamiento. Compuestos como fosfatos, nitritos y sulfatos pueden formar una capa protectora en la superficie del metal, disminuyendo su reactividad en ambientes alcalinos.
La selección y dosificación adecuadas de estos inhibidores dependen de las condiciones operativas específicas y deben ser determinadas mediante ensayos.
Control de la temperatura y la concentración
Mantener la temperatura y la concentración de NaOH dentro de límites seguros es esencial para prevenir el agrietamiento cáustico. Esto puede lograrse mediante el diseño adecuado de los sistemas de proceso y la implementación de controles operativos que eviten la evaporación excesiva y la concentración de soluciones alcalinas.
El monitoreo continuo de estas condiciones permite la detección a tiempo de situaciones de riesgo. Las herramientas hoy en día permiten al usuario controlar estas variables a través de este monitoreo.
Norma Nace SP0403: Control de la corrosión por fragilidad cáustica
Dentro de las estrategias efectivas para combatir el agrietamiento cáustico, la norma NACE SP0403 se erige como un faro de guía para la industria. Esta normativa detalla procedimientos y prácticas óptimas para prevenir la corrosión bajo tensión cáustica en aceros al carbono y de baja aleación, fundamentales en el contexto de equipos de refinería.
Al abogar por una rigurosa selección de materiales, métodos de control de procesos avanzados y diseño consciente de sistemas, la NACE SP0403 proporciona un marco de referencia invaluable para ingenieros, y operadores de plantas. Implementar las recomendaciones de esta norma no solo puede prolongar significativamente la vida útil de los equipos, sino también aumenta la seguridad y la eficiencia operativa en los procesos.
Retos y desafíos en la prevención del agrietamiento cáustico
El agrietamiento cáustico en metales, particularmente en aceros al carbono y de baja aleación, representa un problema persistente para las industrias, incluidas la petroquímica, la refinación de petróleo, y la generación de energía.
A pesar de los esfuerzos significativos para comprender y prevenir este tipo de corrosión bajo tensión, existen varios retos y desafíos que complican su mitigación completa.
Variabilidad de las condiciones operativas
Una de las principales dificultades en la prevención del agrietamiento cáustico es la gran variabilidad de las condiciones operativas a las que están expuestos los equipos y estructuras. Las diferencias en la temperatura, la concentración de soluciones cáusticas, y las tensiones mecánicas pueden variar significativamente, no solo de una instalación a otra, sino también dentro de la misma planta.
Por ejemplo, en las refinerías de petróleo, donde la soda cáustica se utiliza para eliminar los ácidos del crudo, las variaciones en la composición del crudo pueden alterar las condiciones de corrosión de manera impredecible.
Evolución tecnológica de los procesos industriales
La continua evolución de los procesos industriales presenta otro desafío. A medida que las industrias buscan mejorar la eficiencia, reducir costos y cumplir con regulaciones ambientales más estrictas, los procesos y materiales utilizados cambian con el avance tecnológico. Estos cambios pueden introducir nuevas vulnerabilidades al agrietamiento cáustico.
Por ejemplo, el incremento en el uso de técnicas de recuperación mejorada de petróleo, como la inyección de vapor, puede aumentar el riesgo de agrietamiento en los equipos debido a las altas temperaturas y presiones involucradas.
Necesidad de equilibrar la eficiencia de costos con la integridad de los materiales
El equilibrio entre la eficiencia de costos y la integridad de los materiales es quizás el desafío más significativo. Implementar medidas de prevención del agrietamiento cáustico, como la selección de materiales resistentes a la corrosión, el uso de revestimientos protectores y la aplicación de tratamientos térmicos, implica costos adicionales. Las empresas deben equilibrar estos costos con el riesgo potencial de falla del equipo y las consecuencias asociadas, como paradas no planificadas y accidentes.
Un ejemplo de este equilibrio es la decisión entre utilizar acero al carbono, que es más económico, pero susceptible al agrietamiento cáustico, versus aceros inoxidables austeníticos o aleaciones de níquel, que ofrecen una mayor resistencia pero a un costo significativamente mayor.
A pesar de los avances en la comprensión y mitigación del agrietamiento cáustico, la industria enfrenta desafíos continuos en la prevención efectiva de este fenómeno. Estos desafíos incluyen la variabilidad de las condiciones operativas, la evolución de los procesos industriales y la necesidad de equilibrar la eficiencia de costos con la integridad de los materiales.
Avances tecnológicos y limitaciones
Los avances tecnológicos en la prevención del agrietamiento cáustico, especialmente en los campos de los materiales resistentes a la corrosión y los inhibidores de corrosión, están marcando el camino hacia soluciones más efectivas y duraderas. No obstante, la adopción de estas innovaciones enfrenta barreras significativas, principalmente relacionadas con los costos y la complejidad de integrar nuevas tecnologías en infraestructuras y sistemas ya establecidos.
A continuación, se detallan algunos ejemplos prácticos de estos avances y las limitaciones asociadas a su implementación.
Avances tecnológicos en materiales
- Aleaciones resistentes a la corrosión: Se han desarrollado nuevas aleaciones, como las superaleaciones a base de níquel y los aceros inoxidables dúplex, que ofrecen una resistencia superior al agrietamiento cáustico en ambientes extremos. Estas aleaciones están diseñadas para soportar altas concentraciones de sosa cáustica y temperaturas elevadas sin degradarse.
- Ejemplo: En la industria petroquímica, el uso de tuberías de acero inoxidable dúplex en unidades de craqueo catalítico ha demostrado reducir significativamente los riesgos de agrietamiento cáustico, prolongando la vida útil de las instalaciones y minimizando las paradas no programadas para mantenimiento.
- Limitaciones: El costo de estas aleaciones superiores es significativamente más alto que el de los materiales tradicionales, como el acero al carbono. Además, la soldadura y el procesamiento de estas aleaciones pueden requerir técnicas especializadas y equipos avanzados, incrementando aún más los costos de implementación.
Avances en inhibidores de corrosión
- Inhibidores de corrosión de alta eficiencia: La investigación en química de materiales ha llevado al desarrollo de inhibidores de corrosión más efectivos, que pueden ser añadidos a los sistemas para prevenir el agrietamiento cáustico formando una capa protectora sobre las superficies metálicas. Estos inhibidores están diseñados para ser efectivos en bajas concentraciones y en una amplia gama de condiciones operativas.
- Ejemplo: En sistemas de enfriamiento industrial que utilizan agua tratada con soda cáustica, la adición de inhibidores a base de fosfatos o silicatos ha demostrado ser efectiva para prevenir la corrosión y el agrietamiento de los componentes metálicos.
- Limitaciones: Aunque los inhibidores modernos son más eficientes y versátiles, su selección y dosificación requieren un conocimiento profundo de la química del sistema específico y de las condiciones operativas. Además, el monitoreo continuo y el ajuste de la concentración de inhibidores pueden incrementar los costos operativos. También existe el desafío de asegurar la compatibilidad de estos inhibidores con el medio ambiente y con las regulaciones sobre descargas.
Integración de nuevas tecnologías
- Monitoreo y diagnóstico avanzados: Las tecnologías de monitoreo en tiempo real y los sistemas de diagnóstico avanzado, como la espectroscopia de impedancia electroquímica (EIS) y los sensores basados en IoT (Internet de las Cosas), ofrecen nuevas oportunidades para detectar y prevenir el agrietamiento cáustico antes de que cause daños significativos.
- Ejemplo práctico: La implementación de sensores inalámbricos en tuberías y recipientes para monitorear las condiciones de corrosión y las tensiones en tiempo real permite a las plantas químicas y refinerías identificar áreas de riesgo y tomar medidas correctivas de manera proactiva.
- Limitaciones: La instalación de sistemas avanzados de monitoreo y diagnóstico en plantas existentes puede ser desafiante, debido a la necesidad de integrar estos sistemas con el hardware y el software de control existentes. La inversión inicial y los costos de mantenimiento de estas tecnologías pueden ser prohibitivos para algunas operaciones.
Mientras que los avances tecnológicos ofrecen soluciones prometedoras para combatir el agrietamiento cáustico, su implementación efectiva requiere superar desafíos significativos. El equilibrio entre el costo y el beneficio de estas innovaciones es un factor crítico que las industrias.
Conclusiones
El agrietamiento cáustico presenta un desafío significativo para la integridad y seguridad de los equipos industriales, pero con una comprensión profunda de sus causas y la implementación de estrategias efectivas de prevención y mitigación, es posible gestionar y minimizar este riesgo.
A medida que la industria avanza hacia la adopción de tecnologías más avanzadas y procesos más eficientes, la colaboración y el compromiso continuo con la innovación serán clave para superar los desafíos asociados con el agrietamiento cáustico.
Se estima que el agrietamiento cáustico es responsable de más del 20% de los fallos de equipos en la industria petroquímica, lo que subraya la importancia de abordar este problema de manera efectiva.
«Descubre cómo proteger tus equipos contra el agrietamiento cáustico. ¡Actúa ahora!»
Referencias
- API (American Petroleum Institute) Publicaciones
- API 571: «Damage Mechanisms Affecting Fixed Equipment in the Refining Industry»
- API 945: «Avoiding Environmental Cracking in Amine Units»
- NACE International
- NACE TM0177: «Laboratory Testing of Metals for Resistance to Sulfide Stress Cracking and Stress Corrosion Cracking in H2S Environments»
- NACE SP0403: «Avoiding Caustic Stress Corrosion Cracking of Refinery Equipment and Piping”
- Australian Stainless Steel Development Association. (s.f.). FAQ 8 – General Corrosion Resistance: The Normal State for Stainless. Consultado el 1 de marzo de 2024 de https://www.assda.asn.au/publications/technical-faqs/faq-8-general-corrosion-resistance